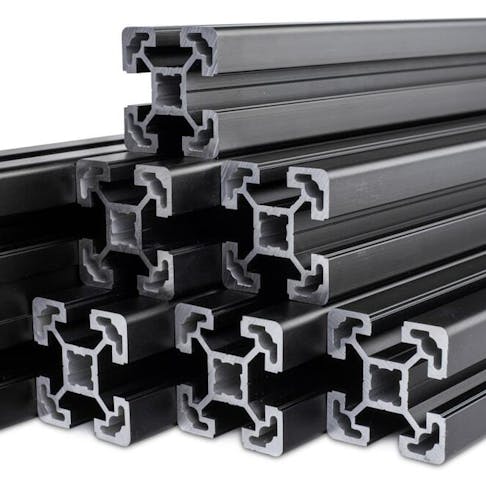
Everything You Need To Know About Black Anodizing
Learn more about how black anodizing is used in manufacturing today.
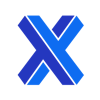
Black anodizing refers to the process of anodizing an aluminum part and then dying it black using a suitable dye. This must not be confused with black oxide coating which is unsuitable for aluminum parts.
Anodized aluminum has improved wear and corrosion properties, while black anodized parts have the additional benefits of being light absorbent as well as being able to effectively radiate heat. This article will describe what black anodizing is, how it works, as well as the various pros and cons. A black anodized flashlight is shown in Figure 1 below:
A black anodized flashlight.
Image Credit: Shutterstock.com/Formatoriginal
What is Black Anodizing?
Black anodizing refers to the process of blackening an aluminum part by first performing standard anodizing to create a semi-porous aluminum oxide layer. The oxide layer is then dyed black using one of three dyeing techniques: organic dyes, inorganic dye, or electrolytic dyeing using metal salts.
What is the Purpose of Black Anodizing?
Black anodizing is performed to achieve an aesthetic or functional black color on an aluminum part while also improving the corrosion and wear properties of the underlying aluminum component.
What Metal Can Be Anodized Black?
The metals that can be black anodized are aluminum, magnesium, and titanium. Aluminum, however, is the most common material used for black anodizing. It must be noted that not all grades of aluminum can be black anodized. Only aluminum series 5, 6, and 7 can be anodized.
Where is Black Anodizing Used?
Black anodized aluminum is used in applications where the black coating is beneficial. Examples are: satellite components that rely on the black anodic coating to more efficiently radiate heat back into space; optical equipment that relies on the ability of black coatings to absorb any stray reflective light; and architectural trimmings in which the deep black colors are both aesthetically pleasing while also having excellent color fastness, and the surface finish provides improved abrasion resistance. Black anodized aluminum has all the benefits of standard anodized aluminum with the additional benefits afforded by the black coloring.
How Does Black Anodizing Work?
Black anodizing works by first anodizing the part using the standard anodizing process with either a type II or type III anodizing process. A minimum anodized thickness of 25 microns or more is recommended for optimal color fastness. Once anodized, the part will have a semi-porous surface structure. These pores are utilized to hold the black dye. There are three types of dyeing techniques, as described below:
- Organic Pigments: These dyes are dissolved in warm water and then placed into the dye bath. The part is placed into the dye bath and the dye fills in the semi-porous surface of the anodic layer. Typically, black dyeing requires additional dyeing time compared to lighter colors. Organic-dyed parts are not recommended for outdoor usage.
- Inorganic Pigments: These pigments are not soluble in water. Inorganic pigments produce coatings with excellent light fastness. For black anodizing, parts can be produced with inorganic salts of cobalt sulfide.
- Electrolytic dyeing: After normal anodizing, parts are placed in another electrolysis bath with a solution containing heavy metal salts. The anodic layer acts as the cathode, and a stainless steel electrode is placed in the bath. The metal salts are then deposited into the bottom of the pores. Nickel, cobalt, and tin salts are used to produce different colors, a proprietary process that produces parts with exceptional color fastness.
After dyeing, the pores on the anodic layer must be sealed to prevent color leaching. Sealing is typically done via hydration of the coating, which closes the pores off by reaction with the anodic layer. Wherever there is a pore, AI2O3H2O is formed; this is less abrasion resistant than the normal aluminum oxide coating. Alternatively, chemical sealing can be put into effect, for example by using nickel acetate or dichromate sealing.
