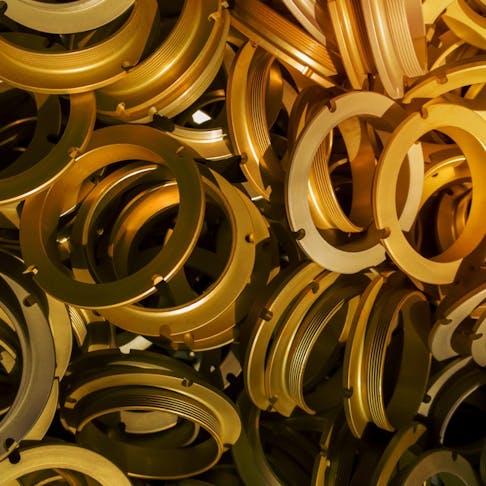
Everything You Need To Know About Sulfuric Acid Anodizing
Learn more about sulfuric acid anodizing and how it works.
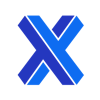
Anodizing refers to the process of converting the surface of a metal part, typically aluminum, into an abrasion and corrosion-resistant oxide layer. Sulfuric acid anodizing is a popular method of creating this oxide layer. Sulfuric acid anodizing is also referred to as Type II anodizing. This process is often used in decorative applications due to the ease with which it can be dyed, as indicated in Figure 1 below:
Aluminum machined parts in color.
Image Credit: Shutterstock.com/Rito Succeed
This article will describe what sulfuric acid anodizing is and how it works, as well as list some of the benefits and limitations of the process.
What Is Sulfuric Acid Anodizing?
Sulfuric acid anodizing refers to a process whereby an aluminum alloy part is exposed to an electric current inside a sulfuric acid electrolyte bath. This process produces an abrasion and corrosion-resistant coating of aluminum oxide (Al₂O₃) on the part’s surface. Sulfuric acid anodizing is often performed in accordance with US military specification MIL-A-8625 and is referred to as either a Type II or Type IIB coating. A standard Type II coating is typically dyed after anodizing and has a thickness of 0.00007 to 0.0010 inches (1.78 to 25.4 µm). Sulfuric acid anodizing that results in a thinner coating (0.00002 to 0.0007 inches (0.51 to 17.78 um)) is referred to as Type IIB anodizing. Because it results in a coating thickness comparable to that of chromic acid (Type I) anodizing, the Type IIB process is often used as a non-chromate alternative to Type I anodized coatings.
Sulfuric acid anodizing can be performed on titanium as well as on aluminum. As is the case for aluminum parts, anodization enhances the naturally occurring oxide layer on titanium and enables the surface to be dyed.
For more information, see our guide on Anodizing.
What Is the Purpose of Sulfuric Acid Anodizing?
The purpose of sulfuric acid anodizing is to increase the corrosion and abrasion resistance of aluminum and its alloys. Any applications in the aerospace, marine, consumer goods, and automotive industries require corrosion protection. In addition to improving corrosion resistance, the oxide layer is non-conductive, electrically insulating the underlying aluminum.
Another purpose of sulfuric acid anodizing is to allow for the coloring of aluminum components by dying the porous anodized coating. This method of coloring aluminum is extremely durable and has excellent color fastness. Anodizing aluminum is also used to create a porous surface that assists with paint adhesion.
Where Is Sulfuric Acid Anodizing Used?
Sulfuric acid anodizing is used in a wide range of industries where aluminum components are likely to be exposed to corrosive or abrasive conditions. In addition to this, anodizing is used to enhance the aesthetic appearance of aluminum parts. The most notable industries making use of anodized aluminum parts include: the medical, consumer products, automotive, and architectural industries. Example parts include aluminum profiles for buildings, surgical tools, and finishing on household appliances.
How Does Sulfuric Acid Anodizing Work?
Sulfuric acid anodizing is a method of creating an oxide coating on aluminum that has more stable and reliable properties than the naturally occurring oxide layer.
Sulfuric acid anodizing begins with the cleaning of the substrate by rinsing it in a strong degreaser. After rinsing, the part moves on to an acid etch station which removes any existing oxide on the substrate's surface. The acid etch also helps create a uniform base for the formation of the oxide layer. The part is then rinsed in a neutralizing bath to remove any traces of etching acid, which could negatively affect the anodizing process.
After the cleaning steps, the parts are placed in an electrolytic solution of sulfuric acid. The part is connected to the positive terminal, making it the anode. A cathode made from an unreactive material is situated in the bath and is hooked to the negative terminal. The application of direct current causes the aluminum to release electrons from the aluminum, creating positively charged aluminum ions on the surface of the part. At the same time, negatively charged oxygen ions produced at the cathode bond to the aluminum ions to create aluminum oxide (Al₂O₃). The characteristics of the oxide layer are controlled by the conditions in the electrolyte bath such as the temperature, surface current density, time, and sulfuric acid concentration.
