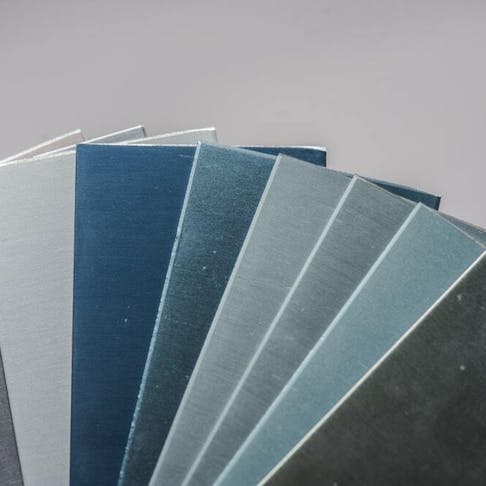
Anodizing: Definition, Importance, and Different Types
Learn more about this finishing process and the different types that are used in manufacturing.
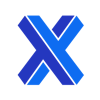
Anodizing is an electrochemical process used to enhance a material’s wear resistance. It also enhances corrosion resistance, leading to an improved cosmetic appearance by altering the surface finish of nonferrous metals like copper, titanium, manganese, magnesium, zinc, and stainless steel. The anodizing process consists of applying a thin oxide film to the metal surface through an electrochemical process. The metal acts as the anode in an acid bath solution and an electrical current is then sent through the bath to cause the formation of tightly adherent metal oxide on the anode surface.
There are three key types of anodizing: Type I (chromic acid), Type II (sulfuric acid), and Type 3 (hard coat). These methods differ in the type of acid that is used and the film thickness that is produced.
In this article, we will discuss the types of anodizing, give a step-by-step walkthrough of the anodizing process, and take a look at the advantages and disadvantages of anodizing.
What is Anodizing?
Anodizing is an electrochemical process by which a metallic surface is converted into a corrosion-resistant, durable, and aesthetically pleasing finish. The anodizing process helps to protect metal against wear and corrosion while also improving its appearance.
When Was Anodizing First Used?
Anodizing was first used on a large scale to protect seaplanes, made from an early aluminum alloy called Duralumin, from saltwater corrosion. Two British men, Bengough and Stuart, filed a patent application for the method in 1923, and the industrial-scale anodizing was implemented in the same year. In 1927, a new sulfuric acid-based process was patented, and it remains the most common method of anodizing used today.
How Does Anodizing Work?
Anodizing is the process of creating a carefully controlled, tightly adherent layer of oxide on an aluminum or other nonferrous metal surface. The process works by using an electric current to force an oxide layer to build up on the workpiece. The workpiece functions as an anode, attracting negatively charged oxygen ions. These oxygen anions come from the acidic electrolyte. The driving force to create the negatively charged ions comes from electrons emitted at the cathode, which is usually made of T-6063 aluminum alloy, though it can be made of other inert, conductive materials. Positively charged hydrogen ions created from the electrolyte at the same time as the negatively charged oxygen ions are reduced (take on electrons) at the cathode. The circuit is completed by a power source and wiring to the anode and cathode outside the anodizing tank.
What is the Importance of Anodizing?
Anodizing provides many key benefits to metals. The most important benefits are increased wear resistance, increased corrosion protection, and aesthetic improvements. Anodizing creates a thin layer of oxide on the surface of a metal, which is much more resistant to wear and tear, as well as protecting against corrosion. The surface created by the anodizing process also makes metals more suitable for dyeing and painting, allowing metal surfaces to be transformed into a variety of colors. Unlike other metallic finishes, anodizing allows the metal to retain its metallic appearance.
What Types of Materials Can be Anodized?
The most common anodized materials are aluminum and aluminum alloys, but the anodizing process can be applied to other metals as well, such as copper, titanium, manganese, magnesium, zinc, and stainless steel.
Which Material is Anodized the Most?
Aluminum is the most commonly anodized material. Aluminum anodizing is a popular preventive measure that protects the metal's surface from corrosion and wear. Anodized aluminum develops a surface that is three times tougher than that of regular aluminum, and that will not flake, chip, or peel, even after being colored. The product won't ever rust, tarnish, or weather because of the controlled aluminum oxidation layer produced by anodizing.
What Are the Anodizing Colors?
Anodized surfaces can be dyed to produce any shade. However, not all dyes are equal, and there are a few colors that are used more commonly than others. Red, blue, green, black, yellow, purple, and orange are some of the most commonly used anodizing colors. Their popularity is mostly due to their low cost and ease of manufacture.
How to Anodize Aluminum
Aluminum can be anodized using the following steps:
1. Pre-treatment: Clean the aluminum component or sheet before placing it in the acid bath. The desired look can be achieved by applying either bright or satin finishes. Light etching is used to provide a satin finish — an even, matte surface finish. A bright finish, on the other hand, is achieved using bright dip anodizing where a phosphoric and nitric acid solution is used.
Aluminum extrusions with bright or satin finishes offer a spotless, smooth surface for anodizing. Aluminum cleaning can also be done by submerging the aluminum in a grease-removal solution before being washed in hot water to prepare it for use as the anode.
2. Anodizing: Depending on the anodizing method used, the aluminum is placed in either a chromic acid or sulfuric acid bath. The material must be immersed in an acid electrolyte bath while an electric current flows through it for the anodic oxide layer to form. Once the process is complete, the item can be taken out of the bath, cleaned, and dried.
