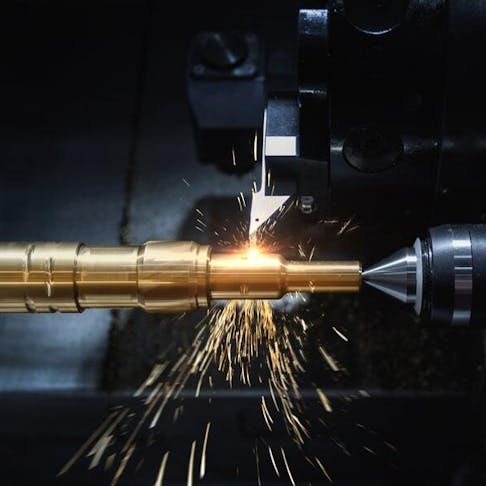
CNC Machining vs. Plastic Injection Molding: Differences and Comparison
Learn about the differences between the CNC machining and plastic injection molding manufacturing processes.
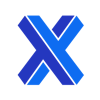
Picking an appropriate manufacturing method for a new product is often easier said than done. CNC machining and plastic injection molding are both commonly used and cost-effective ways to produce parts. While both methods are similar in those regards, they are completely different fabrication methods. CNC machining is a subtractive manufacturing process that uses metal cutters to remove material from a workpiece to create the final part shape. Plastic injection molding forces liquid plastic to conform to the shape of a mold to make the finished part. Three major differences exist between the two methods. These are materials that can be used, the volume of production that can be attained, and part dimensional tolerances and precision.
These differences lead to significantly different costs for the two processes. In this article, we discuss everything there is to know about CNC machining vs. plastic injection molding, including the advantages and disadvantages of each, and process alternatives to both.
CNC Machining Definition and Comparison to Plastic Injection Molding
CNC machining is a subtractive manufacturing process that uses machines like mills, lathes, drill presses, and saws, to make highly precise parts. Computer-Aided Design (CAD) data is developed during the product design phase. This CAD data is then used as the basis for programming and optimizing the machine tool sequences and paths. The material is then processed using cutters, such as end mills and drill bits to create the parts. Auxiliary machinery, including honing, hobbing, or grinding machines, may also be needed to complete parts to customer specifications.
While manual machining of parts has existed since 1300 BC, CNC machining wasn’t developed until the mid-1940s. The first control mechanisms that eventually were used on CNC machines were used to punch code tapes as a way of communication. In 1949, the first experimental 3-axis milling machine was created to make helicopter blades and stiffer skin for various aircraft. In the 1970s, CAD and CAM software began to be integrated into CNC systems. Now, CNC machining is one of the most widely used manufacturing methods in the world. It is used to make products for several industries, from automotive to agriculture. CNC machining is often preferred to injection molding due to the ability to easily accommodate product design changes, its ability to produce tight tolerance parts, and the possibility of using several different materials.
To learn more, see our guide on What is CNC Machining.
What Are the Advantages of CNC Machining Compared to Plastic Injection Molding?
Listed below are some advantages of CNC machining over injection molding:
- Beautiful surface finishes and tight tolerances are easily obtainable with CNC machining since small-diameter tools can be used and each process parameter can be optimized.
- A wide range of materials can be shaped using CNC machining since both plastic and metal materials can be cut.
- It is easy to modify part designs since programs containing the CNC machine instructions and fixtures can quickly be changed to match successive design iterations.
- CNC machining has faster tooling lead times than injection molding since complex molds don’t have to be made.
What Are the Disadvantages of CNC Machining Compared to Plastic Injection Molding?
Listed below are the disadvantages of CNC machining vs. injection molding:
- Large production volumes and price-per-part are more expensive for CNC-machined products due to the longer per-part cycle time needed to make parts.
- Labor-intensive since workpieces, completed parts, tools, and tool holders, must be fixed to and removed from the machine depending on the job.
Plastic Injection Molding Definition and Comparison to CNC Machining
Plastic injection molding is a manufacturing method that uses an injection molding machine (IMM). These machines contain components such as injection screws, injection barrels, and fabricated molds. Plastic pellets are fed into the barrel and are melted through the rotation of the screw and heater bands. The molten plastic is injected into the mold and formed into the geometry of the part. The IMM holds pressure on the mold until products have been properly formed and cooled. The completed parts are ejected and the cycle restarts.
Brothers Isaiah and John Hyatt developed injection molding in 1872 and used it to mold hair combs, buttons, and other small items. In the 150 years since that first machine, injection molding has blossomed into a multi-billion dollar global industry. Injection molding is considered a more cost-effective and efficient way to make plastic parts than CNC machining.
For more information, see our guide on what is plastic injection molding.
What Are the Advantages of Plastic Injection Molding Compared to CNC Machining?
Listed below are the advantages of injection molding vs. CNC machining:
- It can easily produce large volumes of parts in a rapid and repeatable fashion since multiple-cavity molds can create many parts in one injection cycle.
- Injection molding has the lowest price per part of any manufacturing process, since the molds have long lives, and multiple-cavity molds can increase the capacity of each machine to support high-volume orders.
- Minimal post-processing is required because parts are often ready to be shipped immediately after ejection depending on the type of gate (entry point from the runner into the cavity) that is used.
What Are the Disadvantages of Plastic Injection Molding Compared to CNC Machining?
Listed below are the disadvantages of injection molding vs. CNC machining:
- It is difficult to accommodate product design changes since rework on complex molds with several plates, cams, and complex geometries can be troublesome.
- Imperfections on the interior of the mold can result in finished parts with surface flaws.
- Enormous upfront investment is required for mold fabrication since multi-cavity molds can cost anywhere from a few thousand to hundreds of thousands of dollars.
