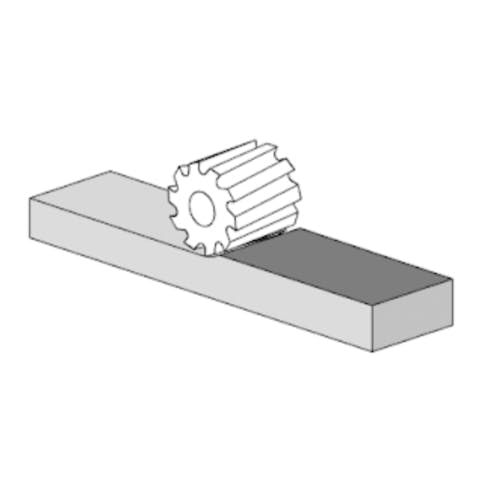
Plain Milling: Process, Uses, Advantages, and Disadvantages
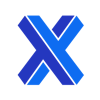
Plain milling is a technique in which the cutting tool axis is parallel to the work surface and the cutting edge is on the periphery of the cutting tool. This design achieves greater contact between the cutting surface and the work surface, allowing for fast removal of material. While plain milling can remove material fast, it also leads to a more coarse surface finish when compared to other milling processes
This article will discuss what plain milling is, how it works, its uses, advantages, and disadvantages.
What Is Plain Milling?
Plain milling, which is also referred to as surface milling or slab milling, is a process used to machine away material with the spinning axis of the tool parallel to the surface of the workpiece. In plain milling, the workpiece is fixed to the bed of the machine as the rotating cutter machine's material from the top face of the workpiece.
What Is the Purpose of Plain Milling?
The purpose of plain milling is to remove material to create a flat surface parallel to the axis of the tool. Plain milling is comparable to face milling. However, it is better suited for the removal of a large amount of material. The purpose of plain milling is not to create a fine surface finish, although the choice of a plain milling tool can impact this measure. Plain milling is also unable to produce geometric features.
Are Plain Milling and Peripheral Milling the Same?
Plain milling and peripheral milling are very similar, but not the same. While plain milling is a form of peripheral milling, not all peripheral milling is plain milling. However, in both instances, the axis of the tool is parallel to the work surface and the cutting is performed by teeth on the periphery of the cutting tool, hence the name.
What Is the Plain Milling Process?
The first step of plain milling operations is choosing a light- or heavy-duty cutter and fitting it to the milling machine. For the removal of a large amount of material, a more coarse tool should be used and vice versa. Additionally, when using coarse tools a high table speed and a lower tool speed should be selected and vice versa. Next, the workpiece is secured to the workbench. The work can be held either in a universal vise or in an adjustable angle plate. The alignment of the machine bed should be checked to ensure the cuts made are level. Once these steps are completed the cuts on the work can be made.
How Is Plain Milling Used in Manufacturing?
In manufacturing, plain milling is used in the creation of a large, flat horizontal surface, which is parallel to the axis of the cutting tool and parallel to the machine bed. Plain milling is used to do this in manufacturing as it is the quickest and most effective way of removing material to create a flat surface.
What Are the Applications of Plain Milling?
Plain milling is best suited for the removal of a large amount of material due to the large contact between the cutting teeth and the workpiece. This leads to applications including:
- Shaping
- Creating level faces
- Creating slots
What Are the Types of Plain Milling Cutters?
There are two types of milling cutters, referred to as heavy-duty and light-duty plain milling cutters. These two types are discussed below:
1. Heavy-Duty Plain Milling Cutters
Heavy-duty cutter tools have fewer teeth and a greater helical angle than light-duty cutters. The helical angle of heavy-duty cutters is between 25°–45°. The lower number of teeth gives heavy-duty cutters a more coarse cut which is used to remove larger amounts of material than light-duty cutters. Heavy-duty cutters are used for shaping rather than finishing operations.
2. Light-Duty Plain Milling Cutters
Light-duty cutters are used for less intensive machining and have more teeth and a helical angle of less than 25°. Light-duty cutters are used for finishing operations when less material removal and a finer surface finish are required.
How To Choose a Plain Milling Cutter?
