
Tapping in Machining: Definition, How It Works, Types, and Processes
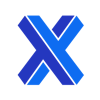
Tapping in machining refers to the process of creating threaded holes in a workpiece to accommodate screws, bolts, or other threaded fasteners and attachments. It is typically performed using a thread-cutting tool called a tap. Tapping is the crucial process for creating secure, precise, and reusable threaded connections in metal and many machined plastic parts, across all industries. It requires a clear understanding of taps and their operation, appropriate hole sizes, and cutting operations to achieve precise and consistent threads. Effective and appropriate lubrication is also essential, to reduce friction and tool wear during the tapping process and to maintain good surface quality on the cut threads.
This article will discuss tapping in machining, how it works, the types, and the processes.
What Is Tapping?
Tapping involves creating threaded holes in a workpiece. These threads are designed to enable engagement with machine screws, bolts, and other threaded features. It allows them to be securely engaged in their intended holes. Anywhere that a machine screw or bolt engages with a component, the hole is likely to have been tapped.
The process involves the use of a cutting tool called a tap. The tap is essentially a screw made of hard material, with straight or helical flutes cut into it. These flutes expose cutting edges that perform the thread-cutting process. The tap can be operated manually using a tap wrench, engaged using a drill press tapping machine, or employed in a manual or CNC machine tool setup.
The precision of tappings is crucial to ensure that threaded connections are strong, secure, and function as intended and the cut thread can appropriately resist the expected shear forces resulting from a fastener being tightened into the threaded hole.
Appropriate tool selection, hole preparation, cutting speeds, and lubrication are all factors in achieving successful tapping operations, resulting in whole, strong, and cleanly cut threads.
What Is the Purpose of Tapping in Machining?
A tapping machine, tapping press, or tapping center is a specialized machine that facilitates accurate and efficient tapping of multiple holes. They are designed to operate a standard series of taps to cut internal threads into pre-drilled holes in workpieces. Tapping facilitates precise control over thread depth and the cutting process, ensuring greater uniformity and consistency of threads in multiple workpieces. Additionally, they improve operator efficiency by more rapidly creating threaded holes with better repeatability despite the faster throughput, compared to manual tapping.
Automated tapping machines further reduce the dependency on operator skill by removing all manual operational processes and allowing the operator to act simply as a loader/unloader. Tapping machines can generally accommodate a very wide range of workpiece sizes and materials, though workholding may require customization for high efficiency and precise part location. They can be operated with all types of taps to produce varied thread profiles—standard metric, UNF, UNC, acme, etc. Automation in turn reduces unexpected forces and poor operation, reducing breakages and wear of taps.
Is Tapping the Same as Drilling?
No, tapping is not the same as drilling. The action of tapping is to use a straight fluted multi-point thread-cutting tool—the tap—to remove material from the wall of a hole, to impose a thread form of a larger tip, or maximum diameter than the hole into which it was cut.
In certain instances, the drilling operation that precedes tapping is performed with a combination drill and tap tool, in which the drill presents the cutting tip that forms the hole, and a tapping region is machined onto the flutes above the tip, to switch from drilling to tapping as the operation proceeds. These tools are unusual in that they use helical flutes like a twist drill, to allow effective bulk chip clearance from the drilling stage and they are used for relatively low-criticality and low-precision threading.
How Does Tapping Work?
Thread tapping is a manual or machining process that cuts the full spectrum of smaller-diameter internal threads. The taps are positioned at an angle between the cutting face and the tap's axis which is referred to as the helix angle. This allows the cutting face to engage more progressively in machine taps, reducing cutting forces and tool wear, as well as improving surface finish.
As the tap rotates, the cutting faces engage with the wall of the hole, dragging the sharp edges of the cutting faces into the material and removing the material to expose the thread. This action involves the cutting faces of the tap shearing material away, creating the thread profile. Swarf is generated during the process which is evacuated via the flutes of the tap.
At the tap tip, a taper is applied which reduces the cutting teeth from their full height. This enables multi-pass cutting in a single rotation, as many teeth of increasing height engage with any given point, as the tap draws itself into the hole by rotation. Proper lubrication is essential, to reduce friction and tool wear and to reduce the incidence of snagging, in which the cut stalls and the risk of tooth or shank breakage greatly increases.
Precise alignment of the tool to the hole is also essential. At the start, there is generally little to no engagement between hole and tap, so the alignment must be imposed by the operator or the machine. Errors in tap alignment will result in defective threads.
What Is the Importance of Tapping in Manufacturing?
