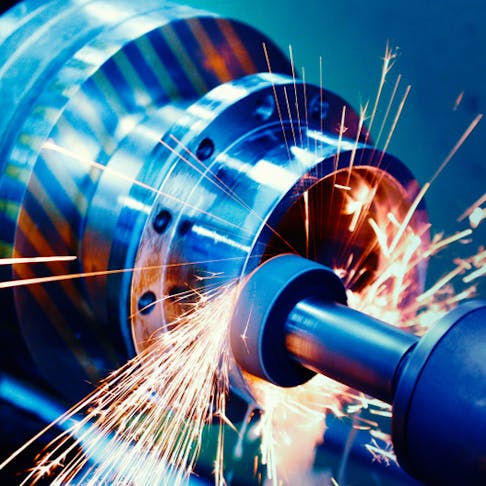
CNC Machining Cost Calculation: Calculator, Factors That Affect Cost, and How to Reduce Cost
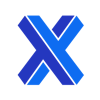
The CNC machining process is critical in modern manufacturing, enabling efficient production of precise components. However, managing the costs associated with CNC machining is essential for businesses to maintain competitiveness and profitability. In this article, we will explore the factors that determine machining costs and provide practical strategies to reduce expenses. We first examine the various factors that influence CNC machining costs, including material selection, complexity of design, machining time, machine tooling, volume and batch size, labor costs, overhead costs, and scrap and rework. Following that, we will delve into actionable tips such as design optimization, material selection and standardization, process optimization, automation and robotics, and supplier collaboration to help manufacturers reduce costs while improving productivity and efficiency.
CNC Machining Cost Calculator
Factors That Determine Machining Cost
The cost of CNC machining projects are influenced by several factors that significantly affect the overall cost calculation. Understanding these factors is crucial for manufacturers seeking to optimize their processes and manage expenses effectively. Let's explore the key elements that determine machining costs:
Material Selection
The choice of raw material has a direct impact on machining costs. Different materials have varying costs, availability, and machining characteristics. High-performance alloys, for example, may be more expensive than common metals. Additionally, the availability of specific materials can affect their pricing. When calculating machining expenses, it's essential to consider the material type required for CNC machined parts and its associated cost.
Complexity of Design
The complexity of the machined part or component plays a crucial role in cost determination. Parts with intricate features, tight tolerances, and complex geometries often require more advanced machining techniques, specialized tooling, and longer machining time. These factors increase the overall cost due to the additional precision and expertise required to produce such complex components.
Machining Time
Machining time is a critical factor in CNC cost calculation. The longer it takes to machine a part, the higher the cost. Machining time includes cycle time (time spent cutting the part), setup time (preparation and tool changes), and overall production efficiency. Optimizing machining processes to reduce cycle time and improve setup efficiency can minimize costs and increase productivity.
Machine Tooling
The choice and management of machine tooling significantly impact machining costs. Tooling costs should be considered, including the purchase, maintenance, and replacement of cutting tools. The life of the cutting tools and the time required for tool changeovers affect production efficiency and, subsequently, cost. Proper selection, maintenance, and optimization of machine tooling can help control expenses in CNC machining.
Volume and Batch Size
The volume and batch size of production runs directly influence machining costs. Economies of scale come into play when larger volumes are produced. The cost per part tends to decrease as production quantities increase. However, it's important to consider the balance between volume and setup time. Small batch sizes may have higher costs per part due to increased setup time, while large volumes benefit from reduced setup time and lower costs per part.
Labor Costs
Labor costs, including CNC machining engineers' wages, contribute significantly to CNC machining expenses. Skilled operators with expertise in CNC programming, setup, and operation are essential for efficient and accurate machining. Labor-intensive operations or intricate part requirements may involve additional labor costs. Finding a balance between skilled labor utilization and cost management is essential in controlling machining expenses.
Overhead Costs
Overhead costs associated with CNC machining operations can impact the overall cost calculation. These include facility expenses, utilities, administrative costs, quality control, and inspection. Managing and optimizing these overhead expenses is crucial for cost control and maintaining a competitive edge in CNC machining.
