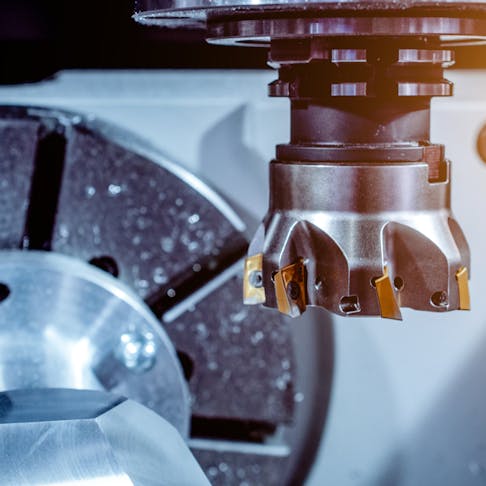
Face Milling vs. End Milling: What Are the Differences?
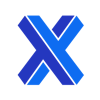
Face milling and end milling are metal removal processes that can both be used for cutting recesses and machining flat surfaces. However, face milling is intended primarily for creating high-quality flat surfaces perpendicular to the cutter spindle, while end milling can perform a larger variety of tasks, creating pockets, slots, recesses, shoulders, profiles, and cavities by cutting mainly parallel to the tool spindle. This article discusses face milling, end milling, and the differences between the two machining methods.
What Is Face Milling?
Face milling is a machining technique that creates a flat surface on a workpiece. In face milling, the cutting occurs using the horizontal face of the milling tool. Face millings often consist of a tool head with inserts that can be changed. A range of tools can be used for face milling.
How Does the Face Milling Process Work?
The face milling process consists of cutting a face that is perpendicular to the tool axis using an end mill, fly cutter, or shell mill. The type of tool used will depend on the application. However, all are used to create flat surfaces on machined parts.
To carry out face milling, the spindle speed, machine feed rate, and other settings appropriate for the workpiece material must first be determined and entered into the cutting program. The workpiece is secured flat on the machine bed so that the face to be cut is perpendicular to the cutting tool axis. Then, the the milling tool is positioned, ready for the cut. The machine must be set for the calculated spindle speed and feed rate, and then the machine can be started and the cutting tool can engage the workpiece. The machining of a face can often be done in one cut, but it may take multiple passes depending on the size of the tool and the face.
Why Use Face Milling?
Face milling is used to generate a flat surface on a part. A face can be generated normally to the axis of rotation of the cutting tool. Face milling is generally used when a large flat surface needs to be produced. They are used in place of peripheral milling to increase the surface finish of the cut, but this comes at the cost of a slower rate of material removal. Face milling is faster than end milling, but creates a more rough surface finish.
When To Use Face Milling?
Face milling is most often used in the creation of a flat face with a medium surface quality finish. It is best at removing a lot of material quickly while retaining an acceptable surface finish. Face milling is used to remove material faster than end milling while also creating a finer surface finish than peripheral milling. Face milling can be used for a range of metals including: steel, aluminum, brass, nickel, and titanium.
What Are the Advantages of Face Milling?
The advantages of face milling include:
- Creates a finer surface finish than peripheral milling (0.4 µm Ra).
- Can be used for a variety of materials.
- High-speed cutting compared to end milling.
- Balanced forces acting on the workpiece during cutting.
- Minimized stress is experienced by the workpiece when the cutting tool engages the workpiece.
What Are the Disadvantages of Face Milling?
Some of the disadvantages of face milling are:
- It can not be used to cut square corners of pockets, only round corners.
- It can cause burning of the material, where the material warps and discolors (although this should be avoidable with a proper supply of coolant).
- Cut depth is limited to 2.8 mm.
- The use of face milling tools (which are often large in diameter) may not be possible if the face being cut already has existing geometry.
What Is End Milling?
End milling is a specific form of milling where the tool has cutting teeth that cut on both the end face and peripheral the cutting tool to cut away material. Unlike face milling tools, end mills have cutting edges on both the end and sides of the tool. This allows end mills to be used for engraving, to make die cavities, and to cut shoulders, contours, slots, and profiles. Figure 1 is an example of a CNC machine performing an end milling operation:
CNC end milling.
Image Credit: Shutterstock.com/Dmitry Kalinovsky
How Does the End Milling Process Work?
The end milling process uses one of several types of end mill tools to cut a workpiece. The end milling process is similar to the face milling process. A workpiece is secured to the machine bed, the right spindle speed and feed rates are chosen, the machine is oriented for the right cutting depth, and then the tool is used to cut. The only difference is that end milling uses both the periphery and the need to cut, whereas the face mill only uses the horizontal face to cut.
Why Use End Milling?
End milling should be used when the application requires both axial and perpendicular cutting. Such applications include milling profiles, slots, contours, die cavities, and shoulders. End milling is also used for the creation of keyways. Although end milling can have a lower quality finish (0.29-0.95 µm), it can create a rough surface finish which is aesthetically pleasing.
When To Use End Milling?
End mill tools are tools that are used for high-precision cuts to make geometry. End milling is used for specific applications including: creating shoulders, slots, profiles, contours, die cavities, counterbores, chamfers, radii, and recesses.
What Are the Advantages of End Milling?
Some of the advantages of end milling are:
- Perform a range of different cuts for different geometric features.
- Good quality surface finish (0.29 - 0.95 µm).
- Application to a wide range of materials.
- Suitable for creating complex geometric features.
- Can make deeper cuts than face milling.
What Are the Disadvantages of End Milling?
The disadvantages of end milling include:
- Costly than the tools used for milling techniques than face milling cutting tools which are simpler in design. Face milling tools also have replaceable cutting tips which can reduce the cost of ownership of the tool.