Tapping is a critical and central function in most areas of industry. It is the only practical method for creating screw threads in machined metal and plastic components.
What Are the Different Types of Taps?
Various types of taps are used for specific applications and materials. The three main types are:
- Taper or Starter Taps: Taper or starter taps have a gradual taper cut onto the first 20–30% of their functional length, allowing gradual engagement and better self-centering when starting threads.
- Plug Taps: Plug taps have a shorter tapered region and are used to progress threading more deeply after a taper tap has started the process.
- Bottoming Taps: Bottoming taps have no taper but a slightly chamfered tip to ease engagement with an already part-formed thread. They are used to thread the bottom of blind holes.
What Are the Different Tapping Processes?
The different tapping processes are listed below:
1. Tapping on the CNC Lathe
Tapping on a CNC (Computer Numerical Control) lathe involves cutting threads into a workpiece using a tap or a thread mill. First, secure the workpiece in the lathe's chuck. Then securely insert the tapping tool into the lathe's tool holder or turret. Use the CNC controls to jog—align the tapping tool with the workpiece, where X-Y axis adjustments are available. Set appropriate spindle speed and feed rate for tapping.
Next, load the CNC program that includes the tapping operation. Once the CNC program is initiated, the lathe will move the tapping tool into the workpiece, engage it with the workpiece, and begin cutting threads with coolant applied. While tapping is in progress, the CNC control continuously monitors the process. More-advanced equipment may include features to detect issues like: excessive torque, tool breakage, or tap wear.
2. Hand Tapping
Manual tapping is a more delicate and skilled operation and requires some experience. It starts with firmly mounting the workpiece in a vice or work holder. Then, select an appropriate tap for the required thread and cutting stage (taper or plug for starting to thread a hole). Fit the tap to a suitable tap wrench, ensuring it is firmly clamped. Next, apply an appropriate cutting compound to the tap and engage its taper with the hole.
While applying axial load to force the tool, rotate the wrench to begin to engage the cutting faces with the bore. This will feel uncertain at the start but will quickly centralize if the engagement remains straight. Once the cut feels secure, advance by a half turn and then retract by a quarter turn, to break off the chips formed. Complete the first pass to finish the entry threads. Change to a bottoming tap if the hole is blind or the space beneath is restricted. Ensure perfect engagement as a second (misaligned) start will create a weak and damaged thread that is at risk of cross-threading when a fastening is fitted. Complete the thread, remove the tool, and clean the swarf.
How to Choose a Tapping Tool?
Choosing the right tapping tool requires consideration of a few factors. First, determine the specific requirements of your application. Consider factors such as: the material being tapped, the type of hole (through-hole or blind hole), and the thread size, profile, and pitch. Next, determine the equipment and methods to be used: manual, manual machine, lathe, mill, or CNC machine. Consider the coating or surface treatment of the tapping tool to reduce friction and heat generation during tapping of extensive workload. Ensure that the tap's direction matches the equipment setup direction.
Next, consider the required thread tolerance, pull-out strength, and quality. Also, consider the tap's design for effective chip evacuation. Taps with spiral flutes or spiral point (gun) taps are better at removing chips from the hole. Determine if your application involves through-hole or blind-hole tapping and select the degree of taper accordingly. Ensure that your tap is compatible with your tapping equipment.
It is often helpful to test options on a sample workpiece to determine which one performs best for your specific needs. Choosing an appropriate tap is essential to cutting accurate and repeatable threads
How Does the Size of the Tapping Tool Affect Its Accuracy?
The size of the tapping tool, specifically its diameter and pitch, can significantly affect the accuracy of the threading operation, depending on several factors. For example, using an improperly sized tap can result in threads that are too loose or too tight, leading to functional issues. Proper alignment and centering are also essential for creating straight and accurate threads. If the hole is undersized, precise alignment will be hard to achieve. Additionally, the relative size of the tap and hole affects how much material it engages with during the tapping process. Heavier engagement requires more force, which can result in inaccuracies, tool breakage, or damage to the workpiece.
Choosing a tap of appropriate length can improve precision and is necessary to allow full depth of thread over the required region. The size and design of the tapping tool's flutes or grooves play a role in chip evacuation during tapping, reducing the risk of thread or tool damage.
Does the Weight of the Tap Affect Its Accuracy?
No, the weight of the tap itself typically does not have an impact on tapping precision, which depends on skill and equipment factors. However, the weight of the tap can indirectly affect tapping performance in repeated manual operations, through user fatigue.
When To Use Tapping?