The choice between a light-duty cutter or a heavy-duty cutter depends on the cut being made. If the cut aims to remove a large amount of material and the surface finish isn't a priority, then use a heavy-duty cutter. A heavy-duty cutter has fewer teeth which makes it more coarse; this allows it to operate with a high table feed rate and a lower spindle speed. If the cut aims to remove a small amount of material and leave a fine surface finish, choose a light-duty cutter with more teeth that operates at a higher spindle speed and low table feed rate.
How Does Xometry Help in Choosing the Right Plain Milling Cutter?
Xometry is both ISO 9001 certified and a plain milling service provider that can help you choose the right plain milling process for your specific application. Xometry can provide a quote to suit your plain milling requirement in minutes here. Using Xometry’s milling service removes the stress of having to choose the right plain milling cutter for your application.
Is Choosing the Right Plain Milling Cutter Important?
Yes, choosing the right plain milling cutter is important. Some tools may be able to do more than one job but usually a particular tool is always more effective. For starters, the tool material is important. High-speed steel tools may be poor at cutting steel; using a cemented carbide tip tool will increase efficiency and reduce tool wear. Tools with more teeth, or flutes, are designed for slower feed rates, and lower overall material removal. Conversely, tools with more teeth have a slower feed rate and remove a smaller amount of material.
What Are the Materials Suited for Plain Milling?
There is a range of materials that can be plain milled, which mostly include metals. Materials for plain milling can include: copper, aluminum, steel, titanium, nylon, acetal, PVC, HDPE, and carbon fiber.
What Are the Advantages of Plain Milling?
There are several advantages to using plain milling over other operations, these include:
- Efficient process for removing a large amount of material
- Light-duty cutters provide a fine surface finish
- Is the most efficient way of creating a level face
- Standard tooling reduces tooling costs
What Are the Disadvantages of Plain Milling?
There are some disadvantages of plain milling to be aware of which are:
- Inability to create geometry
- Coarser surface finish than face milling
- Requires a horizontal milling machine
What Are the Common Issues With Plain Milling?
Some issues may arise during plain milling which include:
- Vibration
- Formation of burrs
- Burning of metal due to excessive heat/poor cooling
- Heavy-duty cutters achieve a poor surface finish
Is Plain Milling for Beginners?
Yes, plain milling can be performed by milling beginners as it is a relatively simple process that has a limited number of variables compared to other milling operations. Milling operations require the selection of the appropriate tool, basic machine setup, and a calculation of feed rate and spindle speed. This is less complex than slot milling, chamfering, or straddle milling.
Is Plain Milling Dangerous?
Yes, plain milling may be considered dangerous if not used properly, for a few reasons. The main hazard of plain milling, as with any milling, is the risk of entanglement. Milling machines are very powerful, and if any loose items including clothes or hair get caught it will result in serious injury. There is also the risk of swarf which can cause burns or damage to the eyes. And finally, there is a risk of fire if the tool and material overheat. However, all of these risks can be minimized with the use of machine guards, PPE, and training.
Is Plain Milling Expensive?
No, plain milling is not expensive compared to other forms of milling. This is because plain milling only uses standard tools: heavy-duty cutters and light-duty cutters. The simplicity of the selection of tools keeps the cost of plain milling operations low.
What Is the Difference Between Plain Milling and Face Milling?
In plain milling, the spinning axis of the tool is parallel with the top face of the workpiece. With face milling the spinning axis of the tool is perpendicular to the surface of the workpiece. This results in one main difference, which is that in plain milling there is more of the cutting edge in contact with the surface of the material. This leads to plain milling being more effective at removing a large amount of material. Since face milling removes less material at a time it is better for producing finer surface finishes.
To learn more, see our article on What is Face Milling.
Summary
This article presented plain milling, explained it, and discussed its process and various uses. To learn more about plain milling, contact a Xometry representative.
Xometry provides a wide range of manufacturing capabilities, including machining and other value-added services for all of your prototyping and production needs. Visit our website to learn more or to request a free, no-obligation quote.
Disclaimer
The content appearing on this webpage is for informational purposes only. Xometry makes no representation or warranty of any kind, be it expressed or implied, as to the accuracy, completeness, or validity of the information. Any performance parameters, geometric tolerances, specific design features, quality and types of materials, or processes should not be inferred to represent what will be delivered by third-party suppliers or manufacturers through Xometry’s network. Buyers seeking quotes for parts are responsible for defining the specific requirements for those parts. Please refer to our terms and conditions for more information.
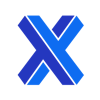