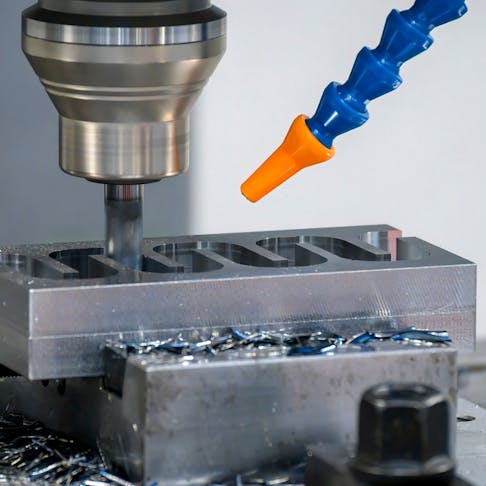
Slot Milling: How It Works, Types, Advantages, and Disadvantages
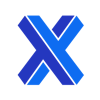
Slot milling is a basic machining technique that is essential to many sectors, including manufacturing and carpentry. This technique uses specialized tools called slot milling cutters to make slots or grooves in a workpiece. Understanding the various slot milling strategies their functions, and their pros and cons is important in selecting the right method for the right machining job.
This article will go into the types, advantages, and disadvantages of slot milling as we examine this machining method.
What Is Slot Milling?
Slot milling is a machining process in which a rotating tool with multiple cutting edges is used to create grooves in a workpiece. This method manufactures components with precision slots, keyways, or channels. Slot milling is a versatile and accurate machining technology.
What Is Slot Milling Used For?
The main applications of slot milling include: the creation of pockets, keyways, and slots in a range of workpieces. Products and machines produced by a variety of industries require slots for assembly or basic functionality. Slot milling makes it possible to precisely fabricate parts like: gears, pulleys, and other mechanical parts. Slot milling enables the production of dimensionally accurate geometries that would be difficult to achieve by other means.
Are Slot Milling and Groove Milling the Same?
Yes, slot milling and groove milling are the same. Both words describe a machining technique in which a slot or groove is cut into a workpiece using a revolving cutting tool.
How Does Slot Milling Work?
Slot milling is a machining process that employs a rotating tool with multiple cutting edges. The primary factors affecting the outcome of a slot milling operation include the required geometry of the slot (width, depth, undercut) and the material characteristics of the workpiece. The correct choice of tools, feed rate, speed, and cooling fluids can have a dramatic effect on the ultimate quality of the machined feature.
How Does Slot Milling Differ From Other Milling Types?
The primary distinguishing factor between slot milling and other milling types is the tool's axis orientation with respect to the workpiece. In slot milling, the tool moves along its own axis, as opposed to face milling, where the cutter moves perpendicular to the workpiece surface, or peripheral milling, which cuts along the workpiece's periphery. The workpiece can have channels or slots created in it thanks to this axial movement. The different axis orientations affect the kinds of operations that each milling technique performs well. While peripheral milling works well for contouring, face milling produces flat surfaces. With its axial movement, slot milling is perfect for making exact grooves or slots. Understanding these nuances aids machinists in selecting the most suitable technique for specific applications, considering factors like: material properties, surface finish requirements, and machining efficiency.
What Are the Types of Slot Milling Cutters?
The types of slot milling cutters are listed and discussed below:
1. Face Milling Cutter
Often used in slotting operations, face milling cutters are best suited for jobs involving linear grooving. These cutters have a flat surface with several cutting teeth positioned around the edge. When slotting, the cutter makes a straight-sided groove in the workpiece by engaging with it. Their usefulness is limited, though, since they work best when creating linear slots. Face milling cutters are not as adaptable for non-linear or more complex slotting applications due to their design. Even with this drawback, they are nevertheless a useful tool for jobs where linear grooving is the essential prerequisite. Figure 1 is an example of a face milling cutter:
Face milling cutter.
