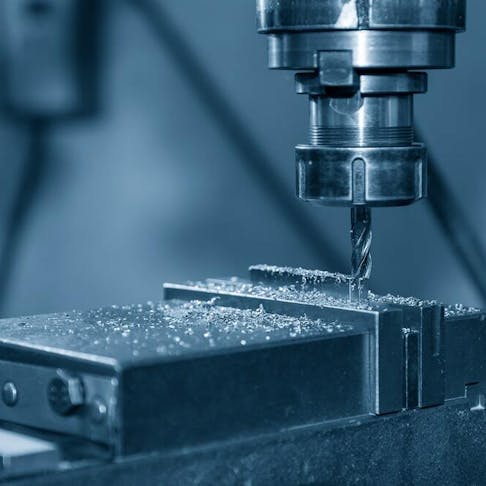
All About NC Machining: Process, Materials, Applications, and Cost
Learn more about this process and how it's used in manufacturing.
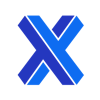
NC (numerical control) machining, not to be confused with CNC (computer numerical control) machining, is the act of machining a part based on a prescribed set of numbers, letters, and symbols in punched tape to drive the operation of the machine. From the 1940s to the 1960s, NC machining was the metalworking industry standard for modern machining, using punched paper tape to control machine program instructions. Starting in the 1960s, as computers began to become more widely available, CNC machining became the new standard.
While CNC machining is now more common than NC machining in the industry, NC machining is still often used in press working, spot welding, automatic drafting, and metal cutting. This article will review NC machining, from how the process works and the materials used, to its cost and the most common applications of NC machining.
What is NC Machining?
Numerical control (NC) machining is the automated machining of parts based on programmable codes in punched tapes. These codes contain a series of numbers, letters, and symbols that direct the machine’s cutting path. In contrast to CNC machining, which is controlled by a set of digital binary data programmed into computers using G-code and M-code, NC machining is powered by an analog system that converts punched tapes into electrical signals. NC was the first method used to automate machine tools based on programmable logic, and it paved the way for the more advanced computer numerical control systems that are more commonly used today. Figure 1 below is an example of an NC milling machine:
Machine operator using NC milling machine.
Image Credit: Shutterstock.com/Pixel B
How Does NC Machining Work?
Programmable codes on punched tapes control the tool path of an NC machining center. The punched tape is interpreted on an NC machine by a series of lights that shine through the punched holes, and sensors that interpret and convert the light into electrical signals. Electrical signals are then sent to and analyzed by the memory control unit (MCU). The MCU sends electrical signals to an output device, such as a stepper motor, to turn electrical signals into mechanical energy. This motor acts as the drive unit for the machine. The drive unit directs the machine tool path via the codes on the punched tape. A feedback control loop measures the actual XYZ travel distance of the spindle and compares it to the programmed distance. This closed-loop operation ensures that accurate cuts are made. This process repeats until the part is completed or until the workpiece must be adjusted.
What is the NC Machining Process?
The NC machining process does not differ much from the now more common CNC machining process. A workpiece material (metal, ceramic, plastic, wood, composite) is cut into a complete part with little to no need for manual control by an operator. However, modifying programmed NC machining codes can be difficult. It requires alterations to the existing program or the creation of a new program in punched tape — which can be a lengthy process. The machining process from the creation of a program to the finished part is described below:
- Programs that direct the machine’s tool path are created in punched tape.
- The tape is fed into the machine’s memory control unit MCU.
- The prepared workpiece is manually mounted into a jig or fixture in the machine.
- The program is executed.
- The machine cuts the workpiece in a methodical, sequential manner until the desired operations are completed is completed or until the workpiece must be adjusted manually by an operator for features to be cut on other faces of the workpiece.
What Are the Materials Used in NC Machining?
The materials used in NC machining are no different from those used in CNC machining. Limitations on the materials used in NC machining depend more on the tool/cutter being used rather than the way the cutting instructions are provided to the machine. A list of the possible materials that can be used in NC machining processes is shown below:
- Metals
- Ceramics
- Plastics
- Wood
- Composites
What Are the Applications of NC Machining?
