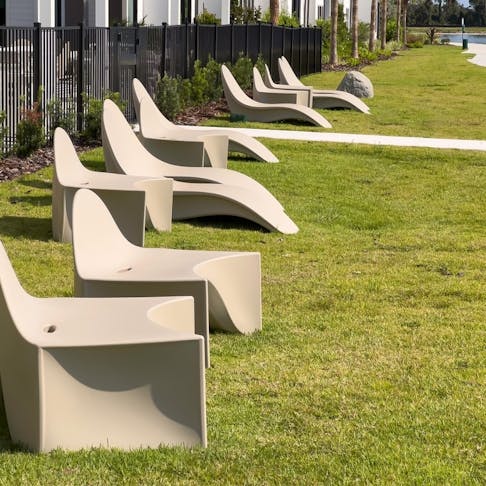
Rotational Molding: Definition, Process, and Advantages
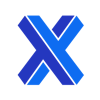
Rotational molding, also known as roto molding, is a versatile manufacturing process used to create hollow plastic products. It entails filling a mold with plastic resin powder and then heating and rotating that mold until the plastic melts and uniformly coats the interior of the mold. It continues turning until the plastic cools and solidifies. Figure 1 below is an example of a rotational molding process:
This innovative manufacturing process has several benefits, including: consistent wall thickness, superior strength and durability, multi-layered configurations, and a capacity to create large, intricate parts. Rotational molding is used across a variety of industries. This article will explain why by examining rotational molding in greater detail.
What Is Rotational Molding?
Rotational molding is an innovative manufacturing technique that starts by filling a heated mold with plastic material. Hollow components are formed by rotating the mold around two perpendicular axes. This causes the molten plastic to spread evenly and stick to the mold’s interior walls. A uniform thickness throughout is ensured by the mold's continuous rotation during both the heating and cooling phases, preventing any unwelcome sagging or deformations. This technique can produce hollow plastic products with consistent wall thicknesses, intricate geometries, and exceptional strength.
Rotational Molding Process
Image Credit: https://en.m.wikipedia.org/wiki/Rotational_molding
What Is Another Term for Rotational Molding?
Rotational molding is also known as roto molding, roto casting, or roto mold. In all cases, the process is the same: plastic powder is put into a mold designed to rotate on multiple axes. When heated, the plastic melts and coats the interior surface of the mold to form the desired shape. Rotomolding is renowned for its affordability and capacity to create sizable plastic components with uniform wall thickness.
What Is the History of Rotational Molding?
The history of rotational molding, or roto molding, can be traced back to 1855. British manufacturer R. Peters utilized biaxial rotation and heat to produce hollow metal artillery shells and other vessels. The process was later adapted for plastics around 1950 for manufacturing doll heads. Since then, roto molding has evolved and expanded to become a common and versatile method for producing plastic products.
What Is the Primary Purpose of Rotational Molding?
The primary purpose of rotational molding is to produce parts with high-quality finishes, uniform wall thicknesses, and excellent stability. This manufacturing process allows inserts and spin weld attachments to be directly added to the rotomolded product.
What Is the Process of Rotational Molding?
The process of rotational molding can be described as follows:
- Fill the hollow mold with powdered plastic resin.
- Initiate bi-axial rotation of the mold.
- Transfer the rotating mold into an oven.
- Maintain the rotation while the resin melts and evenly coats the inner walls of the mold.
- Cool the rotating mold to allow the resin to harden and take the desired shape.
- Stop the rotation and open the mold.
- Carefully remove the finished part from the mold.
What Are the Types of Equipment Used for Rotational Molding?
The equipment used for rotational molding includes the following types of machines:
- Turret Machines: Turret machines usually have three to six rotating arms on the platform. Each arm has a mold at the end of it to move it through the various stages of the molding process. Each mold is given an equal amount of heat exposure as the turret machine rotates, ensuring uniform heating and consistent product quality.
- Rock and Roll Machines: A rock and roll machine is specifically designed to mold very large items. It includes a tilting oven which allows for efficient and precise shaping. Moreover, these machines boast the advantage of automatic cart movement, streamlining the manufacturing process.
- Clamshell Machines: Clamshell machines, used in low-volume manufacturing, each feature an oven and a single arm. Perhaps because of their simplicity and compact footprint, they remain common in current rotational molding facilities. They offer an ideal solution for locations with limited space.
- Open-Flame Machines: Open-flame machines are ideal for producing cylindrical parts such as tanks, benefiting from a close and consistent distance between the burners and the mold. This setup ensures efficiency and cost-effectiveness by optimizing gas consumption.
