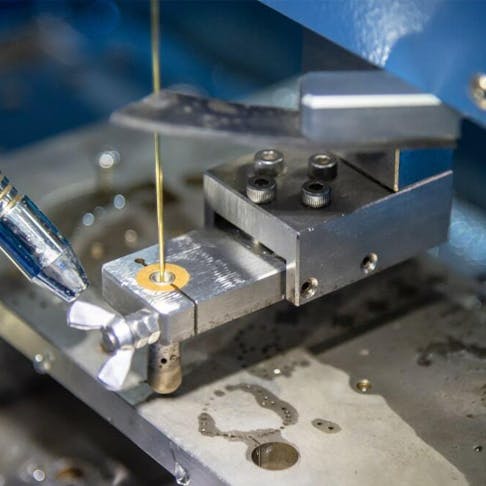
All About Hole Drill EDM Machining: Definition and Applications
Learn more about the common applications of this process and its advantages and disadvantages.
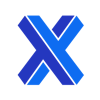
Hole drill EDM (electrical discharge machining) machining is a highly specialized technology developed to drill deep, small-diameter holes into conductive materials. It works by sinking a rotating hollow electrode into the material to be drilled. The diameter of the electrode is slightly smaller than the desired diameter of the finished hole. As the electrode gets close to the material and sufficient electric charge has built up to overcome the resistance of the dielectric fluid, a spark will jump from the electrode to the part. This spark generates extremely high localized temperatures that vaporize the material. A dielectric fluid is pumped through the electrode and prevents a short from occurring while also cooling the part and flushing out the eroded material.
This article will describe the hole drill EDM process, review its history, highlight its advantages and disadvantages, and list some common applications.
What is Hole Drill Electrical Discharge Machining?
Hole drill EDM machining is a type of electrical discharge machining (EDM) that is designed to drill small, deep holes with diameters as small as 0.065 mm, and depths up to 1m (or 250 times the hole diameter). The electrode and the workpiece are connected to a power source, usually with the electrode negatively charged and the workpiece positively charged. When enough charge builds up on the electrode, the dielectric fluid separating the electrode and the workpiece momentarily allows the charge to be conducted to the workpiece, creating a high-temperature spark that vaporizes and erodes the workpiece in a localized area. The electrode is hollow, allowing dielectric fluid to pass through it. This flow, combined with the rotation of the electrode, stabilizes the EDM process and aids in the removal of workpiece debris. This spark erodes the material while the electrode is rotated and moved down until the hole is complete. A hole drill EDM is often used to drill materials that are difficult to machine using conventional methods, such as hardened steels or tungsten carbide. For more information, see our guide on the Types of Machining Processes.
A typical hole drill EDM machine is pictured in Figure 1 below:
EDM machine making small holes in aircraft engine.
Image Credit: Shutterstock.com/Nordroden
How Does Hole Drill EDM Work?
EDM drilling works by using a small electrode to drill a hole in a workpiece. The electrode is typically made from tungsten, graphite, brass, or copper. The electrode is actually a hollow tube, designed to allow dielectric fluid to flow through it. The tubular electrode may have multiple passages in it to smooth and facilitate fluid flow. The electrode is guided to the workpiece. When it comes close enough, sparks are generated between the electrode and the workpiece. These sparks can create localized temperatures of between 8,000 and 12,000 °C. Sparks can be generated at a rate of 500 to 30,000 per second. However, only one spark strikes the work at a time. High-pressure dielectric fluid is typically pumped through the center of the hollow electrode to act as a resistor to prevent shorting until a high enough voltage is supplied. When a high enough voltage is supplied, the dielectric fluid ionizes, and a spark is created. The high-pressure fluid also increases the overall stiffness of the electrode and carries particles eroded from the workpiece out of the hole during drilling.
Who is the Pioneer of Electrical Discharge Machining?
In 1770, Joseph Priestley, an English physicist, was the first to document the effect of spark erosion. A husband and wife team of Soviet scientists named Dr. B. R. and Dr. N.I. Lazarenko took this research further in 1943 and invented the first electrical discharge machining process. The first practical EDM machine was designed to remove broken taps. This machine was developed by a company called Charmilles in 1952.
