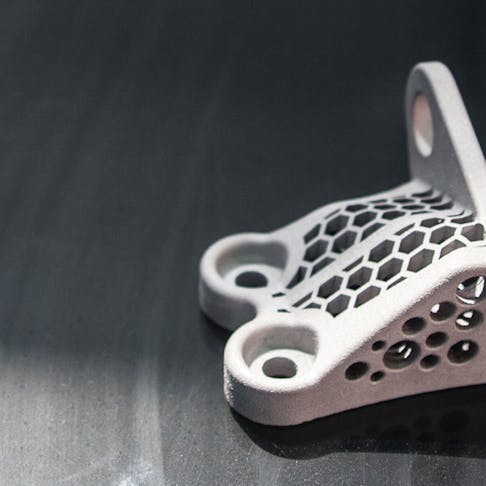
All About Direct Metal Laser Sintering (DMLS) 3D Printing
Learn more about this process for creating metal parts using a 3D printer.
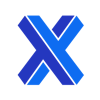
Direct Metal Laser Sintering (DMLS) 3D printing is a metal-based manufacturing technology used to create complex metal parts. It uses a range of materials that include anything from copper to Inconel®. The aerospace, medical and turbomachinery industries are some notable users of the technology. DMLS was first introduced into the market in 1995 by a German company called EOS (Electro Optical Systems).
This article will describe how DMLS works, its advantages and disadvantages, as well as some of the key materials used. We will also review the best metal printing technologies currently on the market. Some typical parts that can be manufactured with DMLS are shown in Figure 1 below:
Close up of metal 3D printed object.
Image Credit: Shutterstock.com/MarinaGrigorivna
What Is Direct Metal Laser Sintering 3D Printing?
A DMLS 3D printer is a powder-bed fusion technology. It is used to manufacture metal parts by directing a high-powered fiber laser beam at a single, thin layer of metal powder and fusing an outline of that layer onto the previous layers. The process is repeated for every successive layer until the entire metal part has been printed, one layer at a time with each layer melted into the previous one. DMLS printing is often incorrectly referred to as a sintering technology. According to EOS, DMLS is a German acronym that stands for “Direkt Metall Laser Schmelzen.” Schmelzen'' means "melt," not "sinter." In spite of the English name of the process, Direct Metal Laser Sintering does not sinter the metal powder. It melts the metal particles together to form the part.
What Is Direct Metal Laser Sintering Used For?
Direct Metal Laser Sintering (DMLS) is used for the serial manufacture of complex industrial metal components that cannot be made economically—or at all—with other metal manufacturing technologies, such as CNC machining or metal injection molding. When parts are manufactured using traditional subtractive processes, they often need to be assembled from multiple components. However, DMLS 3D printing can create a monolithic part that eliminates the inherent weaknesses and complexities of assembled parts. DMLS printing is most often used in the aerospace, medical, turbomachinery, and automotive industries.
How Does DMLS 3D Printing Work?
DMLS printers work by selectively melting a metal or metal alloy powder with a high-powered (up to 1000 W) fiber laser beam. The laser beam scans the cross-section of a part layer and melts the metal powder particles together. Some machines have up to four independent lasers that can all operate on the same layer simultaneously, effectively quadrupling the print speed.
Once a layer is complete, the print bed moves down, and another layer of metal powder is transferred to the print bed with a powder recoater. The DMLS system then fills the build chamber with an inert gas to prevent oxidation during printing. Once the complete part is printed, any support material must be removed.
How Fast Is DMLS 3D Printing?
The speed of a Direct Metal Laser Sintering printer is limited by how quickly the optical mirrors can be repositioned. This speed is often referred to as the “scanning speed," which indicates how quickly the laser can move across the powder bed to melt the metal particles. DMLS printers have a scanning speed of ~7 m/s. The largest DMLS machines have four lasers and can thus print in four locations simultaneously. This dramatically improves machine productivity and print speed.
How Accurate Is Direct Metal Laser Sintering?
The accuracy of a laser-based powder-bed fusion printer depends primarily on the quality of the optical components and the accuracy of its laser. The typical fiber laser used on DMLS machines has a focal point from 40 to 100 microns in diameter, depending on the machine. This means that the smallest theoretical feature size is 40 microns.
What Material Is Used in the DMLS 3D Printing Process?
Direct Metal Laser Sintering (DMLS) can be used with a wide variety of materials. The most common are listed below:
- Aluminum Alloys (AlSi10Mg): This aluminum alloy is typically used for casting applications. It can be used on components with thin walls and fine features. This alloy also has good mechanical and thermal properties.
- Inconel® 718: Inconel® is a nickel superalloy often used in the aerospace industry, where it is useful for its ability to maintain high strength at extremely high temperatures. It is also highly corrosion resistant.
- Titanium (Ti6Al4V): This titanium alloy has excellent mechanical and corrosion resistance properties. In addition, it is biocompatible, making it ideal for medical implants.
- Stainless Steel (316L): 316L is a very corrosion-resistant material. It is used extensively in industrial acid-producing facilities, specifically in handling sulphuric acid.
- Copper: Copper has excellent thermal and electrical conductivity. It is often used for heat exchangers and induction coils. Copper (Cu) and some copper alloys like CuCP and CuCrZr can be printed on DMLS printers.