- Has slower feed rates than face milling.
- Are used at high spindle speed. Any imbalance in the tool (where the center of mass differs from the center of rotation), can result in vibration and unbalanced forces acting on the tool. This can result in a high rate of tool breakage.
What Is the Most Significant Difference Between Face and End Milling?
The most significant difference between face milling and end milling is the cutting tool used. Face mills have a design that only allows them to cut perpendicular to the tool spindle axis. End mills, on the other hand, have cutting edges on both the end and sides of the cutting tool. This allows end milling tools to cut in the horizontal and vertical planes which are parallel and perpendicular to the tool spindle.
How Do You Choose Between Face Milling and End Milling?
While end milling can perform face milling tasks, face milling tools can not complete end milling tasks. Face milling should be used when the application requires a flat face and the removal of a large amount of material. End milling should be chosen when the creation of 3-dimensional profiles is required, which includes: counterbores, chamfers, radii, slots, recesses, shoulders, profiles, and die cavities.
Can an End Mill Be Used as a Face Mill?
Yes, end milling tools can be used for face milling operations. While end mills are different from face mills, because they can cut axially as well as laterally, they can also be used for the same applications. Although face milling is better suited to cutting large flat surfaces, end mills are also capable of cutting flat surfaces.
How Do Face and End Milling Tools Differ in Geometry?
Face milling tools are generally large-diameter tools with cutting inserts on the tool face perpendicular to the spindle. End mills are usually a smaller diameter, and have cutting edges on their end faces as well as several cutting edges on flutes on the sides of the tools.
What Are the Applications of End Milling and Face Milling?
Typical applications of face milling include:
- Leveling surfaces.
- Leveling raised edges.
- Creating pockets and recesses.
- Creating parallel surfaces.
Common applications of end milling are:
- Slotting.
- Profiling.
- Plunge cutting.
- Contouring.
- Counterboring.
The difference in application of face milling and end milling is that face milling generally creates flat surfaces, whereas end milling creates depth cuts such as slots, holes, and recesses. There is some overlap, as end milling can be used to cut flat surfaces, and face milling can be used to create pockets and recesses.
How Is the Workpiece Accessible in Face Milling Compared To End Milling?
In both face milling and end milling, the face of the workpiece is mounted perpendicular to the axis of the tool spindle. In both milling processes, the milling tool may be mounted perpendicular or parallel to the bed of the milling machine depending if it is a horizontal or vertical milling machine. The major difference is that despite the orientation between the tool and workpiece, an end mill can cut in the perpendicular and peripheral directions to the tool spindle axis, whereas the face mill only cuts in the peripheral direction.
What Types of Cutting Tools Are Used for End Milling and Face Milling?
Face milling tools are large-diameter tools that may have several different types of inserts, including:
- Square-end tipped.
- Ball nose.
- Radius tipped.
- Chamfer tipped.
The range of end milling tools includes:
- Square End Mill: Used for general end milling applications.
- Keyway End Mill: Has an undersized diameter used for cutting keyway slots so that the key and keyway fit together snugly.
- Ball End Mill: Has a rounded end used for cutting contoured surfaces in dies and molds.
- Roughing End Mill: Designed for removal of large amounts of material. It produces little vibration during milling but leaves behind a rough surface.
- Corner Radius End Mill: Has a rounded cutting edge and is used for cutting corner radii. Corner chamfer mills have an angled cutting edge used for chamfers.
- Roughing and Finishing End Mills: These are used to remove lots of material and leave a fine finish in one pass.
- Corner Rounding End Mill: Used to cut rounded edges.
- Drill Mill: Used for drilling, spotting, countersinking, and chamfering.
- Tapered End Mill: Has a tapered cutting edge and is used for die and mold cutting.
The difference between these cutting tools is that end milling tools have a cutting surface on the end and sides of the cutting tool, whereas face milling tools only have cutting edges on the face perpendicular to the tool spindle. This is why face milling is primarily used for cutting level faces and end milling is used for contoured surfaces, pockets, slots, and holes.
How Deep Can You Cut With Face Milling and End Milling?
Depth of cut is limited for face milling operations. The usual recommendation is that depth should not exceed 2.8 mm. This value will decrease with an increase in cutting speed. There is no definitive cut depth that covers all situations. However, the depth of the cut is rarely an issue when creating a flat surface, especially since face milling has such a high cutting speed.
With end milling, there is no limit to the depth of the cut that can be made. However, the general rule of thumb is that the depth should be no more than half the diameter of the cut. Otherwise, the risk of a poor quality cut and broken tools rises.
Are Face and End Milling the Most Common Type of Milling in Machining?
Yes, face milling and end milling are both very common machining processes. Other common types of milling machining include: plain, side, straddle, gang, angel, form, saw, gear, thread, and cam milling.
Summary
This article presented face milling and end milling, explained each of them, and discussed their key differences. To learn more about face milling and end milling, contact a Xometry representative.
Xometry provides a wide range of manufacturing capabilities, including machining and other value-added services for all of your prototyping and production needs. Visit our website to learn more or to request a free, no-obligation quote.
Disclaimer
The content appearing on this webpage is for informational purposes only. Xometry makes no representation or warranty of any kind, be it expressed or implied, as to the accuracy, completeness, or validity of the information. Any performance parameters, geometric tolerances, specific design features, quality and types of materials, or processes should not be inferred to represent what will be delivered by third-party suppliers or manufacturers through Xometry’s network. Buyers seeking quotes for parts are responsible for defining the specific requirements for those parts. Please refer to our terms and conditions for more information.
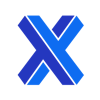