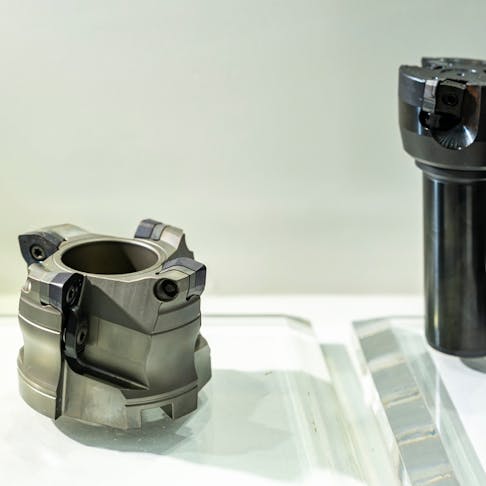
Shoulder Milling: Definition, Process, and Types of Cutters
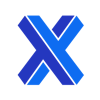
Shoulder milling is a type of precision machining meant to take away material from the shoulder area of a workpiece. The shoulder milling cutter moves both laterally and radially to create a flat, smooth shoulder surface. Different kinds of cutters exist, such as shell mills, face mills, and end mills.
The cutting tools come in many shapes to meet the needs of different jobs. Shoulder milling is useful because it can make flat surfaces to meet very exacting tolerances. This makes it useful in aerospace, automotive, and general manufacturing.
This article will discuss shoulder milling, how it works, the types of cutters, its applications, and its benefits.
What Is Shoulder Milling?
Shoulder milling is a precision milling process that predominantly targets metals. It's a technique designed to fashion, refine, or modify the shoulders or sidewalls (the vertical surfaces that intersect with the horizontal surface) of a workpiece. In essence, shoulder milling targets the perpendicular transitions between the flat top of a workpiece and its vertical sides. The tools create precise and well-defined contours, recesses, or other geometrical features.
What Is Shoulder Milling Used For?
Shoulder milling is used to make shoulders or sides on the workpiece that are flat, smooth, straight, and perpendicular to the upper flat surface. This method is essential for high-precision jobs like making molds and dies.
Shoulder milling can quickly remove material from the sides of the workpiece by carefully managing the feed rate and depth of cut. This makes the shoulders accurate and refines the object’s overall dimensions. Once complete, parts should fit together smoothly, improving the quality and performance of the whole product.
How Does the Shoulder Milling Process Work?
The shoulder milling process employs a rotary milling cutter to remove material from a workpiece's shoulder or flat side. The cutter usually has more than one cutting edge to speed up material removal. Depending on the machined material, these cutting edges may be made from materials like high-speed steel or carbide.
The milling cutter is held in place by an arbor. The arbor is then linked to a milling machine. The workpiece is firmly attached to the machine's worktable, which keeps it stable while it's being cut. The cutting edges make contact with the material's surface as the cutter turns, creating the necessary cutting forces. Oftentimes, coolants or cleaning fluids are used to remove the heat caused by cutting and to keep tools from wearing out. This is especially important when milling rigid materials since too much heat can damage both the tool and the quality of the result.
There are different ways to do shoulder milling, such as side milling, up-milling, and down-milling. Side milling operations create flat surfaces, slots, keyways, and other features on a workpiece. When you up-mill, the cutter turns opposite to the feed direction. This makes the finish smoother but requires the part to be clamped down especially tightly. When down-milling, the cutter spins in the same direction as the feed. This makes the process more stable, but the surface may become harder.
How Does Shoulder Milling Differ From Other Types of Milling?
Shoulder milling stands apart from other types of milling in its approach and application. This technique, distinct from traditional face milling or end milling, is meant for specific purposes.