- Shuttle Machines: The shuttle rotational molding machine incorporates a central oven, two carts, and two stations featuring offset or straight arms. It provides a favorable combination of: productivity, cost-efficiency, seamless mold changing, and the versatility to operate with either one or two stations.
What Materials Are Used for the Rotational Molding Process?
Some of the materials used for rotational molding include:
1. Aluminum
Aluminum is a lightweight, durable material known for its excellent thermal conductivity and strength-to-weight ratio. Aluminum is less common in rotational molding than polymers due to its cost and the limited availability of suitable aluminum powders. For more information, see our guide on the Properties of Aluminum.
2. Polyethylene
Polyethylene is a versatile thermoplastic used extensively in rotational molding. It provides excellent impact strength, chemical resistance, and ease of processing. On the downside, it is not as stiff or heat-resistant as many other materials. For more information, see our guide on Polyethylene Properties.
3. Polyester
Polyester is a synthetic polymer known for its dimensional stability. It is simultaneously strong and resistant to heat and chemicals. However, it typically has a higher cost and may require additional processing steps. For more information, see our guide on the Properties of Polyester.
4. Polypropylene
Polypropylene, a thermoplastic renowned for its toughness and chemical resistance, delivers notable impact resistance, stiffness, and dimensional stability. Unfortunately, it has trouble with heat and impacts, especially compared to materials like ABS. For more information, see our guide on PP Material.
5. Nylon
Nylon is a synthetic polymer recognized for its strength and toughness. It offers excellent wear resistance, impact strength, and dimensional stability. Unfortunately, it is characterized by relatively high prices and may necessitate specialized processing equipment. For more information, see our guide on Nylon Plastic Material.
6. Silicone
Silicone is a versatile elastomer, renowned for its flexibility and temperature resistance. It’s durable and resists both heat and adverse weather conditions. Those traits make it more expensive than natural rubber, though. For more information, see our guide on the Uses of Silicone.
7. Polycarbonate
Polycarbonate is a transparent thermoplastic that is widely recognized for its impact resistance. It is often used as a substitute for glass due to its exceptional strength, clarity, and dimensional stability. However, polycarbonate may require additional precautions, such as UV stabilizers or coatings, to prevent yellowing or degradation when exposed to sunlight. For more information, see our guide on All About Polycarbonate (PC).
How Long Does the Rotational Molding Process Take to Complete?
A single rotationally molded part can take up to three hours to complete when the mold is rotated at a speed of 8 rotations per minute. This duration allows the polymer material inside the mold to evenly coat all surfaces and cool enough to maintain its final form and wall thickness.
What Are the Factors That May Affect the Rotational Molding Process?
Factors that can affect the rotational molding process include:
- Draft Angles: Draft angles make parts easier to remove from their molds. The angles help release the part and compensate for shrinkage during the cooling process.
- Wall Thickness: Wall thickness affects the design in terms of part strength and mass. It also impacts the heat transfer rate and heating and cooling time during manufacture. For PE (polyethylene) applications in rotational molding, a typical wall thickness runs between 0.125 and 0.25 inches.
- Large Flat Surfaces or Parallel Walls: Large flat surfaces easily become distorted, so additional features like recesses or steps are often added to break them up. Parallel walls must be properly spaced to allow for proper material flow and to avoid thinning of walls.
- Material Flow around Corners: Corner radii play a crucial role in ensuring smooth material flow during the molding process. Sharp corners can lead to issues such as bridging or uneven distribution of material.
- Aesthetics: Designers also consider aesthetic factors to meet customer expectations, incorporating details and features into the design phase to achieve the desired appearance.
What Are the Applications of Rotational Molding Products?
Rotational molding products find applications in various sectors. Some common applications include:
- Storage tanks and containers.
- Automotive components such as fuel tanks and fenders.
- Playground equipment.
- Portable barriers.
- Agricultural tanks and equipment.
- Carts and carriers.
- Watercraft and marine products.
- Environmental and waste management products.
- Water treatment and containment components.
- Industrial and material-handling products.
Get started on a new Rotational Molding Quote.
What Are the Common Defects of Rotational Molding Products?
Common defects in rotational molding products include:
- Shrinkage and Deformation: Residual stress during cooling can cause the plastic to shrink and deform. Proper cooling methods and structural design can mitigate these defects.
- Reduced Impact Strength: Factors like heating temperature and time, cooling speed, particle size, mold, and material influence impact strength. A recise mold layout is required to maintain the parts' impact resistance and prevent other design flaws. Sharp corners, inadequate draft angles, issues with material flow, and flat walls are all design flaws that can compromise the usability and quality of rotomolded products. Designers should include rounded corners, suitable draft angles, enough room for material flow, and structural elements for flat surfaces to prevent these problems.
