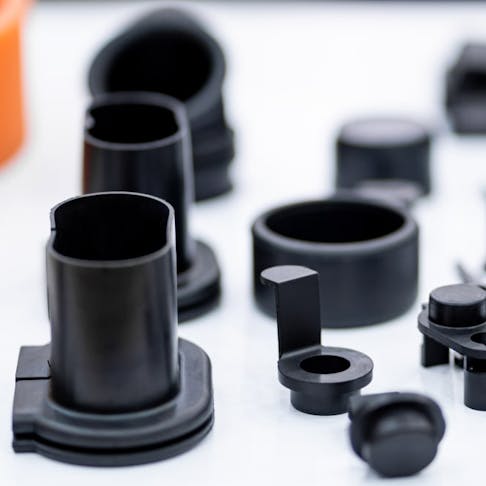
What is a Hesitation Effect in Injection Molding?
Our guide to understanding how the hesitation effect manifests itself in injection molding.
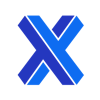
Injection molding is a manufacturing process for creating parts by injecting molten material into a mold. Injection molding can be performed with various materials, including metals, glasses, elastomers, confections, plastic, and most commonly thermoplastic and thermosetting polymers.
Injection molding is widely used for manufacturing a variety of parts, from the smallest components to entire body panels of cars. This article explains what injection molding is, what the hesitation effect represents, and how to address it.
Plastic bottles being molded.
Image Credit: Mr.1/Shutterstock.com
How does the injection molding process work?
The injection molding process creates the majority of plastics consumer and industrial products. The modern injection molding machine consists of an extruder, much like the one described previously, but with the added feature that the screw can be slid forward to quickly inject the stored-up hot melt into the mold's second main part.
A nozzle in the extruder’s end presses tightly into a recess in the stationary half of the mold. The two halves of the mold, with a vertical parting surface, are made from heavy steel and mounted on thick steel tie-bars. Within the mold is a network of runners distributing melt from the sprue to the mold cavities that determine the dimensions of the molded product. The mold halves clamp together with high pressure from a hydraulic piston.
Coolant channels passing near the cavities keep the mold cold, well below the freezing range of the plastic. Next, the screw moves forward, forcing the melt through the runners and into the cavities, and maintains melt pressure (5,000-15,000 psi, 34-103 MPa) while the moldings cool and freeze. Then the far half of the mold is withdrawn, activating ejection pins that push the moldings and runners out of the mold. Meanwhile, the extruder retracts and generates more hot melt.
Typically, the process is highly automated with computer controls. Injection machines are rated by their melting capacity, shot size, and clamping force. They range from machines shooting two ounces of melt into a family mold that makes the parts for a hobbyist’s model airplane to machines that mold 40-gallon trash cans in molds with two cavities—one for the can, the other for its lid.
Injection molding can make identical items with very close tolerances on dimensions, so it is ideal for the production of interchangeable industrial parts destined for complex assemblies.
Micro injection molding is a molding process for manufacturing plastic parts with shot weights of 1 to 0.1 grams and tolerances in the range of 10 to 100 microns. The process allows the manufacture of complicated small geometries with maximum possible accuracy and precision.
Injection mold inspection using a microscope.
Simon Kadula/Shutterstock.com
What is the molding hesitation effect?
Hesitation in injection molding occurs when the flow slows down or stops along a particular flow path.
If plastic filling a cavity can fill either a thin section or a thick section, the plastic will tend to fill the thick area first as this flow path offers less resistance. This principle may result in the injected material, or melt, in the thin section stopping or slowing significantly. Once the melt begins to slow down, it will cool more rapidly, increasing its viscosity. This higher viscosity will inhibit flow further, triggering even faster cooling, so the problem becomes self-propagating.
