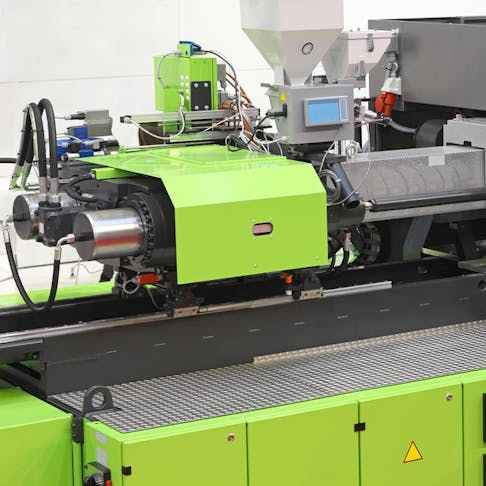
Plastic Injection Molding Machine
Learn about the types of plastic injection molding machines, their components, and uses.
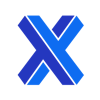
Injection molding is only possible thanks to the plastic injection molding machine. Plastic injection molding machines combine material feeding, melting, injection, and ejection in one condensed space, and allows for the mass production of products. This article will discuss what are the different types of molding machines, what are the major components of injection molding machines, and what are the common uses of injection molding machines, where to buy injection molding machines, as well as the expense of plastic injection molding, and whether it's easy to maintain plastic injection molding machines.
What Are the Different Types of Molding Machines?
Injection molding machines (also known as injection presses) are generally categorized based on their drive system, or based on what powers their major components. The three basic types of drive systems are electrical, hydraulic, and hybrid drives, each of which is suited to unique injection molding applications. Below is a brief explanation of each of these drive types, their main advantages/disadvantages, cost, and general applications.
1. Hydraulic Injection Molding Machines
Hydraulic injection molding machines are considered the first "modern" injection molding machine and were developed in the early 1900s. They utilize hydraulic drives to clamp the injection mold halves together and push molten plastic into the mold cavity. They consume hydraulic fluid and need constant energy input to both pump and cool their hydraulic systems.
Because hydraulic injection molding machines are an established technology stretching back decades, they are the least expensive, and most rugged, and easiest to source and repair. Hydraulics also offer unparalleled clamping forces in their clamping unit (3-4 tons per square inch!), making them ideal for larger molds.
However, hydraulic injection molding machines are energy inefficient and require higher temperatures for molding which can ruin some heat-sensitive plastics. Both hydraulic pumps and coolant need continuous power input and require additional infrastructure to support them. Also, these types of machines can be problematic as they carry the risk of hydraulic fluid leaks, and they produce more noise than other injection molding machines.
Hydraulic injection molding machines tend to be cheaper than all-electric machines, costing anywhere from $3,000-$100,000+ depending on size. They will also require additional maintenance and infrastructure costs, estimated roughly to be around $17,000/year, plus the cost of worker wages for upkeep and operation. They can last up to 7-10 years with proper maintenance, but their hydraulic systems make them prone to frequent issues that can shorten their lifespan with improper care. These types of drive systems are mainly for larger, thick-walled applications such as those found in the automotive industry.
2. Electric Injection Molding Machines
Electric injection molding machines (also known as all-electric machines) are an update to the traditional hydraulic machines, having been first developed in the 1980s in Japan. They implement several digitally controlled servo motors that allow for precise independent control of the four axes of injection molding: injection, extruding, clamping, and ejecting.
Servo motors used can idle when not in use, saving users up to 75% on power demands when compared to hydraulic models that need continuous pumping power. Electric injection molding machines also highly simplify the injection molding process with no necessary consumables, making them easier to run, repair, and scale down for small-to-medium-sized applications. All-electric machines are ideal for cleanroom applications needing high accuracy and a clean, quiet, and energy-efficient machine.
Electric injection molding machines do have some disadvantages. The first disadvantage is lower clamping power compared to hydraulic injection molding machines. The second disadvantage is that electric injection molding machines tend to be more expensive and difficult to repair compared with hydraulic versions.
Electric injection molding machines' prices depend on size and features but generally hover around $5000 to $200,000+ depending on the needed size. All-electric machines will last on average 20+ years with proper maintenance and are mainly specified in cleanroom applications for the production of small to medium-sized parts for medical, biochemical, and pharmaceutical products.
FREE Injection Molding Design Guide
3. Hybrid Injection Molding Machine
Hybrid injection molding machines are a hybrid version of hydraulic injection molding machines and electric injection molding machines.
Hybrid injection molding machines combine the benefits hydraulic and electric machines to create a powerful, accurate, and energy-efficient machine. They implement servo motor pumps for the hydraulic fluid, circulating oil for hydraulic pressure but allowing for power, emission, noise, and energy adjustments. They also have a servo motor-based reciprocating screw that saves energy costs when compared to fully hydraulic models that expend a significant amount of energy on screw recovery.
The advantages of hybrid injection molding machines include energy efficiency, reliability, responsiveness, highly controllable, reasonably priced, and require less maintenance and downtime. Because of their efficiencies, they exhibit faster ROIs than other types while still providing great clamping forces and precision.
The main disadvantages of hybrid injection molding machines is newness. Hybrid injection molding parts may not be readily available. Repairs to hybrid machines will require technicians to be familiar with both electric and hydraulic injection molding machines.
Another disadvantage of hybrid injection molding machines is that the design of the machine will be vary based on the model or manufacturer. For example, some hybrid models use a hydraulic screw drive instead of an electric screw drive will not be as efficient as electric models and will experience many of the same downsides as hydraulic injection molding machines despite having some servo control.
