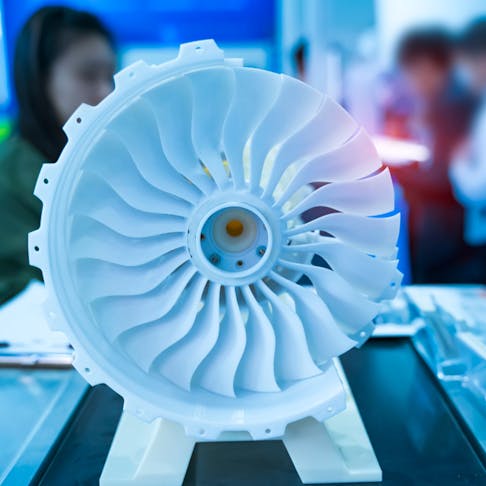
8 Uses of 3D Printing in the Aircraft Industry
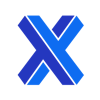
The aircraft industry is constantly evolving, with new technologies being introduced to improve safety, efficiency, and performance. One such technology that has revolutionized aircraft manufacturing and maintenance is 3D printing. 3D printing, also known as additive manufacturing, allows for the creation of complex parts with intricate geometries that cannot be produced using traditional manufacturing methods.
Aerospace was an early adopter of 3D printing and remains a significant contributor to its advancement. Since 1989, companies in this industry have been utilizing 3D printing technology. 3D printing has a wide range of applications in this industry, from prototyping and production of aircraft components to maintenance and repair, tooling, and interior design. In this article, we will discuss the eight uses of 3D printing in the aircraft industry, highlighting how this technology is being used to enhance safety, reduce costs, and improve production efficiency.
1. Tooling and Jigs
3D printing can be used to produce jigs, fixtures, and other tooling equipment, which can improve production efficiency and reduce costs. Aircraft companies require numerous fixtures, templates, guides, and gauges for each plane, and 3D printing allows for their cost-effective and efficient production. Typically, this process results in a 60–90% reduction in cost and lead time compared to other manufacturing methods.
2. Innovation
3D printing allows the production of complex parts that cannot be manufactured using traditional methods. This includes lightweight parts with intricate geometries, such as brackets, housings, and turbine blades. 3D printing also allows for the customization of aircraft parts. Engineers can design and print parts that are specific to the needs of a particular aircraft. This customization ensures that each aircraft is optimized for its intended use, resulting in improved performance and safety.
3. Prototyping
One of the most significant advantages of 3D printing is its ability to quickly produce functional prototypes. With 3D printing, it is possible to create a prototype of a part or component within hours, rather than days or weeks. This means designers can rapidly iterate on designs, test new ideas, and verify form and fit. This can reduce the time and cost associated with traditional prototyping methods, such as CNC machining or injection molding. Figure 1 is an example of a 3D-printed jet engine model:
3D printed jet engine.
Image Credit: Shutterstock.com/asharkyu
4. Surrogates
Surrogates are temporary parts used during production to represent components that will eventually be installed in the final assemblies. These surrogate parts serve primarily as training aids. They are often used by NASA and many Air Force bases as they manufacture aircraft components on the production floor.
5. Replacement Parts
Replacement parts are parts that are produced and installed to replace damaged or worn-out components in an aircraft. The use of 3D printing for replacement parts has the advantage of faster production times, lower costs, and the ability to produce parts that may be difficult or impossible to manufacture using traditional methods.
6. Customization
The flexibility of 3D printing allows for customization on a level that is not possible with traditional manufacturing methods. This is particularly useful in the aerospace industry, where every aircraft is unique, and modifications are often necessary to meet specific customer requirements. With 3D printing, designers can easily create bespoke parts that are tailored to individual aircraft and customer needs.
The aerospace industry experiences a significant impact from 3D printing technologies when the enhanced performance of an aircraft justifies the cost of intricate, one-of-a-kind components. For instance, a single 3D-printed component that is specifically designed and manufactured can reduce air drag by 2.1%, thereby cutting fuel expenses by 5.41%. The technology allows for customized, lightweight bracketry that suits a specific aircraft or type of aircraft, such as cargo, passenger, or helicopter. Additionally, 3D printing provides part consolidation and topology optimization for many custom aerospace components.
7. Lightweighting
The aerospace industry is always seeking ways to reduce the weight of aircraft components to improve fuel efficiency and performance. Reducing the weight of aircraft is a crucial factor in minimizing the environmental impact of flying. 3D printed parts contribute to weight reduction by decreasing air drag, which, in turn, lowers fuel consumption.
