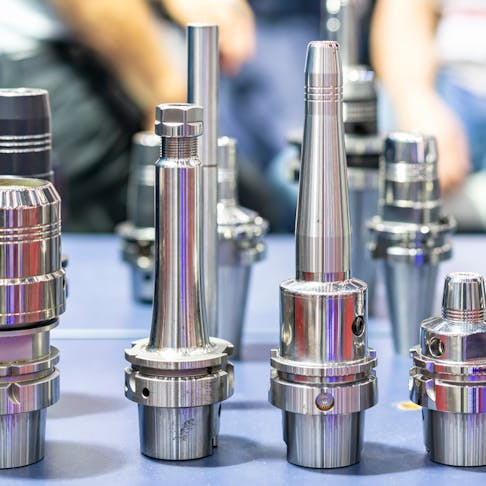
Taper: Definition, Purpose, Types, and Methods
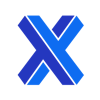
Taper is a word used to refer to a geometrical shape that describes geometry with a gradual reduction in cross-sectional area. Machining tools commonly have a tapered end designed to aid the changing of tools.
This article provides detailed information on the eight types of taper tools used by different machining equipment as well as the different methods of producing a geometrical taper.
What Is Taper?
A taper is a uniform reduction in the cross-section or diameter of a part. When a taper is applied, the resulting part will often resemble the shape of a cone. In the cone example, the cross-section is tapered to a point. However, in the case of a taper tool, the part is just tapered from a wider cross-section to a narrower cross-section.
What Is the Purpose of Taper in Machining?
A machine taper is a tool used to secure tool holders and cutting tools to the spindle head of a machine. Machines that use a taper include handheld drills, bench drills, lathes, and milling machines. The male taper is used to aid the changing over of tools in a machine by making it easy for technicians to locate the taper into the machine head. Using the friction of a tapered interface also reduces the need for a chuck which takes time to manually adjust using a screw mechanism.
How Does Taper Work?
The taper angle of the taper tool and the taper angle in the machine head match to increase the friction between the two parts. For light-duty machining, the friction alone can be strong enough to hold the taper in place. However, for heavy machining, a key and notch are used to prevent the tapered tool from spinning in the machine head.
What Are the Different Types of Taper?
There are eight different types of tapered tools in use which all work on the same principle. The taper tools each vary based on the size they are available in and whether they are quick-release or self-holding. Each of these tapers is discussed below:
1. Jarno
The Jarno taper standard was introduced by Brown and Sharpe Manufacturing. All Jarno tapers have a 0.60" taper-per-foot ratio and are made of 52100 steel. Jarno tapered tools are used as headstock and tailstock spindles on lathes and for profiling and die-sinking machines. Jarno taper has 19 sizes, with the large end ranging from 0.25–2.50" and the small end ranging from 0.20–2.00".
2. Jacobs
A Jacobs tapered tool has a self-holding taper—meaning no drawbar is required. The Jacobs taper ratio will vary depending on the size of the taper. The Jacobs taper is used for light-duty applications since it is self-holding. Jacobs tapered tools are almost exclusively used to secure a drill chuck to an arbor. Jacobs taper comes in 9 sizes, and each size is referred to as JT + a number. For example: JT0, JT2 short, JT2, and JT6.
3. Brown and Sharpe
Brown and Sharpe tapered tools have a standard taper ratio of 0.50" per foot. The Brown and Sharpe taper is made out of 52100 steel, which is the same as the Jarno taper. Brown and Sharpe tapers are most common on older tooling machines for drill bits, reamers, end mill holders, and collets. There are 18 Brown and Sharpe tapers, and they have a large end size between 0.24–3.42" and a small end between 0.20–3.00".
4. Morse
A Morse tapered tool is a tapered spindle used for tool mounting. Morse tapers are used in a variety of applications including: reamers, drill bits, mill holders, collets, and lathe centers. Morse taper is available in eight sizes from MT0 to MT7 and comes as a self-holding taper. All of the different Morse sizes have a taper of approximately 0.625" per foot. The Morse taper end is self-holding and needs to be modified if use with a drawbar is required.
5. B Tapers
Type B tapers are used for: machining centers, high-precision machining, heavy-duty milling machining, and lathes. B taper comes in eight sizes with a large end ranging from 0.25–0.94" and a small end ranging from 0.230.84".
6. HSK Taper
HSK tapers are hollow and short and have a taper ratio of 1 in 10, or 1.20" per foot. The short length of HSK taper tools keeps the spindle of the machine close to the workpiece. There are various uses for HSK taper tools depending on which variant is used, including: lathes, milling machining, and grinding machining. There are 36 HSK sizes which are divided into 6 categories HSK-A to HSK-F.
7. NMTB Taper Family
NMTB stands for the National Machine Tool Builders’ Association, set up in 1927. These tapers have a taper ratio of 3.50" per foot and have 7 common sizes NMTB-25, 30, 35, 40, 45, 50, and 60. The NMTB taper was designed specifically for use in NMTB spindles which use a drawbar to secure the shank in the spindle. There is a single flange on NMTB tapers with two keyways for heavy-duty applications.
