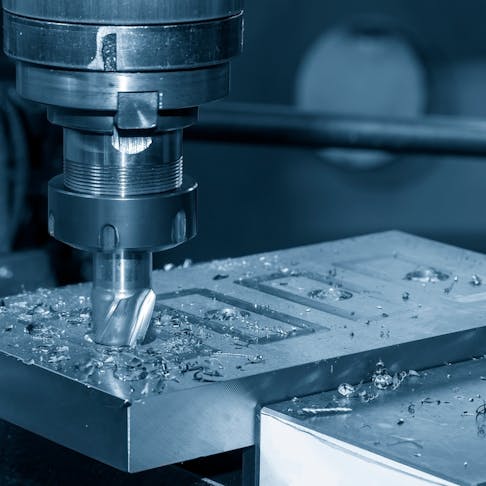
What Is Milling: How It Works, Purpose, and Process
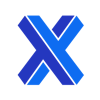
Milling is a generic description for machining processes used in manufacturing to remove material from a workpiece, using rotary cutters. It's a versatile technique that can produce a wide range of shapes, features, and surface finishes in a broad spectrum of materials and via various classes of equipment that loosely fit within the description.
Milling serves in mass production, small runs/one-offs, and repair. Milling is a fundamental machining process employed in various industries, including: manufacturing, aerospace, automotive, and mold-making. It offers versatility, precision, and the ability to produce parts with complex and highly repeatable shapes and dimensions.
This article will discuss what milling is, how it works, its purpose, and the process.
What Does Milling Mean in Machining?
Milling in machining is a much older term than the current usage in metalworking. It originates in the processing of grain to flour using quern stones. A set of quern stones is made up of one static flat stone and one rotating stone with a hole at its center, grain being fed into the hole and flour being expelled at the circumference as the upper quern is rotated. This extremely primitive machine was part of the origin of all rotating machinery, and the term mill broadened in usage to describe all factories early in the Industrial Revolution, later narrowing to primarily describe rotating-tool cutting machines for wood, metal, plastics, and stone.
What Is the Origin of Milling?
The origin of metal milling can be traced back to the development of metalworking processes in ancient civilizations. Early metalworkers used hand tools such as chisels and files to shape and manipulate metals. The concept of rotary cutting was crystalized during the Industrial Revolution in the 18th and 19th centuries when mechanical milling machines were invented. These early machines used rotating cutters to remove metal from workpieces, marking the advent of metal milling as a distinct machining process.
Over time, milling technology advanced, leading to the development of highly precise and automated milling machines, including computer numerical control (CNC) machines, which play a vital role in modern metalworking and manufacturing industries.
What Is the Other Term for Milling?
Another term often used interchangeably with milling in machining is machining. Machining is a broader term that encompasses various processes for shaping and removing material from a workpiece, and milling is one of those specific processes. Other machining processes include: turning, drilling, grinding, and electrical discharge machining (EDM).
As the family of metal processing technologies has broadened, milling has become one of many processes encompassed by machining and more recently CNC machining.
How Does Milling Work?
A hardened-steel or exotic-material cutter is rotated on a fixed X-Y position and its position is able to be adjusted in the Z direction. A workpiece is clamped to a table by various means, to be presented to the cutter. The table is equipped to traverse in the X and Y directions, by winding position control screws. The workpiece and the spindle axis (the quill) are adjusted to pass the workpiece across the face of the cutter for material removal. This involves the material being removed by side cutting, as the circumferential faces of the cutter bite into the workpiece and are traversed in X and Y planes. Either the quill or the table Z axis is adjusted for “plunge” cutting, in which the cutter acts as a drill and the face cuts a cylindrical hole. This can be the preliminary stage in presenting the cutter at the necessary depth to then traverse in X and Y to cut slots and pockets.
More advanced applications of milling can combine the motion of the 3 axes to cut compound and simple curvature, generally under CNC path and speed control. This usually involves automated cutter exchange and some degree of self-calibration to maintain accuracy.
