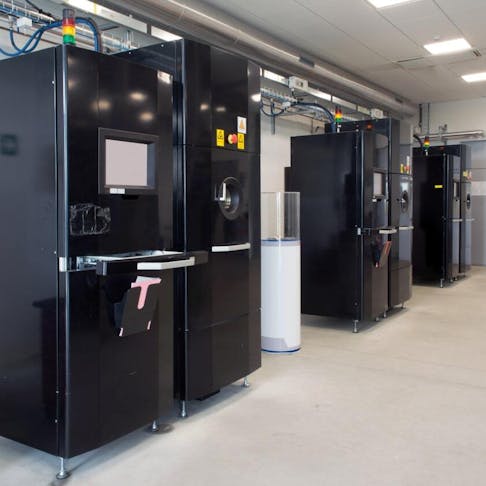
All About Electron Beam Melting (EBM) 3D Printing
Learn how this 3D printing process works, its advantages, and applications.
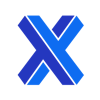
Metal 3D printing has transformed how complex metal tooling and parts are made. Electron beam melting, or EBM, is a sound alternative to CNC machining and metal casting due to its ability to print parts with the durability and strength of metals but at the speeds of 3D printing. EBM is a powder bed fusion process similar to SLM (selective laser melting) and SLS (selective laser sintering) in that each thin layer of metal powder is deposited onto a heated bed and then melted or sintered into place. However, EBM differs from those processes in that the energy source that fuses the powder is an electron beam instead of a laser beam, and the process takes place under a vacuum instead of at atmospheric pressure. Chromium-cobalt and titanium alloys are two of the most commonly used materials in EBM 3D printing.
The history of electron beam melting dates back to 1993, when its principles were first patented by the company Arcam in collaboration with the Chalmers University of Technology in Gothenburg, Sweden. Their goal was to create 3D objects, layer by layer, by melting electrically conductive metal powders with a beam of electrons. In 1997, Arcam was re-organized into Arcam AB, which continued to develop and commercialize the EBM 3D printing process.
In this article, we dive deeper into electron beam melting and discuss everything from what it is, to its advantages and disadvantages, to its similarities and differences from other 3D printing processes.
What Is Electron Beam Melting (EBM)?
Electron beam melting is a 3D printing process that uses electrically conductive metal powders and beams of electrons to produce parts layer by layer. For the process to work, a vacuum of about 0.0001 mbar must be created in the print chamber. In the absence of a vacuum, high-energy electrons collide more frequently with gas molecules, robbing the beam of the energy it needs to complete the printing process. Once a vacuum is obtained, the build platform is heated to extremely high temperatures (600-700 ℃), and the metal powder is precisely deposited to form the current cross-sectional layer of the part to be printed. At that point, the electron beam meticulously moves about the build platform and selectively melts and fuses the new powder layer with the previously printed layers. Once a layer is completed, the build platform drops down by an amount equivalent to one layer. This process repeats until the entire part is printed.
What Is the History of EBM Printing?
Electron beam technology dates back to 1869 when Johann Wilhelm Hittorf and William Crookes experimented with cathode rays (another term for electron beams) in gases to melt metals. Their experiments led to a host of discoveries. However, it wasn’t until 1952 that Dr. h.c. Karl-Heinz Steigerwald developed the first practical electron beam processes for commercial use. At that point, electron beams were mainly used for welding applications. More than 40 years later, however, the principles and theory of EBM were first patented by the Swedish company Arcam in 1993. This was made possible through collaboration with the Chalmers University of Technology in Gothenburg, Sweden. In 1997 the company was organized into Arcam AB as they continued to develop and commercialize the EBM 3D printing process. Arcam AB was acquired by GE in 2016 and reorganized into GE Additive.
What Is Electron Beam Melting Used For?
Electron beam melting 3D printing is used for small-batch manufacturing and proof-of-concept verification of parts with complex geometries. EBM systems and the powders used for printing are expensive, hence the process is seldom used for mass production. EBM produces high-strength metal parts which are mostly used in the aerospace, motorsports, and medical industries. EBM-printed parts are used in turbine blades and engine parts, medical implants, and prostheses.
What Is Electron Beam Melting Similar To?
Electron beam melting is similar to other 3D printing processes, like SLM and SLS. EBM utilizes a beam of electrons to selectively melt and fuse metal powders to form parts layer by layer. In SLM, a laser selectively melts and fuses metal powders on a heated build platform. SLS is a nearly identical process; however, polymeric powders instead of metal powders are selectively sintered and fused by a laser.
EBM differs from these two processes in the use of an electron beam to create parts rather than a laser, the need for a vacuum in which to print parts, and the need for higher build platform temperatures.
How Does Electron Beam Melting Work?
EBM 3D printing is made possible by a tungsten filament that is heated in a vacuum to create the electron beam. Once the vacuum is obtained, the beam is created, and metal powders have been deposited on the build tray, printing can start. The steps in producing an EBM 3D printed part are described below:
- Metal powder is deposited onto the build platform to form the current cross-sectional layer of the part to be printed.
- 3D printer chamber pressure is reduced to around 0.0001 mbar.
- When the required vacuum level is obtained, the electron beam is turned on and heats the entire build platform to the required temperature (600-700 ℃).
- Once the build platform is heated, the electron beam moves precisely to the build platform to melt and fuse the metal powder particles.
- When one layer is completed, the build platform drops down a height equivalent to one layer.
