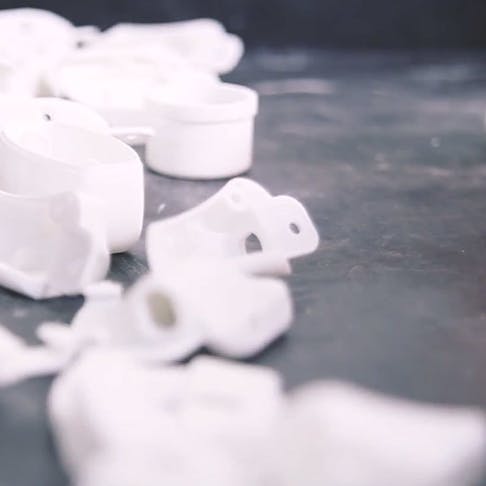
All About Selective Laser Sintering (SLS) 3D Printing
Learn more about the process of selective laser sintering, SLS, including materials used and its pros and cons.
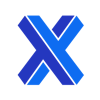
SLS (Selective laser sintering) is a powder bed fusion (PBF) 3D printing technology that makes use of a relatively high-powered laser to sinter plastic particles into a final part. SLS primarily works with nylon powders in a limited range of colors such as black, white, and gray. This technology does not require support material and can print very quickly. However, the materials available are limited and the cost of the technology is high.
An SLS printer consists of a laser, a laser scanning mirror, a heated print bed, a recoater to distribute the powder, and a material handling system to distribute powder to the system. This article will describe what SLS 3D printing is, how it works, as well as the pros and cons of the technology.
What is Selective Laser Sintering 3D Printing?
Selective laser sintering (SLS) is a PBF 3D printing technology. This technology makes use of a laser to sinter plastic particles together layer by layer until the 3D printed part is complete. SLS typically works with plastics and does not require any support structures as the powder itself provides sufficient support.
How Does Selective Laser Sintering 3D Printing Work?
Selective laser sintering works by first distributing a thin layer of plastic particles on the bed plate which is heated to just below the melting temperature of the plastic. This plastic is distributed by a recoater that lays down a layer of material at the desired thickness. A laser is then directed into a scanning mirror to trace out the part’s cross-section and sinter the particles together. After a layer is complete, the print bed moves down and another layer of powder is deposited onto the previous one. The process repeats until the part is complete.
What Are the Pros and Cons of SLS?
Table 1 below lists the pros and cons of SLS 3D printer technology:
Pros | Cons |
---|---|
Pros SLS parts do not need support material as the powder itself supports the material. This makes it easy to print internal volumes provided there is a path for the powder to be drained after printing. | Cons SLS has a relatively limited range of available materials when compared to other technologies like FDM (Fused Deposition Modeling). Nylon, polystyrene, and TPU are possible materials for SLS with nylon being the most commonly used. |
Pros While SLS generally uses white, black, or gray nylon, the parts can be dyed after printing to various different colors. | Cons SLS parts are porous, as the individual plastic particles are not completely melted into a homogenous mass but are rather sintered together at the particle extremities, leaving voids in between. |
Pros SLS parts can have very fine, highly detailed features. This output is due to the focal point of the laser being so small; features as small as 0.75 mm can be printed. | Cons Only 50% of the unspent powder used during printing can be recycled. This means that over time some material must be discarded making SLS relatively wasteful when compared to other technologies like FDM or SLA (stereolithography). |
Pros SLS printing is very fast when compared to technologies like FDM and even SLA, as each layer can be sintered almost instantly. | Cons SLS printing technology is costly compared to SLA and FDM whose core technologies are not as specialized—as it needs a laser to sinter the material. |
What Are the SLS Printing Materials?
SLS has a limited number of available materials, with nylon being the most commonly used. Listed below are the various materials available:
- Nylon/PA11: This material is tough, with good impact resistance. PA11 has higher temperature resistance than PA12 and can undergo higher levels of deformation before breaking when compared to PA12.
