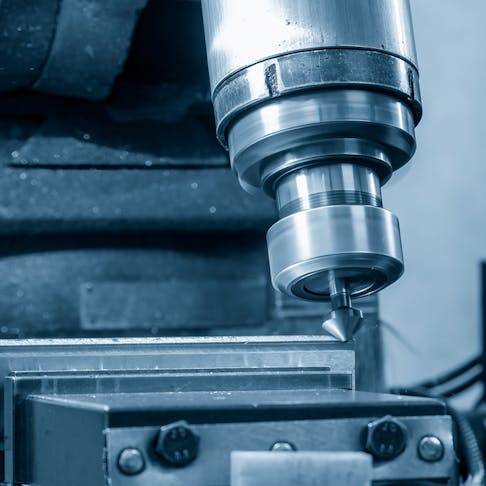
Fillet vs. Chamfer — What Are the Differences and Uses?
Learn more about these two different ways to design edges and when to use each one.
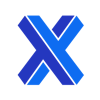
Fillets and chamfers are two ways to design the edges where two surfaces of a part meet. Both fillets and chamfers are used to ease sharp edges and corners. A chamfer replaces the sharp change in direction with an angled slope, while a fillet makes a smooth curve to join two surfaces. Fillets reduce stress concentration at corners or changes of sections because they transmit applied stresses across larger surface areas. While fillets are more difficult to manufacture than chamfers, they reduce overall stress concentration throughout the corner region more than chamfers and therefore result in more durable parts. However, chamfers offer the advantage of easier manufacture and assembly of mating parts. This article will describe the differences between fillets and chamfers, and the application of each.
What Is a Fillet?
A fillet is an interior or exterior edge that has been rounded. Fillets are helpful in improving the mechanical properties of load-bearing parts produced by casting, machining, molding, and 3D printing. For casting, fillets help increase the manufacturability of cast parts because it helps in the removal of the part after molding. The smooth, rounded edges allow the part to easily slide out as opposed to sharp edges.
While fillets can be produced directly in 3D-printed parts, fillets are produced by a radial tool path that connects two non-parallel surfaces and an appropriately sized end mill in machining, casting, and molding. The cost of producing a fillet is influenced by the size of its radius and the edge length. During machining, end mills require clearance to turn and form the corners of a part. It is recommended that the fillet radius does not match the radius of the tool, as the tool will need to come to a complete stop and turn 90 degrees before turning if the radii match. This slows the machining process and adds cost. Instead, manufacturers should start cutting the fillet with an endmill smaller than the radius of the fillet and slowly increase the size of the endmill until the entire fillet is cut.
What Is the Purpose of a Fillet?
Fillets reduce stress concentrations in changes of section and direction on a part. They increase the part’s load-bearing capacity and fatigue life. Fillets accomplish this by distributing stresses over a larger area. Fillets are more effective than chamfers at reducing stress concentrations. This is because stress concentrations in chamfers are focused on the edges of the chamfer where the two surfaces meet. Beyond their mechanical benefits, fillets can improve the aesthetics of a part by removing the harsh appearance of sharp edges and corners.
How Does the Fillet Edge Look Like?
Fillets appear as concave rounded edges for interior corners and as convex rounded edges for exterior corners. The rounded edges blend smoothly with the connecting surfaces in every direction, producing a seamless appearance.
How Are Fillets Designed in AutoCAD®?
Making a fillet in AutoCAD® is done by using the “FILLET” command. Select two lines in your design that meet at an interior or exterior corner. Enter the size of the radius that will form the fillet. Once a value has been prescribed, AutoCAD® will automatically adjust the length of the selected lines, generate the fillet, and remove the sharp corner.
Does a Filleted Edge Look More Appealing?
Yes, filleted edges look more appealing. Fillets can be desired for interior surfaces because they create a seamless surface that is blended together. They may be desired for exterior surfaces because they remove potentially dangerous sharp corners and burrs.
What Is a Chamfer?
A chamfer is an angled or sloped edge between two connecting surfaces of a part. Chamfers, like fillets, help improve the mechanical performance and aesthetic qualities of a part. While chamfers can help reduce stress concentrations, they do not distribute stress as well as fillets do. This makes them less suitable for parts that experience high stresses. Chamfers are more often used to aid in the part assembly since the sharp edges allow parts to mate more easily by allowing them to self-locate. Most chamfers connect two surfaces at a 45-degree angle, but a chamfer can be made at any angle.
What Is the Purpose of a Chamfer?
The primary purpose of a chamfer is to ease sharp edges from a part. It allows parts in an assembly to fit together easily. The angled edges allow male and female parts to slide against each other as they are assembled. It is easy to manufacture chamfers because the required tool does not have to cut a radius and instead cuts a flat surface between two adjacent surfaces. Different sizes of chamfers can be created with a single chamfer tool, countersink, or spot drill. This helps to make the fabrication of chamfers cost-effective.
What Does a Chamfered Edge Look Like?
