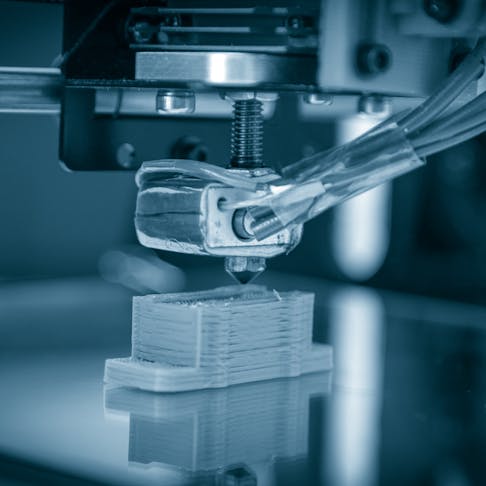
Powder Bed Fusion (PBF) Machines: Definition, Types, Limitations, Benefits, and How They Work
Learn more about this type of 3D printing technology machine that uses thermal energy to selectively melt metal or plastic powders in a layer-by-layer fashion.
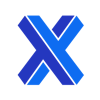
Powder Bed Fusion (PBF) machines are a type of 3D printing technology capable of producing high-quality, intricate, and complex parts for various applications in a range of industries. PBF machines work by melting and fusing layers of metal or plastic powders using a laser or an electron beam to build up a three-dimensional part. The technology uses a layer-by-layer approach to build up parts from a bed of powder, and it is particularly useful in the production of metal components.
This article provides a comprehensive overview of PBF machines, including their definition, types, limitations, benefits, and how they work. We'll delve into the key features of PBF machines and explore their potential applications across different industries. Additionally, we'll compare PBF machines to other types of additive manufacturing processes and highlight the advantages and disadvantages of using PBF technology.
What Are Powder Bed Fusion (PBF) Machines?
Powder Bed Fusion (PBF) machines are additive manufacturing, or 3D printing, machines. The process uses thermal energy (laser or electron beam) to selectively melt materials like ceramic, metal, and plastic, in the form of powder, in a layer-by-layer fashion to build a 3D object. This is all done in a building area. Figure 1 is an example of a PBF machine:
PBF machine example.
Image Credit: Shutterstock.com/Moreno Soppelsa
How Do Powder Bed Fusion (PBF) Machines Work?
Like other additive manufacturing processes, PBF machines also start with a 3D CAD (Computer-Aided Design) file that is loaded into the machine. After this, the machine starts to prepare for the printing process by heating the bed to a consistent temperature. Typically, a layer of 0.1 mm-thick material is spread over the build platform. The first layer of the object to be printed or its support structure is then drawn by fusing the powdered particles, either by a laser or electron beam. This is followed by a new layer of powder that is spread across the previous layer using a blade or a roller. A hopper or a reservoir located below or beside the bed provides a fresh material supply.
The second layer of the object is then fused and added to the previous layer. This process is repeated, layer by layer until the object is printed in full. During the printing process, a platform is used to lower the object accordingly. The separate, unfused powder may remain after the object has been printed, but this will be removed in the post-processing steps.
What Are the Types of Powder Bed Fusion (PBF) Machines?
There are different types of PBF machines that can be used to print parts. There are two primary types of powder bed fusion (PBF) additive manufacturing techniques: laser beam (PBF-LB) and electron beam (PBF-EB). Each of these types has trademarked technologies associated with them. These are Direct metal laser sintering (DMLS), Selective laser sintering (SLS), Selective laser melting (SLM), and Electron beam melting (EBM). The processes are distinguished by the 3D printing materials used and the thermal source used to fuse the powders. PBF methods either use lasers or electron beams to fuse the powdered particles. Each of these methods is discussed separately in the following sections:
1. Direct Metal Laser Sintering (DMLS)
DMLS is a PBF additive manufacturing technique that uses a high-powered laser to selectively fuse metallic powders. The process is similar to SLS but uses metal powders instead of plastics. The laser beam melts and fuses the metal particles to form a solid part layer by layer. DMLS is commonly used in the aerospace and medical industries for the production of complex metal parts with high accuracy and desirable mechanical properties.
2. Selective Laser Sintering (SLS)
SLS is a 3D printing technique that uses a high-powered laser to selectively fuse powdered polymer materials, typically plastics or nylon, into solid objects. It builds parts layer by layer, with each layer being fused by the laser. The unfused powder material supports the part during the build process, eliminating the need for support structures. SLS is widely used in prototyping, product design, and small-batch production.
