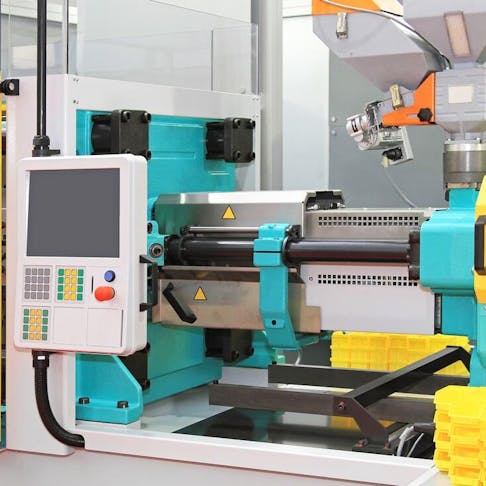
What Are Injection Molded Products?
Learm more about products from different industries created using injection molding.
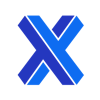
Injection molding is the most cost-effective way to make a plastic part at scale. Injection molding involves injecting molten plastic into a mold tool, then ejecting the solidified part. This process quickly repeats hundreds or thousands of times, amortizing the cost of the mold tool and driving down the cost of each unit to a few dollars or less. In addition, since injection molding uses the same mold tool for each part, the manufacturing process offers consistent quality across every part. Injection molding isn’t just used for plastic but can also be used with other materials like metals and glasses. The process also has a wider variety of materials, colors, cosmetics, polishes, and surface textures than CNC machining or 3D printing.
Injection molding can be used to make many different products. This article looks at some common injection molded products and explains the benefits of injection molding.
1. Healthcare Products
The healthcare industry relies heavily on injection molding. There are thousands of products made for this industry utilizing injection molding. It is used to make multipurpose plastic products manufactured in bulk. Many of these plastic products are single-use, disposable items to maintain sterility or prevent the spread of germs or disease. Injection molded products include plastic syringes, tools used in medical procedures, implantables, imaging components, IV connections, prosthetics, beakers and test tubes, and housings and casings for medical equipment.
The image below shows an example of a white plastic spray bottle used for dispensing medication:
White plastic spray bottles for packaging liquid medicines.
Image Credit: Matveev Aleksandr/Shutterstock.com
The plastic materials used in medical device injection molding are designed to be resistant to contaminants and easily sterilized. Another reason injection molded products are used for healthcare products is that the process can easily meet FDA and other regulatory agency requirements.
2. Electronics
Electronic housings made with plastic injection molding are used for many consumer products. For example, injection molding is used for common household electronics like remote controls, televisions, key fobs, computers, medical instruments, and more products. Injection-molded plastic housings protect and insulate the internal components of many electronics. Injection molding creates plastic molding for electronic components for various applications, such as structural applications, including boards, switch components, enclosures, and supports for finished systems.
Plastic is used for many products in electronics and the material provides versatility. It can be created using conductive or non-conductive plastic resin, combined with watertight seals, made to be UV resistant, and used in rigid or flexible applications, in multiple colors, with design capabilities beyond metal and other materials.
FREE Injection Molding Design Guide
3. Plastic Bottles
Plastic bottles are manufactured by the billions each year, ranging in multiple shapes and sizes. Typically, they are used to hold potable water and other drinks and are made from polyethylene terephthalate (PET), as the material is strong and lightweight. Injection molding is a popular process used to make plastic bottles.
Plastic injection molding is ideal for high-volume orders and mass production, and so it is often used for the manufacturing of bottles. The image below shows a typical mold used for the injection molding of plastic bottles:
Metal molds for making plastic bottles.
Image Credit: Sergey Ryzhov/Shutterstock.com
4. Agricultural Components
The agricultural marketplace is switching to plastic as a low-cost alternative to metal components commonly used throughout the industry. Plastic injection molded products offer higher resistance to impacts during use and from the effects of humidity and extreme temperatures. UV additives also help defend plastic parts from harsh weather conditions or exposure to corrosive substances. Parts for agricultural equipment must meet strict performance, durability, and reliability standards.
Plastic injection molding is used to manufacture crates, pallets & bulk containers, animal troughs, tubs, baskets, pesticide sprayer drone parts, agricultural machine parts and spares, water tanks, irrigation system components, brushes and cleaning equipment, exterior equipment covers, and packaging and animal feed sacks.
5. Bottle Caps Products
Since billions of plastic bottles are manufactured each year, so to are billions of bottle caps. Water, soft drink, liquid soap, and shampoo are a few of the many types of products for which bottle caps are required. Both simple and complex caps are often injection molded products. They can all be manufactured with injection molding, from basic standard bottle caps to specialty liquor bottle caps.
6. Machinery and Automotive Parts
Many machinery and automotive parts are comprised of plastic injection molded products. These parts include dashboards, bumpers, radio controls, interior door panels, cup holders, car bumpers, and truck steps. Plastic injection molded parts are valued for their durability, corrosion resistance, and UV resistance. Plastic components are also lightweight, which contributes to vehicle fuel efficiency.
