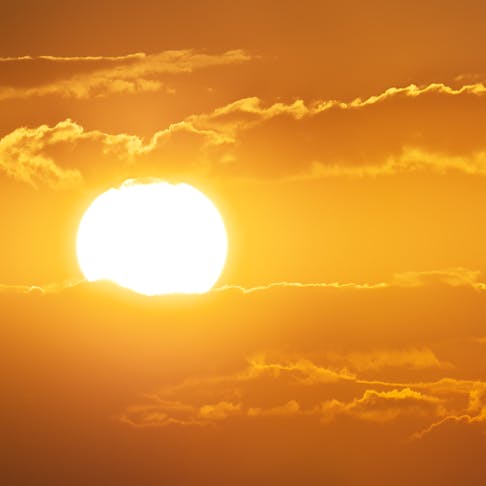
UV-Resistant Plastics, Polypropylene vs. Nylon
Plastic products designed for outdoor use are ideally manufactured using UV-resistant plastics. Learn more about UV-resistant plastics and the differences between polypropylene and nylon here.
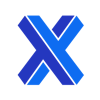
UV-Resistant Plastics, Polypropylene vs. Nylon
Plastics are ubiquitous in today’s world so, naturally, some get exposed to sunlight. Unfortunately, the ultraviolet (UV) radiation in sunlight has a destructive effect on most plastics. Any product designed for outdoor use needs to be manufactured from UV-stabilized or UV-resistant plastics. This article will focus on the UV resistance of two common commodity plastics: nylon and polypropylene.
What Makes up a UV-Resistant Plastic?
When plastics are exposed to the ultraviolet radiation generated by the sun, they either absorb it or produce free radicals that negatively affect the material’s mechanical properties. In addition to a reduction in mechanical strength, exposure to UV radiation can produce the following effects on plastics with low UV resistance:
- A chalk-like surface appearance
- Embrittlement and cracking on the surface
- Color changes/fading
It must be noted that there is a difference between UV-resistant plastics and UV-stabilized plastics. Those that are naturally resistant to UV degradation are referred to as UV-resistant plastics. The ones that do not naturally resist degradation require various additives to improve their UV resistance and are called UV-stabilized plastics. Neither polypropylene nor nylon is naturally resistant to UV, so they need additives.
Effects of UV Radiation on Polypropylene
Polypropylene is highly susceptible to degradation by UV radiation in its base form (i.e. no pigment or additives). The material becomes brittle after prolonged exposure. In fact, basic polypropylene can lose up to 70% of its mechanical strength after 6 days worth of exposure to high-intensity UV radiation. It should be noted, however, that even with the additives, polypropylene will still degrade relatively quickly when exposed to sunlight for a prolonged period of time.
Polypropylene is sensitive to ultraviolet wavelengths of 290-300, 330 & 370 nm (nanometers). These are considered the spectra maxima of polypropylene.
Even though polypropylene has great mechanical strength and is highly chemically resistant, it is not suited for prolonged exposure to sunlight. Polypropylene is also not easy to coat so it’s best to simply keep this material out of direct sunlight altogether.
FREE Injection Molding Design Guide
Effects of UV Radiation on Nylon
Nylon is susceptible to degradation by UV radiation, but not all nylons are the same. Nylon 6, for example, is more resistant than nylon 6/6. The color of nylon parts will tend to fade over time when exposed to UV. Nylon degrades via the same mechanism as polypropylene — the radiation creates free radicals that further break down intermolecular bonds.
Nylon is sensitive to UV radiation in the wavelength range of 290-315 nm. Again, this is known as the material’s spectra maxima.
Nylon is a very durable and flexible material that’s great in products that get exposed to moisture. If moderate exposure to UV radiation is expected, nylon 6 or nylon 12 are good options. However, continuous exposure to UV radiation will result in accelerated degradation.
Improving UV Resistance
While nylon and polypropylene are not generally seen as UV-resistant plastics, certain additives can improve their performance. These additives take the form of stabilizers, absorbers, or blockers.
- Blockers - Fillers like titanium oxide or carbon black pigments can act as UV radiation blockers. These pigments help prevent the UV rays from reaching the plastic’s actual polymers and thus prolong the material’s lifespan.
- Absorbers - Absorbers work by absorbing UV radiation and then converting it into heat. Typical organic absorbers include benzophenones and benzotriazoles. Benzotriazoles can be introduced in concentrations as low as 0.5% by volume and still significantly increase UV resistance.
- Stabilizers - Stabilizers work by trapping any free radicals that get formed. This then minimizes subsequent degradation of the intermolecular bonds within the plastic. Stabilizers are also known as scavengers because they “scavenge” and collect any free radicals. Among the most common are the hindered amine light stabilizers (HALS).
Oftentimes, all three types of additives are introduced into the plastic to improve its UV resistance on multiple fronts.
Which Plastics are Resistant to UV Radiation?
Nylon and polypropylene are not considered UV-resistant plastics, so which plastics actually fall into that category? The main ones are fluoropolymers and imides.
Fluoropolymers naturally have good resistance to UV radiation. This is due to their strong carbon-fluorine bonds that resist degradation. Common fluoropolymers are:
- PTFE - Polytetrafluoroethylene
- PVDF - Polyvinylidene fluoride
- FEP - Fluorinated Ethylene Propylene
Imides are excellent UV-resistant plastics and as such can be used in applications with extreme UV exposure. Typical imides are listed below:
- PI - Polyimide
- PEI - Polyetherimide
Choosing a Material
Many factors will go into your choice of polymer. These include, among others;
- Mechanical strength
- Abrasion resistance
- Temperature resistance
UV resistance is often overlooked but can have serious long-term effects if left unaddressed. The required level of UV resistance depends on the product’s intended purpose, its expected level of exposure (i.e. continuous or just temporary), and any other environmental factors (high temperature and humidity can accelerate the effects of UV degradation). Fluoropolymers or imides are the better options if your product will be exposed to UV and an adverse environment on a long-term basis. However, if your parts just get intermittent UV exposure, UV-stabilized nylon or polypropylene can be ideal. To learn more about which UV-resistant plastics are better suited for specific applications, contact a Xometry expert.
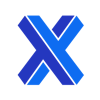