3. Selective Laser Melting (SLM)
SLM and SLS share similarities in that both processes use a high-powered laser to provide heat, falling under the category of PBF-LB. However, SLM differs in that the laser fully melts the powder instead of just sintering it. This results in a denser and stronger final part. The process is commonly used with metal powders such as titanium and its alloys, aluminum alloys, and stainless steel. More uncommon metals such as tungsten can be processed, but their application tends to be more specialized. An inert atmosphere, usually argon, is employed in the build chamber to prevent oxidation or nitriding of the consolidated material. SLM is commonly used in aerospace, medical, and automotive industries for producing parts with high-quality mechanical properties and complex geometries. For more information, see our guide on SLS vs. DMLS 3D Printing.
4. Electron Beam Melting (EBM)
EBM is another powder bed fusion process that is used for creating metal parts. It uses a beam instead of a laser to melt and fuse metallic powders. Unlike laser-based techniques, an EBM printer operates like a small-scale particle accelerator by firing electrons at the powder bed under a vacuum to melt the metal material. The charged electrons can cause the powder particles to disperse, which is why each layer of material is typically pre-sintered before the 3D printing process begins. Additionally, the entire print bed is kept hot throughout the build. During the 3D printing process, parts are built inside the semi-sintered cake of powder, which provides support and often eliminates the need for additional support structures. It is worth noting that there is a variation of EBM that allows for parts to be sintered within the loose powder. For more information, see our guide on EBM vs. SLM 3D Printing.
EBM is typically used for producing large and complex metal parts for aerospace and medical applications. EBM offers higher build speeds and less residual stress in parts than other PBF techniques, but the equipment is typically more expensive than other machines.
What Are the Benefits of Using Powder Bed Fusion (PBF) Machines for 3D Printing?
Powder bed fusion technology offers several advantages, including:
- Reduced Material Waste: Excess powder is collected and recycled after the part is complete. This reduces waste associated with subtractive manufacturing methods.
- Flexibility: Enables quick iteration on designs, allowing engineers to update CAD designs and reprint flawed parts, leading to innovative product development.
- Improved Manufacturing Times: PBF is the preferred choice for complex parts with intricate internal geometry. A complete part can be designed, manufactured, tested, re-designed, and printed again faster than other methods such as metal casting or MIM.
- Material Range: PBF can work with a wide range of materials such as: titanium, tool steel, Inconel®, aluminum, stainless steel, and others that can be turned into powder using gas or plasma atomization processes.
- Limited Support Structures: PBF parts require minimal support structures during printing as the unused powder acts as support. This enables the creation of complex internal structures such as cooling channels inside turbine blades, where the excess powder can simply be poured out.
What Are the Limitations of Using Powder Bed Fusion (PBF) Machines for 3D Printing?
Powder bed fusion technology offers many advantages but also has some notable drawbacks, including:
- Relatively Slow and Long Print Time: Powder bed fusion has a long build time due to powder preheating, vacuum generation, and cooling-off periods, making it one of the slowest additive manufacturing processes.
- Weak Structural Properties: The structural properties of powder bed fusion parts are not as strong as those made using other manufacturing processes due to their layer-based manufacturing.
- Surface Texture: The surface quality of powder bed fusion parts depends on the grain size of the powder and can resemble manufacturing processes like sand casting and die casting.
- Powder Recycling: The powder used in powder bed fusion is expensive, and throwing out partially melted or unused powder can be even more costly. Preheating the powder can also cause some of it to be affected by the heat, even if it's not used in the final part.
- Thermal Distortion: Thermal distortion can cause the shrinking and warping of fabricated parts, especially polymer parts.
- High Power Usage: Powder bed fusion technology uses a lot of energy to create parts.
What Is the Manufacturing Process of Powder Bed Fusion (PBF)?
The manufacturing process of PBF involves the following steps:
- Design a CAD file and link it to the 3D printer. The design is sliced numerically into layers and the printing sequence is predetermined before the actual printing starts.
- Spread the powder across a build platform. A thin layer of powder is evenly distributed across the build area.
- Heat the entire build area to a temperature slightly below the melting point of the powder particles.
- Use a high-powered laser or electron beam to selectively melt the powder in specific areas, according to a pre-programmed pattern. The melted powder solidifies as it cools and forms a solid layer.