The image below illustrates some examples of plastic and rubber components used in automotive molding:
Plastic and rubber parts of automotive manufacturing.
Image Credit: oYOo/Shutterstock.com
7. Toys
Injection molding is used to make many toys, including Lego brand blocks, high-end collectible models, and decorated children’s furniture. Injection molding allows for various sizes and shapes to be manufactured quickly and identically, making the process ideal for bulk toys. Some of the other advantages of creating toys using injection molding are that the plastic parts are durable, easy to clean, and many custom colors can be used.
8. Household Products
Injection molding is used to manufacture many household products like plastic containers and tubs in which consumer products are packaged. Other injection molded household products include drinkware, plastic kitchenware, barbeque accessories, toilet seats, soap dispensers, bird feeders and outdoor furniture in many households.
The plastics used in injection molding are durable enough for repetitive use. Plastic parts made with injection molding also stand up to outdoor wear and tear.
9. Construction Materials
Construction materials are made from various durable plastics, all of which offer distinct characteristics that make them suitable for different applications. They are often used as building materials for flooring, roofing, windows, insulation, walls, and piping. They are also formed into components and assemblies for various construction equipment.
Injection molding is used for conduits for concrete beams, raised flooring panels, insulators, roofing vents, deck fasteners, and railing gaskets.
What Are the Benefits of Using the Injection Molding Process?
The benefits of using the injection molding process are listed below:
- Highly Complex Injection Molded Parts: Injection molding can handle highly complex parts while ensuring uniformity, and enabling the creation of millions of virtually identical parts. The effectiveness of high-volume injection molding and maximization of precision and quality of parts means taking key design elements into account.
- Fast Injection Molding Process: The injection molding process is swift compared to other manufacturing methods, and this high production output rate makes it even more effective. The speed of production is subject to the complexity and size of the mold, but only about 15-120 seconds pass between each cycle time. With the short period between cycles, more injection molded products can be produced in a given period of time.
- Variety of Injection Molding Materials: More than 25,000 engineered materials can be used for complex injection-molded applications. High-performance plastic blends and hybrids can also be created to meet particular part requirements and characteristics, such as high tensile strength.
- Flexibility in Coloring: Injection molding provides flexibility in coloring your parts. The molding process can create parts that are clear or have various colors by aligning plastics, additives, and biocompatibility to achieve the wanted coloration. However, multiple colors are often needed in one product, which can be done using overmolding.
- Low Labor Costs: Labor costs are relatively low compared to other types of molding processes. The capacity to produce the parts at a very high level of quality with a high output rate helps with efficiency and effectiveness.
- Low Waste: This method produces very little post-production scrap relative to traditional manufacturing processes. Any waste plastic typically comes from the sprue and runners. However, any unused or waste plastic can be reground and recycled for future use.
- Flexibility in Surface Finish: Most injection-molded parts have a smooth surface finish close to the desired final look. However, a smooth appearance isn’t suitable for every application. Depending on the physical and chemical properties of the plastic material used, injection molding can create surface finishes that don’t require secondary operations. The injection molding process provides for flexibility in finish, from matte finishes and unique textures to engraving.
- High Precision Parts: Modern high-speed injection mold equipment that is appropriately maintained allows for the mass production of precision molded plastic parts. For the production of plastic components such as connectors and gears that require high precision production, injection molding is the best choice, as it affords tolerances as tight as +/-0.0002”.
- Faster Product Development and Production Cycles: Different skill sets of injection mold engineers can help OEMs achieve a shorter product development timeline. Doing so ensures faster production cycles and getting defect-free parts to market faster — a decided competitive advantage for manufacturers.
For more information see our article on the benefits of using injection mold for your products.
Which Industries Have Benefited from Injection Molding?
The industries that have benefited from injection molding include:
- Automotive
- Packaging
- Home appliances
- Electronics
- Medical
- Agricultural
- Windows & doors
- Food & beverage
- Telecommunications
The plastic injection molding industry is still growing, and the injection molding sectors are growing in number as well. The global injection molded plastics market size was valued at 265.1 billion dollars in 2020 and is anticipated to grow at a compound annual growth rate of 4.6% from 2021 to 2028. The increasing demand for plastic parts from different end-use industries is expected to drive the market’s growth.
Summary
This article provided a review of products from nine different industries produced using the injection molding process.
To learn more about injection molding, review our Ultimate Guide to Injection Molding or reach out to us for help with your injection mold design questions.
Xometry offers a full range of injection molding capabilities to help with your production needs. Visit our website to explore the full range of our capabilities or to request a free, no-obligation quote.
Disclaimer
The content appearing on this webpage is for informational purposes only. Xometry makes no representation or warranty of any kind, be it expressed or implied, as to the accuracy, completeness, or validity of the information. Any performance parameters, geometric tolerances, specific design features, quality and types of materials, or processes should not be inferred to represent what will be delivered by third-party suppliers or manufacturers through Xometry’s network. Buyers seeking quotes for parts are responsible for defining the specific requirements for those parts. Please refer to our terms and conditions for more information.
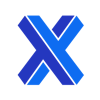