For example, when comparing shoulder milling to face milling, the primary distinction can be seen in their respective cutting surfaces. Shoulder milling focuses on machining a workpiece's sides or shoulders, necessitating a cutter with a distinct geometry tailored to this task. In contrast, face milling concentrates on the upper surface of the material, employing cutters designed for horizontal engagement. The critical difference is that shoulder milling is typically used to create precise vertical features such as groove walls or slots. In contrast, face milling is primarily used to flatten or contour a horizontal area, such as a workpiece's top surface.
Additionally, when shoulder milling is contrasted with end milling, the dissimilarity becomes even more pronounced. End milling entails plunging the cutter axially into the workpiece to create a cavity or groove, but it may not be ideal for producing high-precision vertical shoulders. In contrast, shoulder milling utilizes specialized tools to make these precise vertical surfaces by engaging the material from the side.
What Industries Typically Use Shoulder Milling
Shoulder milling is a versatile machining technique employed across various industries to precisely and efficiently remove metal. This process is particularly favored in sectors where precision, high material removal rates, and surface finish quality are paramount. For example, the aerospace sector, in particular, frequently relies on shoulder milling to create complex components with tight tolerances. This method is an integral part of crafting aircraft engine components, airframes, and other critical parts due to its dimensional accuracy and the quality of its surface finishes.
Shoulder milling is also an essential tool in the automotive business for making engine blocks, transmission parts, and other vital parts. Since it’s both accurate and quick, it helps automakers keep quality standards high. In mold and die-making, shoulder milling is invaluable for shaping and finishing molds for casting and forming various products. The mold and die industry demands impeccable precision, and shoulder milling can meet these stringent requirements. The medical device industry leverages shoulder milling to craft intricate parts such as orthopedic implants, surgical instruments, and prosthetic components. Finally, manufacturers of heavy machinery and equipment employ shoulder milling to craft components such as gears, shafts, and housings. This process helps ensure the durability and reliability of these industrial products.
What Are the Types of Shoulder Milling Cutters?
There are a lot of different kinds of shoulder milling tools. Each one specializes in certain materials and tasks. Listed below are the types of shoulder milling cutters:
End Milling Cutter
An end milling cutter," colloquially recognized as an "end mill," is a vital but relatively simple tool in machining and metalworking. It is a cylindrical cutting instrument that operates precisely. This device possesses cutting teeth on both its end and periphery, permitting multifaceted cutting actions. Figure 1 is an example of an end milling cutter:
End milling cutter.
Image Credit: Shutterstock.com/Matee Nuserm
The tool rotates around its central axis and works on a wide range of materials, including metal, wood, and plastic. It is visually characterized by its helical cutting edges. One notable feature of this helical design is its ability to move chips away from the operating area while it cuts, ensuring a smooth and uninterrupted machining experience.
This versatile tool can adapt to different industries, from aerospace to automotive. It excels at crafting intricate designs, grooves, slots, contours, and other geometric features too complex for a simple drill. In CNC machining, end mills enable the creation of intricate three-dimensional shapes with exceptional precision. This capability significantly enhances the landscape of modern manufacturing.
Face Milling Cutters
Face milling cutters are versatile machining tools employed in the metalworking industry for material removal. These cutting instruments are designed to shape, smooth, and refine flat surfaces. Figure 2 is an example of a face milling cutter:
Face milling cutter.
Image Credit: Shutterstock.com/Pixel B
Face milling cutters sport multiple cutting edges in the form of replaceable inserts. All the inserts revolve around the cutter’s central axis, tracing out a circular motion. As the cutter engages with the workpiece, it progressively removes material in a series of passes.
The angular positioning of the cutter results in a uniform and precise surface finish. This differs from end mills or drills, which primarily target peripheral or axial surfaces. A wide range of tasks are carried out with these tools. They are designed to smooth out the flat surfaces on various materials such as metals, plastics, and composites. They are also essential for ensuring that the sides of a piece are square and that the piece is flat and straight.
Face milling cutters are used in industries that value quality and precision. Aircraft, cars, and general manufacturing parts all get face milled. The cutters are essential tools for making flat areas.
