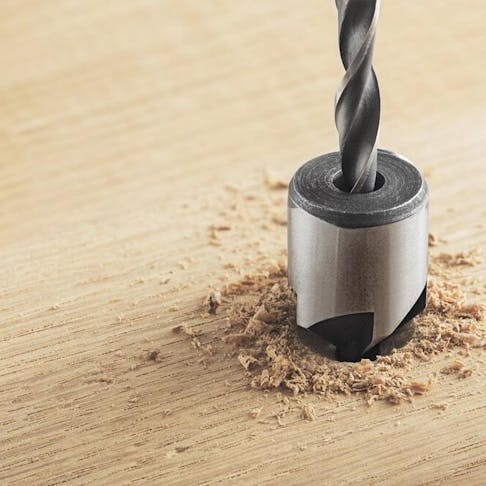
Countersink vs. Counterbore Holes in Machining: Differences and Uses
Learn more about each of these holes and how they are used in machining.
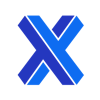
Countersink and counterbore holes are both commonly used in machining. Aside from the shape where counterbores are cylindrical, while countersinks are cone-shaped there are several key differences between them. The type of hole that is used will depend on the specific application.
Typically, countersink holes are used to make conical holes that match the screw's angle. This enables the screw to sit flush against the surface of the part and be fully engaged. Countersinks can be used for a variety of applications and come in different angles, including 60°, 82°, and 90°. Counterbore holes are utilized to increase a hole's opening and produce a flat bottom. As a result, socket-head screws can sit flush against the surface of the part. Counterbores typically serve a single purpose. To guarantee a secure assembly, lock washers may be used. A counterbore is a hole with walls that are 90° from the metal surface. The countersink angles can then be determined about that.
This article will further discuss the differences between countersink and counterbore holes, as well as their specific uses.
What is a Countersink Hole?
A countersunk hole is a conical or cone-shaped hole that is drilled into a material. The cone-shaped part of the hole is wider than the rest of the hole. It is used to allow a screw or bolt to be inserted into it. The angle of the countersink hole is typically around 90° but can be anywhere from 60° to 120°. The angle of the hole is important because it determines how deep the screw or bolt will be sunk into the material. The deeper the screw or bolt is sunk, the more secure it will be.
Countersink holes are typically used in woodworking or when working with softer materials. They can be used to make a joint stronger or allow the faster to make better contact with the material. A countersunk hole is useful because it allows the screw or bolt to be inserted at a shallower angle, which makes it less likely to strip the material. There are purpose-built tools that can be used to create countersink holes, but a drill can also be used in conjunction with a Phillips head bit to create a countersink hole. The important thing is to create a hole that is the right size and shape for the screw or bolt that will be inserted into it.
What is a Counterbore Hole?
A counterbore hole is a type of machined hole that is created to seat a screw or bolt flush with, or below, the surface of a workpiece. A counterbore hole is typically shallower than a countersink hole and has straight sides rather than tapered sides. If a counterbore is inspected, one will notice that it has a flat head. Both the top of the head and the bottom of the head are flat.
There are several advantages to using a counterbore hole, including more holding strength. A counterbore usually has more holding strength compared to a countersink hole because the force applied by the socket cap screw head is parallel to the axis. The force applied by the screw or bolt is distributed evenly over a larger surface area. This is not the case with a countersunk hole, which has tapered sides. As a result, the force applied by the screw or bolt is not evenly distributed, but dispersed at an angle or along the slope of the hole.
A counterbore can also be made large enough so that a washer can be placed over the hole, providing even more holding power. A counterbore usually has more holding strength compared to a countersink hole because the force applied by the socket cap screw head is parallel to the axis. Counterbore holes are made by first drilling a pilot hole with a small diameter drill bit. The next step is to enlarge the hole with a counterbore cutter, which is a type of end mill. This tool has a cutting end with the required diameter that creates a flat-bottomed hole.