Scrap and Rework
Scrap and rework costs are an important consideration in machining expenses. Material waste due to errors or deviations from specifications can significantly increase costs. Minimizing scrap through effective quality control measures, precision machining techniques, and robust inspection processes helps reduce material waste and the need for rework, ultimately lowering overall machining costs.
By understanding and analyzing these factors that determine machining costs, manufacturers can identify areas for improvement, implement cost-saving measures, and optimize their CNC machining processes to achieve greater efficiency and profitability.
How To Reduce CNC Machining Costs
Reducing CNC costs requires a comprehensive approach that optimizes various aspects of the manufacturing process. By implementing the following cost-saving strategies, manufacturers can achieve greater efficiency and maximize their cost-optimization efforts:
Supplier Collaboration
Collaborating with CNC machine suppliers is valuable for exploring cost-saving opportunities. Engage with suppliers to negotiate favorable pricing, especially for bulk material purchasing. Manufacturers can optimize supply chain logistics, improve delivery times, and reduce transportation costs by establishing solid supplier relationships. Collaborative efforts can also lead to developing innovative solutions and cost-saving recommendations based on suppliers' expertise and CNC machining industry knowledge.
By implementing these cost-saving strategies, manufacturers can effectively reduce CNC machining expenses and enhance their competitive edge in the market. A comprehensive approach that combines design optimization, material selection, process optimization, automation, and supplier collaboration can result in significant cost savings while maintaining high-quality production.
Design Optimization
Designing parts for manufacturability is crucial for cost reduction in CNC machining. Manufacturers can streamline the machining process and minimize material waste by simplifying the geometry, minimizing tight tolerances, and reducing the number of operations. Collaborating with design engineers to optimize part designs for CNC machining can significantly reduce production time, tooling requirements, and overall costs.
Material Selection and Standardization
Careful material selection and standardization can significantly save costs. Manufacturers can reduce material expenses by choosing cost-effective materials that meet the required specifications. Standardizing material options across product lines can simplify procurement, minimize waste, and enhance machining efficiency. Material availability, price, and compatibility with machining processes should be considered during material selection.
Process Optimization
Optimizing the machining process is essential for cost reduction. Optimizing the process involves evaluating and refining various aspects of production, including toolpath optimization, minimizing setup time, improving machine utilization, and implementing lean manufacturing principles. Manufacturers can increase productivity and lower costs by optimizing toolpaths to reduce unnecessary movements and minimize setup time through efficient work holding and tool change strategies. Implementing lean manufacturing techniques such as 5S, value stream mapping, and continuous improvement initiatives further contribute to cost optimization.
Automation and Robotics
Integrating automation and robotics in CNC machining processes can significantly enhance efficiency, reduce labor costs, and improve productivity. Automated systems can handle repetitive tasks, allowing skilled operators to focus on more complex operations. Robotics can also facilitate precise and consistent machining, resulting in higher-quality parts and reduced scrap. By embracing automation and robotics, manufacturers can save costs through increased throughput, reduced labor expenses, and improved process control.
Summary
This article presented CNC machining costs, explained it, and discussed factors that influence cost and how to reduce them. To learn more about CNC machining services, contact a Xometry representative.
Xometry provides a wide range of manufacturing capabilities, including casting and other value-added services for all of your prototyping and production needs. Visit our website to learn more or to request a free, no-obligation quote.
Disclaimer
The content appearing on this webpage is for informational purposes only. Xometry makes no representation or warranty of any kind, be it expressed or implied, as to the accuracy, completeness, or validity of the information. Any performance parameters, geometric tolerances, specific design features, quality and types of materials, or processes should not be inferred to represent what will be delivered by third-party suppliers or manufacturers through Xometry’s network. Buyers seeking quotes for parts are responsible for defining the specific requirements for those parts. Please refer to our terms and conditions for more information.
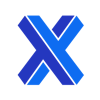