- A fresh layer of powder is deposited, and the process repeats until the entire part has been printed.
- Parts are left to cool—often overnight—before they are removed from the printer.
- After the parts are cooled, residual semi-sintered powder and support structures must be removed.
How Accurate Is Electron Beam Melting?
EBM printing is generally less accurate than SLM printing. This is because, in SLM, the metal powders used are typically finer, and build layers are typically thinner than in EBM. The thicker layers in EBM-printed parts can result in rougher surface finishes. Therefore, post-processing may be required for EBM-printed parts to obtain desired tolerances and surface finishes.
What Materials Are Used in Electron Beam Melting?
Only a limited range of metals can be used in EBM. Titanium and chromium-cobalt alloys are two commonly used materials. Certain steel powders and Inconel® 718 can also be used. Because electron beam melting 3D printing requires electrically conductive materials to build parts, polymeric and ceramic materials cannot be used.
What Are the Temperatures Necessary for EBM?
The EBM 3D printing process requires temperatures as high as 2000 ℃ to fuse the high melting-point materials typically used in EBM printing projects, such as titanium.
Even the preheat phase of EBM printing demands heating the build platform to 600-700 ℃. Preheating the build platform to a high temperature minimizes residual stresses in the printed part, resulting in better mechanical properties. However, a higher build platform temperature requires an adequate amount of support to prevent overhangs from warping. Supports help conduct heat away from the part and into the build platform—effectively reducing thermal stresses throughout the part.
What Are the Advantages of EBM?
The advantages of EBM 3D printing are:
- EBM prints high-density parts with good mechanical properties.
- EBM can print brittle parts that otherwise couldn’t be produced using SLM printing due to the increased print temperatures in EBM.
- Unused powder can be recycled and used in later print jobs, effectively minimizing waste and reducing costs.
- The electron beams used in EBM are more powerful than the laser beams used in SLM because the use of a vacuum assures that no foreign molecules can interfere with printing. This higher energy level leads to faster print speeds for EBM compared to SLM.
- EBM can produce high-quality parts comparable to traditional manufacturing methods like casting or CNC machining.
What Are the Disadvantages of EBM?
The disadvantages of EBM 3D printing are:
- EBM can be an exceptionally expensive process due to the electron beam technology and metal powders used.
- Only a limited group of metals can be printed by the EBM process.
- EBM-printed parts tend to have lower dimensional accuracy compared to SLM-printed parts due to the difference in powder particle size and printed layer height.
Why Is the EBM Process Performed in a Vacuum?
The EBM process is performed in a vacuum to reduce residual stresses in printed parts and to prevent oxidation on printed parts due to increased temperatures. If a vacuum is not present, electrons within the beam can collide with molecules present in the air. This will cause electrons to collide more frequently with gas molecules, robbing the beam of the energy it needs to complete the printing process. In normal practice, heating metals at high temperatures like the ones found in EBM printing can lead to increased oxidation, which makes the final product brittle. However, in EBM, printing inside a vacuum chamber virtually eliminates oxidation and the lack of ductility and toughness it can cause.
What Is the Difference Between EBM and SLM 3D Printing?
The differences between EBM and SLM 3D printing are:
- EBM uses electrons to melt powders, while SLM uses photons from a laser to melt metal powders.
- EBM requires a vacuum to print parts, while SLM prints parts with an inert gas at atmospheric pressure.
- The materials that can be used in EBM (only titanium and chromium-cobalt alloys) are less extensive than the list of materials that can be used in SLM.
- EBM prints parts with lower dimensional accuracy than SLM due to its larger powder particle size and the required print layer heights.
- EBM is more expensive than SLM due to the EBM technology and metal powders that are used.
For more information, see our guide on EBM vs. SLM.
What Is the Difference Between DMLS and EBM 3D Printing?
The differences between DMLS and EBM 3D printing are:
- EBM uses electrons to melt powders, while DMLS uses photons generated by a laser to melt metal powders.
- EBM requires a vacuum for printing, while DMLS can print at atmospheric pressure with the addition of inert gas.
- The materials that can be used in EBM (titanium and chromium-cobalt alloys) are much less extensive than the materials that can be used in DMLS.
- EBM prints parts with lower dimensional accuracy than DMLS because of the difference in powder size and layer heights used in the two technologies.
- EBM is more expensive than DMLS due to the EBM technology and metal powders that are used.
For more information, see our guide on DMLS vs. EBM.
Summary
This article summarized Electron Beam Melting (EBM) 3D printing technology, including how it works, its advantages, materials, and how it compares to other 3d printing processes. To learn more about electron beam melting 3D printing and how you can apply it to your projects, contact a Xometry representative.
Xometry provides a wide range of manufacturing capabilities, including 3D printing and other value-added services for all of your prototyping and production needs. Visit our website to learn more or to request a free, no-obligation quote.
Copyright and Trademark Notices
- Inconel® is a registered trademark of Huntington Alloys division of Special Metals Corp., Huntington, WV.
Disclaimer
The content appearing on this webpage is for informational purposes only. Xometry makes no representation or warranty of any kind, be it expressed or implied, as to the accuracy, completeness, or validity of the information. Any performance parameters, geometric tolerances, specific design features, quality and types of materials, or processes should not be inferred to represent what will be delivered by third-party suppliers or manufacturers through Xometry’s network. Buyers seeking quotes for parts are responsible for defining the specific requirements for those parts. Please refer to our terms and conditions for more information.
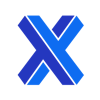