Solid Carbide Cutters
A solid carbide cutter is a monolithic carbide tool. This dense, durable material, created by sintering carbide particles, imparts exceptional hardness, heat resistance, and wear resilience. These cutters are used predominantly in precision milling, drilling, and turning operations. Figure 3 is an example of a solid carbide cutter:
Solid carbide cutter.
Image Credit: Shutterstock.com/Dizfoto
Functionally, the extremely rigid structure of a solid carbide cutter imparts precise cutting motions on its target. The keen edge effortlessly shears through various materials, including steel, aluminum, and composites. The innate toughness and resilience of carbide extends tool life, reducing the frequency of replacements.
Many manufacturing sectors employ carbide cutters for things like engine components and intricate dies. The tools’ utility extends to woodworking, where they sculpt hardwoods, and medical device manufacturing, where precision is paramount.
Indexable Milling Cutter
An indexable milling cutter is characterized by its modularity and versatility. Like a face milling cutter, this one engages the material with a set of replaceable cutting edges on a rotating mechanism. Figure 4 is an example of an indexable milling cutter:
Indexable milling cutter.
Image Credit: Shutterstock.com/Dizfoto
The cutter operates via a revolving motion, where interchangeable inserts with multiple cutting edges interact with the workpiece. These inserts, typically made of carbide, ceramic, or high-speed steel, offer superior wear resistance. They can be rotated or replaced to maintain sharpness and optimize cutting performance.
Indexable milling cutters serve many purposes in metalworking and manufacturing. They excel in tasks like face milling, slotting, and profiling. Their efficiency lies in cost-effectiveness; worn inserts can be swapped without discarding the entire tool. This adaptability reduces production downtime and enhances workflow efficiency.
Square Shoulder Milling Cutters
Indexable square shoulder milling cutters possess a distinctive square shape, which improves their efficiency and versatility during milling processes.
The cutting edges come in the form of multiple indexable inserts or cutting edges securely fastened onto the cutter body. These inserts are replaceable to cut down on tool maintenance costs. The square shoulder design optimizes the tool's rigidity, reducing vibrations and enhancing stability during high-speed machining. Figure 5 is an example of an indexable square shoulder milling cutter:
Indexable square shoulder milling cutter.
Image Credit: https://tse3.mm.bing.net/th/id/OIP.c_FnmJjyqOdY1N3Z943ccwHaHa?rs=1&pid=ImgDetMain
The primary use of indexable square shoulder milling cutters is to create precise 90-degree shoulders, slots, and flat-bottomed cavities in workpieces. They are particularly good at shaping metals, plastics, and composites. These cutters can perform rough and finish milling, making them versatile for various applications across multiple industries, such as aerospace, automotive, and general manufacturing.
How To Select the Correct Shoulder Milling Cutters
Proper shoulder mill selection demands a keen understanding of several crucial factors. Listed below are some aspects to consider:
Workpiece Size
The term "workpiece size" refers to the dimensions and geometry of the item being milled, encompassing its length, width, thickness, and overall shape. A cutter that isn’t right for the workpiece's size could lead to suboptimal results, including excessive tool wear, poor surface finish, and inefficient material removal. If the tool is too large, it can overhang and cause vibration, potentially breaking the tool or harming the surface finish. Conversely, a cutter that is too small could impede productivity, necessitating numerous passes and increasing machining time.
Workpiece Material
The material from which a workpiece is constructed — be it steel, aluminum, composite, plastic, or anything else — has an impact on which milling operations can apply and how quickly the operation may proceed. Every material has its hardness, toughness, and thermal conductivity characteristics, so the cutting tool must be tailored appropriately. A mismatch can result in excessive tool wear, diminished surface quality, or even catastrophic failure. An alloy-optimized cutter, for example, might thrive on ferrous metals but falter on softer plastics.
