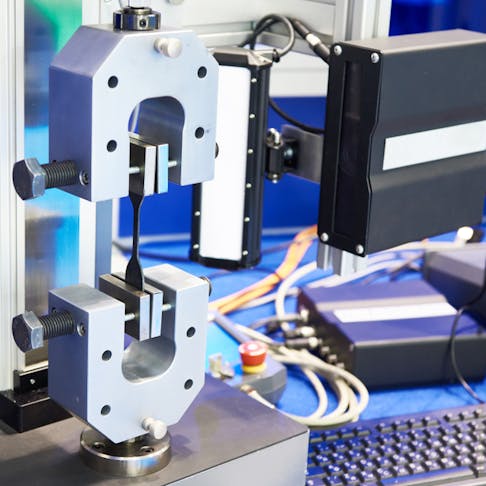
Tensile Strength: Definition, Importance, Types, and Examples
Learn more about how this measurement is used in manufacturing.
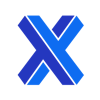
To design a part to withstand a tensile load, it is important to understand how candidate materials for a part behave in tension. Tensile strength is a term used to describe how much load a material can withstand when loaded in tension. It may refer to the yield, ultimate, or fracture (breaking) strength. These values are determined by performing uniaxial tensile tests. This test allows the plotting of stress-strain curves that define the response of a material to loading in tension. This article will explain what tensile strength is, how it is tested, and how it is calculated.
What Is a Tensile Strength?
Tensile strength refers to the load that a material with a particular cross-sectional area can withstand when loaded in tension under specified conditions. For example, a weight hanging on the end of a metal cable creates a tensile load in the cable. As more weight is continually added to the end of the cable, it will begin to stretch until it begins to permanently deform, or “yield,” to the load. reaches its yield point which means that any more weight will cause the cable to permanently deform. If even more weights are added, the cable will eventually begin to neck down at one focal point and break. The various points of failure can be measured as stress which is defined as the force per unit area.
What Is the Importance of Performing Tensile Strength Test?
Tensile tests are used to learn about the strength properties of new material formulations. It is used to check the results of heat treatments of other processes, or to verify that a lot of material meets its original specifications. Validation of the properties of incoming raw materials is a critical part of process control and failure prevention. This is whether a supplier does the testing and the customer accepts it, or whether the customer chooses to check the supplier's claims about a lot of material.
At the part fabricator's plant, testing the tensile strength of materials can be a process control step. It helps ensure that materials are in the correct condition with regard to heat treatment, case hardening, curing, or any other manufacturing step that changes the material's strength and ductility. In a research and development setting, tensile testing is an easy way to check whether a proposed formulation has the characteristics sought for a new application, or for improvement of an existing one.
Tensile tests can be performed on test bars that are cast to shape or machined from raw material. They can also be machined from an actual cast or machined component if there is a critical need to check properties in one section of a large part.
What Is the Importance of Tensile Strength in 3D-Printed Parts?
Tensile strength is an important factor in 3D printing, specifically due to the potential for directional tensile properties. For example, 3D-printed plastic parts using FDM (fused deposition modeling) technology will have a lower tensile strength along their z-axis, where the z-axis refers to the vertical height of the part. This is because the individual layers are not completely fused to each other and are only in contact with each other over a small surface area, as shown in Figure 1 below:
Close-up view of z-axis material contact area of FDM 3D-printed part.
Image Credit: Shutterstock.com/Vladyslav Horoshevych
Many material data sheets for 3D-printed materials will indicate the tensile strengths in different directions within the material (commonly in the Z and XY directions). Other 3D printing technologies, such as SLM (selective laser melting), will produce parts with an isotropic structure, which means their properties are equal in all directions.
What Is the Ideal Tensile Strength for 3D Printing?
The ideal tensile strength depends on the application of the part, the material being used, and the magnitude and direction of loads being applied. For example, if a part is only loaded in compression, then tensile strength does not matter. Or if the part is an enclosure for electronics, then tensile strength is less important than anti-static and moisture absorption properties. When designing 3D-printed parts, the material is selected based on the application and not the other way around.
Is It Important To Determine the Tensile Strength of the 3D-Printed Materials?
Yes, it is important to determine the tensile strength of 3D-printed materials. But, only if the 3D-printed part will be exposed to mechanical loading. For example, if designing a 3D-printed ABS part, then it would be a mistake to use normal ABS properties. 3D printing material may have lower tensile strength compared to the material's theoretical tensile strength based on the 3D printing technology used.
