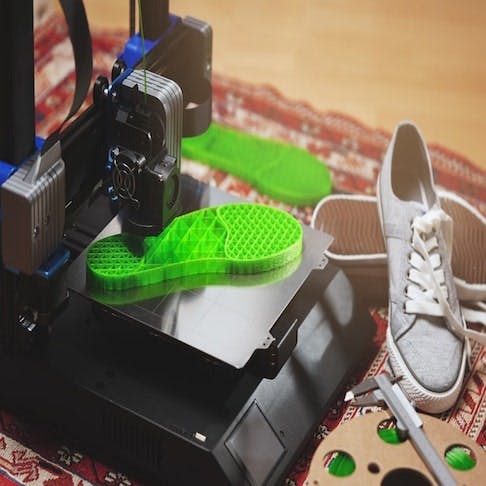
Rapid Prototyping in 3D Printing: Definition, Types, and Methods
Learn all about the process of generating rapid 3D prototypes for products and parts.
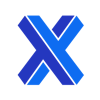
In a time when many products are created to meet customers’ insatiable needs, product developers are looking for ways to improve their manufacturing processes, specifically on the cost or speed of production. This opens up the need for rapid prototyping technologies. Rapid prototyping is the use of a machine (usually a 3D printer) in the actual design and fabrication of production parts. It is a group of techniques that are controlled by computers.
There are different techniques used in rapid prototyping, including additive and subtractive manufacturing and casting. In the 3D printing process, a variety of methods are available, including but not limited to Stereolithography (SLA), Fused Deposition Modeling (FDM), Selective Laser Sintering (SLS), Powder Bed Fusion, and Selective Laser Melting (SLM). This article will discuss what rapid prototyping in 3D printing is, the different types and methods, and how it compares with conventional tooling.
What Is Rapid Prototyping in 3D Printing?
Rapid prototyping in 3D printing is the utilization of 3D printing technology in the design and fabrication of a physical model. This process is quite fast, convenient for time-to-market deliveries, and is an additive manufacturing process. The physical part produced is called a high-fidelity prototype. This means that when examined, the prototype and the finished product have little to no difference. While many other technologies such as casting and CNC machining are known to be relevant for rapid prototyping of designs, 3D printing is preferred by most industries for proof of concept. At this point, it should be noted that a prototype is not an end in itself but a means to an end. The iterations of prototypes culminate in the final production of a fully engineered part. Figure 1 below is an example of a rapid prototyping process using 3D printing:
Rapid Prototyping in 3D Printing
Image Credit: Shutterstock/Pixel B
Types | Description | Differences | Examples |
---|---|---|---|
Types SLA - Stereolithography (SLA) | Description This is the first known method for commercial 3D printing. A bed of photosensitive resin is exposed to ultraviolet light and fused at a various point in a layer-by-layer approach until completion. | Differences Uses a bath of photosensitive resin. | Examples Concept models or cosmetic prototypes. |
Types SLS - Selective Laser Sintering (SLS) | Description This is applicable to both plastics and metals. As the name suggests, a prototype is created by sintering a powder bed with a laser beam one layer at a time. | Differences Uses a powder bed. | Examples Prototypes and end-use parts. |
Types FDM (Fused Deposition Modeling) or Material Extrusion | Description This quite an inexpensive method that uses a spool of thermoplastic filament. This is melted and extruded through a nozzle layer-by-layer until the process is finally complete. | Differences Uses a spool of thermoplastic filament. | Examples For end-use parts. Also included in it uses cases is food and drug packaging. |
Types SLM (Selective Laser Melting (SLM) or Powder Bed Fusion (PBF) | Description This is a highly efficient process and used in most high strength applications. In this process, a fine metal powder is melted one layer at a time until the full solid structure is formed. | Differences Uses a fine metal powder. | Examples Produces medical prosthetics, end-use parts and functional prototypes. |
Types Laminated Object Manufacturing (LOM) or Sheet Lamination | Description A series of thin laminates is created and bonded to one another until the object is completed. The method employs the use of a laser beam or another device that does the work of cutting | Differences Uses adhesive coated plastic, paper, or metal laminates | Examples For prototyping plastic parts. Can create inexpensive yet eye-catching 3D promotional items. |
What Are the Pros and Cons of Rapid Prototyping?