Additional advancements include the ability to tilt the quill to non-vertical positions, to rotate the workpiece on the table, and increasingly to manipulate cutter and workpiece positions in complex and esoteric ways in 6, 9, 12, and more axes.
What Is the Purpose of Milling in the Manufacturing Industry?
Milling is primarily employed in the manufacturing industry to remove material from a workpiece. It allows manufacturers to shape raw materials into specific forms, creating components with desired dimensions and geometries. Milling machines can also achieve extremely tight tolerances and high precision. This is vital in industries like aerospace and medical device manufacturing, in which accuracy is paramount.
Furthermore, milling can provide a range of surface finishes, from rough to highly polished, depending on the cutter and machining parameters. It enables the creation of complex 3D shapes, contours, and features that may be difficult or impossible to achieve with other machining methods. CNC milling machines, in particular, can produce large quantities of identical parts with high repeatability. Milling can be applied to a wide range of materials, including: metals, plastics, and composites.
What Are the Industries That Use Milling?
Milling is used in various industries and plays a central and pivotal role in the manufacturing of virtually all product classes. For example, in the aerospace industry, the milling of high-value, lightweight, and complex parts for any aspect of flight-engineered products is undertaken widely. From airframe components to controls, from flight-surface actuator parts to jet and rocket-engine components, multi-axis CNC milling is the normal production method for most parts.
Milling is also extensively used in the manufacture of surgical tools and medical implants. The ability to process a wide range of biocompatible and easily sterilized materials with high precision and repeatability is greatly valued in these high-value applications. Other industries that use milling are: manufacturing, oil & gas, and infrastructure.
What Are the Different Types of Milling Machine?
Milling machines come in various types, each designed for specific machining tasks and workpiece sizes. The main types of milling machines include:
- Vertical Mill: The spindle axis or quill is oriented vertically. Tasks like face milling and end milling are performed. Smaller workpieces tend to be more applicable.
- Horizontal Mill: The spindle axis is positioned horizontally. Jobs requiring cutting along the entire surface of the workpiece are more applicable. Mass production tasks are common.
- Universal Mill: Features a swiveling table that can alter the workpiece presentation angle. Versatility is greatly increased.
- Turret Mill: There are similarities to a vertical mill but with a turret-style tool head. Multiple cutting tools are immediately available by rotating the turret.
- Bed Mill: A stationary bed supports the workpiece and only the spindle traverses. Larger and heavier workpieces are accommodated without the need for extreme axis drives.
- Knee Mill: A vertical spindle with an adjustable knee is used to allow variation in the angle of the spindle. Greater range in the vertical position of the worktable.
- Ram Mill: The spindle is mounted on a movable ram. Tasks requiring both horizontal and vertical milling can be tackled.
- Planer Mill: A horizontal cutter acts like a planer. The worktable moves perpendicular to the cutter axis, while the cutting tool adjusts vertically.
- CNC Mill: CNC operation allows precise and automated machining. Various configurations are available.
- Gantry Mill: A movable bridge structure that supports the spindle drive. Machining large and heavy workpieces is eased as only the cutter moves.
What Is the Step-by-Step Process of Milling in Machining?
Milling setup and operation is a sequence of skilled stages that must all be performed well, for the result to be useful. Listed and discussed below is the step-by-step process of milling in machining:
1. Loading Workpieces
Depending on the nature of the parts and the volume, the loading of workpieces to be machined can range from being quite low-skilled to highly skilled. Where parts are clamped in a generic restraint such as a vise, or bridge clamped into place using T bolts, the task requires extreme care and precision. Misplacement or poor clamping will result in offset cuts, parts drifting during processing, or parts breaking out during machine operations.
Whenever higher volume dictates the need for specialist nests, these can make setup easy and repeatable, although great skill in such custom nest design and part clamping is required. In extreme cases, for which the volume justifies the investment, loading can be performed by a general-purpose robotic setup or a dedicated loader built into the machine.