After the desired oxide layer thickness has been achieved, the part is removed from the bath and rinsed. Afterward, the anodized part may or may not be dyed, pursuant to the part specification. Either way, a final step to seal the coating is required. If a Class 1 coating is required, the part is not dyed; whereas, a Class 2 coating is dyed. Both anodizing classes require a final sealing step.
What Are the Benefits of Sulfuric Acid Anodizing?
Sulfuric acid anodizing is one of the most popular anodizing techniques due to its numerous advantages, some of which are listed below:
- Increased Corrosion Resistance: Anodized aluminum has excellent corrosion resistance in many adverse environments. This corrosion resistance is maximized when the porous coating is sealed after anodizing.
- Aesthetic Finish: Anodizing is one of the most common aesthetic finishes for aluminum parts, as it has an appealing appearance, especially when dyed. Anodized aluminum is easily dyed due to its porous nature.
What Are the Limitations of Sulfuric Acid Anodizing?
Despite its benefits, sulfuric acid anodizing can have some limitations, as listed below:
- Reduced Fatigue Limit: Anodizing reduces the fatigue limit of the base material. This can result in premature failure if the part is not specifically designed for the known and expected decrease in fatigue strength. Alternatively, Type I chromic acid anodizing can be used.
- Hazardous Process: Sulfuric acid anodizing is a hazardous process that requires specialized equipment and training.
What Is the Material Needed to Perform Sulfuric Acid Anodizing?
Sulfuric acid anodizing is an electrochemical process. The key materials required to carry it out are listed below:
- Anodizing Bath: The anodizing process takes place in an acid-resistant tank that holds the sulfuric acid electrolyte.
- Cathode: The cathode is made from an unreactive material, typically in the form of a lead or graphite sheet.
- Agitation: In some cases, air nozzles are placed in the bottom of the tank to create a turbulent environment that can improve anodizing quality.
- Conductive Wire: Conductive wire is used to attach the part to the anode, completing the electric circuit once the part is submerged in the electrolyte.
- Supporting Baths: In addition to the anodizing bath, degreasing, etching, rinsing, and dying baths are also required.
- Power Supply: Anodizing requires DC power, as such a rectifier is needed to convert mains AC voltage into DC voltage.
How Long Will Sulfuric Acid Anodizing Last?
The longevity of a sulfuric acid anodized coating depends on the thickness of the oxide layer, whether or not it was sealed, and the environment to which it is exposed. However, an anodized part coating can last between 10 and 20 years.
How Long Does It Take To Perform Sulfuric Acid Anodizing?
The time required to perform sulfuric acid anodizing depends on numerous factors such as: the electrolyte concentration, bath temperature, voltage, and desired thickness. Typically the process can take anywhere from 10 to 60 minutes. However, this excludes any pretreatment and post-treatment steps.
Are Sulfuric Acid Anodized Materials Prone to Rust?
No, sulfuric acid anodized materials are not prone to rust. The oxide layer on aluminum forms due to an oxidation process, but this oxide layer is not destructive and improves the corrosion resistance of the base metal.
Is Sulfuric Acid Anodizing Permanent?
No, sulfuric acid anodizing is not permanent. While sulfuric acid anodizing produces a durable, long-lasting oxide layer on the surface of the part, the oxide is not completely impervious to all forms of attack. Mechanical damage can expose the base metal to corrosive conditions and some strong acids can dissolve the anodic layer at the expense of some of the base metal.
Are Sulfuric Acid Anodized Materials Conductive?
No, sulfuric acid anodized materials are not conductive. While aluminum is conductive, the oxide layer formed during anodizing is not.
Summary
This article presented sulfuric acid anodizing, explained what it is, and discussed its use in manufacturing. To learn more about sulfuric acid anodizing, contact a Xometry representative.
Xometry provides a wide range of manufacturing capabilities and other value-added services for all of your prototyping and production needs. Visit our website to learn more or to request a free, no-obligation quote.
Disclaimer
The content appearing on this webpage is for informational purposes only. Xometry makes no representation or warranty of any kind, be it expressed or implied, as to the accuracy, completeness, or validity of the information. Any performance parameters, geometric tolerances, specific design features, quality and types of materials, or processes should not be inferred to represent what will be delivered by third-party suppliers or manufacturers through Xometry’s network. Buyers seeking quotes for parts are responsible for defining the specific requirements for those parts. Please refer to our terms and conditions for more information.
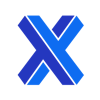