- Case-Hardening Steel (20MnCr5): This material can be case hardened after printing. That makes it ideal for applications requiring superior wear resistance, such as gear wheels.
- Cobalt-Chrome (CoCr): This CoCr alloy family has excellent corrosion resistance and maintains its mechanical properties at elevated temperatures. It is a nickel-free alternative to Inconel®. It is also biocompatible and used for components in gas turbines and orthopedic implants.
What Type of Laser Is Used in DMLS?
Direct Metal Laser Sintering makes use of fiber lasers. For the largest machines, up to four fiber lasers are used during printing to increase productivity. Unlike CO2 lasers, fiber lasers have no moving parts and are therefore maintenance-free. Fiber lasers can also produce a very small focal point diameter of 40 microns. The beam power ranges from 200 to 1000 W, depending on the machine.
What Is the Size of Metal Particles Produced in DMLS?
Direct Metal Laser Sintering 3D printing makes use of fine metal powder as its raw material. The typical size of the metal particles is around 20 to 80 microns in diameter. This powder is manufactured using a gas atomization process, during which a metal starting material is melted and then ejected from a nozzle into a stream of high-pressure gas. The molten metal is thus atomized into small particles. This is a high-energy process, which is part of the reason why metal powders for 3D printing are so expensive.
What Are the Advantages of Direct Metal Laser Sintering?
Direct Metal Laser Sintering is one of the most mature and efficient metal printing technologies. Listed below are some of its key advantages:
- DMLS is capable of printing high-strength functional metal parts in a wide variety of metals.
- It is possible to print mixtures of plastic (nylon) and metal (aluminum).
- DMLS is a high-resolution printing process that can produce very small feature sizes. This is because the DMLS laser beam can be as narrow as 40 micrometers.
What Are the Disadvantages of Direct Metal Laser Sintering?
Despite its many advantages, Direct Metal Laser Sintering has the following disadvantages that must be considered:
- DMLS parts need support during printing. This is due to the mass of the metal parts.
- DMLS parts can have internal stresses due to the high-temperature manufacturing process. Removing these internal stresses during printing requires multiple test samples and additional characterization. Alternatively, post-print heat treatment can also remove these stresses. However, both of these processes ultimately result in a higher cost per part.
- DMLS makes use of lower-powered lasers compared to SLM and EBM machines. Therefore, it produces a smaller melt pool and cannot print very high layers. This ultimately results in slower prints and, therefore, higher cost per part.
What Is the Difference Between DMLS and SLM 3D Printing?
Both DMLS and SLM are powder-bed fusion printing technologies. SLM makes use of higher-power lasers, can handle bigger parts, and can incorporate up to 12 lasers. Thus, SLM is better suited to high-volume production, whereas DMLS is better suited to smaller volumes and more highly detailed parts. For more information, see our guide on DMLS vs. SLM 3D Printing.
What Is the Difference Between DMLS and EBM 3D Printing?
Both DMLS and EBM are powder-bed fusion printing technologies. The key difference is that EBM makes use of an electron beam to melt the metal powder. EBM also prints inside a vacuum chamber that enables it to print with materials with very high melting temperatures without the risk of oxidation. DMLS gets around this challenge by printing in an inert gas atmosphere. For more information, see our guide on DMLS vs. EBM.
What Is the Best Metal 3D Printer?
There are three leaders in the metal 3D printing space. Their flagship machines are listed below:
- SLM Solutions: The NXG XII 600 is a metal printer with an extremely high production rate. It is specifically designed for serial production. This machine allows metal printing to be a true contender to subtractive technologies like CNC machining.
- EOS: The M 100 is a highly accurate printer that can produce parts made from a wide range of materials. It makes use of a fiber laser with a focal point diameter of 40 microns. The M 100 can therefore produce highly accurate parts.
- GE Additive: The EBM Q20 Plus is an EBM (Electron Beam Melting) machine specifically designed for producing high-quality aerospace components. GE owns the technology behind EBM 3D printing. This technology can print metal parts made from materials with very high melting temperatures. The EBM process produces parts with negligible residual stresses reducing the need for expensive post-processing.
To learn more, see our guide on the Best Metal 3D Printers.
Summary
This article summarized the Direct Metal Laser Sintering (DMLS) 3D printing process, including how it works, its advantages, limitations, and materials used. To learn more about how Direct Metal Laser Sintering 3D printing technology can be leveraged to produce top-quality metal parts, contact a Xometry representative.
Xometry provides a wide range of manufacturing capabilities, including 3D printing and other value-added services for all of your prototyping and production needs. Visit our website to learn more or to request a free, no-obligation quote.
Copyright and Trademark Notices
- Inconel® is a registered trademark of Huntington Alloys division of Special Metals Corp., Huntington, WV.
Disclaimer
The content appearing on this webpage is for informational purposes only. Xometry makes no representation or warranty of any kind, be it expressed or implied, as to the accuracy, completeness, or validity of the information. Any performance parameters, geometric tolerances, specific design features, quality and types of materials, or processes should not be inferred to represent what will be delivered by third-party suppliers or manufacturers through Xometry’s network. Buyers seeking quotes for parts are responsible for defining the specific requirements for those parts. Please refer to our terms and conditions for more information.
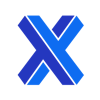