How To Calculate the Tensile Strength of a Material?
The tensile strength cannot be calculated directly without first testing the material to obtain a stress-strain curve. A stress-strain curve is developed by placing a test specimen into a tensile testing machine and then extending the specimen at a fixed rate until it fails. The force and deflection are measured to plot a stress-strain curve while the sample is being extended.
For materials with a well-defined, linear elastic zone, the yield strength can be defined as the applied force over the cross-sectional area as per the equation below.
Yield strength formula.
The SI tensile strength unit is MPa (N/mm2). Basically, the strength equals the stress at the point of failure of the material and this failure point can be characterized by the force per unit area.
What Are the Different Types of Tensile Strength?
The term tensile strength can mean whatever is most useful to the user. Values that are obtained under standardized conditions are the ones that are of most use to an engineer trying to compare material formulations or lots, or trying to determine whether a material will be adequate for a task.
The standard tensile strength points in widest use are the yield strength, the ultimate tensile strength, and, less commonly, the breaking (fracture) strength. These points are illustrated on the diagram in Figure 2 below:
Stress-strain curve for various materials.
Image Credit: https://whatispiping.com/
Each class of material has a different behavior when exposed to tensile load. Ductile materials like low-carbon steel will plastically deform before failure, whereas brittle materials like high-carbon steel will experience very little deformation before failure.
1. Yield Strength
The yield strength of a material refers to the point at which permanent (or plastic) deformation begins. For steel, this is once the material has been deformed past its proportional limit, usually represented by a straight line on a stress-strain curve, points O to A in Figure 3 below. Alternatively, for material without a distinct yield point, like aluminum, yield strength is reported as the stress that coincides with 0.2 % strain:
Ductile metal stress-strain curve.
Image Credit: https://www.smlease.com/
In most cases, metal parts are designed to keep stresses in the service environment below the yield strength.
Highly brittle materials like ceramics will fail at very small deformations and do not yield. Other materials, like elastomers, can deform multiple times their original length. They do not yield but do have a small amount of permanent deformation once the load has been removed.
2. Breaking Strength
Also known as fracture strength, this refers to the point at which the material can no longer carry any more load and breaks. This can be seen as the end point of a stress-strain curve, i.e. point E in Figure 3 above. The breaking point is also the point used for measuring total elongation
3. Ultimate Strength
The ultimate tensile strength is the maximum stress the material can withstand before it ultimately breaks under a tensile load (point D in Figure 3 above). Some metals will experience strain hardening after passing their yield point and will continue to deform as the stress increases to the material’s ultimate tensile strength. Not all materials have a well-defined ultimate tensile strength. This includes some plastics.
What Are the Advantage and Disadvantages of Tensile Strength?
Tensile strength is a material property and does not have an advantage or disadvantage.
What Are the Examples of Tensile Strength of Different Materials?
Table 1 below summarizes the tensile strengths of some common materials:
Material | Yield Strength in Tension (MPa) |
---|---|
Material AISI 1018 Mild Steel (Cold Drawn) | Yield Strength in Tension (MPa) 370 |
Material Tungsten | Yield Strength in Tension (MPa) 750 |
Material Type 316 Stainless Steel (Annealed) | Yield Strength in Tension (MPa) 434 |
Material Copper (Annealed) | Yield Strength in Tension (MPa) 33.3 |
Material 230 Brass (OSO70 Temper) | Yield Strength in Tension (MPa) 69 |
Material T6061-0 Aluminum | Yield Strength in Tension (MPa) 48.3 |
Material ABS | Yield Strength in Tension (MPa) 44.9 |
Material Nylon 6 | Yield Strength in Tension (MPa) 63.6 |
Table Credit: https://matweb.com/
What Material Has the Highest Tensile Strength?
The material that has the highest tensile strength is graphene. Graphene has an ultimate tensile strength of approximately 130 GPa, making it stronger than carbon nanotubes, which until recently had the highest tensile strength. These materials are far stronger than the strongest elemental metal, tungsten, which has an ultimate tensile strength of 0.98 GPa, or the slightly stronger heat-treated Inconel®, with an ultimate tensile strength of 1.034 GPa. It must be noted, however, that neither graphene nor carbon nanotubes can be cheaply mass-produced.