Countersink vs. Counterbore: Size
Countersinks are typically used for wood screws and metal screws, while counterbores are typically used for larger fasteners such as lag bolts. Both countersink and counterbore tools have a pilot drill bit that determines the size of their respective countersink hole. The size of the pilot is one of the factors that determine which tool should be used for a given application. Countersinks require smaller pilots than counterbores, so they can be used for smaller screws. Counterbore tools are designed to produce flat-bottomed holes that provide more room for metal screws and lock washers to be tightened securely.
Countersink and counterbore sizes are typically expressed in terms of their diameter and depth and angle of countersink. The diameter is the width of the countersink or counterbore, while the depth is the distance from the surface of the material being drilled down to the top of the pilot hole. Counterbore sizes typically range from 3/16" to 1", while countersink sizes can be as small as 1/16" or as large as 1/2". It is recommended to check the standard counterbore and countersink size chart for accuracy of measurement.
Countersink vs. Counterbore: Shape
A countersink is a cone-shaped hole. A counterbore, on the other hand, is a cylindrical flat-bottomed hole that is created to contain a socket or hexhead cap screw. In other words, a countersink hole is cone-shaped while a counterbore hole is cylindrical.
Countersink vs. Counterbore: Drilling Angle
Depending on the application, drill bits that come in different sizes and drilling angles are available for producing countersinks. Some of the applied angles include 120° angles, 110° angles, 100° angles, 90° angles, 82° angles, and 60° angles. However, the most commonly applied drilling angles are 82° angles and 90° angles. For the best result, the angle of the countersink must be matched with the tapered angle on the underside of the fastener head. On the other hand, a counterbore hole has the sides parallel to each other and therefore does not require any tapering.
Countersink vs. Counterbore: Callout Symbol
The callout symbol for a countersink hole is "⌵" while the callout symbol for a counterbore hole is "⌴". The symbols attempt to depict the cross-sectional shapes of the different hole types after the countersink or counterbore has been created.
Countersink vs. Counterbore: Applications
The choice of a countersink or counterbore depends on the design requirements. Either countersink or counterbore can be used in each of the given applications: woodworking, printed circuit boards (PCB), sheet metal, and plastic. However, counterbore tools are designed to produce flat-bottomed holes that provide more room for metal screws and lock washers to be tightened securely. As a result, counterbores are usually used for heavy-duty applications which include machinery, construction, and automotive applications.
Other Types of Holes in Machining
Other types of holes used in machining besides countersink and counterbore include:
- Blind Hole: A blind hole can be created through a machining operation such as drilling, reaming, or milling. However, the hole reaches a specified depth and does not break or pass through the other side of the workpiece. Moreso, a blind hole is also a counterbore hole since it has a cylindrical shape and allows a flat-head screw to sit flush against it.
- Simple Hole: A simple hole in a machining operation refers to a hole of a single diameter that passes through the entire thickness of a material. These holes can be used for a variety of purposes, such as fastening the components together.
- Counterdrill Hole: A counterdrilled hole is one that has a countersink recessed below the surface.
- Tapped Hole: A tapped hole is created through a tapping process that cuts threads into the walls of the hole. This comes in handy in applications where bolts and nuts cannot be utilized.
- Spotface: A spotface is essentially a shallow counterbore hole. The machined feature gives a smooth and high surface finish at the top or surface of the hole.
Summary
This article presented countersink and counterbore holes, explained what they are, and discussed when each is used in machining. To learn more about holes in machining, contact a Xometry representative.
Xometry provides a wide range of manufacturing capabilities, including CNC machining and other value-added services for all of your prototyping and production needs. Visit our website to learn more or to request a free, no-obligation quote.
Disclaimer
The content appearing on this webpage is for informational purposes only. Xometry makes no representation or warranty of any kind, be it expressed or implied, as to the accuracy, completeness, or validity of the information. Any performance parameters, geometric tolerances, specific design features, quality and types of materials, or processes should not be inferred to represent what will be delivered by third-party suppliers or manufacturers through Xometry’s network. Buyers seeking quotes for parts are responsible for defining the specific requirements for those parts. Please refer to our terms and conditions for more information.
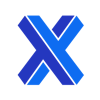