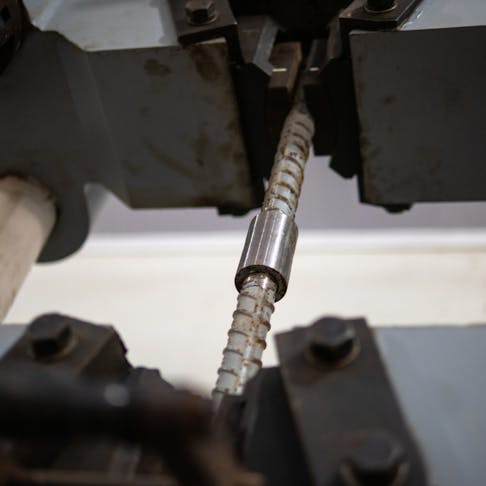
Yield Strength: Definition, Importance, Graphs, and How to Calculate
Learn more about yield strength and how it affects the performance of materials.
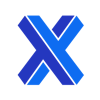
Yield strength is defined as the stress at which a material ceases elastic deformation and begins plastic deformation. It is one of a material's most important mechanical properties. It helps engineers to understand how a material deforms when subjected to stress, therefore assisting them in picking appropriate materials for different applications. Yield strength is determined by conducting a tensile test on a material specimen. This article will define yield strength, discuss its importance in engineering, and describe how it is plotted on graphs and how it is calculated.
What Is Yield Strength?
Yield strength is defined as the maximum stress a material will tolerate before plastic deformation begins. The term “yield strength” is typically used in the context of ductile materials, or materials that can deform.
How Does Yield Strength Relate to 3D Printing?
Yield strength is relevant to 3D printing because the strength of a 3D-printed part is largely based on the material, print orientation, and print quality. 3D-printed parts are stronger within the plane of each printed layer than they are in the direction across the built-up stack of printed layers. The molecular bonds between layers are weaker than those within layers, so if excessive force is applied across, they can delaminate. Orienting a part to take advantage of the better within-layer strength can increase the overall yield strength of the part. For more information, see our guide on the process of 3D printing.
Does Yield Strength Affect the Performance of a 3D Printed Material?
Yes, the yield strength of a 3D-printed material has a big impact on its performance. A 3D-printed part with inadequate yield strength may plastically deform under the normal service loads in an application. The plastic deformation not only reduces the load-bearing capacity of the part but also increases the likelihood of a fracture to occur.
How to Understand the Stress-Strain Curve Graph of Yield Strength?
Yield strength can be understood by looking at the stress-strain curve for a material. Figure 1 is an example of a stress-strain curve graph:
Stress-strain curve graph.
Image Credit: https://en.wikipedia.org/
First, identify the linear portion of the graph. This is the portion of the curve where the stress and strain are proportional to each other. Second, identify where the linear portion of the curve ends and the non-linear portion begins.
There are several ways to define a material’s yield strength based on its stress-strain graph. The most common way of characterizing a material's yield strength is called the "0.2% offset yield strength." To determine the 0.2% offset yield strength, a line is drawn on the stress-strain curve parallel to the initial linear, elastic stress-strain loading curve. The origin of this offset line is at zero stress (0 on the y-axis) and 0.2% strain (0.2% on the x-axis). The point where this offset parallel line intersects the actual stress-strain curve is considered the yield strength of the material. For more information, see our guide on the Stress-Strain Curve.
What Are the Different Ways to Explain the Stress-Strain Graph of Yield Strength?
The yield point is just one point on a stress-strain curve. Surrounding that point are other features that can be described and measured from a stress-strain curve.These points of interest and regions are explained in the list below:
1. Yield Point
The yield point is the observed point on the stress-strain curve where plastic deformation begins. The material deforms elastically from the start of the tensile stress to the yield point. The yield point can be estimated by observing where the linear portion of the stress-strain graph ends and where the non-linear portion begins. Some metals, like mild steel, have two yield points.
2. Elastic Limit
The elastic limit is the point on the stress-strain curve that characterizes the maximum amount of strain a material can withstand without permanent deformation. When stress is released, the material returns to its original dimensions. Beyond the elastic limit, deformation is permanent.
3. Proportionality Limit
The proportionality limit is the point at the end of the linear portion of the stress-strain curve. Prior to the proportionality limit, stress is directly proportional to strain in the material. The proportion of the stress to strain is the modulus of elasticity or Young’s modulus of the material. Once the proportionality limit is surpassed, the relationship between stress and strain is no longer linear.
4. True Elastic Limit
The true elastic limit is the lowest stress that allows dislocations in the crystalline structure of materials to move. It is seldom used to describe material yield since dislocations can move at low stress and it is difficult to detect such movements.
5. Upper and Lower Yield Points
The upper yield point indicates the onset of plastic deformation in the test specimen due to the rapid generation of dislocations in the crystal lattice. However, this point occurs at an unstable value which is dependent on strain rate and test equipment and is not a good basis for design work. The lower yield point denotes a period before strain hardening begins, during which localized bands of plastic deformation, called Luders bands, form and spread across the test section at almost constant stress. The lower yield point is both more repeatable and more conservative.
6. Offset Yield Stress (Proof Stress)
The offset yield stress or proof stress is the most common method for describing a material’s yield strength. It is determined by drawing a line parallel to the linear portion of the stress-strain curve. This line is offset 0.2% strain in the positive direction. The point where this offset line intersects the stress-strain curve is taken to be the yield strength of the material.
