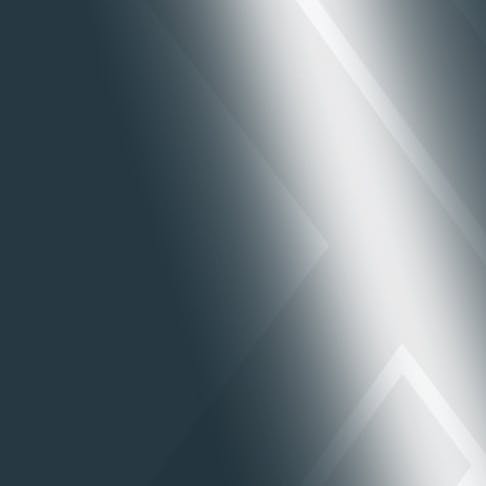
The X-Tiles Video Series: Our Most Popular 3D Printing Processes, Pt. 1
Watch our video series, the X-Tiles, to help you distinguish between our 3D printing processes—SLA, SLS, polyjet, HP Multi Jet Fusion, FDM, DLS, and DMLS—and choose the best process for your project.
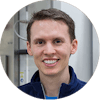
Xometry boasts 11 distinct manufacturing technologies available at the touch of a button. Of these, 7 are additive manufacturing processes--also known as 3D Printing. There is often much confusion around the differences between each process and how the final prints differ in outcomes
I have put together a series of videos, called the X-Tiles, to help you distinguish between SLA, SLS, poly jet, HP Multi Jet Fusion, FDM, DLS, and DMLS and choose the best process for your project. And yes, you guessed it, our X-tiles are inspired by the famous X-Files TV series.
What is an X-Tile? We took the ‘X’ from our Xometry logo and designed a custom part that is about 1.5 inches square. It has flats as well as angled surfaces. The tile is producible in multiple manufacturing processes and acts as a good comparison part for material finishes and cosmetic features like layers.
The first three videos of the series bite-sized—ranging from 2 to 4 minutes—and you can watch them below. They answer some of the most common questions regarding choices in similar 3D printing processes.
In the video below, I compare 3D printed 17-4 stainless steel and aluminum alloy (AlSi10Mg). Beyond the mechanical characteristics, it is important to be mindful of extra thermal effects that occur with aluminum. Because aluminum has a much higher thermal conductivity compared to steel, gaps and thin features may be slightly larger on the print. I recommend an offset of 0.002”-0.004” on critical surfaces to mitigate this effect on aluminum DMLS parts.
SLS and HP MJF are two processes that use identical base materials and would be considered powder bed fusion additive manufacturing. In the video below, I show how SLS white nylon can be dyed in both black and non-black colors but the inherent grey finish of HP MJF can only be dyed black. However, MJF is jet black on the inside and shows less cosmetic issues if scratched during use. SLS tends to be more cost-competitive at lower quantities, but MJF can often become more economical in scale due to efficiencies in the process.
SLA typically is used to simulate an engineered plastic, and polyjet is best used to simulate the feel of a part such as an overmold. In the video below, Greg shows how SLA has more diversity of individual materials, including clear options that can be post-processed further. Polyjet’s strength is its ability to print in Shore A durometers and do multi-material projects.
If you have a suggestion for an X-Tile spotlight or comparison, let us know! Subscribe to Xometry’s YouTube page to get the latest video content as it comes out!
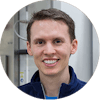