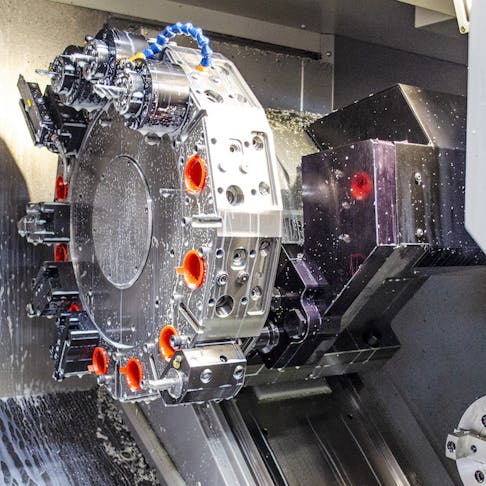
CNC Machining Trends in 2020
While 2019 delivered challenges to CNC machining shops, 2020 holds much potential for technological advancement. Turnkey parts, complex multi-axis manufacturing, smaller batch sizes, competitive lead times, and an embrace of the web are among the top trends shaping CNC machine shops for 2020 and beyond.
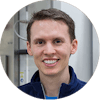
Custom manufacturing in the United States has been under significant pressure to grow over the last several years. Although the pricing of equipment overall has been more accessible, the development of a skilled workforce has been slower. Traditionally, the machinist workforce is the lifeblood of a shop, where generations of workers build a legacy through talent and lifetime clients. However, with global competition and demand for lower prices, there has been a strain to retain talent while also achieving customer goals. In spite of these challenges—or perhaps because of them—the market is growing and advanced manufacturing is on the cusp of a renaissance.
Much in the same way that Eliyahu Goldratt’s book, The Goal: A Process of Ongoing Improvement, discusses, the custom manufacturing industry has innovated in ways to eliminate bottlenecks, increase throughput, and, of course, make money. What do these innovations look like? Below are some key points of advancement, which meet modern needs while maintaining a bottom line. Customers demand turnkey parts, complex multi-axis manufacturing, smaller batch sizes, competitive lead times, and of course, an embrace of the web. Here are the top trends shaping CNC machine shops for 2020 and beyond.
Enhanced Machining Equipment
Machines Are a Platform
Very often, the machine in the shop is seen as a means to an end: a program goes in, the material is fixtured, tools cut per computer numeric controlled pathing, the process is repeated in different operations, the part is sent to inspection, and the next project begins. The truth is that a CNC machine is a platform that can streamline each one of these steps through integrations both physically and digitally. By treating a modern machine as a platform, different features can be augmented and upgraded on both the physical side, such as integrated tool measurement, and the software side, adding high levels of customization and performance monitoring. The following advancements work to enhance CNC milling by saving time, reducing setups, and sometimes catching an error before the operator says “oops!”
CAM is the Machines’ Digital Twin
Computer-aided manufacturing (CAM) software, like MasterCam, is used to program the manufacturing of a part by inserting a 3D computer-aided design (CAD) model into a virtual setup. Toolsets are added, and each machining operation is programmed and simulated. Machine tool pathing is often as simple as defining the orientation and machine parameters and letting the software compute the optimized runs. New tool pathing software can lead to double wins by reducing cutting times and mitigating wear on the endmill.
Over the last several years, CAM software has been elevated by incorporating features like advanced collision detection as standard. In the past, this software could be prohibitively expensive for a shop to license as an independent add-on. With multi-axis machining becoming more commonplace, the risk of collision increases significantly. Improved CAM software now mitigates this risk as well as improves part machining itself by taking advantage of simulation. These advancements in CAM are bridging years of workforce training by building in would-be tribal knowledge into the software.
Microservices have also helped augment CAM software in the machining industry. The company Provencut, for example, has built a platform that allows machinists to access tried-and-true “recipes,” or instructions that incorporate the machine platform, tool specifications, and the optimum pathing. These snippets can be downloaded on demand and added to other code to construct a machining operation with little risk. With the reduced risk to the cutting, machinists can produce more parts with less downtime.
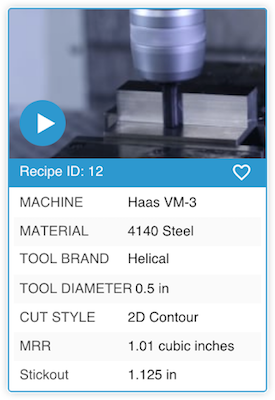
Provencut has built a library of CNC recipes that effectively allows for drag-and-drop programming for part features. (Source: Provencut)
Methods like model-based definition (MBD) and part modeling information (PMI) are also becoming more powerful for communicating design intent without the requirement of a 2D drawing. Information like tolerances, GD&T, surface finishes, and materials can be embedded in the digital model. With increased integration between CAD and CAM, MBD will become an industry standard to increase communication and reduce risk in custom manufacturing. Software like Autodesk’s Fusion 360 has seamlessly integrated CAD and CAM, allowing shop floor operators and engineers to work within the same platform.
