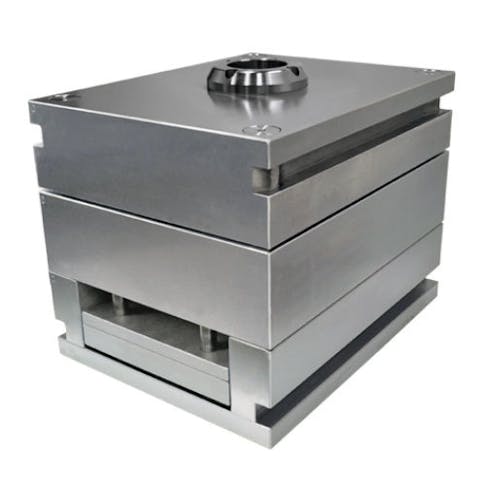
A Tool Maker’s Strategies to Avoid Injection Molding Pitfalls
Even when a tool is designed perfectly, accounting for material shrink rates, mold makers must also mitigate or eliminate pitfalls inherent to the injection molding process.
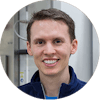
The quality of injection molded parts is controlled by a set of standards that enable parts to hit dimensional and cosmetic requirements. For even when a mold tool is designed perfectly, accounting for material shrink rates, mold machine operators must also mitigate or eliminate various pitfalls inherent to the injection molding process.
When parts cool within the mold, certain features that are thicker will solidify more slowly than surrounding walls or features. This causes warping and sink, or surface depressions. Sink and warping can prevent parts from being in tolerance or properly assembling with other parts. Thus, mold manufacturers use tooling design strategies to ensure injection molded parts are high quality. The following strategies include adjustments to temperature, pressure (tonnage), holding time, ejector mechanisms, and more.
Tool Design Strategy 1: Ensure Sufficient Tonnage
Injection molding press size and tooling are designed around the clamping force required to hold the tool shut during the high-pressure material injection. This clamping force is called tonnage. Common tonnage for small parts can be 50T, with medium parts moving to 500-750T, and larger parts being over 1000T. Injection mold operators determine the liquid material injection pressure, as well as the time in which that pressure is held in the cavity. When pack and hold pressure is sufficient, it ensures that enough plastic material is pushed into the cavity to make all the molded features. Increased holding pressure helps eliminate uneven portions that cool at different rates.
Tool Design Strategy 2: Control Cooling
Typically injection mold tools are cooled with water running through internal tooling channels. Controlling cooling is critical to maintaining even shrinkage rates. Placing cooling channels at thicker sections to help them cool faster, for example, can significantly improve part consistency as well as decrease cycle times.
Tool Design Strategy 3: Place Ejector Pins Evenly
Ejector pins push the molded part out of the tool as it opens. This step needs to happen as quickly as possible to minimize cycle time and keep production costs low. Since uneven ejection can cause significant warping and dimensional inconsistency, multiple ejector pins are typically used to evenly remove the part. For some designs, a stripper plate can be used to complement ejectors. Stripper plates make continuous contact with the outer edge of a part for even removal.
Tool Design Strategy 5: Add Vents
Vents are required on all mold designs to allow air to move out of the build cavity as it is displaced by molten plastic. Vents are very small gaps around the parting line or ejector pins. If vents are too large, material will fill into the gaps and cause flash, or material that bleeds out. Alternatively, if there are not enough vents, trapped air can stop material flow—causing incomplete features—or even create a small burn mark as the air overheats to plasma.
Tooling Design Strategy 6: Sensors
In complex, multi-feature parts, it may be beneficial to embed pressure and temperature sensors into the tool in order to measure these parameters during manufacturing to allow for real-time feedback and process control. Consistently maintaining pressure and temperature in the tool can go a long way toward ensuring consistent tolerances.
Xometry Injection Molding
Xometry injection molding manufacturers have the expertise to account for each of these quality factors in custom injection molded parts. To speak with an injection molding consultant, simply get a quote and we’ll reach out.
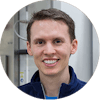