Image Credit: Shutterstock.com/Pixel B
2. Side Milling Cutter
The side milling cutter is a good option for a variety of milling processes because of its ability to remove metal from the sides of a workpiece effectively. It has teeth on both or all of its sides, as well as along its periphery. With the specific purpose of cutting slots and keyways, this cutter is available in different configurations: side milling cutters with staggered teeth, side milling cutters with interlocking teeth, side milling cutters with planes, and half side milling cutters. These variants address certain machining needs and provide information about the kinds of slots, depths, and uses that can be achieved by side milling processes. Particularly, side cutters are very stable and productive when handling long, deep, open slots. Figure 2 below is an example of a side milling cutter:
Side milling cutter
Image Credit: https://cadcamengineering.net/side-milling-cutters-and-side-milling/
3. End Milling Cutter
End milling cutters are characterized by a center 'dead' area and a special construction that makes them useful for a variety of milling applications. Due to their limited cutting teeth on the side and outer edge, they are good for precision machining, especially when working with complex closed slots. End mills are in use for slots that are angled, curved, or straight. They are a go-to tool for various machining tasks because of their capacity to handle designated pockets and traverse through wider gaps than the tool's diameter. Figure 3 below is an example of an end milling cutter:
End milling cutter.
Image Credit: Shutterstock.com/Pixel B
4. Gang Milling Cutter
Gang milling cutters are excellent at precisely and efficiently creating slots by using several groove cutters on a single arbor. In slot machining, this simultaneous multi-cutter method greatly increases productivity and saves time. Its special strength is its capacity to form slots with different designs in a single pass. This efficiency does have drawbacks, though, as the procedure produces significant cutting forces. The machine tool and the arbor need to be very rigid to fully utilize gang milling cutters. This brings to light an important point for users: a robust setup is required to withstand the forces involved and guarantee optimal performance in slot machining operations. Figure 4 shows an example of a gang milling cutter:
Gang milling cutter.
Image Credit: https://caddesignr.com/milling-machine-operations-photos/
5. Woodruff Key Slotting Cutter
Woodruff Key Slot Cutters are circular cutters, usually of HSS M2 grade, with a parallel shank for stability. They are essential for creating keyways in shafts. For companies requiring accurate, narrow slots, the Woodruff-Style Narrow-Width Slotting Cutters are the preferred choice. These cutters are similar to side milling cutters in that they are plain milling cutters with concave sides.
They create slots with rounded or square bottoms by cutting a semicircular cross-section. Positioning the cutter over the workpiece and modifying the depth in accordance with standard Woodruff key sizes is the process of milling a Woodruff key slot. Using a vise, chuck, between centers, or clamping to the milling machine table are several workpiece securing techniques. Figure 5 below is an example of a woodruff key slotting cutter:
Woodruff key slotting cutter.
Image Credit: https://en.m.wikipedia.org/wiki/File:WoodruffCutters-Keys.jpg
6. T-Slot Cutter
A T-Slot Cutter is distinguished by its unique function of cutting lateral slots that extend beneath the material's surface. Because of its particular design, it generates a groove that looks like an upside-down T. With flexibility in machining applications, this tool is useful for operations requiring slots to reach beneath the surface of the material. Its capability to cut along the axis of rotation allows for precise and strategic placement of T-shaped grooves. This makes the T-slot cutter a crucial tool for various machining processes, offering efficiency and precision in creating slots that go beyond the surface of the material. Figure 6 below is an example of a T-slot cutter:
T-slot milling cutter.
Image Credit: Shutterstock.com/Pixel B
What Are the Advantages of Slot Milling?
Some advantages of slot milling include:
- It allows for the creation of deeper slots or pockets compared to end milling.
- One of the benefits of slot milling is that it makes creating inner and outer profiles easier. Traditional milling machines have to deal with complexity since they need to constantly realign the spindle. On the other hand, slot milling effectively tackles these difficulties by permitting simplified machining without the need for continuous spindle adjustments, improving accuracy, and simplifying production processes.
- Slot milling cutters excel in machining solid-jaw mandrels, guide bars, and flat metal parts. These cutters enable precise shaping and slot creation by efficiently removing material in a rotational motion. Their adaptability makes them indispensable in various metalworking applications, providing accuracy and efficiency in crafting intricate components.
What Are the Disadvantages of Slot Milling?
The following are a few drawbacks of slot milling:
- Can result in high vibrations, especially when cutting deep slots or working with hard-to-cut materials.
- Continuous cutting action in slot milling generates high radial forces, making it less stable for deep cuts.
- The cutting operation can lead to rapid heat buildup in the tool and workpiece, affecting tool life and part quality.
How To Choose Slot Milling Cutters?
The choice of a slot milling cutter must take into account several important factors:
- Material: Different materials call for different kinds of cutters and cutter coatings.