Machines that Train the Workforce
Haas Automation, as well as other equipment manufacturers, are installing 3D CAD viewers, and even CAD/CAM packages within their machine platforms. The display on the machine controller has progressively become larger, becoming the primary interface as well as a visual guide for setups and operation progression. To address errors during machining, Haas has pre-installed troubleshooting videos directly on its machine for instant operator access.
Haas machining centers have controllers which can contain instructional images and videos to mitigate mistakes, train operators, and reduce downtime. (Source: Haascnc.com)
Integrating intelligent software like CAM and other tools within traditional machining hardware controllers help offset workforce training and development challenges. Although this equipment can sometimes be more expensive, with recurring licenses for the embedded software, it can significantly increase what an operator can do as well as mitigate risks from operator error. This leads to efficiencies like increasing throughput and decreasing workforce barriers. Amada’s press brakes for sheet metal include built-in tools and feedback to ensure operators are using the right dies and tools per operation through a digital control interface.
To put the cherry on top, newer operating platforms, like those for CNC machines, lathes, brakes, and cutters, have been upgraded with faster processing speed. This increased speed allows for more seamless inputs and feedback for operators.
More Axes To Reduce Machining Cost
Beyond software and CAD/CAM integrations, there have also been improvements to machining hardware and equipment, making them more capable and more affordable than ever before. Multi-axis machining centers such as 4- or 5-axis have entered competitive marketplaces, enabling ownership or use of high-quality machines at a lower price. These machines can be dedicated, with pre-installed rotary axes, or upgraded using interchangeable rotary tables or trunnions. For example, a 3-axis machining center can be upgraded with 5-axis capabilities by adding a trunnion that adds tilt and rotation of the workpiece. Automated tool changers can also come as a stock item or upgrade, with increases in the count of tool holders allowing for more operations with fewer setups due to tool capacity.
The benefit of adding axes to a machining center is a reduction in setups. For each setup, custom fixturing may require additional operations and materials. With the reduction of setups, the labor per part is decreased. This reduces both cost and risk as measured by the number of steps per operation which could have operator error and, therefore, increased scrap. Improvements in machining CAM software have further empowered 5th axis machining centers by optimizing guiding curves for tool pathing, improving material removal using live contouring. Utilizing additional axes is also becoming common on other platforms beyond mills, such as wire EDM and laser, plasma, and waterjet cutting to create more features in fewer operations.
A live tooling lathe with a 4+ axis machine, allowing for multiple operations to be completed beyond axial/concentric features, often completing full parts in a single operation. (Source: Xometry)
Better Tooling and Fixturing
Purchasing Drills, Mills, Inserts and more through eCommerce Sites
Like a value-added reseller (VAR) for CAD software, machine tooling representatives often add significant insight and application expertise when identifying what tooling to purchase to match the material, feature sets, and machine capabilities. Over the past several years, and moving into 2020, online resources have become available to augment some of this expertise with eCommerce platforms. Tool supply websites like Xometry Supplies offer direct-from-manufacturer selections and pricing with simple searching and filtering. This can include raw material, like 6061-T6 aluminum, as well as a variety of drills, mills, and indexable tools with inserts. Adding eCommerce to a traditionally consultation-based buying experience reduces bottlenecks in sourcing and procurement, particularly for reorders and stocking.
eCommerce options for difficult-to-source tooling have become popular resources for shop purchases. (Source: Xometry Supplies)
Other resources for online sourcing and purchasing of tools include industrial vending machines like AutoCrib and MSC Direct. These reduce lost time due to tool breakage and re-order. These machines are cabinets that are typically connected to the internet and can track the inventory of items. Based on the needs of the machine shop, these cabinets can automatically re-order stock of commodity bits and tools once a minimum quantity is reached. The combination of vending platforms with accessible tooling, regardless of the configuration, empowers CNC machine shops to find the right tools for the job.
Universal Fixturing on the Rise
Vacuum fixtures are typically used only as they’re required for projects that are difficult to secure—or easy to deform—with a standard vise. A vacuum fixture, or vacuum plate, includes an embedded valve where a hose can draw suction and a grooved surface accompanied by gaskets or O-rings to create even negative pressure around a part or blank. This pressure can hold the part in place even when it's being machined. Workholding suppliers like Pierson have created universal bases called SmartVac that can be custom configured for multiple operations without a custom build per part. Vacuum fixtures like these are extremely powerful for initial machining operations since they offer a turnkey alternative to a vise. Many of these universal base styles can also be easily augmented by adding custom top plates for repeat work at a fraction of the cost versus making a full fixture from scratch.