The pros and cons of rapid prototyping relate mostly to the speed and cost of creating a part. One main advantage is that an individual can gain a feel for how the final design will look and operate. This allows improvements and changes to be implemented quite early before final production takes place. The drawback with rapid prototyping is that, sometimes, product developers tend to lavish a lot of attention on a limited prototype. This prevents them from doing a complete analysis of the product to check for its strengths and weaknesses so that the quality of the product may not be compromised. Another benefit of the process is its cost-efficiency. It is an automated process that requires few people to operate.
What is Rapid Prototyping Used for?
Rapid prototyping is used in making physical and digital models. It is a very fast and efficient process that helps in the production of prototypes. Rapid prototyping aids in the assessment of a part for faults or issues that need to be resolved before the final iteration takes place.
What is the Rapid Prototyping Method?
The rapid prototyping method includes the fast production of a physical part using a variety of techniques, including 3D printing (an additive manufacturing process), high-speed machining (a subtractive manufacturing process), injection molding, and casting.
How Does Rapid Prototyping Work?
Rapid prototyping works by:
- Computer-Aided Design (CAD) software generates a digital 3D model of the part. The CAD model is converted into a file format (examples are: STL, OBJ, and DXF).
- Slicing software slices down the 3D model into a series of 2D layered slices.
- The 3D printer interprets these slices in the actual build process until the object is complete.
Supportive structures may be needed in the prototyping model to avoid distortion or warping. Prototypes may require post-processing such as sanding, cleaning, and painting, to achieve a good surface finish.
How to Use Rapid Prototyping?
Rapid prototyping is used to reduce cost and lead time when producing a new product. Prototypes first exist as a concept before a physical validation of the model (called proof of concept) is produced. This enables a team to know where to go in the next step of the iteration process. To maximize a rapid prototyping process, some things have to be considered, including:
- The early stage prototypes are almost always the roughest. They are usually made with different materials and in different colors.
- After the prototype has been identified in its roughest form, the next step is post-processing, which helps improve the quality of the product and meet requirements
- After every process, the prototype is transitioned to a functional prototype: although it may not be fully functional yet. At this stage, prototypes are usually created with materials that will be used in the development of the end product. The performance is assessed to see if it closely matches the desired result. Questions that may arise include: how well does it adapt to a stipulated condition, does it fit at the proposed point in an assembly?
Why Do Engineers Use Rapid Prototyping?
Engineers use rapid prototyping in quickly developing prototype models directly from CAD files. Rather than simply relying on the conceptual framework, engineers can revise their designs based on the feedback from real-world testing. They can see how the final or actual product looks and operates before moving on to mass production.
Is Rapid Prototyping the Same as 3D Printing?
No, rapid prototyping is different compared to 3D printing. Although the words are used interchangeably, technically speaking, they are different. Rapid prototyping is the general term used in quickly developing a prototype with computer-aided software. 3D printing, on the other hand, is the process of constructing 3D models from a CAD model, regardless if they are prototypes or not. This means that 3D printing is merely one of the many processes and methods used for rapid prototyping.
How Does Rapid Prototyping Differ From Conventional Machining?
Rapid prototyping differs from conventional machining in that rapid prototyping is an automated process that allows for the creation of product models. Conventional machining, on the other hand, is a human-controlled process. It is wider in scope than rapid prototyping and uses different machining tools, including turning, drilling, and milling machines.
Summary
This article presented rapid prototyping in 3D printing, explained what it is, and discussed the different types of rapid prototyping. To learn more about rapid prototyping in 3D printing, contact a Xometry representative.
Xometry provides a wide range of manufacturing capabilities, including 3D printing and other value-added services for all of your prototyping and production needs. Visit our website to learn more or to request a free, no-obligation quote.
Disclaimer
The content appearing on this webpage is for informational purposes only. Xometry makes no representation or warranty of any kind, be it expressed or implied, as to the accuracy, completeness, or validity of the information. Any performance parameters, geometric tolerances, specific design features, quality and types of materials, or processes should not be inferred to represent what will be delivered by third-party suppliers or manufacturers through Xometry’s network. Buyers seeking quotes for parts are responsible for defining the specific requirements for those parts. Please refer to our terms and conditions for more information.
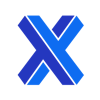