What is Hole Drill EDM Used For?
Hole drill EDM machining is mostly used for drilling small, precise holes in hard materials. It can be used to drill through holes or blind holes. Blind holes, however, are better suited to sinker EDM machines as hole drill EDM machines cannot always create a flat-bottomed hole. Some of the important applications for hole drill EDM are creating cooling channels in turbine blades, making starter holes for wire EDM cutting, and removing broken taps and drills from machinery being manufactured or reworked.
How Accurate is Hole Drill EDM?
A hole drill EDM machine is extremely accurate. It can hold tolerances as small as +0.0025 mm on hole diameter and +0.025 mm on hole straightness for a hole depth of 150 mm and diameter of 1 mm. This level of accuracy for small, deep holes is impossible to achieve with traditional drills because drill bits that are small in diameter will deflect, bend and break during drilling.
Who Manufactures Hole Drill EDM Machines?
A number of companies manufacture hole drill EDM machines. Some of the most well-regarded brands include Makino, Mitsubishi, TEK4, and Sodick.
What Are the Advantages of Hole Drill EDM?
Hole drill EDM machining has some advantages over other drilling methods, as listed below:
- Hole drill EDM can drill holes with diameters as small as 0.065 mm.
- Hole drill EDM can drill holes with a depth of up to 1 m. This measurement is impossible to achieve with any other manufacturing technology.
- Hole drill EDM can drill through very hard materials, including: stainless steel, tool steel, and tungsten carbide. Any material can be drilled provided it is conductive.
- A hole drill EDM electrode can drill holes through curved surfaces. Attempting to drill holes through curved surfaces with a mechanical drilling machine will result in the drill bit "walking" along the curved surface.
What Are the Disadvantages of Hole Drill EDM?
Hole drill EDM is an extremely capable process, but it has some disadvantages that must be taken into account. The most important downsides are listed below:
- Hole drill EDM is a slow process, although the speeds are continuously being improved. In general, drilling a single hole can take several minutes. For that reason, it is not suitable for high-volume production applications.
- Hole drill EDM is a relatively expensive process because of the time it takes to produce parts and the high energy consumption.
- Hole drill EDM is limited to drilling conductive materials. It cannot be used on plastics or composites.
What is the Best Hole Drill EDM Machine?
There are many different hole drill machines on the market. Choosing the correct one for your needs depends heavily on the application and the available budget. Some of the best hole drill EDM machines are listed below:
- TEK4 6g FHD GXL: This range of hole drill EDM machines has a number of useful features including a multi-access build table to allow for the drilling of angled holes. A built-in CMM (coordinate measuring machine) probe ensures repeatable accuracy and an ATC (automatic tool changer) allows for the automatic selection of different electrodes.
- Makino EDAF: The EDAF range of EDM machines is capable of drilling small diameter holes as well as performing sinker EDM processes. This feature makes it an excellent machine for the smaller job shop that requires maximum flexibility.
- Mitsubishi VH10: This machine can produce holes as small as 0.065 mm in diameter in hard materials like tungsten carbide.
Is Stainless Steel Suitable for Hole Drill EDM?
Stainless steel is a conductive material. As such, it can be processed using hole drill EDM.
Is Hole Drill EDM Machining Available at Xometry?
Yes, Xometry offers hole drill EDM machine services through our extensive network of certified partners.
Summary
This article presented hole drill EDM machining, explained what it is, and discussed its history and common applications. To learn more about hole drill EDM machining, contact a Xometry representative.
Xometry provides a wide range of manufacturing capabilities, including CNC machining and other value-added services for all of your prototyping and production needs. Visit our website to learn more or to request a free, no-obligation quote.
Disclaimer
The content appearing on this webpage is for informational purposes only. Xometry makes no representation or warranty of any kind, be it expressed or implied, as to the accuracy, completeness, or validity of the information. Any performance parameters, geometric tolerances, specific design features, quality and types of materials, or processes should not be inferred to represent what will be delivered by third-party suppliers or manufacturers through Xometry’s network. Buyers seeking quotes for parts are responsible for defining the specific requirements for those parts. Please refer to our terms and conditions for more information.
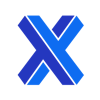