2. Selecting Milling Tools
The selection of milling tools can be considered a skilled operation. In a CNC machine with a tool changer, the cutters must be depth referenced and have the correct offsets applied, so the machine has correct awareness of tip and cylindrical positions. In CNC operations, the selection of tools will either occur as part of the automated toolpath generation or as a manual selection by the programmer. Errors in tool selection can have catastrophic results.
3. Setting Up the Machine
The setup of the machine involves clamping and tool selection as the first stages. After this, a range of critical operations must be performed. For a one-off part, the machine must be “taught” the workpiece position. A range of spatial calibration input methods and devices are used, but the central need is to reference the material on three sides (for X-Y-Z positioning) and if necessary “clock” the part as flat onto the table.
With material loaded and calibrated to the spatial reference of the machine, cutters set up for length and diametral offset, coolant supply assured and the guards closed, cutting can commence.
4. Executing Milling
In general, the great majority of milling is performed on CNC machines of varied capability: from 3 to 6+ axes (degrees of freedom). Whether the process is manual or programmed, a similar level of care and attention is required in the motion of the cutter.
The operator will either a) monitor the CNC operation as the machine executes the cutting process or b) operate the machine axes manually to direct the cutter according to the plan. A manual machine requires full operator engagement with all parts at every stage. This includes the constant need to stop operations and check dimensions to affirm correct operation and plan the next cut.
5. Roughing the Material
Roughing involves deep and fast traverse cuts that take off extensive material without much regard to precision—as long as the cut is completed well before reaching the “finished” surfaces to be extracted from the workpiece.
6. Performing Semi-Finishing
Semi-finishing requires shallower cuts and lower feed speeds, to start to impose higher accuracy.
7. Completing the Finishing
Finishing cuts are generally fine and more slowly fed, to deliver the required precision. Some areas will only require roughing, whereas others will require best-possible tolerances, achieved by slow-moving and fine cuts. Finishing is slower and can often consume the majority of the machine's time per part.
8. Unloading the Workpiece
Unloading simply requires the release of the clamping that engages the workpiece and its removal either manually or by a robot. Generally, machine cleaning is performed at this stage, to leave the machine prepared for its next use.
9. Inspecting for Quality
Various measurements and surface quality evaluations will be undertaken, either manually, or using advanced inspection equipment. On occasion, fully automated part checking can be used, for particularly high-volume parts.
10. Conducting Post-Processing
Post-processing can involve simple deburring and packing for storage or later use. It can also involve various types of heat treatment, surface coatings, chemical surface treatments, or plating.
What Are the Materials Suitable for Milling?
Milling is a versatile machining process that can be applied to a wide range of materials, including: metals, plastics, and composites. The suitability of a material for milling depends on factors such as its machinability, hardness, and the specific form of milling operation. Listed below are the materials suitable for milling:
- Metals such as: aluminum, steel, brass, copper, titanium, and nickel alloys
- Acrylic (PMMA)
- Polycarbonate (PC)
- Nylon
- Polyethylene (PE)
- Polypropylene (PP)
- Delrin® (polyoxymethylene, POM)
- Carbon fiber reinforced composites
- Fiberglass (GRP)
- Resin-bonded Kevlar®
- Wood (hardwood, softwood, and man-made boards)
- Ceramics and cermets like alumina, zirconia, and silicon nitride
- Graphite
- Glass
What Are the Two Main Milling Methods?
The two main milling methods are listed below:
1. Climb Milling
Climb milling (or down milling) rotates the tool against the direction of the workpiece's motion, so the tool moves in the same direction as the material feed. This positions the cutter to climb over the workpiece and it is best suited to high-quality parts and thin sections. This results in reduced tool wear, less heat, better chip management, improved surface finish, and lower workpiece deflection.
The choice to use climb milling depends on the workpiece material, machine capabilities, tooling type, and the required part quality.