Spindle Speed
Spindle speed is the cutting tool’s rotational velocity, expressed in revolutions per minute (RPM). An inadequate spindle speed can induce tool wear and harm the cutter's longevity, increasing production costs. Conversely, an excessively high speed may lead to too much heat generation and vibration, compromising workpiece quality and endangering the machining operation.
Balancing spindle speed with factors like tool material, workpiece material, and cutter geometry is fundamental to the precision and productivity of shoulder milling operations.
Cutter head
The cutter head is the uppermost segment of the shoulder milling cutter. Its design determines the tool’s chip-evacuation capabilities, cutting-edge orientation, and abrasive insert design. You must choose the proper head for your tasks.
The cutter head also governs the cutter's ability to withstand high cutting forces and thermal loads, prolonging tool life. Moreover, it should quickly evacuate chips, averting chip recutting and heat accumulation. It directly influences the precision of the milling process, a paramount concern when tight tolerances and surface quality are non-negotiable.
How Does the Choice of Shoulder Milling Cutter Affect Its Accuracy?
Some shoulder mills are more accurate than others, and they often serve specific materials. The cutter's geometrical characteristics, material, and coating directly impact precision. Using a cutter of the wrong type may give you an undesirable surface finish or even dimensional inaccuracies. The cutter's helix angle, rake angle, and edge radius must align with the specific machining task to ensure accurate results.
The tool’s material composition also plays a pivotal role. The cutter must be compatible with the workpiece material. If it has inappropriate hardness, heat resistance, or wear resistance properties the tool may experience premature wear and tear, reducing accuracy over time. Coatings on the cutter, such as TiN (titanium nitride) or TiAlN (titanium aluminum nitride), enhance lubricity and wear resistance, improving accuracy by extending tool life and reducing friction-induced errors.
What Are the Advantages of Shoulder Milling Operation?
Shoulder milling is a very useful machining process. First, it can enhance surface finish precision. Shoulder milling can yield remarkably smooth surfaces with exceptional dimensional accuracy using specialized cutters and a lateral approach. This is particularly critical where components must fit together seamlessly.
Moreover, the tool's ability to engage a workpiece at various depths allows for versatile machining. It excels at producing complex contours and maintaining tool stability, which can be challenging with other milling methods. Additionally, the operation minimizes tool deflection, reducing the risk of workpiece damage and extending tool life.
Efficiency is another critical advantage. Shoulder milling generates minimal heat, safeguarding the workpiece from thermal damage. Its capacity to remove material swiftly, thanks to multiple cutting edges, makes it a time-efficient choice. Furthermore, shoulder milling is cost-effective. Minimal tool changes, long tool life, and low energy consumption contribute to cost savings.
Is Shoulder Milling Expensive?
Yes. Shoulder milling is often considered an expensive machining method due to several key factors. First, the cost of tooling tends to be higher than for the likes of end mills and face mills. This arises from the intricacy of shoulder milling cutters and the need for superior materials to ensure their quality.
In addition, the setup process for shoulder milling can be more time-consuming than other milling techniques. You must meticulously position the tool to hit the proper depth and width. Furthermore, the actual machining cost for shoulder milling tends to be higher. This is mainly because shoulder milling necessitates slower feed rates and increased spindle speeds to achieve its aims.
Is Shoulder Milling Safe?
Yes. Shoulder milling is safe as long as proper safety precautions are taken. Nonetheless, it's essential to be aware that shoulder milling can pose certain dangers if not executed correctly. One significant hazard is the potential for flying debris, which can injure the face or eyes. Loose clothing, hair, or jewelry can also potentially get caught in the rotating mill. Such incidents have caused major injuries and fatalities. All moving components on a milling machine pose a potential threat.
To mitigate these risks, always adhere to proper safety precautions. First, wear appropriate personal protective equipment (PPE). Secure loose hair and jewelry and fasten your clothing so that it doesn’t hang away from your body. Maintain awareness of the moving parts of the shoulder milling machine and use a protective guard on the machine to shield against flying debris. Finally, always stand clear of the shoulder mill while it operates.