Attribute | CNC Machining | Plastic Injection Molding |
---|---|---|
Attribute Typical tolerances | CNC Machining 0.001” | Plastic Injection Molding 0.005” |
Attribute Fast per part cycle times | CNC Machining No | Plastic Injection Molding Yes |
Attribute Fast Lead Times for Tooling | CNC Machining Yes | Plastic Injection Molding No |
Attribute Easily make design modifications | CNC Machining Yes | Plastic Injection Molding No |
Attribute Wide range of available materials | CNC Machining Yes | Plastic Injection Molding No |
Attribute High-volume production (>1000 pcs) | CNC Machining No | Plastic Injection Molding Yes |
Attribute Large upfront investment | CNC Machining No | Plastic Injection Molding Yes |
With CNC machining, tighter-tolerance parts can be made from a wider range of materials than with injection molding. However, injection molding can produce parts at a much more rapid pace without the need for post-processing - making it ideal for high-volume production. While injection molding is ideal for higher volumes, a large upfront investment must be made to fabricate an injection mold. However, injection molds will pay for themselves once a sufficient amount of parts are produced and sold.
CNC Machining vs. Injection Molding: Lead Cost Comparison
Tooling costs for CNC machining are significantly less than for injection molding. CNC machining costs are associated with the fabrication of fixtures and jigs and the procurement of raw materials and tools. Molds for injection molding can cost a few thousand dollars for single-cavity and low-cavitation molds and up to hundreds of thousand dollars for multiple-cavity molds. An injection mold will pay for itself when its cost is spread over a sufficiently high production volume. Assuming you have the necessary machinery to make parts and only need to make arrangements for tooling like molds, fixtures, and jigs, upfront costs on CNC machining are lower.
CNC Machining vs. Injection Molding: Speed Comparison
Both CNC machining and injection molding are notable for their ability to rapidly produce parts. For small-volume runs, CNC machining is often preferred. Injection molding is preferred for larger runs because multiple-cavity molds can rapidly produce parts and reduce per-piece cost. Taking into account the lead time for mold production, it takes longer to start series production using injection molding than using CNC machining. Consider using CNC machining for small production runs and injection molding for large runs.
CNC Machining vs. Injection Molding: Volume Comparison
Injection molding can both produce more parts per base machine and more parts per dollar invested compared to CNC machining. Molds used in injection molding can have multiple cavities - from one cavity to several hundred. Hence, injection molding can quickly produce large numbers of parts. In CNC machining, parts are generally made one by one. While CNC machining is fast at producing parts, injection molding is even faster.
CNC Machining vs. Injection Molding: Materials Comparison
A broader range of materials can be used in CNC machining processes than in injection molding. CNC machining is capable of producing parts from certain plastics, but also from metals, like aluminum and steel. Many thermoplastics, thermosets, and elastomers are too soft to be CNC machined. However, they can easily be fabricated into parts using injection molding machines.
What Are the Mutual Alternatives to CNC Machining and Plastic Injection Molding?
Mutual alternatives to CNC machining and plastic injection molding are:
- 3D Printing: With 3D printing, almost any geometry can be made - no matter how complex. 3D printing also gets around many of the part geometry limitations that can impact the manufacturability of products using CNC machining or injection molding. Many of the same materials used in CNC machining and injection molding can also be used in 3D printing.
- Casting: Casting won’t produce parts nearly as precisely as CNC machining or injection molding. As it relates to plastics, casting involves pouring molten material into a non-pressurized mold and allowing it to cure. It is a much simpler process than CNC machining or injection molding but can take much longer to produce parts. Casting is also not practical for large-scale production.
What Are the Similarities between CNC Machining and Plastic Injection Molding?
Perhaps the biggest similarity between CNC machining and plastic injection molding is that both can utilize many of the same materials, including polycarbonate (PC), High-density polyethylene plastics (HDPE), and ABS (acrylonitrile butadiene styrene). Aside from that, there are not many similarities between the two processes.
What Are the Other Comparisons for CNC Machining Besides Plastic Injection Molding?
Another alternative to CNC machining is CNC laser cutting:
- CNC Machining vs. CNC Laser Cutting: With CNC laser cutting, a computer-controlled laser moves about a programmed path to cut, engrave, etch, and mark parts. It is just as precise as CNC machining and can be used as a substitute for cutting processes, but can only be used on selected plastic materials due to harmful fumes that can be emitted from workpieces during laser cutting.
What are the other Comparisons for Plastic Injection Molding besides CNC Machining?
Another alternative to Plastic Injection Molding is:
- Injection Molding vs. Thermoforming: In thermoforming, heated and stretched sheets of plastic are pressed over a one-sided mold to create parts. While thermoforming can’t produce parts as fast as injection molding and is limited to non-complex parts, it is still an excellent alternative that can be used to make accurate plastic parts.
Summary
This article presented the comparison of CNC machining and plastic injection molding, explained what they are, and discussed each of their different attributes. To learn more about CNC machining and plastic injection molding, contact a Xometry representative.
Xometry provides a wide range of manufacturing capabilities, including CNC machining and other value-added services for all of your prototyping and production needs. Visit our website to learn more or to request a free, no-obligation quote.
Disclaimer
The content appearing on this webpage is for informational purposes only. Xometry makes no representation or warranty of any kind, be it expressed or implied, as to the accuracy, completeness, or validity of the information. Any performance parameters, geometric tolerances, specific design features, quality and types of materials, or processes should not be inferred to represent what will be delivered by third-party suppliers or manufacturers through Xometry’s network. Buyers seeking quotes for parts are responsible for defining the specific requirements for those parts. Please refer to our terms and conditions for more information.
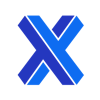