Hybrid models vary in price based on size and application but generally somewhere between electric and hydraulic injection molding machine prices. Also, there will be lower maintenance costs associated with these machines, leading to a faster ROI than either all-electric or hydraulic machines. Hybrid injection molding machines can easily last as long (or longer) than other injection molding machine designs with proper care. Their applications involve high volume parts for the medical industry, heavy industrial products, varying wall-thickness parts, and other applications both small and large.
Injection molding machine components.
Image Credit: Wikimedia
Below is a brief list of the different parts found in the typical injection molding machine. Note that model-specific parts will not be highlighted to provide the most inclusive summary for injection molding machines.
- Hopper: The hopper is essentially s large funnel that accepts stock material and feeds it into the machine.
- Barrel: The barrel contains the reciprocating screw and is the outer housing of the machine. The barrel is wrapped in heater bands and is tasked with both containing the material and the heating portion of the cycle.
- Reciprocating screw: This is the corkscrew component that moves back and forth with every cycle (powered by either an electrical or hydraulic drive system), conveying material through the heating sections, through the nozzle, and ultimately into the injection mold.
- Heaters: The heaters supply thermal energy through the barrel, converting solid plastic pellets into molten plastic as they are pushed by the reciprocating screw. Heaters allow for precise temperature control and are usually staggered in temperature for gradual heating.
- Nozzle: The nozzle dispenses molten plastic from the barrel and into the mold cavity. The nozzle usually sits within a depression in the mold known as the injection mold bushing and is heated to ensure that the plastic does not lose temperature before entering the mold.
- Mold: The mold contains the mold cavity and additional supporting features like ejector pins, runner channels, cooling channels, vents, etc. Molds are commonly separated into two halves: the stationary side (closer to the barrel) and the mold core (on the moving platen), but can also come in more sections depending on the specific machine being considered.
- Mold Cavity: The mold cavity is a negative of the desired part shape plus supports, gates, runners, sprues, etc., and it will be the location where molten plastic fills, cools, and is ejected from.
- Movable Platen: The platen is part of the clamping unit and clamps the mold together and releases the mold core when revealing the finished part. This component is either hydraulically or electrically driven and ensures that no material escapes the mold when injection occurs.
What Is the Most Common Use of Plastic Injection Molding Machines?
Plastic injection molding machines allow for the mass production of plastic parts. They can produce over 10,000 parts in a workday (depending upon machine and part design) with virtually no defects or variance between each part. Their use is only limited by the size of the machine and the imagination of the designers. Injection molding has so many uses that nearly every household in the US has had contact with dozens of injection molded items, if not more.
Where Can I Buy a Plastic Injection Molding Machine?
If interested in desktop injection molding machines, common suppliers like Alibaba, Amazon, and other retailers can provide good options. However, it will be necessary to connect with direct manufacturers if looking for a high-volume, large-scale injection molding machine. There are also extensive aftermarket sources for used injection molding machines, however, these involve the risks associated with any aftermarket purchase and may require maintenance/repair.
Are Plastic Injection Molding Machines Expensive?
Yes, plastic injection molding machines are the most expensive part of the injection molding process, second only to the molds themselves.
Injection molding machines vary in price depending upon type, where worktop/desktop machines cost anywhere from $2,000-$20,000, and large industrial models range from $50,000 to over $200,000. Also, these prices do not include the facility upgrades, skilled worker costs, maintenance fees, and monitoring equipment needed for such a system. This massive overhead incentivizes companies to outsource their injection molding to dedicated companies with existing infrastructure. Only those companies with a core need for injection molding and a developed, high-volume product would consider purchasing an injection molding machine—otherwise, the investment is not recommended.
Are Plastic Injection Molding Machines Easy To Maintain?
It depends on the specific injection molding machine, but generally no, there are considerable maintenance demands from injection molding machines. It is recommended to perform daily visual checks to catch early problems, and at least 4-5 hours per quarter for a general maintenance checkup. A dedicated full maintenance day is required annually to identify issues, perform adjustments, and replace aging parts.
Parts that need an especially keen eye are oil filters (regardless of indicator status), valves, safeties, hoses, machine cylinders, power lines, lubrication points, nozzle alignment, and control modules. Finally, injection molding machines can be temperamental with seasonal changes, so be extra vigilant during transitional months and during extreme temperature days. A lack of preventative maintenance will not only stall the machine, but any profits made from it, so performing regular checks will decrease headaches over the long run (and extend the lifespan of the machine, allowing you to extract more value from the investment in this technology).
For more information, see our guide on the Major Components of a Plastic Injection Molding Machine.
Summary
This article presented a review of the plastic injection molding machine and how it works. We hope this article helped readers understand this amazing piece of machinery, its types, and other vital pieces of information for those interested in injection molding machines or the process of injection molding.
About Xometry
Xometry offers a full range of injection molding capabilities to help with your production needs. Visit our website to explore the full range of our capabilities or to request a free, no-obligation quote.
Disclaimer
The content appearing on this webpage is for informational purposes only. Xometry makes no representation or warranty of any kind, be it expressed or implied, as to the accuracy, completeness, or validity of the information. Any performance parameters, geometric tolerances, specific design features, quality and types of materials, or processes should not be inferred to represent what will be delivered by third-party suppliers or manufacturers through Xometry’s network. Buyers seeking quotes for parts are responsible for defining the specific requirements for those parts. Please refer to our terms and conditions for more information.
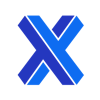