What Are the Tips for Effective Shoulder Milling?
Certain guidelines are used across all industries to achieve optimal shoulder milling results. Here's a list of tips for successful shoulder milling:
- Choose a suitable shoulder mill for the specific material and application. Different materials require different tool geometries and coatings for optimal performance.
- Adjust the cutting speed, feed rate, and depth of cut to meet the needs of your workpiece material. Consult tool manufacturer recommendations or machining handbooks for guidance.
- Regularly inspect the shoulder mill for wear, damage, or dullness.
- Ensure the workpiece is securely clamped or held in place.
- Use the appropriate coolant or lubricant to reduce friction and dissipate heat. Proper lubrication extends tool life and enhances surface finish.
- Keep the milling machine stable and well-maintained.
- Wear personal protective equipment, including safety glasses, face shields, and gloves.
- Plan the toolpath to minimize tool engagement and ensure smooth chip evacuation.
- Employ chip-breaking techniques and tools with chip breakers to maintain a clear workspace and prevent chip accumulation.
- Minimize tool overhang, as excessive overhang can cause tool deflection and poor surface quality. Use tool holders with sufficient rigidity.
- Understand the properties of the workpiece material — including hardness and thermal conductivity — before selecting your tool.
- Have a tool replacement plan to minimize the impact of unexpected tool failures.
- Ensure the machine operator is well-trained and knowledgeable about shoulder milling techniques.
- Maintain a clean and organized workspace, free of debris or obstructions.
What Is the Difference Between Shoulder Milling and Face Milling?
Face milling is a type of shoulder milling that refines the flat surface of a workpiece. This process often produces large, continuous chips and removes material quickly. It is particularly effective for achieving precise and flat surface finishes.
Shoulder milling, as the name implies, is aimed at creating precise 90-degree shoulders on a workpiece. A shoulder mill is designed for cutting in perpendicular or axial directions. This process can create distinct shoulder features on components.
To learn more, see our guide on Face Milling.
What Is the Difference Between Shoulder Milling and End Milling?
End milling is a type of shoulder milling that is intended for profiling, slotting, and contouring. It deploys end mills, and tools with cutting edges at the tip. This technique also caters to a broad spectrum of materials, including metals, plastics, and composites.
One significant disparity is in the types of cuts. Shoulder milling specializes in forming precise shoulders or square edges. In contrast, end milling leans towards creating intricate, curved contours and slots. Furthermore, tool geometry varies; shoulder mills have straight edges suitable for 90-degree shoulders. End mills sport various cutting profiles, allowing for diverse shapes and angles.
Regarding tool engagement, shoulder milling operates more shallowly, focusing on the shoulder alone. End milling can penetrate deeper into the material, leading to versatile machining capabilities. Finally, the practicality of these methods varies. Shoulder milling excels when sharp shoulders are imperative, such as when assembling mechanical components. End milling, on the other hand, is a go-to choice for intricate design and profiling, making it more suitable for creating complex shapes and slots.
To learn more, see our guide on End Milling.
Summary
This article presented shoulder milling, explained it, and discussed its process and various types. To learn more about shoulder milling, contact a Xometry representative.
Xometry provides a wide range of manufacturing capabilities, including machining and other value-added services for all of your prototyping and production needs. Visit our website to learn more or to request a free, no-obligation quote.
Disclaimer
The content appearing on this webpage is for informational purposes only. Xometry makes no representation or warranty of any kind, be it expressed or implied, as to the accuracy, completeness, or validity of the information. Any performance parameters, geometric tolerances, specific design features, quality and types of materials, or processes should not be inferred to represent what will be delivered by third-party suppliers or manufacturers through Xometry’s network. Buyers seeking quotes for parts are responsible for defining the specific requirements for those parts. Please refer to our terms and conditions for more information.
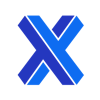