- Bubbles and Perforations: Bubbles that form in the plastic during the melting or bonding phases will impact both the part’s appearance and its mechanical properties.
What Is the Lifespan of Rotational Molding Products?
Rotational molding products' lifespans can vary depending on variables like application, material, and environmental conditions. However, rotational molding products generally last for a very long time with proper use and maintenance. Storage tanks, playground equipment, automotive parts, watercraft, agricultural tanks, and numerous other custom-made goods last for many years.
Is Rotational Molding Sustainable?
In the strictest sense, no, rotational molding is generally not sustainable because its raw materials are non-renewable plastics made from petroleum. Compared to many plastic forming techniques, though, it is less environmentally hazardous. The process does not release harmful chemicals, creates minimal material waste, and requires less fuel compared to other methods. The plastic that goes into roto-molded parts is also often recycled and/or recyclable, thus reducing the need for virgin raw materials and limiting the carbon footprint.
How Thick is the Rotational Molding Product?
The thickness of rotational molding products can vary depending on their specific applications and design requirements. Generally, wall thicknesses range from 1/32 to 1 inch (0.8-25 mm). The resins used in rotational molding are typically supplied in powder form, ground to 35 mesh, with particle diameters ranging from 74-2000 microns. Overall part thickness depends upon the function, material characteristics, and structural requirements that went into the design.
What Are the Advantages of Rotational Molding?
Here are some of the advantages of rotational molding:
- The rotation ensures a consistent coating of mold walls, resulting in even wall thicknesses throughout the molded product.
- Low molding pressures mean molds can be made from inexpensive metals like aluminum.
- It enables the production of complex double-walled open containers without the need for additional post-processing steps.
- The seamless, one-piece construction of rotationally molded parts eliminates the need for joining techniques, resulting in stronger and more durable products.
- With the absence of external pressure, rotational molding enhances the material stability during the molding process, reducing the likelihood of defects in the final product.
What Are the Disadvantages of Rotational Molding?
Some disadvantages of rotational molding include:
- The process demands materials with a certain level of thermal stability. Specialized additives and grinding processes for the powder help in this regard, but also drive raw material prices higher.
- Tooling for rotational molding can be expensive, especially for large or custom molds.
- This method typically has longer production cycles compared to other molding processes, which can impact time-to-market.
Is Rotational Molding Expensive?
No. Rotational molding can be considered an affordable process compared to other molding techniques. The initial investment in rotational molding machines is relatively low. The inherent production flexibility also lets you mold large products or multiple products simultaneously. Additionally, a case study that compared rotational molding versus blow molding for 50-gallon trash cans showed that the former was far cheaper. The tooling cost for rotational molding was $20,000 compared to blow molding at $210,000. The tooling maintenance cost for rotational molding was also lower ($1,000/year compared to $5,000/year).
Is Rotomolding Cheaper Than Injection Molding?
Yes, roto molding is generally cheaper than injection molding. The low-pressure process of roto molding means the molds can be made of less expensive materials. There is also no need for high-pressure pumps or heavy-duty hydraulics. This cost advantage makes roto molding the best option in terms of up-front manufacturing costs. For more information, see our guide on Mold Processing.
What Is the Difference Between Rotational Molding and Compression Molding?
Compression molding and rotational molding are two separate processes intended for different materials. The materials that go into rotational molds must be capable of melting and reforming when they’re reheated. Thermoplastics and metals fit this bill, but thermoset polymers do not. Compression molding can produce thermoset items that are similar in appearance, but which are put under higher pressure and cannot be reshaped once the process is completed.
Summary
This article presented rotational molding, explained what it is, and discussed its various applications. To learn more about rotational molding, contact a Xometry representative.
Xometry provides a wide range of manufacturing capabilities, including injection molding and other value-added services for all of your prototyping and production needs. Visit our website to learn more or to request a free, no-obligation quote.
Disclaimer
The content appearing on this webpage is for informational purposes only. Xometry makes no representation or warranty of any kind, be it expressed or implied, as to the accuracy, completeness, or validity of the information. Any performance parameters, geometric tolerances, specific design features, quality and types of materials, or processes should not be inferred to represent what will be delivered by third-party suppliers or manufacturers through Xometry’s network. Buyers seeking quotes for parts are responsible for defining the specific requirements for those parts. Please refer to our terms and conditions for more information.
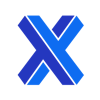