There are several applications of NC machining, from press working to spot welding, in various industries. CNC machining produces a higher level of accuracy and precision compared to NC machining since a computer makes the cut instead of a human. Though not as accurate as CNC machining, NC machining is still capable of producing far more precise and accurate parts, with less labor, compared to conventional, manual machining. Some industries where NC machining is often used to make parts include: aerospace, automotive, agriculture, marine, and construction. Listed below are detailed descriptions of the suitable machining applications of NC machining:
1. Press Working
Press working, or cold stamping, is one of several uses of NC machines. With NC machining, sheet metal parts can be easily formed and produced automatically with little to no need for an operator.
2. Automatic Drafting
While not as common today due to the popularity of CAD software, NC machines can also be used to automate the drafting of both engineering drawings and illustrations on parts.
3. Metal Cutting
NC machining is used in metal cutting, engraving, and mass production of parts for a wide range of industries. NC machining processes can consist of many of the same processes used in CNC machining including: drilling, milling, turning, and finishing.
4. Spot Welding
Another common use of NC machines is spot welding. Spot welding is the joining of the components of parts in an assembly by welding them together at one or several separate points. NC machines can automate and control the movement of the welder, as well as the currents and voltages required to complete a weld.
What Are the Benefits of NC Machining?
While the use of computer-controlled machining centers has overtaken NC machining, there are still several benefits of NC machining. Automation and the reduction of manual labor compared to manual machining of parts is perhaps the biggest benefit of NC machining. Due to the automation NC machining allows, manufacturers can see several other benefits from NC machining including: reducing the amount of scrap and the number of non-conforming parts, increasing shop floor space as they don’t require too much area, and improving manufacturing efficiency.
What Are the Limitations of NC Machining?
Though NC machining has several benefits, it also has some limitations. Perhaps the biggest limitation of NC machining when compared to CNC machining is its lower cutting speed and accuracy. Computer programs in CNC machining are much more capable of achieving precise cuts at fast speeds due to the capabilities presented by binary code within the computer. This is because digital signals that are present in CNC machines are less prone to noise (fluctuations in the signal), use discrete numbers to represent data rather than continuous values, and thus can produce more accurate cuts and movements. Other limitations of NC machining include: the difficulty of modifying punched tape machining programs, the need to replace worn tapes, the inability of NC machines to store information, and the impossibility of altering machine parameters such as: spindle speed, spindle travel, and cut depth during operation when unexpected changes are required.
How Much Does NC Machining Cost?
NC machining centers cost considerably less than CNC ones. Though NC machines are seldom produced now, NC machines can still be purchased second-hand from private sellers. NC machines suitable for mass production can cost anywhere between $10,000 and $50,000, while CNC machines capable of mass production can cost between $50,000 for 3-axis milling machines and $500,000 for 5-axis machines.
What Are the Different Types of NC Machines?
There are several different types of NC machines. A few are listed and described below:
- NC Milling Machine - These machines conduct cutting operations uses a rotating multi-point cutter (a milling tool), automatically on a rectangular workpiece using a program created in punched tape.
- NC Lathes - NC lathes are used to conduct automatic turning and facing operations on cylindrical parts.
- NC Press Brake - NC press brakes are used for automatic sheet metal forming.
What Are the Types of NC Machining Services?
NC machining services include everything from milling and turning to sheet-metal forming. Additionally, routing, surface grinding, spot welding, automatic drafting, and inspection are all also possible with NC machining.
Summary
This article presented NC machining, explained what it is, and discussed how it works and the different materials used in this process. To learn more about NC machining, contact a Xometry representative.
Xometry provides a wide range of manufacturing capabilities, including CNC Machining and other value-added services for all of your prototyping and production needs. Visit our website to learn more or to request a free, no-obligation quote.
Disclaimer
The content appearing on this webpage is for informational purposes only. Xometry makes no representation or warranty of any kind, be it expressed or implied, as to the accuracy, completeness, or validity of the information. Any performance parameters, geometric tolerances, specific design features, quality and types of materials, or processes should not be inferred to represent what will be delivered by third-party suppliers or manufacturers through Xometry’s network. Buyers seeking quotes for parts are responsible for defining the specific requirements for those parts. Please refer to our terms and conditions for more information.
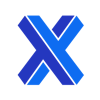