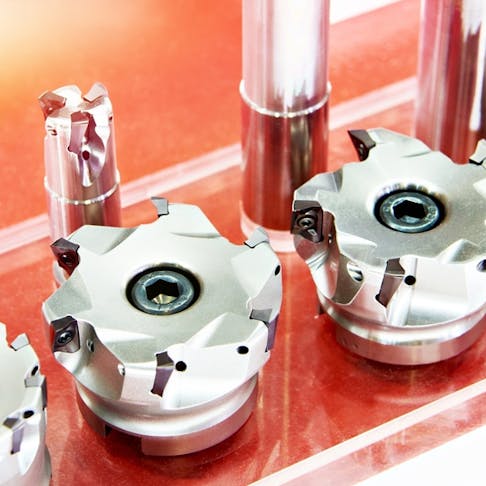
Profile Milling: Definition, Process Types, and Tools
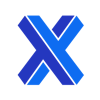
Profile Milling is a computer numerical control (CNC) milling process that is used to create intricate shapes in workpieces. There are four different types of profile milling processes, each of which serves a different purpose: roughing, semi-finishing, finishing, and super-finishing. Aerospace and automotive industries, among others, commonly employ these techniques.
This article looks at how profile milling works, the different tools and process types used in this technique, and some characteristics and considerations when profile milling machine parts.
What Is Profile Milling?
Profile milling is a CNC milling process used to create complex profiles or shapes in workpieces by removing material using cutting tools. It is used to produce components with intricate geometries, tight tolerances, and impressive surface quality.
What Is the Purpose of Profile Milling?
The purpose of profile milling is to create complex geometrical shapes in a workpiece and to produce components with high dimensional accuracy. Another purpose is to achieve extremely smooth surface finishes on vertical or slanted surfaces. Engine components in the aerospace and automotive industries often need this sort of dimensional precision.
What Are the Features of the Profile Mill Machine?
The main distinguishing features of a profile mill machine are its CNC and multi-axis capabilities. Only computer numerical control can give it the necessary precision, and the machine must be able to move on at least 3 axes to produce complex geometries. Profile mill machines also have features found in traditional mills, such as work-holding solutions, coolant systems, chip management systems, and safety systems.
How Much Does Profile Milling Cost?
The costs of profile milling depend on many factors, whether you buy a profile milling machine or use a profile milling service. A profile milling machine can cost anywhere from $50,000 for an entry-level unit, to $500,000 for a production-level machine. The price varies based on the size of the machine, the power, its machining speed, and any additional accessories. This does not include the cost of cutting tools or materials.
The cost of profile milling services can also vary significantly, but will likely be determined by the size of the component, machining time, material selection, and level of precision.
How Does Profile Milling Differ from a Traditional Milling?
Profile milling and traditional milling (also known as face milling) are two types of milling with distinct purposes. Profile milling is used to machine profiles on workpieces, while traditional milling’s purpose is to remove material consistently so as to flatten and smooth a workpiece’s surface.
Traditional milling can be used to cut slots or pockets into a workpiece with reasonable accuracy, but not to the level of complexity or precision that can be achieved with profile milling.
How Does the Profile Milling Process Work?
The profile milling process works by using a CNC profile milling machine to remove material and produce a finished part. The part is designed on computer-aided drawing (CAD) software. After this, a toolpath is generated using computer-aided manufacturing (CAM) software. The toolpath tells the machine how and where to move the cutting tool in order to produce the final design.
Once the workpiece is secured to the machine and setup is complete, the milling process will begin. Material is then removed from the workpiece using rotating cutting tools attached to the milling machine. These cutting tools move across the workpiece according to the toolpath, removing small layers of material each time. Multiple passes are made until the final shape is achieved.
Profile milling consists of multiple processes, such as: roughing, semi-finishing, and finishing. Each process requires different cutting tools and machine settings. The workpiece will go through all these processes before the part is considered finalized.
What Are the Different Types of Profile Milling Processes?
There are four different types of profile-milling processes:
1. Roughing/Semi-Roughing
Roughing or semi-roughing is the first step of the profile milling process. The purpose of roughing is to remove the majority of unneeded material quickly to produce a rough shape that is close to the final design. The roughing stage usually uses a cutting tool that can remove material efficiently, such as an end mill. This is sometimes followed by a semi-roughing stage, where a finer cutting tool brings the part closer to its final state.
2. Semi-Finishing
Semi-finishing is an intermediate step in the profile milling process after the roughing stage is complete. The purpose of semi-finishing is to remove some of the excess material left over from the roughing process and get the part closer to its final shape so that the finishing stage won’t struggle to remove enough material. Semi-finishing tools are typically smaller than roughing tools and have a higher number of cutting edges to remove material more precisely. Ball nose end mills are popular options.
3. Finishing
Finishing is usually the final step in the profile milling process. In the finishing stage, very precise cutting tools shave the part down to its final dimensions, leaving a high-quality surface finish. High-precision cutting tools such as ball nose end mills are used in this stage.
4. Super-Finishing
Super-finishing is an optional step in the profile milling process which is used to achieve even higher-quality surface finishes and tighter dimensional accuracy. The super-finishing stage is usually employed in applications where extreme precision or surface finishes are required, such as in the aerospace industry.
What Are the Different Tools Used for Profile Milling?