8. R8 Taper
The R8 taper is also referred to as the M1TR taper. R8 taper tools, which are secured in their spindles with a drawbar, were designed by Bridgeport Machines, Inc. specifically for use on milling machines. The end of this taper is a direct collet and is held in place by a drawbar. R8 taper tools are available in 26 sizes starting at 1/16" and going up to ⅞" in 1/32" increments.
Where Is Taper Used?
A taper tool is used as an interface between a machine (lathe, milling, or drilling) head and the cutting tool. The taper is used to hold the tool in place and allow for quick changes in tooling. Tapers are also used because they allow large machine heads to use both large and small tools. In comparison, machines that use a single chuck may require a long time to adjust when changing from a large to a small tool, as the chuck needs to be tightened with a screw mechanism.
What Is Taper Turning?
Taper turning is the process whereby a tool is given its gradual reduction in diameter using a lathe. There are many methods to achieve a taper using a lathe depending on how the tool and workpiece are held by the lathe. However, they all achieve the same result. In order to machine a taper, the material is taken away from the workpiece gradually to reduce heat and stress during turning, preventing the metal from overheating or the tool from snapping. The gradual reduction of material also produces a higher-quality surface finish. To learn more, see our guide on What is Turning in Machining.
What Are Taper Turning Methods?
Creating a taper using a lathe is the process of creating a gradual reduction in diameter or cross-section on a tapered tool. There are many ways in which this can be achieved. The methods vary depending on how the workpiece is held, how the tool is held, and how the tool and workpiece interact. Some different methods for taper turning are:
- Tailstock Set Over.
- Taper Turning Attachment.
- Form Tool.
- Combining Feeds.
What Is the Taper Ratio Formula?
The taper ratio is calculated using the formula:
K=(D -d)/L
Where:
K = The taper ratio
D = The large diameter
d = Smaller diameter
L = Length of taper
For example, if the larger diameter is 5", the smaller diameter is 2.5", and the length is 3", then the values can be plugged into the formula as shown:
K=(5-2.5)/ 3
K =0.83
This formula can be used for any unit of measure as long as the units are the same for all values.
How To Calculate the Taper Ratio?
To calculate the taper ratio, measure the large and small end diameters of the taper, as well as the length between the two ends. The measurements can be taken in metric or imperial units as long as all of the measurements use the same units. Plug the numbers into the taper ratio formula. The value provided by the formula will be the taper ratio which denotes the reduction in a cross-section per unit of length.
What Are Example Applications of Taper?
Tapered tools are used to fix cutting tools into various machining equipment including:
- Milling machines are a type of machinery that remove material from an object using rotary cutters. The removal of this material is achieved by holding the workpieces and using cylindrical tools to cut the material in different designs, including tapering.
- Lathes are similar to milling machines and remove excess or unwanted material from objects. Unlike milling machines, however, lathes rotate the workpiece in the horizontal position to eliminate excess material rather than holding it still.
- Pillar drills often use tapered tools for the quick change of drill bits. The use of tapers in pillar drills also allows for the use of a wider range of drill bit sizes than can be achieved with a standard chuck.
Is Taper Only for Cylindrical Objects?
No. While a taper is best suited to cylindrical objects, a taper can be achieved on a square bar, but not through the use of a lathe. The gradual reduction of the diameter of a non-cylindrical object such as a square bar is achieved by tapering at an angle to the axis of the work to produce a taper externally.
Is Tapering Only for Design Purposes?
No. Tapering can be used for design purposes, however, this is not the only purpose. Tapers can be used for ornamental purposes for the end product to look more aesthetically pleasing as well as functional. An example of this would be on columns of buildings. Another crucial purpose of tapering is for mechanical purposes: to quickly and precisely align machine parts.
Is a Lathe Machine Used for Tapering Materials?
Yes, a lathe machine can be used for tapering materials, alongside many other things, as it is one of the most versatile tools within the machining/engineering industry. There are a few different methods of producing a taper on a lathe machine such as: using a form tool, combined feeds, taper turning attachment, tailstock set over, and compound rest. For example, in the combined feeds method, both feeds can be engaged at the same time to allow the cutting tool to move diagonally to the center of rotation creating a taper. To learn more, check out our guide on the Parts of a CNC Lathe Machine.
Summary
This article presented taper, explained it, and discussed its purpose and types. To learn more about taper, contact a Xometry representative.
Xometry provides a wide range of manufacturing capabilities, including CNC machining and other value-added services for all of your prototyping and production needs. Visit our website to learn more or to request a free, no-obligation quote.
Disclaimer
The content appearing on this webpage is for informational purposes only. Xometry makes no representation or warranty of any kind, be it expressed or implied, as to the accuracy, completeness, or validity of the information. Any performance parameters, geometric tolerances, specific design features, quality and types of materials, or processes should not be inferred to represent what will be delivered by third-party suppliers or manufacturers through Xometry’s network. Buyers seeking quotes for parts are responsible for defining the specific requirements for those parts. Please refer to our terms and conditions for more information.
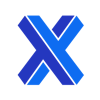