2. Conventional Milling
Conventional milling (or up milling) is a milling process in which the cutting tool rotates in the same direction as the workpiece's motion, so the tool moves in the opposite direction to the material feed. It is more applicable to higher ductility materials and allows faster machining. This results in progressive cutter engagement, increased tool wear, rougher finish, greater work deflection, and reduced precision.
Conventional milling is a valuable technique in specific machining scenarios in which it provides better results or is more suitable for the given conditions.
How Long Does It Take for Milling To Finish?
It depends. There are too many varied applications of milling to make a general definition of timing possible. However, for the majority of one-off and low-volume components, few alternative processes can compete for speed of outcome, except by sacrificing either material qualities (3D printing for example) or precision (fabrication).
What Is the Precision of Milling in Machining?
The accuracy of a milling machine can vary widely depending on the machine design, component (particularly slide) quality, and the operator.
For many standard milling machines, positional accuracy can range from a few thou (0.001” or 0.0254 mm) to a few ten-thousandths of an inch (0.0001” or 0.00254 mm). Repeatability is the ability of the machine to return to a specific position consistently. Repeatability varies between machines but is generally considered to be 0.001” in well-maintained equipment. Tolerances within a few thousandths of an inch are generally expected, but better machines and user techniques can achieve higher tolerances. All screw feeds (manual or CNC) suffer from a degree of hysteresis (or slack motion), so the direction of motion must be considered, to take up any slack before cutting commences.
Is the Milling Machine Accurate?
Yes. Milling machines are high-value assets that are generally manufactured to precise tolerances and with low hysteresis in their linear and rotary positioning systems. On that basis, the best milling machines are among the most precise instruments made. However, their operation and maintenance can have a marked effect both on their precision and repeatability in a given task and their ability to maintain these criteria long-term. A badly operated or badly maintained machine will deliver poor accuracy and repeatability in the parts it produces.
What Are the Advantages of Milling in Machining?
Milling is a near-universal machining process in manufacturing due to its advantages. Such as:
- Versatility of material.
- Size.
- Quality.
- Precision.
- Delivering complex geometry.
- Surface finish.
- Adaptive to low- and high-volume.
- Low material wastage.
- Speed of processing.
- Ability to automate.
- Overall cost efficiency.
What Are the Disadvantages of Milling in Machining?
Although milling is a versatile and broad-spectrum machining-process family, it carries some disadvantages and limitations. These are:
- Slow processing of heavy cuts.
- Machine complexity/wear.
- Chatter and vibration.
- Slow processing of compound curvatures.
- Tool wear.
- Poor processing of hardened materials.
- Heat generation.
Is Milling Expensive?
It depends. The relative costs of milling and alternative manufacturing processes are highly varied and dependent on a range of factors. At one-off component manufacture, milling is generally the low-cost production method. For simple geometries, hand production by a skilled craftsman is feasible, but considerably slower and more costly. It can, for larger parts with low general tolerances, be cost-effective to sand cast a part and only use milling when higher precision is required as a post-casting treatment. At serial production levels, in which tens to a few hundred parts are required, milling can still be cost-effective when compared with molded plastics or die-cast metal parts. At high-volume production levels (thousands of parts), other methods become highly competitive, against full milling of parts. This can include lower-precision first-step part production such as sand or investment casting, which must often be followed by milling for precision finishing of areas of higher tolerance. This is the norm in large steel and aluminum parts in the automotive sector, for example. For the highest-volume parts, die casting and plastic molding are primary methods for cost reduction, and milling is generally uncompetitive.
Is Milling Popular?
Yes. Milling is among the most centrally important methods used across all manufacturing sectors. It finds application at every level in every sector, from medical to consumer goods, from one-off to mass production, and in the manufacture of alternative tooling that handles the volumes above which milling loses cost-effectiveness. For volume, precision, repeatability, prototyping, toolmaking, and customization/repairs, milling is a go-to process in all production environments.
What Are the Precautions of Using Milling Machine?
The advised precautions for using a milling machine are listed below:
- Always wear appropriate personal protective equipment: safety glasses, hearing protection, and, when necessary, a dust mask or respirator.
