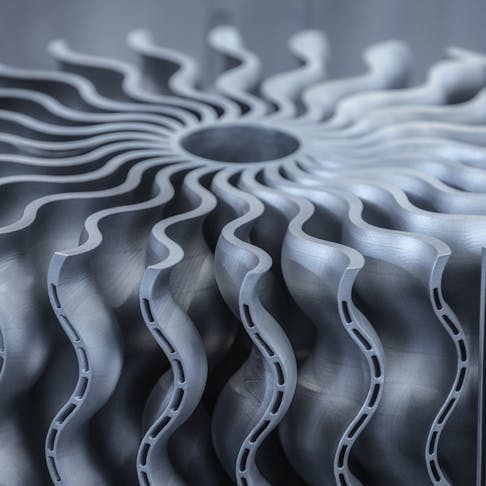
9 Disadvantages of 3D Printing in the Aircraft Industry
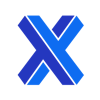
The aviation industry has been using 3D printing in building 3D-printed aircraft components. Although the technology has many advantages, such as: less material waste, quicker production, and more design flexibility, it also has some drawbacks.
In this article, we will go over nine limitations that may affect the functionality, security, and economic viability of 3D-printed aircraft components. We will examine the various difficulties that this technology presents to the aviation sector, from material constraints to the requirement for skilled technicians. It is crucial to remember that these barriers can be overcome with more research and development, so they are not insurmountable. Let's examine the disadvantages of 3D printing in the aircraft industry in more detail and discuss solutions:
1. Quality Control
Quality control is the process of ensuring that the final product meets the desired requirements and standards. Quality control is a challenging process that calls for meticulous attention to detail in the world of 3D printing. This is because 3D printing has the potential to introduce flaws like voids, delamination, and layer inconsistencies that could endanger the structural integrity of the aircraft. Manufacturers must develop quality control procedures and purchase state-of-the-art inspection tools to address this problem. Boeing, for instance, uses CT scanning to find internal flaws in 3D-printed parts.
2. Regulatory Compliance
Standards for safety and quality are met in the aircraft industry through regulatory compliance. One drawback of 3D printing is that it might not adhere to rules established by agencies like the Federal Aviation Administration (FAA). By creating certification procedures and standards for 3D-printed aircraft parts, compliance can be improved. For use in the Boeing 787 Dreamliner aircraft, the FAA has certified a titanium bracket that was 3D printed.
3. Post Processing
Post-processing describes the extra steps needed to complete a 3D-printed part. Sanding, polishing, and coating are just a few of the post-processing techniques used in the aircraft industry. It is a disadvantage because it makes the manufacturing process more time- and money-consuming. Nevertheless, the issue can be fixed by creating better printing methods and materials. For instance, GE Aviation has created a 3D-printed fuel nozzle that only needs a few post-processing steps.
4. Problems With Copyright
In the aircraft industry, 3D printing can lead to copyright issues because businesses might print parts that are protected by copyright without permission. Legal trouble and financial penalties may result from copyright infringement. To address this, businesses can either create their own designs or obtain licenses to use copyrighted components. For example, Airbus has partnered with the 3D printing company Materialise to create and print their aircraft parts.
5. Limited Materials
One significant disadvantage of 3D printing aircraft parts is the lack of suitable materials, which limits the range of components that can be produced using this technology. The requirement for specialized materials that adhere to the standards for particular characteristics set by the aviation industry results in the restriction on material choice. Possible remedies for this problem include creating new materials specifically designed for 3D printing in the aerospace industry or making existing materials more compatible. The aviation industry currently only uses a small selection of plastics and metals for 3D printing, which results in design restrictions that could affect aircraft performance and safety.
6. High Initial Investment
High initial investment refers to the high cost of getting 3D printing technology and the infrastructure needed to put it into use in the aircraft industry. This has the disadvantage of potentially making technology less accessible to small and medium-sized businesses. It might be necessary to form alliances with more powerful businesses or seek government funding to overcome this obstacle. Airbus's collaboration with Stratasys to integrate 3D printing technology into their aircraft manufacturing processes serves as an illustration of this.
