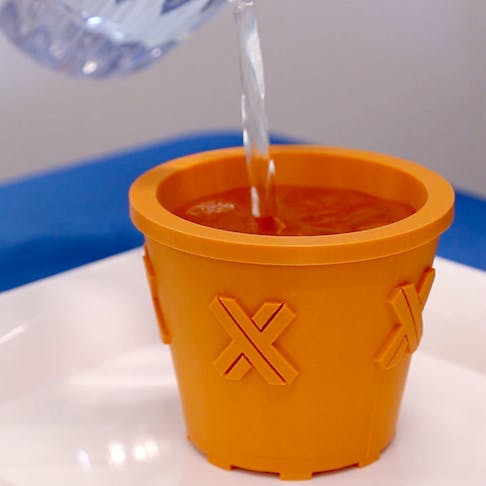
Fused Deposition Modeling vs Selective Laser Sintering Watertightness Test
Will It Leak, or Won’t It?
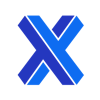
Each additive manufacturing process has its strengths and weaknesses. In our latest video, Director of Project Engineering, Greg Paulsen, puts two 3D Printing processes to the test to see which is better for liquid-tight application: Fused Deposition Modeling (FDM) or Selective Laser Sintering (SLS).
FDM parts start as a plastic filament. The filament is extruded out of a heated end, laying down in a zig-zag pattern to create the shape of the part from the bottom to the top. FDM technology can be used for rapid prototyping and is widely known for its speed, accuracy, and competitive cost.
SLS parts begin very differently as a fine nylon powder that is heated by a laser. The heat fuses the powder together, layer by layer, to create a finished part. SLS technology is highly accurate and can also be utilized for rapid prototyping as well as end-use, low-volume production.
Watch the video to find out which part leaks and which doesn’t in our Fused Deposition Modeling vs Selective Laser Sintering Watertight Test!
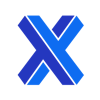