- Before operating the machine, inspect it for any visible damage, loose components, or signs of wear.
- Ensure all safety features, such as guards and emergency stop buttons, are functional.
- Never circumvent guards and interlocks.
- Know where the emergency stops are located.
- Keep the work area clean, well-lit, and well-organized.
- Appropriately clamp the workpiece to prevent it from moving during machining.
- Set the correct cutting speed and feed rates for the material and tooling.
- Turn off the machine and wait for it to come to a complete stop before changing tools.
- Keep hands, hair, and other body parts and clothing away from rotating or moving parts of the machine.
- Ensure that operators are properly trained and have a good understanding of the milling machine's operation, safety procedures, and potential hazards.
- Thoroughly adhere to maintenance schedules to keep the machine in good working condition.
What Is the Difference Between Milling and Cutting in Machining?
All milling, in a general sense, involves cutting as rotating tools are passed over a part. It precisely removes chips of material as the teeth cut through the billet to “extract” the required part from a blank. Cutting as a standalone process usually involves a broaching type action, during which teeth pass over the surface of a part in a linear motion to remove an elongated kerf the entire length of the part, resulting in a slot being cut that separates the material into two parts. This motion can be reciprocating (i.e., a saw blade that works in a cut and return sequence) or continuous. The continuous cut can be a bandsaw blade that passes the material in one direction, or it can be a slitting wheel/saw that is circular but traverses the part in a linear motion as it rotates.
The line between milling and cutting is quite blurred in many cases, as milling cutters can often be used for simple cutting tasks. However, linear cutters are not generally used in milling operations.
What Is the Difference Between Milling and Taper Turning?
Milling has developed into a multi-axis methodology that blurs the differentials with other methods/equipment. A 5+ axis CNC mill can perform turning operations as part of its normal programming, with workpieces held in a rotating chuck and presented to rotating or stationary tools to complete full circumferential cuts. Equally, a 3.5-axis CNC machine can perform a tapered (assumed cylindrical) cut-by-side cutting of a circular profile while adjusting the tilt of the arbor/quill to maintain the cylindrical form of the cut.
Taper turning is generally performed on a lathe, with the part spun in a chuck and a non-rotating tool traversed at an angle to the primary axis of the machine, to cut a tapered cylindrical surface. This generally involves setting the compound slide of the lathe to traverse the tool at the required angle, but it can equally be achieved on a CNC lathe by cooperative motion of the longitudinal and transverse axes of the tool motion.
What Is the Difference Between Milling and Swiss Machining?
Swiss machines are, in reality, early versions of multi-axis machining centers, developed for clock/watch mass production in the 19th Century. The addition of cutter rotation that can operate alone or in combination with the part rotation in the chuck allowed the production of flat and square features on otherwise cylindrical workpieces, held stationary in the chuck and cut by traverses of rotating cutters.
It was not until the 1970s that lathes began to be able to encompass these types of combined features, and it has taken the development of 6-axis CNC machines to truly compete with the functionality of Swiss machines.
To learn more, see our article on Swiss Machining.
Summary
This article presented copper, explained it, and discussed its various applications. To learn more about copper, contact a Xometry representative.
Xometry provides a wide range of manufacturing capabilities, including casting and other value-added services for all of your prototyping and production needs. Visit our website to learn more or to request a free, no-obligation quote.
Copyright and Trademark Notice
- Delrin® and Kevlar® are registered trademarks of DuPont.
Disclaimer
The content appearing on this webpage is for informational purposes only. Xometry makes no representation or warranty of any kind, be it expressed or implied, as to the accuracy, completeness, or validity of the information. Any performance parameters, geometric tolerances, specific design features, quality and types of materials, or processes should not be inferred to represent what will be delivered by third-party suppliers or manufacturers through Xometry’s network. Buyers seeking quotes for parts are responsible for defining the specific requirements for those parts. Please refer to our terms and conditions for more information.
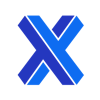