At a given speed, the weight of an aircraft increases drag since the wing needs to generate sufficient lift. However, weight has the most significant impact on cruising altitude. Heavier aircraft have a lower cruising altitude because of the air density required for lift. Greater air density leads to more drag, resulting in higher fuel consumption. The use of carbon fiber materials and shape memory alloys can decrease the weight of aircraft while enhancing construction efficiency.
8. Mounting Brackets
The use of 3D printing technology is widespread in the production of low-volume metal brackets that are structurally sound and can mount complex life-saving systems to the interior walls of an aircraft. The manufacturing process typically involves Direct Metal Laser Sintering (DMLS) or Selective Laser Melting (SLM) techniques to create high-quality brackets that meet the safety standards required for the aerospace industry.
Why Is 3D Printing Important in the Aerospace Industry?
The importance of 3D printing in the aerospace industry mainly comes down to the improvement in aircraft design and component production. 3D printing can produce complex, lightweight, and durable parts that cannot be made with traditional manufacturing methods. It has enabled the production of components with intricate geometries, including brackets, housings, and turbine blades, which are critical to the aerospace industry.
Moreover, the ability to produce parts on-demand and at a lower cost has enabled aircraft manufacturers to reduce inventory and lead times, while also enabling them to design and produce customized parts for specific applications. Additionally, the use of 3D printing for tooling, jigs, and fixtures has led to significant cost savings and improved production efficiency.
How Has 3D Printing Impacted the Aerospace Industry?
3D printing is revolutionizing the aerospace industry in various areas, including:
- The production of fixtures, jigs, gauges, and templates, resulting in cost reduction.
- The creation of placeholder parts for training purposes.
- The manufacturing of metal brackets that perform structural functions within aircraft.
- The utilization of 3D printed prototypes to refine the form and fit of finished parts.
- The production of interior aircraft components, such as door handles and cockpit dashboards.
- The manufacture of lighter and more efficient engine and turbine components can be attributed to the advancement of 3D printing technology.
- Enabling the production of complex and lightweight parts that are difficult or impossible to manufacture using traditional methods, results in stronger, more efficient, and safer aircraft.
- Reducing the time and cost associated with producing parts and components by eliminating the need for expensive tooling and molds, leading to reduced inventory and improved supply-chain efficiency.
- Innovations in aerospace manufacturing, such as the use of additive manufacturing in space, have allowed for the production of parts on demand and reduced the need for expensive and time-consuming supply missions.
How Is 3D Modeling Used in Aerospace?
3D modeling has a wide range of applications in the aerospace industry. 3D modeling is the process of creating a three-dimensional representation of an object or structure. One way 3D modeling is used is in building aircraft hangars. Engineers create 3D models of the hangar to help them understand how to put the hangar together and how it interacts with the surrounding environment.
Another way 3D modeling is used is in designing aircraft fuselages. Engineers use 3D models to test how different designs interact with the rest of the plane and the air around it. They can also use 3D models to create prototypes to test how other materials will affect the strength and durability of the fuselage. 3D models also help in estimating the price and cost of an aircraft or aerospace project, including information about the materials, labor, and other expenses associated with the project.
3D models also provide detailed plans and specifications for the project. 3D scanning can store a lot of data about the different parts and components of the project. Finally, 3D models help engineers break down a structure into its parts and components for granular analysis. This helps engineers better understand how a particular feature works or identify potential design problems.
What Are the Aerospace Companies Use 3D Printing?
Many aerospace companies use 3D printing in various capacities. Some of the major players in the aerospace industry that use 3D printing include:
- Airbus
- Boeing
- Lockheed Martin
- GE Aviation
- Rolls-Royce
- SpaceX
- NASA
These aerospace companies have been using 3D printing technology to create parts for their aircraft. They have also started exploring the use of 3D printing in their production processes.
How Does Boeing Use 3D Printing?
Boeing has been engaged in 3D printing experimentation for some time. A few years ago, the company began using 3D printing in satellite production. In 2019, it created the first metal satellite antenna through additive manufacturing. The antenna was made for the Israeli company Spacecom and launched with its AMOS 17 satellite in August of that year. By replacing multiple parts in large assemblies with a single 3D-printed part, Boeing was able to reduce the weight of the antenna and the time it took to produce it.
Boeing is also utilizing additive manufacturing in the production of its top-of-the-line jets. The new Boeing 777x features two GE9X engines, which are the world's largest jet engines by GE Aviation. Incorporating more than 300 printed parts, the engine's weight was reduced and helped to make the Boeing 777x the most efficient twin-engine jet in the world, with fuel consumption lowered by 12% and operating costs lowered by 10%.
