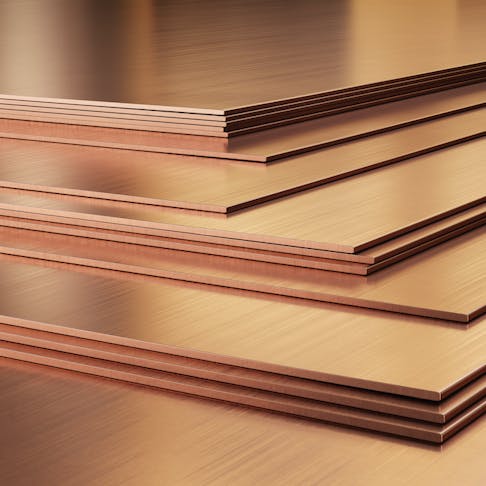
Common Corrosion Resistant Metal Materials
Corrosion-resistant metals see wide use in everything from the culinary industry to aerospace applications. Like most metals, they provide structural strength and heat resistance, but the ones on this list also resist corrosion better than others. This article will describe some of the more common corrosion-resistant metals and their various subsets.
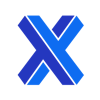
Common Corrosion-Resistant Metals
Corrosion-resistant metals see wide use in everything from the culinary industry to aerospace applications. Like most metals, they provide structural strength and heat resistance, but the ones on this list also resist corrosion better than others. This article will describe some of the more common corrosion-resistant metals and their various subsets.
1. Stainless Steel
Stainless steel is a blanket term that covers a wide range of corrosion-resistant metals. The degree of corrosion resistance depends on the elemental makeup of the alloy. The specific chemical resistance varies with the metal’s chemistry as well. The key mechanism of corrosion resistance in stainless steel is the formation of a chromium oxide passive layer on the surface that provides excellent corrosion resistance.
Stainless steel can be broken into 3 main categories based on its microstructure:
- Austenitic Stainless Steel: This range of alloys is often called 300-series stainless steel. Typical grades include 304 and 316 stainless steel with 316 being the most corrosion-resistant. The elemental makeup includes around 18% chromium and 8% nickel depending on the grade. In addition to this, small amounts of nitrogen and manganese are included. Austenitic stainless steel is the most common corrosion-resistant metal on the market.
- Martensitic Stainless Steel: This range of alloys is often called 400-series stainless steel and a common grade is 420A. This steel alloy also has 18% chromium with no nickel but has a higher carbon content making it tougher than other corrosion-resistant metals in the stainless steel family. However, this alloy is not as corrosion-resistant as the 300 series of steel.
- Ferritic Stainless Steel: This alloy also forms part of the 400 series of stainless steel. Among the most common grades is 430A. However, ferritic stainless steel has a much higher chromium percentage of up to 27% (to boost the resilience) but a lower carbon content (making it more ductile).
Duplex Stainless Steel
Duplex steel is a type of steel alloy that contains two different phases, hence the name. Common phases are ferritic and austenitic. Duplex steels take the best properties from both phases and combine them into an advanced corrosion-resistant metal for use in the most challenging applications. Typical grades include 2205 with 22% chromium, 5% nickel, and 3% molybdenum and S32750 with 25% chromium, 7% nickel, and 4% molybdenum.
Xometry Logo in Stainless Steel
2. Superalloys
The term superalloy refers to a high-performance metal that has been specially formulated to offer excellent mechanical and corrosion-resistance properties at high temperatures. This is why these grades of corrosion-resistant metals are often used in aerospace and energy applications. Superalloys are differentiated by the main matrix element.
- Nickel Superalloy: Nickel superalloys have high strength and excellent corrosion resistance. This superalloy is generally cheaper than cobalt versions and is also the most common of the superalloys.
- Cobalt Superalloy: Cobalt superalloys have a higher melting point when compared to other superalloys and as such have superior hot corrosion resistance.
- Iron Superalloy: Iron superalloys have high strength at room temperature and high corrosion resistance. They are also much cheaper than the other two types of superalloy.
3. Aluminum
Aluminum has good corrosion resistance and forms a passive oxide layer on its surface which is what enables it to resist corrosion. Most grades of aluminum are very chemically resilient but grades 1xxx, 3xxx, and 5xxx are the most corrosion-resistant metals in the aluminum family. They are particularly tough in a pH range of 4.5 to 8.5.
- 1xxx Series: This aluminum grade has a high purity of 99% aluminum and has the best corrosion-resistant properties in normal applications.
- 3xxx Series: Manganese is the main alloying element in this series. That makes it slightly less resilient against corrosion than 1xxx aluminum. However, it is a highly ductile material making it ideal for cold forming applications that require good corrosion resistance.
- 5xxx Series: This grade of aluminum uses magnesium as its main alloying element and has similar corrosion resistance as 3xxx aluminum.
Aluminum Sheet Metal Parts
4. Copper Alloys
Copper resists corrosion very well and is often included in other metal alloys to improve overall corrosion resistance. Some of the most common corrosion-resistant metals in the copper alloy family are listed below.
- Bronze: This is a copper alloy whose major alloying element is tin. It is specifically suited to applications that come into contact with seawater. When small amounts of silicon are added to the alloy, the corrosion resistance is significantly improved.
- Brass: This is a copper-zinc alloy and is extremely common. The addition of small amounts of tin to the alloy also increases the overall corrosion resistance of this alloy whereas ever-increasing amounts of zinc will decrease the corrosion resistance. Brass also has a lower melting point than pure copper or bronze.
5. Titanium
Titanium is widely used in the aerospace industry due to its strength to weight ratio, but its corrosion resistance makes it ideal in some industrial applications as well. Like many other metals, titanium’s corrosion resistance is derived from its ability to form a passive oxide layer on its surface. If this oxide layer is stripped off, it can quickly form again in the presence of oxygen or moisture. Titanium has a unique resistance to chlorine solutions so it is a widely used corrosion-resistant metal in applications that work with these chemicals (often called the chloralkali industry).
Which Metal is Ideal for My Application?
When it comes to selecting a corrosion-resistant metal the first step is to make use of a chemical compatibility chart. It will help narrow the options down to those with good resistance to your specific conditions. However, this requires some knowledge of which chemicals your application involves. In addition to this, certain types of loads and fabrication methods will also affect the corrosion properties. To learn how to optimally select a metal for corrosion resistance, contact a Xometry expert or get your instant quote today.
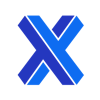