What Are the Benefits of Black Anodizing?
The benefits of black anodizing include increased corrosion and wear resistance that comes with standard anodizing. However, black anodizing has a few additional specific benefits described below:
- Heat Emissivity: Aluminum components are often dyed black to increase their emissivity; applications can include heat sinks as well as satellite components.
- No Outgassing: Black anodized parts, if properly sealed after dyeing, do not undergo outgassing when exposed to a vacuum. This lack of outgassing helps protect sensitive equipment, especially sensitive space-based equipment.
- Color Fastness: Black anodized parts, especially if dyed with inorganic or metal salts, have excellent color fastness, which means they will typically maintain their color when exposed to UV (ultraviolet) light.
What Are the Limitations of Black Anodizing?
Black anodizing has some limitations as described below:
- Surface Cracking: When exposed to thermal cycling, black anodized parts will form cracks in the anodic coating. These cracks are mainly due to the difference in thermal expansion rates of the substrate and the coating.
- Limited Materials: Not all aluminum series can be black anodized. In general, the most commonly anodized aluminum series are 5, 6, and 7, with series 6 being the most commonly anodized.
- Color Fading: If organic dyes are used, black anodized parts will lose their color as these dyes are unsuitable for exposure to UV light.
How to Black Anodize Material
Type II sulfuric acid anodizing is the most common method used when black anodizing parts. The process is listed below:
- Clean the part with a strong degreaser to remove any dirt, cutting fluid, or grease.
- Rinse the part in deionized water.
- Chemically etch the part to remove any naturally formed oxide layer.
- Rinse the part in deionized water.
- Anodize the part by passing an electrical current through the part in the presence of a sulfuric acid electrolyte. This process causes the anodic layer to form. The anodic layer is semi-porous.
- After anodizing, the part is rinsed and then placed into a dyeing bath where the pores are filled with either an organic or inorganic dye to color it black. Metal salts, however, are the preferred method for black anodizing as they produce parts with exceptional color fastness.
What Are the Materials Needed to Black Anodize?
The materials needed to black anodize aluminum are:
- Sulfuric acid electrolyte.
- Acid-resistant tank to hold the electrolyte.
- Cathode.
- DC power source to provide current.
- Conductive wire to hang the aluminum part.
- Degreaser for cleaning.
- Dyeing bath with a suitable dye to color the part black after anodizing.
How Long Will Black Anodizing Last?
An anodized coating can last between 10 and 20 years depending on the application, the thickness of the coating, and whether or not the relevant sealing steps were performed after anodizing. When metal salts are used for dyeing, the color will not fade. However organic dyes will fade over time.
How Long Does It Take to Black Anodize a Material?
The time required to black anodize a part depends on the desired anodic layer thickness, the dyeing method, and the post-dye sealing technique. In general, it takes five minutes to anodize 2.5 microns. So to anodize the minimum recommended black anodized thickness of 25 microns will take around an hour. The dyeing process can take up to 20 minutes. However, these time frames also depend on the cleaning and rinsing processes.
Are Black Anodized Materials Prone to Rust?
No, anodized aluminum is not prone to rust. Rust is typically used to describe the formation of a destructive flaking oxide layer on ferrous metals. When an oxide layer forms on aluminum, it adheres to the surface and prevents further oxidation of the base material.
Summary
This article presented black anodizing, explained what it is, and discussed the different factors to consider when choosing black anodizing. To learn more about black anodizing, contact a Xometry representative.
Xometry provides a wide range of manufacturing capabilities and other value-added services for all of your prototyping and production needs. Visit our website to learn more or to request a free, no-obligation quote.
Disclaimer
The content appearing on this webpage is for informational purposes only. Xometry makes no representation or warranty of any kind, be it expressed or implied, as to the accuracy, completeness, or validity of the information. Any performance parameters, geometric tolerances, specific design features, quality and types of materials, or processes should not be inferred to represent what will be delivered by third-party suppliers or manufacturers through Xometry’s network. Buyers seeking quotes for parts are responsible for defining the specific requirements for those parts. Please refer to our terms and conditions for more information.
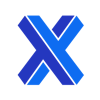