3. Coloring: After anodizing, parts can be dyed to any desired color.A variety of methods exist for coloring anodized aluminum. Electrolytic coloring involves soaking anodized aluminum in a solution of inorganic metal salts. This bath receives an electric current as the metal salts oxidize in the pores of the aluminum oxide layer. The final, dyed color of the metal depends on the chemical makeup of the bath and the amount of time spent submerged. Gold, black, transparent, brown, bronze, and nickel are common anodized color finishes. Some businesses that employ cutting-edge technology also provide color matching and personalized color anodizing.
4. Sealing: The metal is sealed in the process of anodizing to stop corrosion and water leakage. There are three methods for sealing anodized aluminum extrusions: cold sealing, hot sealing, or a mixture of both. Sealing the metal stops the surface from getting scratched or stained.
What Are the Types of Anodizing?
The most common types of anodizing include Type I-chromic acid anodizing, Type II-sulfuric acid anodizing, and Type III-hard anodizing. Other anodizing methods that are less common include phosphoric acid and titanium anodizing. The most common anodizing processes are listed and described below:
1. Type I — Chromic Acid Anodize
Of the three main types of anodizing, chromic acid anodizing (Type I) produces the thinnest oxide layer, at 0.00002 to 0.0001 inches. When properly sealed, the oxide layer produced by chromic acid anodization provides aluminum with a similar level of corrosion resistance to the thicker layers produced by other anodizing methods, such as sulfuric acid or hard coat.
Due to the coating layer being thinner, Type I oxide coatings absorb less color when dyed, and the coating has a grayish cast. This grayish cast restricts the use of chromic acid anodizing as a decorative finish. Nevertheless, it is possible to dye a Type I coating black and apply it as a protection for housings for optical components.
Some of the key features of chromic acid anodizing include: good bonding with adhesives to other objects and electrically non-conductive properties. Chromic acid anodizing is frequently used for aerospace components, welded components, or as a substrate for additional painting.
2. Type II — Sulfuric Acid Anodize
Type II (sulfuric acid) is the most popular anodizing method. Films produced by the sulfuric acid anodizing technique have a thickness between .0002 and .001 inches. The oxide build-up changes the part's surface, making it well-suited for situations where abrasion resistance and hardness are necessary.
The colorful surface finish on aluminum and related alloys is obtained by making use of the porosity of the sulfuric acid coatings before sealing. The porous aluminum oxide readily absorbs dyes. Sealing the anodic oxide film after the dye has been applied helps avoid color fading while the part is in use. Despite being generally colorfast, colored anodized films tend to fade in continuous exposure to UV light. Some color options available with this anodizing technique include black, gray, brown, red, blue, green, and gold.
Compared to other methods of anodizing, sulfuric acid anodizing uses less expensive chemicals, less energy, and less time to reach the desired thickness. It is also possible to finish more types of alloys. Other advantages of this method are that it produces a more durable coating than chromic acid anodizing, and results in a clear and natural finish, which allows other colors to be added when dying. Treating Type II anodizing process waste is also less expensive and simpler than treating chromic acid anodizing waste. Common applications for Type II anodizing include optical and electronic parts, bodies for hydraulic valves, and enclosures for electronics and computers.
3. Type III — Hard Anodize or Hard Coat
Hard coat anodizing is typically applied using an electrolyte based on sulfuric acid. It produces a substantially denser and thicker oxide layer than sulfuric acid anodizing. The coating thickness of hard anodizing is typically between 0.0005 to 0.002 inches. The hard anodizing process is recommended for applications requiring superior abrasion resistance in corrosive environments. It can also be useful in cases where better electrical insulation is needed.
Because Type III anodized coatings can be made quite thick, they are useful for refurbishing wear coatings or for remanufacturing out-of-spec components. Some key characteristics of hard anodized coatings include increased wear resistance compared to other types of anodized coating, electrically non-conductive surface, fixing aluminum's worn surfaces by creating a uniform layer across the surface, and enhanced lubrication for sliding applications. Hard coat anodizing can be used for valves and pistons, sliding parts, gears, joint swivels, electrical insulation, blast shields, and more.
What Are the Benefits of Anodizing?
Table 1 lists the benefits of anodizing:
Benefits | Description |
---|---|
Benefits Corrosion protection | Description The thin layer formed by anodizing helps protect metals against corrosion. |
Benefits Durability | Description Anodizing causes the surface of metals to be more resistant to wear. |
Benefits Improved Appearance | Description Anodizing transforms the surface of a metal and leaves it more suitable for dyeing or painting. |
Limitations | Description |
---|---|
Limitations Color selection | Description Color options are severely constrained due to the chemicals utilized in the anodizing process. |
Limitations Touch-ups are visible | Description Colored anodized coatings are susceptible to scratching. The scratches cannot be easily touched up. |
Is Anodizing a Chemical Process?
Yes, anodizing is an electrochemical process where a part (an anodically connected metal) is immersed in an acid electrolyte solution and an electric current is passed through the medium.
Summary
This article presented anodizing, explained what it is, and discussed the uses of this finishing service in manufacturing. To learn more about anodizing, contact a Xometry representative.
Xometry provides a wide range of manufacturing capabilities and other value-added services for all of your prototyping and production needs. Visit our website to learn more or to request a free, no-obligation quote.
Disclaimer
The content appearing on this webpage is for informational purposes only. Xometry makes no representation or warranty of any kind, be it expressed or implied, as to the accuracy, completeness, or validity of the information. Any performance parameters, geometric tolerances, specific design features, quality and types of materials, or processes should not be inferred to represent what will be delivered by third-party suppliers or manufacturers through Xometry’s network. Buyers seeking quotes for parts are responsible for defining the specific requirements for those parts. Please refer to our terms and conditions for more information.
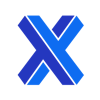