A universal vacuum plate can often live on a workcenter full-time and serve multiple operations without part-specific custom fixtures (Source: NYCCNC).
Another workholding solution comes from Matrix Innovations, who has created universal soft jaws. These specialized sets of jaws have pins that adjust individually to contours and can be locked once in place for repeated operations. Both of these solutions, vacuum tables and reusable soft jaws, reduce the parts needed to be custom manufactured per operation, allowing the machinist to focus on value-added processes that can be delivered and invoiced.
Robots and Cobots
Robots have worked on factory floors in various ways for decades, and typically have best served automation for high-volume production. This can include using robots to move parts in process or control end effectors which can weld, rivet, paint, etc. Once programmed, an industrial robot works autonomously and is caged for safety in the workspace.
Collaborative robots, better known as cobots, have been more prevalent in smaller shop floors in the last few years, and are rising in popularity moving through 2020. The difference between an industrial robot and a cobot is that cobots are designed to operate alongside human workers. Cobots also typically have more intuitive means of programming, including being “taught” their intended operation through manual movements. With cobot units, such as those provided by Universal Robots, an operator can train a cobot by holding and adjusting its arm and end effector through its intended operation, which the cobot will remember and repeat. By simplifying the programming, a cobot can be versatile, with applications for both production as well as non-production environments like job shops and high-mix manufacturing environments.
The rise of cobots in CNC machine shops can make workers more productive without significant infrastructural changes and intensive training. This technology, along with improvements in tooling options and fixturing, can improve daily production output while reducing human error, which then improves overall shop deliverables.
A collaborative robot, or cobot, can work alongside machinists and operators to increase productivity. (Source: Universal Robots)
Sensors, Feedback Loops, and the IIOT
The book, The Goal, stresses the necessity of identifying the primary bottleneck in operation and determining a way to eliminate it or increase its throughput. In the novel, the bottleneck is easily identified by identifying where production parts are stacking up in the process. Once identified, another machine is introduced in that process step to run parallel jobs and better streamline the workflow.
This approach is useful for production, but with higher demands in custom low-volume manufacturing, it is often difficult to truly understand critical bottlenecks without good data. This is where novel sensors, feedback systems, and predictive software help bridge these awareness gaps by aggregating data over various jobs to separate signals from noise on the shop floor.
Machine Monitoring Combines Hardware and Software
Manufacturing, even in small shops, is adopting the industrial internet of things, or IIOT, which utilizes a software dashboard to aggregate and report on data coming from various operations. MTConnect has built a series of hardware integrations for machines that monitor and output machine data, which can be used to schedule work more effectively. MTConnect’s hardware is installed on machining centers or can use integrated sensors, which are becoming more standard with new equipment.
The company Amper has a novel alternative to MTConnect’s retrofits. Amper has an IIOT device that wraps around the shop equipment’s power cable and monitors electric current. It then uses artificial intelligence (AI) and machine learning to build a signature library for that machine. These signatures could be when this machine is idle or when it moving, and when it is cutting material.
Once this data is gathered, trends can be identified by floor managers and company leads. This information, along with software-augmented suggestions, can help better apply resources to operations that strategically increase overall output. More importantly, the effect of shop floor decisions can be measured and improved upon.
Another important trend in machine monitoring is the improvement of preventative maintenance, which means using predictive models and data to ensure downtime is scheduled and not a surprise. This is historically difficult without IIOT-enabled feedback loops, such as in a generational shop where machines are from various OEMs and were purchased over time.
Tool Presetters and In-Machine Measurement
Tool presetters measure the cutting faces of a tool and ensure the machine program’s assumption of tool length and diameter is accurate to reality. Presetters can be stand-alone units or integrated within the machine platform. The benefit of having a presetter installed within a CNC machine is that the tool can automatically check tools during changes. For example, a presetter may identify broken or worn endmills and drills during a change and prevent upstream rejections. Tool presetters can provide feedback and in-situ correction for most new machining CAM software and platforms.
Presetters, combined with machine probe kits like those from Renishaw, significantly mitigate risks during operation. These sensors provide concrete, in-situ feedback for what the CAM program has predicted digitally. Vertical and horizontal machining units with CMM touch-trigger probes can double-check manual indication of part setups and provide minor corrections to maintain repeatable, consistent quality over multiple cycles. Probes can also provide accurate measurements of features, and savvy operators will utilize them to check for features during multi-operation jobs to ensure the part and program are matched appropriately. This use is extremely valuable for shops that have separate programmers and operators over multiple shifts to reduce scrap.
