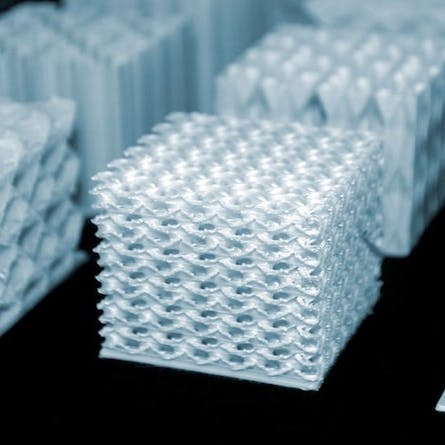
All About Fused Deposition Modeling (FDM) 3D Printing
Learn about this process and its applications and benefits.
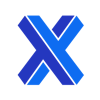
3D printing is now one of the most common and efficient methods of creating parts for businesses and home users. One of the most popular 3D printing technologies is FDM or Fused Deposition Modeling. This is a method that extrudes a thermoplastic filament through a nozzle onto the build plate. FDM is a preferred and highly rated technique due to its speed and reliability. Some industrial requirements for the more advanced 3D prints made with glass or ceramic are restricted in FDM printers, however. Although FDM has limitations in print quality, it's still the most standard method in 3D printing.
This article will discuss FDM—its definition, history, benefits, and limitations—and compare it to other 3D printing technologies.
What Is Fused Deposition Modeling (FDM) in 3D Printing?
Fused Deposition Modeling is a 3D printing technique that creates three-dimensional images by fusing, layer by layer, the melted materials ejected through a nozzle. The thermoplastic filament is heated while printing and is deposited into 2D layers onto the build platform. These layers then fuse together to create a part. For more information, see our guide on 3D printing.
Figure 1 below is an example of an FDM 3D printer:
Figure 1: FDM 3D Printer
Image Credit: Shutterstock/R_Boe
Who Created FDM Technology?
FDM technology was created by Scott Crump in 1988. Crump had the idea of combining polyethylene and candle wax using a glue gun to create a frog toy for his daughter. He patented the technology and founded Stratasys, Inc with his wife a year later, in 1989. Various 3D manufacturers took the lead from his creativity to produce different brands of 3D printers.
How Does FDM Printing Work?
FDM printing works by using CAD files. Before an image is printed, it is translated into a format that the printer can interpret, usually an STL file. The anchor point, which aids in holding the materials during printing, is used in FDM printers along with the material for making the final object. The thermoplastic filament is uncoiled during printing and then pushed through an extruder nozzle. The filament is heated by the nozzle before being released onto the platform. The computer controls this by relaying information about the X, Y, and Z measurements of the object. The material then cools and hardens. Each successive layer builds on the layer underneath it. As the building up of one layer is completed, the platform moves down to allow the next building layer to continue until the whole part is fully formed. It could take a little while to print smaller objects, but more complicated ones take longer to print.
What Are the Benefits of FDM Technology?
The benefits of FDM technology include creating fast and low-cost parts using thermoplastic polymers such as nylon, polyethylene, and rubbers. Manufacturers can easily make prototypes of products with FDM to illustrate the product plan or design. Listed below are the additional benefits of FDM:
1. FDM Technology Is Neat, Easy To Use, and Appropriate for the Workplace.
Compared to other 3D printing technologies, FDM is less complex and easy to use. It is generally preferred for hobbyists and home use. FDM printers are also available in compact sizes without any loss of precision to fit into the workspace, especially when used for exhibitions and sales.
2. Production-grade Thermoplastics Are Mechanically and Ecologically Stable.
FDM can use engineering-grade thermoplastic that results in a more stable product. Thermoplastics, such as PC (polycarbonate), Ultem, and ABS (Acrylonitrile Butadiene Styrene), have high impact strength, thermal stability, and biocompatibility. Production-grade thermoplastic can also be recycled, creating a stable environment and reducing pollution.
3. FDM Technology Makes Complex Shapes and Voids That Would Otherwise Be Impractical or Impossible.
FDM technology’s ability to construct in sections allows it to create complicated structures. The printer may produce several components of the main structure as it extrudes material through the nozzle, binding it in a thin layer. The ability to print complex structures is made possible by the additive replication of structures.
What Are the Limitations of FDM Technology?
FDM technology's limitations include the limited range of materials that can be utilized, the fact that the technology doesn't provide extremely precise details for very small features, and suboptimal print quality. These restrictions are detailed below:
1. The Materials That FDM Can Print.
A constraining factor for FDM in terms of industrial production is the unavailability of more advanced printing materials like glass and ceramics that it can copy. While FDM makes use of engineering-grade thermoplastics, it still lacks the strength and durability that other 3D printing technologies can produce.
2. The Difficulties of 3D Printing Extremely Detailed Objects.
FDM produces parts with low resolution (typically about 100 microns). Its relatively thick layer height only makes it possible to produce parts that do not require small details. A standard nozzle has a size of 0.4 mm, making it impossible for small-size parts. While a nozzle replacement is possible using a size of 0.2 mm, the result still falls short of the precision of parts produced using other 3D printing technologies such as SLS (Selective Laser Sintering) or SLA (Stereolithography).
3. Issues With Finished Product Quality.
FDM-printed parts are anisotropic and can easily break when faced with compressive forces parallel to their layers. Additionally, lines between interfaces of the layers of printed objects may be seen after printing. While these lines can be eliminated using chemical and mechanical polishing processes, this step adds more labor to the printing work.