Tapping by various methods is the necessary step to generate internal threads in already drilled holes.
Is Tapping Very Common in Engineering?
Yes. Tapping is among the most common actions in the engineering manufacture of metal parts. Every thread must be cut individually, and tapping is an overwhelmingly common method for holes up to 20mm or ¾” in diameter, though lathe thread cutting becomes increasingly common above these sizes.
How Deep Can You Tap a Thread?
The limiting factor in the depth of thread cutting is the length of the tap shank, or in some cases the accessibility of the tool in presenting to the workpiece over a long tapping process. For example, it is typical for an M3 tap to be able to cut a thread to the limit of its 40–50 mm shank, as long as the tap wrench or machine chuck can approach close to the surface without obstruction.
What Are the Advantages of Tapping?
Tapping offers significant advantages such as:
- A cost-efficient method for creating threads in materials, compared with all other methods.
- Produces precise and accurate threads.
- Can be applied to the widest range of materials, from metals to composites, from ceramics and plastics, and also natural materials such as wood.
- It is quick, especially for small-scale production.
- Provides consistent thread quality and pitch when performed well.
- Generates minimal waste.
- Allows for the creation of various thread types, such as: metric, UNF, UNC, and specialized threads like NPT and acme.
- Can be used for both through holes and blind holes.
- Manual tapping is straightforward and low-cost to set up, and automated CNC tapping machines offer precise control and repeatability.
- Is valuable for repairing damaged threads in existing components, extending their service life.
What Are the Disadvantages of Tapping?
While tapping is a widely used method for creating threads in various materials, it does have some disadvantages and limitations such as:
- Can be challenging and less effective in extremely hard materials, requiring specialized taps or alternative threading methods.
- Tapping tools can wear out relatively quickly, especially when used on harder or abrasive materials.
- Taps are relatively delicate cutting tools that break or chip easily.
- The length of threads created by tapping is limited by the length of the tap.
- Ensuring consistent and high-quality threads can be challenging, using manual tapping.
- Effective chip evacuation is essential to prevent tap breakage and maintain thread quality, and this can be challenging—especially in blind holes.
- Manual tapping relies heavily on operator skill and experience. In manual tapping, there is a risk of cross-threading, especially when starting the tap incorrectly, which can damage both the tap and the workpiece.
Can You Tap With a Milling Machine?
Yes, you can tap using a milling machine. This can use standard taps for smaller holes, or thread milling to create threads in larger holes using a specialist milling cutter rather than a traditional tap. Tapping is commonly used in CNC milling machines but can also be performed manually with a milling machine.
Is Tapping Necessary?
Yes. Tapping is an essential function for creating small to medium threaded holes. While there are various approaches to tapping such holes, the alternatives—such as thread-forming screws, and self-tapping screws—offer lower-quality threads, lesser pull-out forces, and poorer reusability in the feature, should the fixture need to be removed and replaced.
What Is the Difference Between Tapping and Thread Milling?
Tapping and thread milling are two distinct machining processes used to create threads in a workpiece, each with its advantages and disadvantages. For example, tapping uses a tap that has all of the thread diameter and tooth profile in its form, and it cuts the threads as it rotates concentrically with the hole. Thread milling, on the other hand, uses a milling cutter with multiple flutes or inserts to create threads. Instead of cutting threads with a single-point tool like a tap, thread milling removes material by spiraling along the desired thread path.
Additionally, tapping is a faster and more straightforward process for creating threads in certain applications but has limitations in terms of thread type, diameter, and depth. Thread milling offers greater flexibility and versatility. The choice between tapping and thread milling depends on the specific needs of the machining operation and most of all on the intended diameter of the bore to be threaded.
Summary
This article presented tapping in machining, explained it, and discussed how it works and its various types. To learn more about tapping in machining, contact a Xometry representative.
Xometry provides a wide range of manufacturing capabilities, including machining and other value-added services for all of your prototyping and production needs. Visit our website to learn more or to request a free, no-obligation quote.
Disclaimer
The content appearing on this webpage is for informational purposes only. Xometry makes no representation or warranty of any kind, be it expressed or implied, as to the accuracy, completeness, or validity of the information. Any performance parameters, geometric tolerances, specific design features, quality and types of materials, or processes should not be inferred to represent what will be delivered by third-party suppliers or manufacturers through Xometry’s network. Buyers seeking quotes for parts are responsible for defining the specific requirements for those parts. Please refer to our terms and conditions for more information.
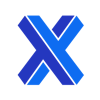