While in-situ IIOT feedback loops are finding a common home in larger shops, even smaller machine shops are now considering digital probes, wifi connections, and embedded machine monitoring a standard for their equipment. In 2020 and beyond, more integration will happen across digital and physical machining platforms to build better decision-making tools for high-throughput machining businesses.
Specialized CMM probes are safe for machine tool changers and the shop floor to assist accurate indication, in-process inspection, and operational checks. (Source: Renishaw)
3D Printing Is Helping Machining Businesses
There is a high chance that a 3D printed part or tool has found its way to your shop floor. 3D printing, also known as additive manufacturing, allows for custom shapes to be created with only a CAD file. Due to a lack of setup requirements, and a robust list of materials and processes available for printing, 3D printers have become assistive technologies for machining production.
The Right Parts for Custom Needs
3D printed plastic parts are typically not as strong as machined components. However, they have a distinct advantage of being able to hold complex shapes and geometries with little associated costs and lead times. A common use for 3D prints in shops is custom fixturing. For example, a complex part made on a live tooling lathe may be difficult to hold and index for operations like installing threaded inserts, pressing in pins, or aligning for laser marking. With 3D printed jigs and fixtures, an operator can easily create cradle-like structures to hold work consistently in the place of performance, ensuring repeatability in a product. 3D printed components also commonly act as drill guides, edge protectors, and other tools which can benefit from custom, purpose-designed geometries. Because making a 3D printed part does not occupy a CNC machine, it is an ideal parallel process for machine shop production for specific tools.
Depending on the application, 3D printed components can also be deliverable units for prototyping or low-volume production. Fused deposition modeling (FDM or FFF) can be easily sourced via online 3D printing services or built in-house using desktop 3D printers like Ultimaker or Markforged platforms. FDM creates parts by melting a filament of plastic, such as ABS or PC, and extruding it in the shape of the provided CAD design. Other industrial offerings like selective laser sintering (SLS), multi jet fusion (HP MJF), direct metal laser sintering (DMLS), and digital light synthesis (Carbon DLS) offer more robust end-use application materials ranging from polymers to metals.
A 3D printable jig (blue) designed to hold a part in place (translucent gray) for consistent marking. (Source: Xometry)
Manufacturing as a Service and Online Marketplaces
Many of the tools and trends previously described work on the guidance of eliminating bottlenecks, reducing labor and operations, and enhancing the workforce through better software. All of these solutions aim to increase quality deliverables per day as they are processed through the machine shop. However, there is a trend which is a consistent challenge amongst small business manufacturing companies: securing work.
Connecting buyers with machining suppliers can be a challenge due to mismatches with capabilities, capacity, and location. 2020 is a defining year for Manufacturing as a Service (Maas). MaaS platforms like Xometry act as both a storefront for buyers as well as a matchmaker for manufacturing shops. For the buyers, a MaaS platform provides the ease of a single vendor, allowing multiple manufacturing projects to be channeled through a digital supply chain manager. Work on a MaaS platform is distributed to capable manufacturing partners, who can secure it on demand. In many ways, MaaS is the gig economy response to custom manufacturing. Due to the aggregate power of a MaaS platform, CNC machine shops and other suppliers can use it both as a primary business channel or an ad-hoc capacity filler. A MaaS service benefits buyers with its large, elastic capacity that leverages the strengths of each manufacturer on its network. More machine shops are joining MaaS networks and going through steps to onboard as a manufacturing partner to gain access to online job boards.
MaaS platforms add significant benefit to suppliers as well, by complementing in-house services and extending shop capabilities without investment. Machine shops have the ability to off-load work to qualified manufacturers without losing days to RFQs and negotiations. Complementing services in the MaaS ecosystem include tooling and material providers like Xometry Supplies and finishing services consolidate and simplify resource procurement on active jobs, regardless of if it was internal or accepted through a MaaS job board.
The Future of Machining in 2020 and Beyond
Many of the CNC machining trends for 2020 and beyond are the increasing prevalence of tools and technologies that help shops adapt to a highly competitive, global manufacturing marketplace. The buyers, procurers, engineers, and supply chain managers who are purchasing manufactured components have an objective to secure quality suppliers at low costs and with timely deliveries. With the evolution of the internet, all systems are becoming interconnected, from the digital probes monitoring workpieces to MaaS platforms that bring in new work.
Machine shops are building more flexible workflows, with quicker responses to lower volume work and tighter manufacturing deadlines on production projects. Internal processes and planning software is improving throughput, increasing daily revenue and discovering more capacity even on legacy equipment. In a market that increasingly demands shorter lead times and cheaper prices, novel new technologies, including those in additive manufacturing, are equipping the machining workforce with the necessary tools to take on the challenges of a global marketplace.
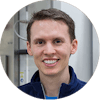