7. Jobs Lost in Manufacturing
The use of 3D printing technology in the aircraft industry could have unintended consequences; namely, highly automated manufacturing processes may eliminate jobs. While 3D printing can speed up and streamline production, it may also lessen the need for manual labor, which could result in skilled workers losing their jobs. One solution to this problem might be to retrain employees to be proficient in 3D printing or to look into other uses for their knowledge within the sector. For instance, they might concentrate on improving and designing 3D-printed parts.
8. Design Errors
When it comes to manufacturing, design errors are flaws or omissions in a part or component's planning that could lead to operational problems or safety hazards in the finished product. The use of 3D printing in the aviation industry has a significant disadvantage because it could result in the failure of vital components while in use. Implementing meticulous design verification and validation procedures, such as thorough testing and analysis, is necessary to address this issue. Fissures and porosity that appear as a result of poor material selection or processing conditions are examples of design mistakes in 3D-printed aerospace components.
9. Size Limitations
In 3D printing, size limitation pertains to the largest size of the objects that can be produced. As a result, it is difficult to manufacture large structural parts, which is a disadvantage for the aircraft industry. For larger components, alternative manufacturing processes like CNC machining or composite layup can be used to solve this problem. As an example, Airbus uses 3D printing for small brackets and fittings while using conventional manufacturing techniques for larger components.
How Do Aerospace 3D Printing Disadvantages Affect Its Potential To Revolutionize the Industry?
Aerospace 3D printing has the potential to completely transform the industry by lowering costs, enhancing design flexibility, and speeding up production. However, some drawbacks may prevent its wide adoption. First off, the size of the 3D printer currently determines the size of the printed parts, which might not be adequate for large aerospace components. Secondly, because of aspects like surface finish and material properties, the quality of the printed parts might not meet the high standards needed for aerospace applications. And finally, some businesses might be discouraged from investing in technology because the price of 3D printing tools and materials is still quite high. Because of this, even though aerospace 3D printing has great potential, these drawbacks need to be resolved before it can truly transform the industry.
What Happens if 3D-Printed Parts Are Defective?
If 3D-printed components have flaws, they might not function properly or fail if they don't meet the design requirements. Inspection, testing, and measurement methods can be used to confirm quality. Common non-destructive testing techniques include X-ray, CT scanning, and ultrasonic testing, whereas destructive testing can also include compression and tensile tests. Visual inspection, measurement, and the use of calibrated tools are all examples of inspection.
How Does 3D Printing Standardization Affect Its Use in Different Aircraft Models?
The use of 3D printing in various aircraft models is greatly impacted by standardization in the field. The parts created by 3D printing can be more easily certified for use in aviation if processes and materials are standardized. In addition to ensuring safety and reliability, this lessens the need for costly and time-consuming testing. The Federal Aviation Administration (FAA), for instance, has created guidelines for using additive manufacturing in the production of aircraft parts, including standards for material, process, and part qualification.
Are 3D-Printed Parts Strong and Durable Enough for Aircraft Applications Compared to Traditional Parts?
It depends on various factors such as the material used, the design, and the application of the part. The strength and durability of 3D-printed parts have been shown in some instances to be on par with or even better than those of conventional parts. However, to ensure their dependability and safety for use in aircraft, extensive testing and certification processes are necessary.
How Important 3D Printing in Aerospace Industry?
In the aerospace industry, 3D printing is essential because it enables quick prototyping and production of intricate, lightweight parts that would be difficult or impossible to create using conventional manufacturing techniques. This technology has made it possible to produce parts that are more effective, lighter, and more durable, increasing the efficiency and safety of aerospace systems. In addition, it has decreased production costs and time, making it a crucial tool for the sector. Figure 1 is an example of a 3D-printed aircraft turbofan plastic replica:
3D printed jet engine turbine.
Image Credit: Shutterstock.com/joelpc
What Are the Different Uses of 3D Printing in Aerospace Industry?
