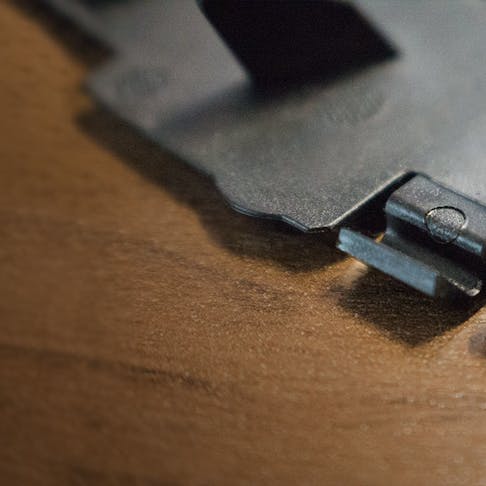
Video: 7 Ways to Save on Injection Molding
Save thousands of dollars on injection molding tooling using these 7 simple steps from expert Travis Minyard
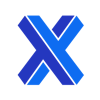
Injection Molding is the number one way to make plastic parts in mass production. Our industry expert Travis Minyard has nearly 30 years of experience in the injection molding field, and he's collected his 7 best design practices on how to get the most out of injection molding.
How can you save thousands of dollars in injection molding tooling? Watch and find out!
1. Coring and Wall Thickness
Coring reduces material volume, weight, and cycle time.
A lack of coring results in a chain of events which ultimately gives you a higher part cost. When you don’t have coring in your part, you get an uneven wall thickness. This in turn results in uneven cooling, which leads to sink marks. Because you have more material, and a greater material volume overall, you’ll get an increased cycle time (and higher cost as a result). This can also result in differential shrinkage and your part will go out of tolerance.
Coring reduces material volume, weight, and cycle time.
Drafts are angled wall sections that help parts eject smoothly.
Die-locked part
4. Pass-Thru Coring
Without pass-thru coring, clips, snaps and similar features require additional lifters or slides to release the part from the mold. This increases the overall mold cost.
To use pass-thru coring, insert a cutout thru the parallel feature for steel to shut-off.
Pass-Thru Coring
Annular Snap
6. Shrinkage
Almost every material shrinks, and the rate of this must be compensated for. To understand shrink rate values well, a great resource is matweb.com, or checking with the supplier of your material to see what shrink rate you need to know.
Plastics generally shrink towards their centroid, which is their center mass. Some plastics do shrink linearly, so always be aware of your specific material’s specs.
Potential shrinkage
Parting line on a CAD design
Key Takeaways
Injection molding is a fantastic process for both high and low volume production parts. Now that you know how to reduce costs and time to market for your design, use Xometry to get your parts with competitive pricing and fast lead times!
Learn more about our injection molding services and request a quote online from our expert injection molding engineers at Xometry—we turn quotes around within 24 business hours.
Want more design tips? Get a comprehensive design overview in our Injection Molding Design Guide.
Check out more cost-saving educational trade secrets:
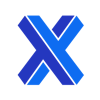