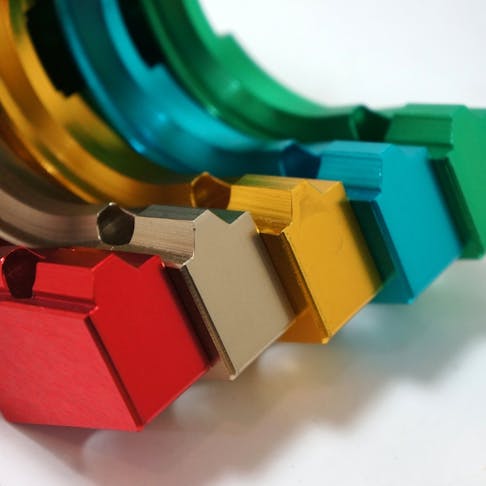
Anodized Aluminum Colors: What You Need to Know
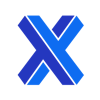
Aluminum that has undergone the electrochemical process of anodization is referred to as anodized aluminum. This procedure improves its longevity and resistance, but it also enables you to apply coloration. Anodization generates a protective oxide coating on the surface of the aluminum. It is essential for halting corrosion and wear.
Aluminum is electrochemically colored by immersing it in an electrolytic solution and running an electric current through it. The oxide layer takes up any dye color in that solution, producing a long-lasting and fade-resistant finish. This uniform, reflective oxide layer is what gives anodized aluminum its gleam. A popular option for many applications, anodization protects the metal better than aluminum’s natural oxide layer in addition to the coloration.
This article will discuss aluminum anodization, the colors available, its purpose, and a lot more.
What Is Anodized Aluminum?
Anodized aluminum is aluminum that has been subjected to an electrochemical process called anodization, creating a protective oxide layer on its surface. This layer makes it more resilient to corrosion and can also accept custom surface coloration.
To learn more, see our guide on How to Anodize Aluminum.
What are the Available Colors for Anodized Aluminum?
Aluminum can accept a wide spectrum of anodized colors, including: pink, blue, black, silver, gold, green, orange, red, and purple. Anodization improves the durability, stability, abrasion resistance, and surface polish of these colors by permanently binding them to the metal’s surface and encasing them in a protective oxide layer.
What Is the Purpose of Anodizing Aluminum?
The main goal of aluminum anodization is to change the metal’s surface chemistry. It simultaneously creates a barrier against corrosion, enhances aesthetics, and increases scratch resistance via a very tough and transparent anodic finish.
What Is the Importance of the Anodized Aluminum Process?
The anodization process is significant because it can improve important qualities like wear resistance, corrosion resistance, surface lubricity, heat dissipation, dielectric characteristics, adhesion, and aesthetics. These improvements make it essential in some sectors.
What Are the Stages of Anodizing Aluminum?
Aluminum can go through a multistage electrochemical process called anodization which gives it several advantageous qualities. The stages are listed and discussed below:
1. Pre-Treatment
Before anything else, you must clean and prep the metal item’s surfaces. Any impurities, oils, and existing oxides have to be removed. This step is essential to ensure effective adhesion of future layers and to produce a clean substrate for anodization.
2. Electrolysis
Electrolysis is the core of the anodizing process. In this stage, the prepared aluminum part is immersed in an electrolytic bath, typically containing sulfuric acid. A direct current is applied, causing oxygen atoms to come out of the solution and bind to exposed surface atoms, where they build up an oxide layer. This controlled oxidation is what gives anodized aluminum its unique properties, including enhanced corrosion resistance and durability.
3. Barrier Oxide Film
During the anodizing process, a thin, non-porous "barrier" oxide layer is formed on the aluminum's surface. This first layer acts as a protective shield, preventing further oxidation and enhancing the metal's resistance to corrosion. It also serves as a base for subsequent layers, if color or other finishes are to be added.
4. Porous Oxide Film
In this stage, the anodization process is taken a step further to create a porous oxide film. The oxide layer thickens, allowing it to absorb dyes or other substances for coloration or additional functional properties. The porous structure also makes adhesive materials stick better to the surface. Alternatively, this layer can be sealed for added protection.
What Are the Types of Anodized Aluminum?