- The build platform is lowered by one layer of thickness, and the process repeats until the part is complete.
- Once the printing is finished, the parts are removed from the powder bed. They undergo various post-processing steps such as the removal of support structures, heat treatment, machining, or polishing.
How Is the Post Manufacture Process for PBF?
Post-processing of PBF-printed parts will be different for different materials used and the different methods used to print the part.
Metal PBF parts require heat treatment due to the internal stresses caused by the process. After heat treatment, support structures are removed and additional post-processing can proceed. Depending on customer requirements, there are several post-processing options available, including CNC machining and polishing.
Metal EBM parts are free-floating off the substrate and supported by semi-sintered powder during the build. Sacrificial supports may be added for heat control or post-processing. EBM parts require breaking out of the powder cake but do not necessarily require a heat treatment step due to elevated temperatures inside the printer.
Plastic parts, on the other hand, are removed from the bed of unfused powder, and excess material is removed with a bead blast, resulting in a consistent surface finish. SLS parts are left as-is once the bead blast is completed, but they are good candidates for additional dyeing if color is desired.
How Do PBF Machines Differ From Other Types of 3D Printers?
PBF machines differ from other types of 3D printers in several ways. The most significant difference is how they build parts layer by layer using powdered materials. PBF machines use a high-powered laser or electron beam to selectively fuse metal or plastic powders, while other 3D printers may use extrusion or photopolymerization methods. PBF machines are also capable of producing highly complex and intricate parts with a high degree of precision and accuracy. Additionally, PBF machines are capable of producing functional plastic parts with exceptional mechanical properties, surpassing those achievable by any other 3D printing technology. However, they often require post-processing to achieve the desired surface finish and may have limitations in terms of the size and geometry of the parts they can produce. What’s more, PBF machines tend to be more expensive and require more specialized knowledge and training to operate.
What Materials Can Be Used With PBF Machines?
PBF 3D printers support a wide range of materials, which are listed below:
Plastics | Metals |
---|---|
Plastics Glass-filled nylon | Metals Aluminum and light alloys |
Plastics Mineral-filled nylon | Metals Chrome-Cobalt alloys |
Plastics Nylon | Metals Precious metals (gold, silver) |
Plastics Polypropylene | Metals Copper and alloys (bronze, brass) |
Plastics Polyetheretherketone (PEEK) | Metals Inconel® |
Plastics Polyetherketoneketone (PEKK) | Metals Steel (mild steel, alloy steel, and stainless steel (316 L and 17-4PH)) |
Plastics TPU | Metals Titanium and alloys |
Metals Nickel and alloys |
Table Credit: https://www.protolabs.com/
Each material has its unique properties, strengths, and weaknesses that can affect the printing process. The use of metals requires high temperatures and energy to melt and solidify the material, which can increase printing time and cost. Polymers, on the other hand, require lower temperatures and less energy than metals, which can result in faster printing times and lower costs. However, polymers may have lower-quality mechanical properties than metals and can be more susceptible to warping and deformation.
What Are the Common Applications of PBF Machines in Different Industries?
PBF 3D printers have found numerous applications across a wide range of industrial sectors due to their flexibility. Some examples of industries that use this technology include:
- Aerospace: PBF 3D printers are used to produce critical aerospace components such as: turbine blades, fuel nozzles, and guide vanes that minimize weight.
- Medical: PBF systems are used to manufacture custom-made orthopedic components like titanium alloy cranial or acetabular implants. PBF is also used to manufacture medical implants like artificial hip joints.
- Automotive: PBF machines are used for prototyping, as well as for manufacturing metal components such as brake pads with cooling ducts for motorsports applications.
- Military: The technology is used to produce components for military aircraft.
How Has the Development of PBF Machines Impacted the Manufacturing Industry?
The development of powder bed fusion (PBF) machines has revolutionized the manufacturing industry in various ways. One of the most significant impacts is the increased design freedom it provides. PBF machines allow for the creation of complex and intricate geometries that would be difficult or impossible to produce using traditional manufacturing methods.
Another key impact of PBF machines is faster prototyping, which has significantly reduced the time and cost required to develop new products. With rapid prototyping, manufacturers can quickly test their design concepts and make improvements before finalizing the production design.