For the fabrication of microscopic and sub-microscopic patterns, the hesitation effect is likely to occur. The polymer melt is pushed into the microscopic patterns only after the main cavity body is filled. However, as the mold is constantly cooled throughout the process, the melt viscosity increases while the microscopic patterns are being filled. As a result, the melt flow cannot reach the patterns, and the replication becomes unsatisfactory. If pressure is applied to the cavity air during the melt injection, the flow through the main cavity will slow down. This slow-down of the cavity flow allows the patterns to be filled alongside the main cavity flow and improves the replication quality.
A change in pressure is likely whenever the viscosity changes or the flow channel thickness (or diameter) changes. Pressure increases when there is a reduced thickness. As the material hesitates, it will slow down and possibly prematurely freeze, thereby producing a short shot. If the flow of the material hesitates but can complete the making of a full part, then there may be more internal stresses resident in the completed component.
Hesitation typically occurs in thin sections of parts that have significant changes in wall thickness. It can reduce part quality because it creates variation in surface appearance, high stresses, poor packing, and non-uniform orientation of the plastic molecules. If the hesitation makes the flow front freeze completely, part of the cavity may remain unfilled. Hesitation can also lead to asymmetrical and unpredictable flow patterns.
How can the hesitation effect be avoided in conventional injection molding?
There are some techniques that can be employed to address the hesitation effect.
The polymer injection location should be moved away from the area of hesitation so that most of the cavity fills before the melt reaches the thin area. The lack of alternative flow paths gives less time for the melt to hesitate.
The injection location should be moved to a place that will cause greater pressure to be applied where the hesitation happened. It is useful to have the thin ribs or thin areas as the last point to fill so that all the injection pressure has already been applied. Different injection locations have different effects on plastic flow pressure.
Increasing the wall thickness where the hesitation occurred reduces the resistance to flow. Or, a less viscous material, that is, a material with a higher melt flow index can be used.
Injecting more quickly also reduces the potential of hesitation time. Or the melt temp can be increased so that it flows into the thin area more readily.
A filling analysis also helps avoid hesitation. The analysis simulates how plastics fill the mold under given product design, material, machine, mold, gating, and processing conditions. Filling analysis is the first step of any injection molding simulation and does not include packing, cooling, and warpage analysis and is generally required to perform any further analysis of any injection molding simulation. After analysis, the best injection location can be determined to avoid hesitation effect and short shot.
Colored resins used in injection molding.
XXLPhoto/Shutterstock.com
What are injection molding’s applications?
While injection molding is a versatile process that has application in countless industries, it is becoming increasingly valuable to the construction industry. Custom injection-molded plastic parts have high material stability, high durability when exposed to the elements, high energy efficiency, and material recyclability.
Injection molding creates many products such as wire spools, packaging, bottle caps, automotive parts and components, toys, some musical instruments, pocket combs, one-piece chairs and small tables, storage containers, mechanical parts, and most other plastic items available. It is the most common method of manufacturing plastic parts and is ideal for manufacturing high volumes of the same object.
Summary
This guide presented an understanding of what the hesitation effect is in injection molding and how to address it. If you need assistance understanding the issues with injection molded parts, reach out to us for help.
Xometry provides quotes on injection molding services. Visit our plastic injection molding capabilities page to get a free, no-obligation quote or to learn more about our material capabilities, finishes, and injection mold classes. Also, be sure to review our Ultimate Guide to Injection Molding, where you can learn more about optimizing your design for the injection molding process.
Disclaimer:
The content appearing on this webpage is for informational purposes only. Xometry makes no representation or warranty of any kind, be it expressed or implied, as to the accuracy, completeness, or validity of the information. Any performance parameters, geometric tolerances, specific design features, quality and types of materials, or processes should not be inferred to represent what will be delivered by third-party suppliers or manufacturers through Xometry’s network. Buyers seeking quotes for parts are responsible for defining the specific requirements for those parts. Please refer to our terms and conditions for more information.
Sources:
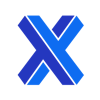