How Will 3D Printing Benefit Space Travel?
Manufacturing for space applications requires a high degree of precision. Additive manufacturing processes like DMLS (Direct Metal Laser Sintering) and EBM (Electron Beam Melting) excel at producing parts to close tolerances. A high level of dimensional accuracy is achievable when layers are as thin as 20 or 40 microns. However, some metal 3D printing techniques, such as SLM (Selective Laser Melting), are not suitable for microgravity environments due to their bulky nature, substantial power requirements, and association with flammable powders and respiratory hazards. NASA and its partners are developing metal printing technologies that will be suitable for use on the International Space Station, enabling the production of metal parts for space missions using 3D printing technology.
The ability to print tools and replacement parts in space is essential for long-term missions. 3D printing technology can provide a solution by enabling astronauts to produce necessary parts on demand without waiting for them to be sent from Earth. 3D printing can also reduce the weight of payloads, as only raw materials need to be transported, leading to significant weight and space requirement reductions, and cost savings in launching payloads into space.
Moreover, 3D printing can create more complex and intricate designs not possible with traditional manufacturing methods. This allows for the creation of advanced and efficient components for space travel, such as rocket engine parts and heat shields. Additionally, 3D printing technology can be used to create habitats and infrastructure on other planets. This will facilitate the creation of a sustainable human presence in space with the ability to build and repair structures as needed.
What Is the Most Common Materials Is Used for 3D Printing in Aerospace Industry?
The most common materials used for 3D printing in the aerospace industry are various types of metal alloys, including: titanium, aluminum, stainless steel, and cobalt-chromium. These materials have high strength-to-weight ratios, excellent thermal and mechanical properties, and resistance to corrosion, making them ideal for producing lightweight and durable aerospace components. However, other materials like polymers and composites are also used in some applications. Listed below are some of the materials used in 3D printing for the aerospace industry:
- ABS: Used for bezels such as a dashboard interface.
- Castable Resin or Wax: Used for casted metal parts such as door handles and brackets.
- Glass-Filled Nylon: Used for engine compartments such as a tarmac nozzle bezel.
- Nylon 12: Used for creating air ducts such as airflow ducting.
- Standard Resin: Used in full-size panels such as entry doors and seat backs. These are also used in the production of cabin accessories such as console control parts.
- Titanium or Aluminum: Used as metal components such as GE Jet Engine and suspension wishbones.
- Transparent Resin: Used in the manufacturing of headlight prototypes.
How Does Composite Materials Used for 3D Printing in Aerospace Industry?
Composite materials are increasingly being used in 3D printing for aerospace applications due to their unique combination of strength and lightness. They are typically composed of matrix material, such as a polymer or metal, and reinforcing fibers, such as carbon or glass.
Composite materials are commonly used for components such as airframe structures, engine components, and interior components. 3D printing offers several advantages for producing composite components, including the ability to create complex geometries and structures that are difficult or impossible to manufacture using traditional methods.
Is Titanium a Good Material for 3D Printing in Aerospace Industry?
Yes, titanium is a commonly used material for 3D printing in the aerospace industry. It has an excellent strength-to-weight ratio and high corrosion resistance, making it an ideal material for use in aircraft components. Additionally, 3D printing allows for the creation of complex geometries that may not be possible with traditional manufacturing methods. It is a valuable tool in the production of titanium parts for aerospace applications. However, titanium can be more expensive and difficult to work with compared to other materials. It is typically reserved for high-performance or critical components for which its unique properties are necessary.
Summary
This article presented use of 3D printing in the aircraft industry, explained what they are, and discussed each use in detail and their benefits. To learn more about uses of 3D printing in various industries, contact a Xometry representative.
Xometry provides a wide range of manufacturing capabilities, including 3D printing and other value-added services for all of your prototyping and production needs. Visit our website to learn more or to request a free, no-obligation quote.
Disclaimer
The content appearing on this webpage is for informational purposes only. Xometry makes no representation or warranty of any kind, be it expressed or implied, as to the accuracy, completeness, or validity of the information. Any performance parameters, geometric tolerances, specific design features, quality and types of materials, or processes should not be inferred to represent what will be delivered by third-party suppliers or manufacturers through Xometry’s network. Buyers seeking quotes for parts are responsible for defining the specific requirements for those parts. Please refer to our terms and conditions for more information.
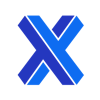