PBF machines have also contributed to reducing waste in manufacturing. By using only the material required to create a part, PBF machines reduce waste and lower the cost of materials. This not only benefits the environment but also the bottom line of manufacturers. In terms of efficiency, PBF machines can produce multiple parts simultaneously, which improves productivity and reduces the time required to manufacture parts. Finally, PBF machines enable the production of customized parts with specific properties, such as strength, durability, and heat resistance. This has led to the development of new products with unique features that meet the specific needs of customers.
How Much Are the PBF Machines Compared to DED?
The cost of PBF machines and DED (directed energy deposition) machines can vary depending on several factors such as the manufacturer, the model, the size, and the features. However, in general, PBF machines tend to be more expensive than DED machines. PBF machines use more advanced technology and are capable of producing parts with higher precision and better surface finish.
What Safety Measures Are When Operating PBF Machines?
There are several safety measures that should be taken when operating PBF machines, including:
- PBF machines can emit potentially harmful fumes and dust during the printing process. It is important to ensure that the printing area is well-ventilated to minimize the risk of inhalation.
- It is recommended to wear personal protective equipment (PPE) such as gloves, safety glasses, and respirators when handling powders and during the printing process. Also, take care when the machine is operating as this is a thermal process and the material and work surface is heated to high temperatures. Do not touch heated components when the printer is running, and allow an appropriate amount of cooling time before attempting to touch either the machine or the printed object. It’s also important to be aware of sharp edges and surface defects that could cut or pierce the skin, especially with metal objects.
- The printing process can generate high temperatures and sparks, which can create a fire hazard. It is important to have a fire extinguisher nearby and to ensure that the printing area is free of flammable materials.
- PBF machines use metal powders, which can be hazardous if they are inhaled or come into contact with the skin. It is important to handle the powders carefully and to use protective equipment when necessary.
- Regular maintenance and inspection of the PBF machine are necessary to ensure it is functioning properly and to prevent accidents or malfunctions.
How Does PBF Contribute to Additive Manufacturing?
PBF contributes to additive manufacturing in several ways. First, it enables the production of complex geometries that would be difficult or impossible to create using traditional manufacturing methods. Second, it allows for the creation of customized parts with specific properties, such as strength or heat resistance. Third, it can produce parts more quickly and with less waste than traditional manufacturing methods. Finally, it has the potential to reduce the cost of manufacturing, particularly for low-volume, high-value products.
Is PBF Machine Expensive?
Yes, PBF machines are quite expensive. While it is possible to find end-to-end systems below $100,000, prices typically start in the $150,000–$200,000 range. High-end PBF machines can cost over $1,000,000. The cost of these systems is dependent on the size, capabilities, and features of the machine. The cost of PBF machines does, however, decrease over time as the technology becomes more widespread and new manufacturers enter the market. Additionally, the potential cost savings and efficiencies gained from using PBF machines for certain applications can justify the investment for some businesses.
Do PBF Machines Produce High-Quality Solutions than DED?
PBF machines and DED (directed energy deposition) machines have different strengths and weaknesses, so it's difficult to make a blanket statement about which produces higher-quality solutions. PBF machines are generally better suited for producing high-precision parts with fine details, better surface finishes, and excellent mechanical properties. The powder bed fusion process allows for intricate geometries and precise control over the material distribution, resulting in parts with excellent dimensional accuracy and surface finish, although post-processing is sometimes required. PBF machines can also produce parts in a wide range of materials, including metals, ceramics, and plastics.
On the other hand, DED machines are better suited for producing large parts with complex geometries, such as aerospace components or industrial molds. DED machines are typically faster than PBF machines and can handle larger part sizes, but they may not have the same level of precision or surface finish.
Summary
This article presented PBF machines, explained what they are, and discussed its various types and benefits. To learn more about PBF machines, contact a Xometry representative.
Xometry provides a wide range of manufacturing capabilities, including 3D printing and other value-added services for all of your prototyping and production needs. Visit our website to learn more or to request a free, no-obligation quote.
Copyright and Trademark Notices
- Inconel® is a registered trademark of Special Metals Corporation
Disclaimer
The content appearing on this webpage is for informational purposes only. Xometry makes no representation or warranty of any kind, be it expressed or implied, as to the accuracy, completeness, or validity of the information. Any performance parameters, geometric tolerances, specific design features, quality and types of materials, or processes should not be inferred to represent what will be delivered by third-party suppliers or manufacturers through Xometry’s network. Buyers seeking quotes for parts are responsible for defining the specific requirements for those parts. Please refer to our terms and conditions for more information.
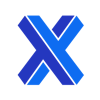