- Nylon/PA12: This material is rigid, with high strength, good chemical resistance, and biocompatible. PA12 has lower thermal resistance when compared to PA11. PA12 is the most commonly used material in SLS printing.
- Filled Nylon: PA11 and PA12 can have their properties modified with the inclusion of fillers like glass and carbon fiber which improve thermal and mechanical properties.
- Castable Polystyrene: This material is designed to be used as a master part for vacuum forming and sand casting. It has low toughness and a low melting point and is not intended for functional parts.
- TPU Elastomer: This material has rubber-like flexibility, with good toughness and abrasion resistance. It can also be modified to have different hardnesses on the shore A scale.
What Are the Primary Parts of an SLS 3D Printer?
The different parts of a 3D SLS printer are listed below:
- Laser: The laser (typically a CO2 laser) is used to sinter the plastic particles into each other. The laser is directed using a scanning mirror which directs the laser to trace out the layer cross-section.
- Material Delivery System: The material delivery system stores all the powder. As the part is built, this mechanism supplies material to the recoater.
- Recoater: The recoater drags material from the powder delivery system and lays it out onto the print bed/preceding layers.
- Print Bed: The print bed moves down as the part is printed, typically between 50 and 200 microns per layer depending on the required resolution. A thin layer of plastic is placed on the print bed for each new part layer by the recoater.
- Heaters: Heaters keep the build volume at an elevated temperature to assist with the sintering process by reducing the energy required by the laser to sinter the powder.
What Are the Best SLS 3D Printing Resins?
SLS has a limited range of 3D printing materials; however, the best of these are listed below:
- PA12 (Nylon): PA12 offers a good range of mechanical, thermal, and chemical resistance properties making it the ideal material for a wide range of applications. PA12 is the most commonly used material for SLS printing.
- PA12CF (Nylon): Carbon-filled nylon significantly improves the stiffness, strength, and hardness of the base nylon and can allow for the creation of high-performance parts with an excellent strength-to-weight ratio.
- TPU Elastomer: TPU elastomer allows for the creation of flexible parts with good abrasion resistance and toughness.
How is SLS 3D Printing Used in the Medical Industry?
SLS 3D printing is used for custom-fit prostheses based on 3D scans of a patient’s body. SLS 3D printing is also used to create patient-specific reference models based on 3D scans for surgical procedure planning.
How is SLS 3D Printing Used in the Jewelry Industry?
SLS 3D printing is used to create highly detailed models not possible using other methods. These models are used for creating casting molds. Specifically, materials like polystyrene can be printed and used to create molds for casting precious metals.
Are SLS Printers Capable of Producing Large, Detailed Pieces?
Yes, SLS printers have large build volumes that can accommodate sizable parts. The use of a precision laser still allows for fine details to be incorporated into very large parts.
What is the Difference Between SLS and SLA?
SLS (selective laser sintering) makes use of a laser to sinter plastic particles, whereas SLA (stereolithography) uses a laser to selectively cure a liquid photopolymer. Both technologies can produce highly detailed parts and their print speeds are comparable. For more information, see our guide on SLS vs. SLA.
Summary
This article presented selective laser sintering (SLS), explained what it is, and discussed the process and the materials used for SLS. To learn more about selective laser sintering, contact a Xometry representative.
Xometry provides a wide range of manufacturing capabilities, including 3D printing and other value-added services for all of your prototyping and production needs. Visit our website to learn more or to request a free, no-obligation quote.
Disclaimer
The content appearing on this webpage is for informational purposes only. Xometry makes no representation or warranty of any kind, be it expressed or implied, as to the accuracy, completeness, or validity of the information. Any performance parameters, geometric tolerances, specific design features, quality and types of materials, or processes should not be inferred to represent what will be delivered by third-party suppliers or manufacturers through Xometry’s network. Buyers seeking quotes for parts are responsible for defining the specific requirements for those parts. Please refer to our terms and conditions for more information.
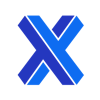