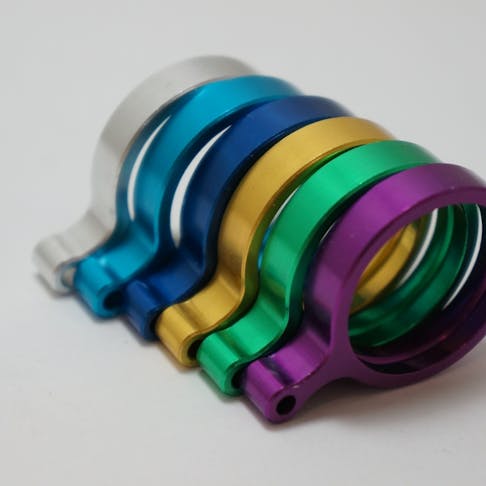
Hard Anodizing Colors: What You Need To Know
Learn more about hard anodizing colors and how it works.
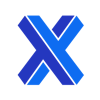
The anodization of colors into metals, including aluminum components, has proven reliable in not just maintaining but improving the overall quality of the materials. Hard anodization helps in the functional refinement of aluminum alloys and other metals. The anodic layer or aluminum oxide coating formed during the process provides a protective encasement of the metal.
There are different ways to color anodize: Type 1 anodizing, Type 2 anodizing, and Type 3 anodizing which is also called hard anodization. Anodization of colors into metals is not complete until it goes through some steps including: cleaning, acid desmutting, anodizing, coloring, and anodizing sealing. All in all, the hard anodization of colors into metals is a process that makes metal products durable, scratch-resistant, and corrosion-resistant. This article will define hard coat anodizing, the ways to color anodize metals, its benefits, and the process.
What Is Hard Coat Anodizing?
Hard coat anodizing, also called Type 3 anodizing, is an electrochemical process. It deposits a layer of a controlled oxide film or non-conductive anodic oxide on non-ferrous metal surfaces such as aluminum. One of the most commonly used acids for hard anodizing is sulfuric acid—for best results, certain conditions must be maintained during the process of electrolysis. The bath temperature should fall between 28–32°F and the applied DC voltage should start at a low value (25 V) and gradually increase to a relatively high value (60–100 V). A very hard surface hardness, upwards of 60 Rockwell C, should be achieved if the process is properly executed.
For more information, see our guide on Anodizing.
What Are the Ways To Color Anodize Metals?
Manufacturers utilize one of three options to anodize color into metals, depending on the peculiarity of the application. These are listed below:
- Type 1 Anodization: In this method, the electrolyte used is chromic acid. During the electrochemical process, a fine, thin, and non-conductive anodized coating is formed around the metal or aluminum component. This helps enhance adhesion before painting. Needless to say, the fatigue strength and structural integrity of the base material is maintained.
- Type 2 Anodization: The electrolyte used in this process is sulfuric acid. A thicker oxide of aluminum or anodized layer builds up around the aluminum component after it is placed in the sulfuric bath. The result of the electrochemical process is a porous anodic finish which allows the absorption of more dye before finally being sealed to retain the color.
- Type 3 Anodization: The anodized coating formed is the thickest of the three methods. Hence, the name hard coat color anodization. A bath of sulfuric acid is also used during the process. Metals (including aluminum components) produced with this method, have the added advantage of being suitable for environments in which extreme wear is possible.
What Are the Types of Acid Used To Color Anodize?
Different types of acid are used to anodize color into metals, including aluminum components, depending on the application. These are listed below:
- Sulfuric Acid: This is the most common and highly effective method to color anodize metals. Sulfuric acid, also known as oil of vitriol, is fundamentally composed of two atoms of hydrogen, one atom of sulfur, and four atoms of oxygen. It is given by the chemical formula H2SO4. The anodizing finish or aluminum oxide formed not only coats the metal but also penetrates it. The thickness of this film falls between .0001"–.001" (100 to 1000 micro inches)
- Chromic Acid: The thickness of the coating or aluminum oxide produced by this acid is quite thin. In most cases, the value falls between .00002”–.0001” (20 to 100 microinches). This lack of thickness may seem like a disadvantage when compared to the more popular sulfuric acid. However, if properly sealed, the same level of corrosion resistance can be achieved with this acid. Chromic acid can be described by the chemical formula H2CrO4.
What Are the Benefits of Color Anodizing?
The benefits of color anodizing are listed below:
- Aesthetics: A variety of colors can be applied during color anodizing. This makes the process suitable for prospects who consider color as a factor before making a purchase. Aside from the fact that it is aesthetically pleasing, color anodizing does not affect the metallic appearance of the aluminum parts.
- Durability: Accrual of economic benefits is made possible as a result of the extremely long life span of the product. Maintenance and operating costs may be reduced by a considerable amount.
- Excellent corrosion resistance: Anodizing is useful in that it provides a perfectly formed oxide layer around the metal. This ensures that its metallic quality is preserved against the destructive process of corrosion.
What Is the Color Anodizing Process?