A chamfer looks like an angle or ramp that connects two surfaces. Chamfers are often made at 45 degrees from the point where the two surfaces meet but chamfers also can be specified based on the leg lengths of a right triangle. Additionally, designers can specify the angle or the length of the face of the chamfer (the hypotenuse of the right triangle). Figure 1 is an example of a chamfered part:
Chamfered part.
Image Credit: Shutterstock.com/LizaLucky
How Is Chamfer in AutoCAD®?
Chamfers are created in AutoCAD® using the “CHAMFER” command. Type “CHAMFER” in the command line, then select the two lines in the design that will be connected by the chamfer. Specify the length of the flat face section or the angles of the chamfer, and AutoCAD® will automatically remove the sharp edge and generate the chamfer.
Does a Chamfer Cost Less than a Fillet?
Yes, the cost of fabricating a chamfer costs less than creating a fillet. This is because chamfers don’t require the same levels of precision as cutting a radius or fillet. The tool paths for creating chamfers are more straightforward. Additionally, different-sized chamfers can be created with a single tool, unlike fillets that may require multiple tools to cut a single radius.
Does a Chamfer Angle Need to be 45 Degrees?
No, chamfer angles are not required to be 45 degrees. Chamfers can be specified at any angle and can also be specified by the length of the face.
When to Know if You Need Fillet or Chamfer?
Both fillets and chamfers can enhance the visual appeal of a part. However, when determining whether to use a fillet versus a chamfer on a part, consider whether the part will be subjected to high loading while in use, or if the part is mated to another part to comprise a larger assembly. A fillet is preferred if the following conditions are present:
- Parts Will Be Subjected to High Loads: Fillets reduce stress concentrations at edges and interior corners and distribute load across a larger surface. They help increase the part’s load-bearing capacity and improve its fatigue resistance to make the part more durable.
- Presentation Parts: Fillets create seamless, smooth surfaces and are more visually appealing than chamfers. Because of these smooth surfaces, it is easier to uniformly distribute coatings and paints.
- Benefit of Fillet Outweighs Cost: Fillets are more expensive to fabricate than chamfers due to the complexities of machining radii and the longer machining time required. Different tools may be needed to cut different-sized fillets, further increasing the overall cost.
A chamfer, on the other hand, is preferred if the following conditions are present:
- Parts Are Not Subjected to High Loads: Chamfers are better suited for parts that aren’t subjected to high loads.
- Paired Parts: The angled surfaces of chamfers allow parts to easily slide against each other when mated together. Or for parts that must fit together in an assembly. Examples include a pin, bolt, or drive screw that must fit into a hole.
- Requires Lower Cost: Chamfers are easier to manufacture than fillets since tool paths are simpler. Different-sized chamfers can be cut with the same tool, which reduces the need to change tools and therefore reduces the overall machining time.
What Are the Differences Between Fillets and Chamfers?
The three primary differences between fillets and chamfers are listed below:
- Fillets connect two surfaces with a rounded edge, while chamfers connect two surfaces with an angled edge.
- Fillets are better for parts that are load-bearing while chamfers are better for parts that must be assembled together.
- Fillets are more difficult and more costly to manufacture, while chamfers are easier and cheaper to manufacture.
Is Fillet a Stronger Edge Design than Chamfer?
Yes, a fillet is a stronger edge design than a chamfer. They make parts more visually appealing than chamfers and safer because there is no edge. Fillets also greatly increase the load-bearing capability and fatigue resistance of a part. This is because fillets allow stresses to be more evenly distributed across an interior or exterior edge.
Is Chamfer the Same as a Taper?
No, a chamfer is not the same as a taper. A taper is a gradual reduction in a dimension over a particular length. Chamfers are applied only at the edge where two surfaces of a part meet.
Is Fillet the Same as a Bevel?
No, a fillet is not the same as a bevel. Fillets are rounded edges between two adjacent surfaces, while bevels are diagonal cuts that join two parallel surfaces. Bevels are most often used on parts that are to be welded together. Bevels allow a significant amount of surface area for molten metal to bond to the two halves of a workpiece, which makes for a strong and effective joint.
Summary
This article presented fillet vs. chamfer, explained what they are, and discussed the differences and uses for each. To learn more about fillet and chamfer, contact a Xometry representative.
Xometry provides a wide range of manufacturing capabilities and other value-added services for all of your prototyping and production needs. Visit our website to learn more or to request a free, no-obligation quote.
Copyright and Trademark Notice
- AutoCAD® is a registered trademark of Autodesk, Inc., and/or its subsidiaries and/or affiliates, in the United States.
Disclaimer
The content appearing on this webpage is for informational purposes only. Xometry makes no representation or warranty of any kind, be it expressed or implied, as to the accuracy, completeness, or validity of the information. Any performance parameters, geometric tolerances, specific design features, quality and types of materials, or processes should not be inferred to represent what will be delivered by third-party suppliers or manufacturers through Xometry’s network. Buyers seeking quotes for parts are responsible for defining the specific requirements for those parts. Please refer to our terms and conditions for more information.
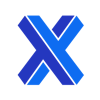