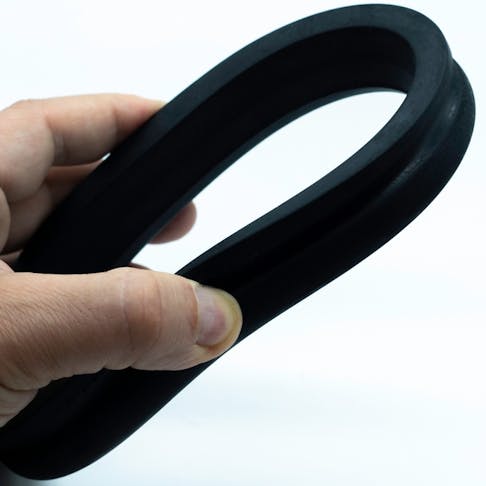
Ductility: Definition, Importance, and Examples of Ductile Materials
Learn more about this property and examples of materials that have good ducility.
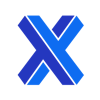
Ductility is a crucial property that describes the ability of a material to be stretched, pulled, or drawn into a thin wire or thread without breaking. It is a property associated mainly with metals and determined by the number of electrons and how they are arranged within the atom. The more electrons a metal has, the greater its ductility. High ductility is essential in applications like structural beams and cables, while low ductility makes a material brittle and more likely to break before deforming.
This article provides an overview of ductility, its importance, how to calculate ductility, and examples of ductile materials. It also discusses the factors that affect ductility, including chemical composition, grain size, and cell structure.
What Is Ductility?
Ductility is a physical property of a material that describes its ability to be stretched, pulled, or drawn into a thin wire or thread without breaking. It is the measure of how much a material can be deformed or elongated under stress before it fractures. Ductility is typically a property that is associated mainly with metals. Metallic bonds are formed between the atoms in metals. This simply implies that electrons from each atom are free to flow between one another. This characteristic also enables the metal's atoms to slide past one another, allowing the metal to be stretched.
The ductility of a metal is determined by the number of electrons and how they are organized within the atom. Around the atom's nucleus, electrons are arranged in rings, each of which is referred to as an electron shell. Any metal's valence electrons are the ones that are located in the outermost shell and migrate within the metal. In general, the most ductile metals are those with the greatest numbers of outer shell electrons and electron shells. A metal's valence electrons become more mobile as its temperature rises, improving the metal's ductility.
What Is the Importance of Ductility?
Ductility is a very important property when it comes to structures. Structures with ductility can flex and deform to some degree without rupturing. High ductility is important in applications like structural beams and cables. It is also possible to create wires out of ductile metals.
What Are Examples of Ductile Materials?
The majority of metals, including: gold, silver, erbium, copper, terbium, and samarium, are excellent examples of ductile materials; whereas non-metals are generally not ductile. Tungsten and high-carbon steel are, however, two examples of metals that are not highly ductile.
What Is the Most Ductile Metal?
The most ductile natural metals are gold, platinum, and silver. All of which can be stretched into fine wires and used for jewelry. Copper is another extremely ductile metal that is frequently used for electrical wires.
What Does High Ductility Mean?
A material with a high degree of ductility is more likely to distort than to break. A material with high strength and ductility will be tougher compared to a material with low strength and ductility. Brittle materials have restricted strain values; so while they may be strong, they lack toughness.
What Does Low Ductility Mean?
A material with low ductility is brittle and will break before deforming when subjected to a tensile force.
How To Calculate Ductility?
Ductility is reported as a percentage of elongation (seen in Figure 1 below), or sometimes as the percentage of area reduction. The following equations can be used to calculate ductility:
Ductility formula.
Measuring elongation after fracture.
Image Credit: https://www.engineersedge.com/
Both percentages of elongation and area reduction are measures that indicate the ductility of a material. The percentage of elongation is not an absolute measure on its own. The elongation is not uniform and will be the most extreme at the center. The reduction of area, which is measured at the minimum diameter, is a better measure of ductility.
What Is Ductility Testing?
Testing for ductility provides a valuable and practical approach to gauging a specimen's capacity for plastic deformation before breaking. It can be used on a number of materials to discover where each material bends or fractures. Simply put, it is a measurement of how far a sample can be stretched before breaking.
When conducting a ductility test (bend test), a specimen is put under tensile stress. The moment the material starts to distort or fracture is noted. In a straightforward test, the specimen might be clamped by a machine between two anvils.
What Are the Factors Affecting Ductility?
Ductility is mainly influenced by three key factors as discussed below:
1. Composition
The composition of a material can affect its ductility in several ways. For example, adding impurities or alloying elements to a metal can alter its microstructure, which in turn can affect its ductility. The presence of impurities can cause defects and inclusions in the material that can act as stress concentrators, leading to premature fracture. Alloying elements, on the other hand, can alter the grain size, texture, and strength of the material, which can have a significant impact on its ductility.
2. Grain Size
Grain size affects ductility due to the comparative number of grain boundaries. Smaller grain sizes mean a higher number of grain boundaries and a decrease in ductility, but increased strength and hardness. Larger grain sizes mean fewer grain boundaries, and an increase in ductility, at the expense of strength and hardness.
3. Cell Structure
Another important factor that influences the ductility of a material is its crystalline structure. Materials with a crystalline structure, such as metals, can exhibit different crystal structures depending on their composition, which can affect their ductility. For example, materials with a face-centered cubic (FCC) crystal structure, such as aluminum and copper, tend to be more ductile than those with a body-centered cubic (BCC) or hexagonal close-packed (HCP) crystal structure.
Why Does Cold Decrease Ductility?
Cold working metal decreases ductility because the microscopic grain structure of metal gets deformed, increasing internal stresses. This has the effect of decreasing ductility while increasing hardness and strength.
Does Hot Working Increase Ductility?
Yes, hot working metal increases its ductility. At high enough temperatures, the internal grain structure of metal changes in such a way that most internal stresses have been eliminated. This results in higher ductility but also in decreased strength and hardness. The temperatures needed to have this effect are dependent on the metal being worked and have to do with the metal’s re-crystallization temperature.
What Is the Difference Between Ductility and Malleability?
Malleability is the ability of a metal to change shape without failing under compression, whereas ductility is the ability of a metal to change shape under stretching forces, or tensile stress. They are similar in that both have to do with the ability of metals to deform without failing. The difference is in the types of forces that are used. Malleability uses a compression force, whereas ductility uses tensile stress.
Ductility gives you an idea of how well a metal can be formed into materials like wires, whereas malleability can tell you how well a metal can be rolled and compressed into sheets.
Summary
This article presented ducility, explained what it is, and discussed the various materials that have good ducility. To learn more about ducility, contact a Xometry representative.
Xometry provides a wide range of manufacturing capabilities, including 3D printing and other value-added services for all of your prototyping and production needs. Visit our website to learn more or to request a free, no-obligation quote.
Disclaimer
The content appearing on this webpage is for informational purposes only. Xometry makes no representation or warranty of any kind, be it expressed or implied, as to the accuracy, completeness, or validity of the information. Any performance parameters, geometric tolerances, specific design features, quality and types of materials, or processes should not be inferred to represent what will be delivered by third-party suppliers or manufacturers through Xometry’s network. Buyers seeking quotes for parts are responsible for defining the specific requirements for those parts. Please refer to our terms and conditions for more information.
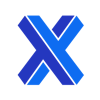