What Material Has the Lowest Tensile Strength?
Plastics tend to have very low tensile strengths compared to metals and ceramics. For example, LDPE (low-density polyethylene) has a tensile strength of 10 MPa. Defining the material with the lowest tensile strength is difficult, as low-tensile strength materials have limited practical application, specifically for load-bearing uses. The listing of materials based on low tensile strength is not common practice.
What Device Is Used To Measure Tensile Strength?
A tensile tester is used to measure the tensile strength of a specimen. This machine grips the test piece at each end and applies a controlled amount of tensile force to it, at a constant rate. The machine automatically logs data on the load applied and the displacement of the grips for further analysis. Figure 4 below shows a typical tensile testing machine:
Electromechanical testing tensile machine.
Image Credit: Shutterstock.com/Sergey Ryzhov
What Are the Applications of Tensile Strength?
Tensile strength is a material property and does not have an application.
What Are the Factors That Can Affect the Tensile Strength of a Material?
Tensile strength can be affected by a number of factors as listed below:
- Temperature: The tensile strength of material trends generally downward with increasing temperature. At values below room temperature, most materials become slightly stronger, but also less ductile.
- Work Hardening: Work hardening consists of plastically deforming a metal - for example, by rolling, hammering, bending, or stretching it. In response, the metal's crystal structure undergoes microscopic changes that increase both the yield strength and the ultimate tensile strength, simultaneously decreasing ductility.
- Additives: Additives like glass or carbon fiber can significantly increase the tensile strength of nonmetals like nylon for example.
- Heat Treatment: Heat treatment changes the microstructure of metal. This can result in either an increase OR a decrease in tensile strength, depending on the treatment applied.
- Defects: Surface and internal defects can reduce the tensile strength of a material. These defects create a weak point where a crack is able to initiate.
What Are The Two Types of Tensile Strength Failure?
Materials subjected to tensile stresses beyond their ultimate tensile strength fail in one of two common ways: ductile failure or brittle failure.
1. Brittle Failure
Brittle failure occurs primarily with hard materials. The material will not deform much before suddenly failing. An example of how a brittle failure looks is shown in Figure 5 below:
An example of brittle failure.
Image Credit: Shutterstock.com/lbrumf2
Materials like cast iron are prone to brittle failure.
2. Ductile Failure
Ductile failure is the primary tensile failure mode for many structural steels and softer materials like aluminum. Failure is not sudden but rather gradual. After the material begins to yield, plastic deformation will continue, then localize, producing a "neck" that will be the site of the final separation of the material. For more information, see our guide on Ductile Failure.
Figure 6 below shows a typical ductile failure:
An example of ductile failure.
Image Credit: Shutterstock.com/High Simple
What Is the Difference Between Tensile Strength and Tensile Stress?
Tensile strength refers to either yield, ultimate, or fracture strength of a material, whereas tensile stress is the amount of force per unit area experienced by a part loaded in tension. For more information, see our guide on Tensile Stress.
What Is the Difference Between Tensile Strength and Yield Strength?
The tensile strength of a material characterizes its ability to resist applied loads in tension. Several specifically defined tensile strength metrics are valuable to engineers: yield strength, the stress at which a material begins to plastically deform, and ultimate tensile strength, often referred to simply as "tensile strength" for short, which is the maximum stress a material can sustain before failure becomes inevitable.
Summary
This article presented tensile strength, explained what it is, and discussed how its measurement is used on various materials. To learn more about tensile strength, contact a Xometry representative.
Xometry provides a wide range of manufacturing capabilities, including 3D printing and other value-added services for all of your prototyping and production needs. Visit our website to learn more or to request a free, no-obligation quote.
Copyright and Trademark Notices
- Inconel® is a registered trademark of Special Metals Corporation.
Disclaimer
The content appearing on this webpage is for informational purposes only. Xometry makes no representation or warranty of any kind, be it expressed or implied, as to the accuracy, completeness, or validity of the information. Any performance parameters, geometric tolerances, specific design features, quality and types of materials, or processes should not be inferred to represent what will be delivered by third-party suppliers or manufacturers through Xometry’s network. Buyers seeking quotes for parts are responsible for defining the specific requirements for those parts. Please refer to our terms and conditions for more information.
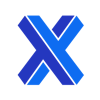