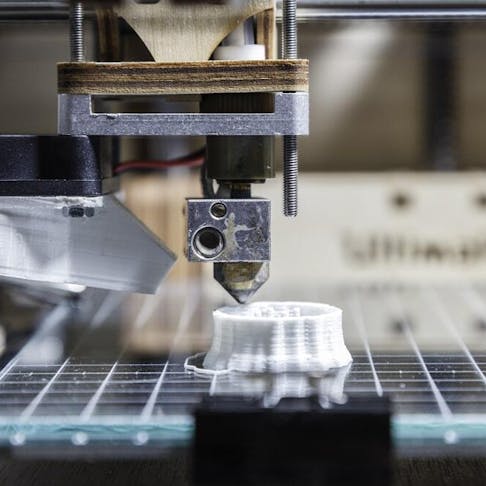
3D Printing vs. Traditional Manufacturing: Differences and Comparison
Learn what makes 3D printing different from traditional manufacturing technologies.
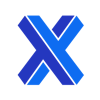
3D printing, or additive manufacturing, is a process in which 3D models are constructed from a CAD or digital 3D model. During the process, the material is deposited layer-by-layer to form the desired object. Traditional manufacturing processes, by contrast, refers to established manufacturing techniques whereby material can either be removed through grinding, drilling, or machining or cast into a mold.
Besides being different in their working principle, 3D printing and traditional manufacturing have other differences. Traditional manufacturing requires mass production to amortize the upfront and running cost of production, tooling, and labor for assembly. Whereas, with 3D printing, the manufacturing cost is independent of the quantity, making it more economical for smaller volumes. 3D printing also offers more design flexibility and the ability to manufacture a product using only one machine, which is not always the case with traditional methods. 3D printing is much faster than many traditional manufacturing methods when producing small to medium objects. This speed improvement is because of the time needed to create the tooling for casts and molds used in traditional manufacturing. However, traditional manufacturing has more material options than 3D printing.
This article will further discuss the differences between 3D printing and traditional manufacturing, present their advantages and disadvantages, and their alternatives.
3D Printing Definition and Comparison to Traditional Manufacturing
3D printing, as a technology, has advanced a lot since its invention by Chuck Hall in 1983. It was initially designed as a rapid prototyping method but has now grown into a true manufacturing process. 3D printing offers many advantages to the manufacturing industry, including design freedom, the ability to create complex designs, mass customization, and a cost-effective, low-volume production method.
3D printing prints an object layer-by-layer as opposed to subtractive processes—like many traditional manufacturing processes—in which the product is cut out of a larger block of material. As a result, 3D printing creates less material waste. There is a wide range of 3D printing types: direct energy deposition, resin-based printers (or VAT polymerization), binder jetting, material extrusion, material jetting, powder bed fusion, and sheet lamination. All forms of 3D printing fall into one of these categories. 3D printing technology also offers a wide selection of materials that can be used to print objects. Industries that currently use 3D printing include robotics, aerospace, automotive, medical, dental, sports, and other consumer products. For more information, see our guide on What is 3D Printing.
Figure 1 below is an example of an item being 3D printed:
A red object being 3D printed.
Image Credit: Shutterstock.com/MarinaGrigorivna
What Are the Advantages of 3D Printing Compared to Traditional Manufacturing?
3D printing offers several advantages over its traditional manufacturing counterpart, including:
- More design freedom.
- Able to print complex designs at no additional cost.
- Generally faster, especially for small and medium-sized objects.
- Involves less waste material.
- Can combine the manufacturing and assembly stages of a product.
- Can easily be used to create custom parts.
- It is a completely automated process with limited labor requirements.
- It uses a single device to handle all aspects of creating the object.
What Are the Disadvantages of 3D Printing Compared to Traditional Manufacturing?
The disadvantages of 3D printing vs. traditional manufacturing are:
- It has fewer material options compared to traditional manufacturing.
- The process is less economical compared to traditional manufacturing in large-scale production.
- Batch quality testing cannot be applied to 3D printed products.
- Print quality can be inconsistent and so varies from product to product.
Traditional Manufacturing Definition and Comparison to 3D Printing
The history of manufacturing dates back to the industrial revolution in the 1900s, when raw materials were turned into useful products. During this period, there was a transition away from human labor (at least partly) toward chemical manufacturing and machinery. Traditional manufacturing processes are mainly subtractive. This means that an object is machined or otherwise removed from a larger block of material. Conventional manufacturing methods can be divided into four main families: molding, forming, machining, and joining. These processes are typically more suitable for large-scale manufacturing, primarily due to the tooling, molding, and/or casting costs, as well as the overall limited design flexibility of the processes. Simply put, the cost of a custom product will not be justified if only 50 units are manufactured, for example., as it is difficult to recoup the upfront expenses that are needed for developing the customization.
One of the most significant advantages of traditional manufacturing, compared to 3D printing, is that it offers a wide range of material selections. The process is also more established. 3D printing, however, has the upper hand regarding design flexibility, cost, and speed. Traditional manufacturing processes are commonly used in industries that mass-produce products made from materials like wood, steel, or plastic. These include producing furniture, plastic bottles or tanks, toys, textiles, and luggage. Figure 2 below is an example of a CNC milling machine:
A CNC milling machine.