What Does Necking and Fracture Mean in Yield Strength Test?
A neck is a region of localized high plastic deformation formed during a tensile test that will inevitably lead to fracture with further application of load. There is a noticeable decrease in the cross-sectional area of the test specimen at the neck perpendicular to the direction of application of the tensile forces. Necking normally occurs in ductile metals after the peak engineering stress (ultimate tensile strength) has been reached. After that point, engineering stress decreases because the neck reduces the sample's cross-sectional area.
What Is the Importance of Yield Strength?
Yield strength is important because it characterizes the highest stress a material can tolerate before permanent deformation occurs. The yield stress of a material is often used by engineers to determine the maximum permissible load a designed part or structure can withstand. By knowing a material’s yield strength, engineers can design safer and more durable parts.
What Is the Formula for Yield Strength?
The mathematical formula for yield strength, or stress at yielding, is simply the basic formula for determining stress: force divided by area normal to the force. Yield strength is specifically defined as the applied force when plastic deformation begins divided by the original cross-sectional area of the test sample. This can also be referred to as the engineering stress at the yield point. The formula is given below:
Yield strength formula.
Where:
- F is the applied force
- A0 is the original cross-sectional area of the test specimen
The stress used to calculate yield strength can be based upon either the engineering stress at 0.2% offset strain or upon the engineering stress at the lower yield point.
What Is the Unit for Yield Strength?
Yield strength is usually expressed in Pascals (Pa), the SI unit for stress, or in pounds per square inch (psi).
What Is the Symbol for Yield Strength?
The symbol for yield strength is σY. The Greek letter σ is the symbol used for engineering stress, while the subscript “Y” means “yield.” Occasionally, “SY” is also used to denote yield strength.
How to Read Yield Strength Graph
To read a yield strength graph (stress-strain curve), first pick a value of stress on the Y-axis. Second, draw a horizontal line that spans between the selected point on the Y-axis to the line of the stress-strain graph. Third, mark the intersection point of the drawn line and the yield strength graph. Next, draw a vertical line starting from the marked point down to the X-axis. The point where the line vertical line intersects the X-axis is the strain that corresponds with the selected stress on the Y-axis. This procedure can be used to interpret any point along the yield strength curve. Figure 2 below is an example of a stress-strain curve with a yield-strength graph:
Stress-strain curve with yield-strength.
Image Credit: https://civilsguide.com/
What Are Examples of Yield Strength
The yield strength of a material depends on its crystal structure, its chemical composition, and whether it is a fiber-reinforced composite. The yield strengths of some example materials are listed below:
- Steels: The yield strength of steel ranges from as low as 220 MPa (hot-rolled A36 steel) to as high as 1570 MPa (4140 alloys, oil-quenched and tempered).
- Stainless Steels: Yield strength for stainless steel varies between about 250 MPa (austenitic stainless steel) to 1000 MPa (precipitation-hardened stainless steel).
- Aluminum Alloys: The yield strengths of aluminum alloys range between 24 MPa (1100 aluminum alloy) and 483 MPa (7075 aluminum alloy).
- Plastics: The yield strengths of plastics range from as low as 4 MPa (plasticized PVC) to as high as 300 MPa (carbon-fiber filled PA 66).
What Device Is Used to Measure Yield Strength?
A universal testing machine, also known as a tensile test machine, is used to measure yield strength. These machines carry out tensile tests during which a continuously increasing tensile load is applied to a test specimen normally at a constant strain rate. As the load is applied, the stress and strain experienced by the test specimen are captured digitally and graphed. Stress is displayed on the Y-axis, while a strain is shown on the X-axis. The yield strength is determined by creating a parallel, offset line at 0.2% positive strain from the linear portion of the stress-strain graph. The stress at the intersection point of the offset line and the stress-strain graph is the yield strength of the material.
Is There a Difference Between Yield Strength and Yield Stress?
No, there is no difference between yield strength and yield stress. The two terms are used to describe the same thing, which is the stress at which a material ceases elastic deformation and begins plastic deformation.
What Is the Difference Between Tensile Strength and Yield Strength?
Tensile strength, sometimes referred to as ultimate tensile strength, is defined as the highest stress a material can experience before fracturing. Yield stress, on the other hand, is defined as the highest stress a material will experience before plastic deformation occurs. For more information, see our guide on Tensile Strength.
Summary
This article presented yield strength, explained what it is, and discussed how to calculate it and its importance. To learn more about yield strength, contact a Xometry representative.
Xometry provides a wide range of manufacturing capabilities, including 3D printing and other value-added services for all of your prototyping and production needs. Visit our website to learn more or to request a free, no-obligation quote.
Disclaimer
The content appearing on this webpage is for informational purposes only. Xometry makes no representation or warranty of any kind, be it expressed or implied, as to the accuracy, completeness, or validity of the information. Any performance parameters, geometric tolerances, specific design features, quality and types of materials, or processes should not be inferred to represent what will be delivered by third-party suppliers or manufacturers through Xometry’s network. Buyers seeking quotes for parts are responsible for defining the specific requirements for those parts. Please refer to our terms and conditions for more information.
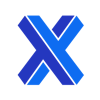