What Are the Best FDM Technology Printers?
The best FDM printers are:
- Creality Ender 3 V2: The Creality Ender 3 V2 is included in the Ender Series by Creality. This printer is one of the most affordable and user-friendly 3D printers, especially for beginners and hobbyists.
- Ultimaker S3: Although relatively pricey at $4,395, the Ultimaker S3 is a professional desktop 3D printer with high-level features including dual extrusion using print cores, a 20-micron layer resolution capability, and active bed leveling.
- Prusa i3 MK3S+: Prusa Research has resolved difficulties with the earlier MK3S model, namely shifting and first layering issues. The Prusa i3 MK3S+ has a power-back feature, a direct drive filament feeder with a sensor, a dual gear extruder, and an automatic leveling bed.
What Materials Are Used in FDM?
The materials used in FDM are:
- Acrylonitrile Butadiene Styrene (ABS): ABS is a thermoplastic polymer known for high rigidity, good weldability, and high impact resistance. It comes into its own when an increased temperature and toughness are required. ABS is typically utilized in kitchen equipment, surgical applications, and toys (e.g., LEGO blocks).
- Polylactic Acid (PLA): PLA is a brittle biodegradable polymer made from renewable sources like cornstarch and sugar cane. It's mostly adopted in the food industry and in health applications for surgical uses.
- Polyethylene Terephthalate Glycol (PETG): PETG is the modified version of PET. It is known for having good strength and is easy to print with. Engineering companies take advantage of its chemical resistance, moisture retainage, and transparency to build containers, graphic showcasing, and textile products.
- Thermoplastic Polyurethane (TPU): TPU is a type of polyurethane with excellent mechanical properties and rubber-like elasticity. It is commonly used in applications that require flexibility. TPU finds wide use in industries such as automotive, footwear, and sports equipment.
- Nylon (PA): Nylon has good properties in mechanical applications, including high strength and excellent wear and chemical resistance. It is especially used for non-flexible filaments. It gives resistance to unbendable materials.
Which Industries Make Use of FDM Technology?
The industries that use FDM include aerospace, education, and commercial products. Aerospace engineering can build lighter components and fixtures that are cost-effective using FDM. The education sector, on the other hand, uses FDM for affordable experiential learning or project-based learning. Other commercial product industries use the technology for product prototypes and screening before mass production.
Where Is FDM Most Effective?
FDM is most effective in applications that need a quick prototype of a product design to test and alter the product before mass production.
What Is the Difference Between FDM and DLP in 3D Printing?
The difference between FDM and DLP in 3D printing is in the technology used and their applications. FDM produces printed parts that are extruded through a heated nozzle. Applications are seen in technology fields that require higher temperatures like surgical tools, automotive parts, and sporting kits. DLP (Digital Light Processing), on the other hand, creates parts using UV light that is projected onto the build platform to polymerize the layer of the part. DLP is used in products that need fast printing, higher grading, and precision—examples are dental tools and footwear. For more information, see our guide on FDM vs. DLP 3D Printing.
What Is the Difference Between FDM and MJF in 3D Printing?
FDM and MJF are two very different 3D printing technologies. While FDM extrudes a melted thermoplastic to form a part, MJF uses an inkjet to apply a fusing and detailing agent on a powder bed. The powder is then fused by heating elements to create a solid layer. This process is repeated until a part is complete. MJF parts are generally stronger and tougher than FDM printed parts. For more information, see our guide on FDM vs. MJF 3D Printing.
What Is the Difference Between FDM and FFF in 3D Printing?
Fused Deposition Modeling and Fused Filament Fabrication (FFF) are often used interchangeably. This is because FDM and FFF are both examples of material extrusion technology. However, they differ in terms of the resulting part quality and applications. FDM printed parts have better resolution compared to FFF parts. FFF-printed parts tend to have low strength and resolution. For more information, see our guide on FDM vs. FFF 3D Printing.
What Is the Difference Between FDM and PolyJet in 3D Printing?
FDM and PolyJet use different techniques in producing 3D printed parts. FDM heats the filament to build the layers, while PolyJet deposits a layer of liquid photopolymer and cures it during each printhead pass. PolyJet is also more expensive compared to FDM and produces parts with higher resolution and smoother surfaces. For more information, see our guide on FDM vs. Polyjet 3D Printing.
Summary
This article summarized the 3D printing process known as Fused Deposition Modeling (FDM), including what it is, how it works, its advantages, its applications, and how it compares with other 3D printing methods. To learn more about Fused Deposition Modeling 3D printing and how it can be applied in your applications, contact a Xometry representative.
Xometry provides a wide range of manufacturing capabilities, including 3D printing and other value-added services for all of your prototyping and production needs. Visit our website to learn more or to request a free, no-obligation quote.
Disclaimer
The content appearing on this webpage is for informational purposes only. Xometry makes no representation or warranty of any kind, be it expressed or implied, as to the accuracy, completeness, or validity of the information. Any performance parameters, geometric tolerances, specific design features, quality and types of materials, or processes should not be inferred to represent what will be delivered by third-party suppliers or manufacturers through Xometry’s network. Buyers seeking quotes for parts are responsible for defining the specific requirements for those parts. Please refer to our terms and conditions for more information.
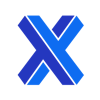