The value and purpose of anodized aluminum depend on its type. Three varieties of anodized aluminum are explained below:
1. Type I - Anodized Aluminum
Type I anodization employs chromic acid as the electrolyte. It results in a thin, non-conductive anodized coating that the paint adheres well to. This type is often used for items like architectural components, where maintaining the base material's structural integrity is the top concern.
2. Type II - Anodized Aluminum
Type II anodization uses sulfuric acid as the electrolyte. This process creates a thicker oxide layer around the aluminum and forms a porous anodic finish. The porous structure allows it to absorb dyes, making it suitable for colored finishes. Common applications include consumer products like colored laptop frames.
3. Type III - Anodized Aluminum
Type III anodization, also known as hard coat color anodization, utilizes sulfuric acid. It results in the thickest anodized coating among the three types, offering exceptional wear resistance. Like Type II, it can accept dyes, but the porous layer is covered over by an additional sealing layer. This type is ideal for environments with extreme wear conditions, making it suitable for aerospace or military purposes.
What Are the Other Types of Anodizing Aluminum?
The many types of anodizing processes cater to diverse applications. Each has unique features and advantages. Here are some of those alternate styles:
1. Phosphoric Acid Anodizing (PAA)
PAA is an electrolytic passivation process that alters the microscopic texture of aluminum surfaces. It serves as an excellent pretreatment for adhesives or paints.
2. Clear Anodizing
Clear anodizing is a common surface finishing method. It enhances aluminum's stability, effectiveness, and controllability leaving the metal stronger and more durable than when it began.
3. Black Anodizing
Black anodizing is a standard semi-porous color anodization process that uses black dye. It generates a black surface on aluminum while enhancing corrosion and wear resistance.
4. Color Anodizing
Color anodizing artificially develops an oxide layer on aluminum and adds color to improve both functional and aesthetic properties, including corrosion resistance.
5. Boric-Sulfuric Acid Anodizing
BSAA is another option for chromic acid anodizing that was developed primarily to make the process safer and less environmentally hazardous. It is commonly used in aerospace and aircraft components for corrosion protection and paint adhesion.
6. Bright Dip Anodizing
Bright dip anodizing is an electrochemical process that enhances the functional and aesthetic aluminum properties. It smoothes microscopic roughness, providing an enhanced, highly reflective sheen.
7. Thin-Film Sulfuric Acid Anodizing (Type I b)
This process produces lightweight films that perform well in paint adhesion, corrosion resistance, acid resistance, abrasion resistance, and adhesive bonding.
How is Anodized Aluminum Colored?
Color may be introduced into anodized aluminum using any of the following methods:
1. Dye/Coloring:
If you immerse porous anodized aluminum into a dye solution, the pores will absorb the dye deep enough that it cannot simply be rubbed or scraped off. Color intensity depends on film thickness, dye concentration, immersion time, and temperature.
2. Electrolytic Coloring:
For this version, the metal is placed in a bath with inorganic metal salts after it has already been anodized. Current is applied, depositing salts into pores. Colors vary with metal type and processing conditions.
3. Integral Coloring:
This one-step method combines anodizing and coloring to produce abrasion-resistant oxide cells in bronze and black hues.
4. Interference Coloring:
Modifying pore structure in the presence of sulfuric acid leads to pore enlargement. Metal deposition at the base creates the illusion of color through optical interference effects.
5. Dip Coloring:
Porous parts are immersed in a dye tank, filling pores. Boiling the parts in deionized water stops the reaction. Various colors are available this way, but they have limited UV resistance.
6. Sealing:
This is the anodization finishing stage. Hot water traps dye molecules in pores, preventing them from escaping and unwanted molecules from invading. The procedure involves hydrated aluminum oxide crystallization or metal salt deposition.
What Is the Barrier Layer That is Formed During Anodizing?
The barrier layer created during anodizing is a non-porous, thin, and sturdy aluminum oxide layer. This layer acts as a protective barrier for the underlying metal. It also serves as the foundation for additional oxide layers, contributing to the anodized finish's durability and properties.
How Durable is the Anodized Aluminum Color?
The anodized aluminum color is remarkably resilient, primarily because the color is integrated into the oxide layer. The process makes it resistant to fading, abrasion, and environmental factors, ensuring long-lasting vibrancy.