- Geometry: The dimensions of the required slot will determine cutter size as well as process variables such as cut depth, feed rate, and speed.
- Machine Capabilities: Ensure that the machine driving the tool has the required feed, speed, and control features needed to work properly with the intended tool and material.
- Chip Removal: Choose a tool that has good chip evacuation characteristics.
- Surface Finish: Select a tool with cutters designed to produce the surface finish quality needed for your application.
Lastly, assess your spending limit and select a cutter that strikes a compromise between affordability and performance for your particular machining requirements.
What Is the Importance of Choosing the Right Slot Milling Cutter?
Selecting the proper slot milling cutter is essential because it has a direct effect on the quality of the workpiece, tool longevity, and machining efficiency. The right cutter enables effective material removal, which cuts costs and machining time. Additionally, it prolongs the tool's life. Finally, choosing the right cutter for the material and slot dimensions produces an accurate slot geometry and a smoother surface finish, improving the machined part's overall quality.
How Does the Choice of Slot Milling Cutter Affect Its Performance?
The choice of slot milling cutter significantly affects its tool life. Using the wrong cutter can lead to increased cutting forces, tool wear, and decreased efficiency. Selecting the right tool has a substantial impact on the results, improving the surface finish quality and dimensional accuracy of the machined part. Optimal cutter selection ensures better performance, minimizing defects, and improving overall machining outcomes.
How Can Xometry Help in Choosing the Right Slot Milling Cutter?
Using its online platform, Xometry, a top manufacturing marketplace, can help select the best slot milling cutter. Users can specify their slot milling needs and get fast quotes for custom CNC machining. The knowledge in tool selection offered by Xometry's network of manufacturing partners guarantees that the appropriate cutter is used for the task. Their support staff may also provide advice to clients so they can make the best decisions possible for the best machining outcomes.
How To Slot Mill?
The first step in slot milling is to select the proper slot milling cutter based on the material and slot dimensions. Then, clamp the workpiece into the machine vise. After adjusting the feed rate and spindle speed, carefully position the cutter at the starting point of the intended slot on the workpiece. Once in position, initiate the milling process by turning on the cutter. Make successive passes along the slot route as needed, ensuring optimal chip evacuation for a smooth and efficient slot milling operation.
What Are Some Tips for Successful Slot Milling?
The following is a list of tips that can result in successful slot milling operations:
- Opt for down milling to enhance stability and improve chip evacuation.
- Ensure that at least one cutting tooth is always engaged to improve surface finish and reduce vibration.
- Manage chips effectively with multiple passes, chip-breaker cutters, and coolant/lubricant flushing.
- Balance cutting feed rates to prevent thermal issues while maintaining productivity.
- Use larger diameter cutters for deep slots or consider more rigid materials.
- Use a ramp-down motion for smoother cutter entry, reducing vibrations.
Is Slot Milling Better Than Side Milling?
No. Slot milling and side milling are different machining operations, even though a side milling cutter can be used for cutting slots. The choice between these milling techniques depends on the specific machining requirements. Slot milling is used for creating slots and grooves, while side milling is the creation of a flat, vertical surface on the side of a workpiece. Ultimately, the decision should depend on whether or not you want to make a slot. Other actors should also be considered, including: material, tool geometry, and desired surface finish.
What Is the Difference Between Slot Milling and End Milling?
The primary distinction between end milling and slot milling is the way they cut. A slot mill may plunge like a drill and then cut across like an end mill, combining drilling and lateral cutting capabilities. An end mill, on the other hand, mainly concentrates on lateral and horizontal cutting.
Summary
This article presented slot milling, explained it, and discussed how it works and its various types. To learn more about slot milling, contact a Xometry representative.
Xometry provides a wide range of manufacturing capabilities, including machining and other value-added services for all of your prototyping and production needs. Visit our website to learn more or to request a free, no-obligation quote.
Disclaimer
The content appearing on this webpage is for informational purposes only. Xometry makes no representation or warranty of any kind, be it expressed or implied, as to the accuracy, completeness, or validity of the information. Any performance parameters, geometric tolerances, specific design features, quality and types of materials, or processes should not be inferred to represent what will be delivered by third-party suppliers or manufacturers through Xometry’s network. Buyers seeking quotes for parts are responsible for defining the specific requirements for those parts. Please refer to our terms and conditions for more information.
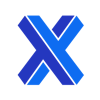