The different uses of 3D printing in the aerospace industry are as follows:
- Prototyping and Rapid Manufacturing: Compared to conventional manufacturing techniques, 3D printing enables aerospace engineers to produce prototypes and functional parts more quickly and at a lower cost.
- Testing and Simulation: Models for testing and simulation can also be made using 3D printing. Before spending money on pricey full-scale testing, businesses, for instance, use a 3D-printed model of an airplane to test aerodynamics and other performance characteristics.
- Customization and Personalization: 3D printing allows for the customization and personalization of parts. This leads to better ergonomics and performance for individual users, such as pilots or astronauts.
- Replacement Parts: The aerospace industry often relies on parts that are no longer in production or are difficult to source. With 3D printing, it is possible to create replacement parts on demand, which can help reduce downtime and increase the life span of aircraft.
What Materials Is Best to Used for 3D Printing in Aerospace Industry?
Aluminum, titanium, Inconel®, and other high-performance alloys are the most commonly employed 3D printing materials in the aerospace sector. These materials are perfect for use in important parts like engine components, turbine blades, and structural elements because they have high strength-to-weight ratios, superb heat resistance, and durability.
Are Ceramics Materials Used in 3D Printing in Aerospace Industry?
Yes, ceramics are used in 3D printing in the aerospace industry. They are used to make lightweight, heat-resistant components for aircraft and spacecraft. Ceramics are also very good thermal and electrical insulators, which makes them perfect for some aerospace applications.
Are Composite Materials Used in 3D Printing in Aerospace Industry?
Yes, composite materials are used in 3D printing in the aerospace industry. Materials, like carbon fiber and fiberglass, can be precisely printed using additive manufacturing methods. They are perfect for aerospace applications in which it's essential to use lightweight yet sturdy parts. Furthermore, complex geometries that would be challenging or impossible to produce using conventional manufacturing techniques can now be produced thanks to 3D printing.
What Are Some Advantages of 3D Printing in Aerospace Industry?
Some advantages of 3D printing in the aerospace industry are:
- Customization: Produce complex and specialized aerospace parts, which is not possible with conventional manufacturing techniques.
- Faster Production: Shorten lead times and time to market. 3D printing enables rapid prototyping and production of aerospace components.
- Lightweight Parts: Enable the development of intricate, lightweight designs that lighten the weight of aerospace components and increase general fuel efficiency.
- Cost Savings: Reduce the cost of aerospace parts by eliminating the need for tooling and reducing waste material.
What 3D Printing Machine Is Used in Aerospace Industry?
To produce various types of components and parts, the aerospace industry uses some 3D printing technologies. EBM (Electron Beam Melting), SLM (Selective Laser Melting), and DMLS (Direct Metal Laser Sintering) are often employed in the production of metal-based components. On the other hand, SLS (Selective Laser Sintering), SLA (Stereolithography), DLP (Digital Light Processing), FDM (Fused Deposition Modeling), and material jetting are used to create polymer or composite-based components. The type of material, design, complexity, and functional requirements of the component or part all play a role in the decision to use 3D printing technology.
Summary
This article presented 9 disadvantages of 3D printing in the aircraft industry, explained what each are, and discussed them in detail. To learn more about 3D printing in the aircraft industry, contact a Xometry representative.
Xometry provides a wide range of manufacturing capabilities, including 3D printing and other value-added services for all of your prototyping and production needs. Visit our website to learn more or to request a free, no-obligation quote.
Copyright and Trademark Notices
- Inconel® is a registered trademark of Special Metals Corporation
Disclaimer
The content appearing on this webpage is for informational purposes only. Xometry makes no representation or warranty of any kind, be it expressed or implied, as to the accuracy, completeness, or validity of the information. Any performance parameters, geometric tolerances, specific design features, quality and types of materials, or processes should not be inferred to represent what will be delivered by third-party suppliers or manufacturers through Xometry’s network. Buyers seeking quotes for parts are responsible for defining the specific requirements for those parts. Please refer to our terms and conditions for more information.
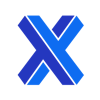