What Is the Benefit of Anodized Aluminum?
Some important advantages of aluminum anodization include:
- Parts maintain their color stability over extended lifespans. This quality improves the cost-benefit analysis since these colors are far less likely to need maintenance or recoating.
- A wide range of gloss and color options are possible. Anodization allows aluminum’s natural sheen to show through in spite of the coloration, making it relatively unusual among surface finishes.
- Finished parts pose no harm to human health. Anodized finishes are chemically stable, non-toxic, and heat-resistant. Since anodizing reinforces a naturally occurring oxide process, it is non-hazardous and generates no harmful by-products in the anodized item itself (though the electrolytic chemicals are often hazardous).
- Anodized aluminum pieces maintain their mechanical properties far longer than many other materials. The oxide layer integrates with the metal at a molecular level rather than merely adhering to it like paint. This leads to economic advantages through reduced maintenance, replacement, and operating costs.
What Are the Downsides of Anodized Aluminum?
Like anything, there are downsides to using anodized aluminum:
- Maintaining consistency between batches is harder with anodizing than plating. It won’t be the right choice if you expect precise color matching. This is especially a problem in low-grade metals.
- Anodized parts are hard to weld due to the non-conductive oxide layer at the surface. Special techniques and equipment may be needed for welding.
- Anodization can be expensive for small quantities, as it involves both higher-grade alloy requirements and substantial setup costs.
- Only certain grades of aluminum accept this process, limiting your material choices.
What Is the Appearance of Colored Anodized Aluminum?
The appearance of colored anodized aluminum is characterized by a durable, vibrant, and uniform surface. An anodized finish can showcase a wide range of colors and gloss levels, offering both aesthetic appeal and resilience.
Why Does Aluminum Have a Shiny Finish?
Due to a thin oxide layer that naturally develops on aluminum's surface when it is exposed to air, the metal has a glossy sheen. Polishing or anodizing procedures can further develop this layer to give aluminum its characteristic sheen and corrosion resistance.
Does the Anodized Aluminum Corrode?
No. Anodized aluminum is highly corrosion-resistant. The anodizing process forms a protective oxide layer on its surface which shields it from environmental factors. This makes it exceptionally durable even in conditions that damage other metals.
Is the Color of Anodized Aluminum Easy To Peel Off?
No, the color of anodized aluminum does not peel off. The dye gets integrated into the porous oxide layer during anodization making it resistant to peeling, chipping, or fading. It will typically remain as long as the anodized oxide layer survives.
Is Anodized Aluminum Scratch Resistant?
Yes, anodized aluminum is scratch-resistant. The anodizing process hardens the surface, enhancing its durability and resistance to scratches, and making it ideal for applications that demand a tough surface.
Is the Color Palette of Anodized Aluminum Limited?
No. Many colors are compatible with the anodization process. The various sealing and dyeing procedures give you a wide range of color options, from muted to bright.
Can Other Metals be Anodized?
Yes, certain other metals, like titanium and magnesium, can also be anodized using similar electrochemical processes to create protective oxide layers or color finishes.
To learn more, see our guide on Titanium Anodizing Colors: What You Need to Know.
Can I Change the Color of the Anodized Aluminum?
It is difficult to change the color of anodized aluminum. To do so, you typically have to remove the existing anodized coating and start over, adding a new color when you create a whole new anodized oxide layer.
Summary
This article presented anodized aluminum colors, explained it, and discussed the colors available and the process of coloring. To learn more about anodized aluminum, contact a Xometry representative.
Xometry provides a wide range of manufacturing capabilities, including machining and other value-added services for all of your prototyping and production needs. Visit our website to learn more or to request a free, no-obligation quote.
Disclaimer
The content appearing on this webpage is for informational purposes only. Xometry makes no representation or warranty of any kind, be it expressed or implied, as to the accuracy, completeness, or validity of the information. Any performance parameters, geometric tolerances, specific design features, quality and types of materials, or processes should not be inferred to represent what will be delivered by third-party suppliers or manufacturers through Xometry’s network. Buyers seeking quotes for parts are responsible for defining the specific requirements for those parts. Please refer to our terms and conditions for more information.
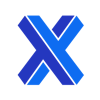