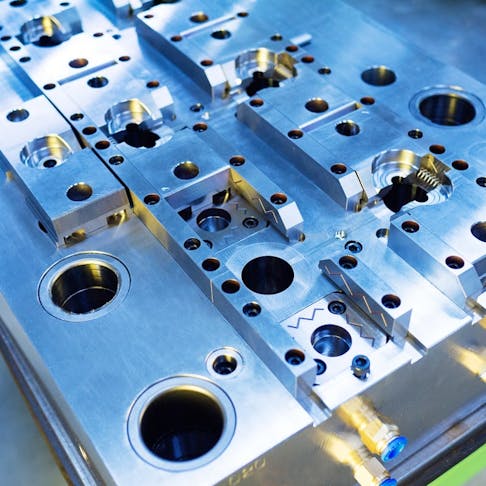
Conformal Cooling: What It is and Why to Use It
Understand the benefits and uses of this process in injection molding.
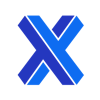
Conformal cooling is a way to cool plastic parts, typically during the injection molding process. This method of cooling was developed to remove heat evenly from complex parts. By using metal 3D printing to manufacture the cooling channels, they can be custom designed and manufactured to closely conform to the shapes of even the most complex part geometries.
With conformal cooling, cooling channels are placed close to the corners and cored-out features of the part. This design is nearly impossible to achieve with conventional methods, like milling or drilling. Evenly distributed curved channels are wrapped strategically around the part to cool the sections that are hard to reach and usually difficult to cool. The channels can also be designed to easily accommodate features like ejector pins or attachment screws while maintaining a constant distance from the mold surface. Overall, conformal cooling allows for faster cooling times, better cooling efficiencies, improved part quality, and cost reductions.
This article will further describe conformal cooling, discussing how it works, its importance, and its limitations.
What is Conformal Cooling?
Conformal cooling is a technique that incorporates custom cooling channels into the tools used in plastic injection molding or blow molding processes. The cooling channels can be specifically designed to match part geometries for more effective and uniform cooling. Pairing conventional cooling with injection molding can reduce cycle times by 10 to 40%, and sometimes even up to 70%.
How Does Conformal Cooling Work?
Conformal cooling works by circulating a coolant through channels designed into injection molds for plastic parts. The coolant can be either liquid or gas, depending on the application’s requirements. Liquid conformal cooling is used with plastic injection molding materials that cannot withstand high temperatures or that require fast cycle times. Gas conformal cooling, on the other hand, is used for less demanding applications, where the material being molded has higher temperature resistance, and/or longer cycle times are used (i.e., polycarbonate). While water is used as a coolant for most applications, oil is used when the mold should be chilled at temperatures close to or above the boiling point of water. If the mold needs to be cooled at low temperatures (below the freezing temperature of water), a mixture of ethylene glycol and water is typically used. For gas coolants, air can be used, but this is not as efficient as the other coolant options (e.g., water).
Why Should You Use Conformal Cooling?
Conformal cooling is used because it outperforms conventional cooling methods in terms of cooling speed, part quality (less warpage), process efficiency, and cost. With conformal cooling, cycle times are typically reduced by 10 to 40%, and sometimes even up to 70%. It also addresses the limitations of conventional cooling by providing uniform, effective cooling of complex part geometries. For more information, see our guide on Plastic Injection Molding.
Why is Conformal Cooling Important for Injection Molding?
Conformal cooling is important for injection molding because it promotes faster cooling and more uniform temperature control. This faster cooling and uniform temperature control results in improved injection molding process performance in terms of both the production rate and the quality of the plastic parts. Conformal cooling in injection molding outperforms simpler straight cooling channels created with drilling machines. The uniform temperature distribution produced by conformal cooling results in better quality parts and less warpage. Sink marks, weld lines, and differential shrinkage are also minimized with conformal cooling. In addition to these benefits, conformal cooling reduces the overall cycle time and has the potential to increase productivity while reducing production costs, raw material usage, and energy consumption of injection molding processes.
Which Injection Molding Part Should Be Cooled Conformally?
Conformal cooling is ideal for plastic parts with complex geometries (parts with thin walls and intricate features) that are difficult to cool evenly. Uniform cooling minimizes the chance of part defects in these complex designs. Conformal cooling is also ideal for parts that have:difficult-to-reach spots, curves, bends, or features like ejector pins or attachment screws. For more information, see our guide on the Plastic Injection Machine.