Many different types of cutting tools are used in profile milling, depending on the specific milling process. Several are listed below:
1. Ball Nose Exchangeable - Head
A ball nose end mill with an exchangeable head consists of a tool body and an interchangeable ball nose cutting head. The main feature of this cutting tool is the cutting head which can be replaced if it becomes damaged or worn out. This makes it more cost-effective than most, as the entire cutting tool does not need to be replaced.
The ball nose cutter is used for shaping and finishing curves and contours, primarily in the semi-finishing and finishing stages of profile milling.
2. Ball Nose Solid Carbide
Ball nose solid carbide end mills are cutting tools whose cutting tips have radiused end sections. This makes them very effective for producing shapes and finishing contoured surfaces.
Ball nose cutting tools are used primarily for the semi-finishing and finishing processes, as they can precisely remove material to make curved or contoured surfaces with excellent surface finishes.
3. Round Inserts
A round insert cutter features a tool body with several round cutting inserts attached. The cutting inserts are usually indexable with multiple cutting edges, allowing them to be rotated or replaced if they become damaged or worn.
They are primarily used in the roughing process, as they have a large cutting area, and are very efficient at removing material.
4. Ball Nose Indexable
Indexable ball nose cutters are cutting tools that feature a ball nose shape but have indexable cutting inserts. These cutting inserts have multiple cutting edges and can be rotated or replaced if they become damaged, making the whole cutter more cost-efficient.
Indexable ball nose cutters are primarily used in the semi-finishing and finishing stages, as they are designed for the precision removal of material on contoured or curved shapes.
How To Do Profile Milling?
In order to do profile milling, follow these steps:
- Design the part using CAD software. The material selection will also happen in this design phase.
- Generate a toolpath using CAM software. This toolpath will be programmed into the profile milling machine.
- Fix the workpiece to the machine, ensuring stability and proper alignment.
- Set up the machine and select a cutting tool that fits the profile milling stage and the level of precision you need.
- Start machining with the roughing stage, where most of the material is removed to produce a rough shape of the design. This shape will then be refined in the subsequent semi-roughing, semi-finishing, and finishing stages.
When To Use Profile Milling?
Profile milling is used to machine complex shapes into a component. It can also be a good finishing operation for the item’s vertical faces.
What Industries Use Profile Milling?
Profile milling is commonly used in industries that demand precise, dimensionally accurate parts with complex geometries. The aerospace industry is one of the main industries that uses profile milling to manufacture components like aircraft engine parts. The automotive industry also uses profile milling for engine components. Profile milling is a common way to produce complex but accurate molds and dies for injection molding and other manufacturing processes.
What Materials Are Suitable for Profile Milling?
Profile milling can generally be performed on any materials that accept traditional milling. Metals such as aluminum, steel, and brass are the most common targets, but composites and certain plastics such as polycarbonate or nylon are also suitable for profile milling.
What Are the Advantages of Profile Milling?
Profile milling has several distinct advantages, including:
- It produces high-precision components.
- It achieves complex geometries.
- Profile millers can create extremely smooth surface finishes.
- Parts can be produced very efficiently when compared with manual methods of creating complex shapes.
- Parts made this way are all very consistent.
What Are the Disadvantages of Profile Milling?
Profile milling has some disadvantages:
- The precision and complexity required in profile milling operations make the machinery very expensive.
- Skilled and highly trained operators are required in order to run and maintain profile milling machines.
- The setup for a profile milling operation can be time-consuming, especially for complex components.
Can Profile Mills Be Used for Cutting?
No, profile mills cannot be used for cutting in the traditional sense of shearing or separating materials. They do cut in the sense that they use cutting tools to remove materials, but this is done to carve specific profiles into the material.
Is Profile Milling Accurate?
Yes, profile milling can be extremely accurate, especially if a super-finishing process is added. This accuracy is why profile milling is popular in industries where high precision is needed, such as the aerospace and automotive industries.
What Is the Difference Between Profile Milling and Knurling?
Profile milling and knurling are two machining processes with completely distinct uses. Profile milling carves geometric shapes into materials while knurling creates a textured surface on the workpiece. Profile milling’s purpose is to produce a finished part according to a specific design while knurling’s primary purpose is to improve grip or alter the component’s surface to have a particular texture or finish.
What Is the Difference Between Profile Milling and Grinding?
Profile milling and grinding are both machining processes that remove material, but they are quite distinct. The purpose of profile milling is to produce a finished component according to a geometric design. Grinding, meanwhile, is intended to generate a high-quality surface finish or to improve dimensional tolerances by removing any inaccuracies left by other machining processes.
Summary
This article presented profile milling, explained it, and discussed the process in detail. To learn more about profile milling, contact a Xometry representative.
Xometry provides a wide range of manufacturing capabilities, including machining and other value-added services for all of your prototyping and production needs. Visit our website to learn more or to request a free, no-obligation quote.
Disclaimer
The content appearing on this webpage is for informational purposes only. Xometry makes no representation or warranty of any kind, be it expressed or implied, as to the accuracy, completeness, or validity of the information. Any performance parameters, geometric tolerances, specific design features, quality and types of materials, or processes should not be inferred to represent what will be delivered by third-party suppliers or manufacturers through Xometry’s network. Buyers seeking quotes for parts are responsible for defining the specific requirements for those parts. Please refer to our terms and conditions for more information.
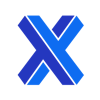