The color anodizing process is listed below:
- Clean the aluminum in a solution of lye, also called sodium hydroxide. Thoroughly remove any existing anodizing layer from the surface. It is important to note that the lye should not be used directly but must be diluted in distilled water. For the best result, mix 3 tablespoons of lye in half a gallon of distilled water.
- Start the electrochemical process by electrically connecting the acid or electrolyte, battery, and metal components. The electrolyte should be a 50/50 mix of water and sulfuric acid.
- Allow the process to continue for about 45 minutes before removing the anodized metal from the sulfuric acid bath. Ensure that this is done in a well-ventilated room.
- Place the anodized metal in a bath of hot dye for 15 minutes.
- Apply a chemical sealant to the surface. It should be ready for use afterward.
What Are the Anodizing Color Choices?
The range of colors that aluminum can be anodized include:
- Gold
- Bronze
- Blue
- Green
- Red
- Copper
- Black
- Silver
- Gray
- Bronze
When Are Hard Anodizing Colors Applied?
Hard anodizing colors should be applied when there is a possibility of wear and tear occurring, especially when the environment is harsh or caustic. It is beneficial when surfaces of components are used for slide applications. The typically smooth and glossy surface is easily moved across other surfaces. The frictional force is reduced to a considerable extent.
How To Anodize With Different Colors
The following lists the steps in anodizing with different colors:
- Cleaning: The metal of choice should not be used directly but should go through a cleaning process that rids it of foreign matters and light oils. This is the first step and should not be overlooked. Failure to do this may hinder the anodizing process. A proper alkaline solution such as lye should be used as the cleaning agent. This process is also called etching since it strikes out the natural oxides found on the surface of crude aluminum.
- Acid Desmutting: The drawback of etching is that it leaves behind a deposit of smut or dirt on the aluminum surface. This smut may appear gray or black and is a metal alloy remnant that is insoluble in sulfuric acid. To dissolve it, put the metal in a solution of nitric acid.
- Anodizing: This is when the electrochemical process begins. A suitable electrolyte such as sulfuric acid should be used. The aluminum component or alloy serves as the anode during the process. A battery that delivers a high DC voltage also comes in handy. The anodic film or metal oxide is dependent on the electrolyte concentration, anodizing temperature, and current density after the application of the high voltage.
- Coloring: At this stage, the metal is dipped in a bath of dye. A convenient color should be chosen. The dye is absorbed by the pores which were created during the process of anodization, after which the metal is boiled in distilled water to prevent further reactions.
- Anodizing sealing: Two well-known anodizing sealants are nickel fluoride cold sealing (NFCS) and nickel acetate hot sealing (NAHS). They help to improve the corrosion resistance of the aluminum alloy. This is the final step, and it helps avoid the removal of color forcibly.
Product designers should be aware of the factors that affect color matching and the consistency of color.
What Are the Applications for Color Anodizing?
Applications for color anodizing cover a vast range of manufacturing possibilities. However, a few applications have been listed below:
- Color anodizing is used to create decorative finishes on food preparation equipment.
- It makes artwork and jewelry visually appealing.
- Household metal parts such as door handles and metal window frames can be color anodized.
- Automotive or vehicle components.
What Are Some Tips When Color Anodizing?
To achieve better color consistency during the color anodizing process. Here are some tips to take note of:
- If the same shade of color is needed for particular components, it is important to assemble them side by side. In other words, they should be of the same batch. This will help create better color consistency during the process.
- Don't rely on images; get an approved sample. Images are not always accurate in determining the color of choice. Due to the lighting effect, the color of images of metal components stored on a laptop or other devices may vary slightly from the actual color.
- Another useful tip is to ensure the consolidation of the supply chain. Product parts should be sent to the same facility for anodization. This will ensure that better color consistency is achieved.
Is Hard Anodizing Colorable?
Yes, hard anodizing can be colorable. After the anodizing process is complete, the surface can be dyed to a range of colors using anodizing dyes. The color of the anodized surface is determined by the type and concentration of dye used, as well as the thickness of the anodized layer. Typically, the colorations on hard coat anodized parts will be darker than a Type 2 coating, so consider this when considering colorized hard coatings. Even undyed (class 1) hard coatings will darken the surface due to the higher thickness of the coating and usually vary from a light to darker gray or brown.
Summary
This article presented hard anodizing colors, explained what it is, and discussed how to use this process in manufacturing. To learn more about anodizing, contact a Xometry representative.
Xometry provides a wide range of manufacturing capabilities and other value-added services for all of your prototyping and production needs. Visit our website to learn more or to request a free, no-obligation quote.
Disclaimer
The content appearing on this webpage is for informational purposes only. Xometry makes no representation or warranty of any kind, be it expressed or implied, as to the accuracy, completeness, or validity of the information. Any performance parameters, geometric tolerances, specific design features, quality and types of materials, or processes should not be inferred to represent what will be delivered by third-party suppliers or manufacturers through Xometry’s network. Buyers seeking quotes for parts are responsible for defining the specific requirements for those parts. Please refer to our terms and conditions for more information.
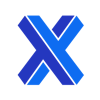