What Are the Benefits of Conformal Cooling?
There are some distinct benefits associated with conformal cooling, including:
- Reduced Cycle Times: The cooling phase is typically the most time-consuming phase of the overall injection molding cycle. Conformal cooling reduces the cooling time and, therefore, reduces the total cycle time.
- Higher Quality Parts: Because conformal cooling causes more uniform mold cooling, it produces fewer molding defects and less part warpage. This uniform mold cooling results in higher quality parts.
- Less Raw Material: Conformal cooling uses less raw material than conventional cooling methods due to less material being required to make the mold.
What Are the Limitations of Conformal Cooling?
The following limitations are associated with conformal cooling:
- Time-Consuming Design Phase: Conformal cooling mold designs need to be carefully optimized to generate the best and most efficient cooling. Preparing 3D printed mold tooling is more time-consuming than preparing a conventional mold.
- Limited Tool Size: For conformal cooling molds created using 3D printing technology, the part size will be limited to the size of the 3D printing bed.
- Cost of the Mold: Conformal cooling molds are more expensive than conventional cooling molds. The cost is only justified when parts are produced in large production volumes.
- Small and long channels: It can be difficult to remove the support powder when long and small channels are used to cool the part.
- Scaling: For intricate channel designs scaling can occur. Scaling means that the flow is decreased and the integrity of the wall of the cooling channel can be compromised, which can lead to leaking.
How Are Conformal Cooling Channels Created?
It is possible to manufacture a conformally cooled mold in several ways: direct metal laser sintering (DMLS - a 3D printing technology), vacuum brazing, and liquid interface diffusion. Of these, only DMLS is currently a practical production method. Vacuum brazing and liquid interface diffusion are considered to be too expensive over conventional cooling methods.
Today, the best way to make conformal cooling channels is with metal 3D printing technology – more specifically, direct metal laser sintering (DMLS), also known as powder bed fusion. With this additive manufacturing process, custom conformal cooling molds can be cost-competitive with conventional designs for large production volumes only. 3D printing allows for complex internal structures that would be impossible to produce with conventional methods. This capability allows the inserts of mold tools to be customized with cooling channels that will fit the shape of the molded part, leading to more uniform part cooling.
What is the Temperature After Conforming Cooling Has Been Performed?
Conformal cooling does not change the target part temperature after cooling. The change in temperature is based on the material and the design being molded. What conformal cooling does is change the rate at which the part cools to the desired temperature.
How Long Has Conformal Cooling Been Around?
Conformal cooling using additive manufacturing started in 1990 after the invention of the first metal powder 3D printer. Back then, CO2 lasers and metal powder, coated with a polymer binder, were used to manufacture the molds. Technology has since advanced and now uses 3D printing systems with precise lasers and metal powder to create the mold in an oxygen-free environment.
What is the Difference Between Conformal Cooling and Convention Cooling?
The main difference between conventional cooling and conformal cooling is that conventional cooling systems are designed to cool the surface of the plastic as it is being molded; whereas conformal cooling cools the internal cores as the plastic part is being molded. Compared to conventional cooling, conformal cooling facilitates faster and more uniform cooling. Conformal cooling is also used to cool complex geometries through curved custom-designed cooling channels, whereas conventional cooling implements straight cooling channels.
Conformal cooling is a great way to improve the quality of your plastic parts. It's also an energy-efficient and cost-effective process that can save you time and money in production.
Summary
This article presented conformal cooling, explained what it is, and discussed when to best use conformal cooling in manufacturing. To learn more about conformal cooling, contact a Xometry representative.
Xometry provides a wide range of manufacturing capabilities, including injection molding and other value-added services for all of your prototyping and production needs. Visit our website to learn more or to request a free, no-obligation quote.
Disclaimer
The content appearing on this webpage is for informational purposes only. Xometry makes no representation or warranty of any kind, be it expressed or implied, as to the accuracy, completeness, or validity of the information. Any performance parameters, geometric tolerances, specific design features, quality and types of materials, or processes should not be inferred to represent what will be delivered by third-party suppliers or manufacturers through Xometry’s network. Buyers seeking quotes for parts are responsible for defining the specific requirements for those parts. Please refer to our terms and conditions for more information.
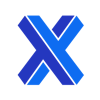