Image Credit: Shutterstock.com/Pixel B
What Are the Advantages of Traditional Manufacturing Compared to 3D Printing?
Listed below are some of the advantages that traditional manufacturing processes have over 3D printing:
- Best suited for mass production.
- Batch quality checks are possible with traditional manufacturing processes.
- Most traditional manufacturing processes offer good repeatability.
- Traditional processes offer a wider material selection.
What Are the Disadvantages of Traditional Manufacturing Compared to 3D Printing?
Some of the limitations that traditional manufacturing processes have compared to 3D printing include:
- A single part commonly involves the use of many processes and machines.
- Traditional manufacturing is not well suited for low-volume, customized products.
- Subtractive (traditional) manufacturing generally wastes a lot of material.
- Traditional methods are more labor intensive and more expensive.
Attribute | 3D Printing | Traditional Manufacturing |
---|---|---|
Attribute Lead time | 3D Printing Fast | Traditional Manufacturing Slow |
Attribute Material selection | 3D Printing Good | Traditional Manufacturing Excellent |
Attribute Surface finish | 3D Printing Moderate | Traditional Manufacturing Excellent |
Attribute Profitability | 3D Printing Independent from scale | Traditional Manufacturing Large-scale production |
Attribute Design complexity | 3D Printing Yes | Traditional Manufacturing No |
Attribute Customizability | 3D Printing Yes | Traditional Manufacturing No |
3D printing is ideal for low-volume manufacturing, complex or customized parts, fully assembled components, and fast production. However, traditional manufacturing methods have the upper hand regarding surface finish and high-volume production of simple objects.
3D Printing vs. Traditional Manufacturing: Lead Cost Comparison
The cost comparison of 3D printing vs. traditional manufacturing depends on the number of units produced. The initial costs of traditional methods are quite high, but large-scale production makes such processes economical. With 3D printing, the cost is independent of the quantity; essentially, there is a flat rate per unit.
3D Printing vs. Traditional Manufacturing: Speed Comparison
3D printing is known to be a lot faster than conventional manufacturing. This is mainly due to traditional processes' molding and casting steps before production can commence. With 3D printing, this is not an issue. Designs are created through CAD or 3D modeling software, and the 3D printer prints the model.
3D Printing vs. Traditional Manufacturing: Volume Comparison
Traditional manufacturing processes are established industrial processes known for their ability to be used in high-volume production, whereas 3D printing is ideal for rapid prototyping or small-scale production. Traditional processes are, therefore, mainly used for batch production of simple designs, such as plastic bottles. 3D printing, on the other hand, offers excellent design flexibility and customization. It can be used to troubleshoot designs and introduce minor tweaks to a design before mass production occurs.
3D Printing vs. Traditional Manufacturing: Materials Comparison
Though 3D printing is broadening its material selection and does offer quite a few options, traditional manufacturing processes provide a wider selection and range of materials. However, the continuing evolution of 3D printing technology makes it almost certain that it will be able to compete with traditional manufacturing processes in terms of material range in the near future.
What Are the Mutual Alternatives to 3D Printing and Traditional Manufacturing?
An alternative to both 3D printing and traditional manufacturing is:
- Rapid Tooling: With rapid tooling, a tool or mold is produced which enables manufacturers to rapidly produce parts that function as a tool. Low-volume injection molding is mostly used. Rapid tooling is similar to both 3D printing and traditional manufacturing in that 3D printing and CNC machining (one of the main subtractive manufacturing methods in traditional manufacturing) are used to rapidly produce parts.
What Are the Similarities Between 3D Printing and Traditional Manufacturing?
Aside from their ability to produce working parts, there is not much similarity between 3D printing and traditional manufacturing.
What Are the Other Comparisons for 3D Printing Besides Traditional Manufacturing?
Another alternative to 3D printing is:
- 3D Printing vs. Laser Cutting: 3D printing (specifically SLA, SLS, and SLM) and laser cutting are similar in that both technologies use a laser to produce parts.
What Are the Other Comparisons for Traditional Manufacturing Besides 3D Printing?
Another alternative to traditional manufacturing is:
- Traditional Manufacturing vs. Smart Manufacturing: Smart factories, associated with smart manufacturing, digitize traditional manufacturing processes and machinery.
Summary
This article contrasted 3D printing and traditional manufacturing processes to see how they differ in approach, material selection, production volume, and other factors. To learn more about 3D printing or traditional manufacturing processes, contact a Xometry representative.
Xometry provides a wide range of manufacturing capabilities, including 3D printing and other value-added services for all of your prototyping and production needs. Visit our website to learn more or to request a free, no-obligation quote.
Disclaimer
The content appearing on this webpage is for informational purposes only. Xometry makes no representation or warranty of any kind, be it expressed or implied, as to the accuracy, completeness, or validity of the information. Any performance parameters, geometric tolerances, specific design features, quality and types of materials, or processes should not be inferred to represent what will be delivered by third-party suppliers or manufacturers through Xometry’s network. Buyers seeking quotes for parts are responsible for defining the specific requirements for those parts. Please refer to our terms and conditions for more information.
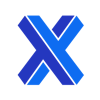