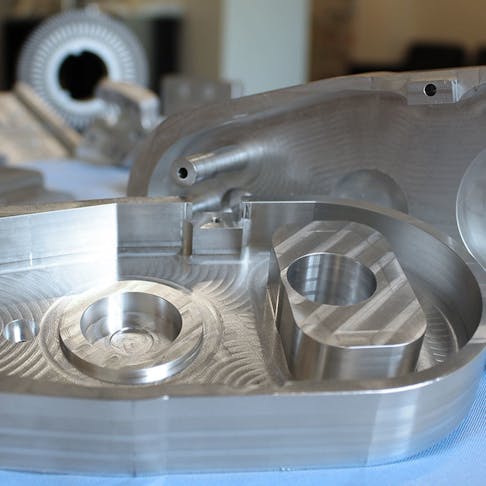
How to Choose the Right CNC Material for Your Part
Regardless of your industry, choosing the right material is one of the most important components in determining the overall functionality and cost of your part. Here are some quick tips for choosing the right material.
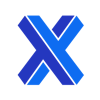
CNC machining can create high precision, end-use parts for nearly any application. It allows for amazingly tight tolerances on part dimensions and complex designs. But like any manufacturing process, the material selection is a critical component in determining the overall functionality and cost of your part: the designer defines the important material characteristics to the design—hardness, rigidity, chemical resistance, heat treatability, and thermal stability to name a few.
Xometry machines a wide variety of metals and plastic materials as well as other custom materials available on request. Read on to learn more about the advantages and tradeoffs of manufacturing metals and plastics.
Metals
As a general rule, softer metals, like aluminum and brass, as well as plastics machine easily and will take less time to remove material from the part blank which in turn reduces machine time and cost of machining. Harder materials, like stainless steel and carbon steel, must be machined with slower spindle RPMs and machine feed rates which would increase the cycle times versus the softer materials. As a general rule, aluminum will machine about 4 times faster than carbon steel, and stainless steel will machine half as fast as carbon steel.
The type of metal is a critical driver in determining the overall cost of the part. For example, 6061 aluminum bar stock is approximately half the price per pound of aluminum plate, and 7075 aluminum bar stock can be 2 to 3 times the cost of 6061 bar stock. 304 stainless steel costs about 2 to 3 times what 6061 aluminum costs and is about twice as much as 1018 carbon steel. Depending on the size and geometry of the part, the material cost can be a significant portion of the overall price of the part. If the design does not warrant the properties of carbon or stainless steel, consider using 6061 aluminum to minimize the material cost.
Plastics
Plastic material can be a less expensive alternative to metals if the design does not require the rigidity of metal. Polyethylene is easy to machine, and it is about 1/3 the cost of 6061 aluminum. ABS is typically 1.5 times the cost of acetal. Nylon and polycarbonate are approximately 3 times the cost of acetal. Although plastics could be a cost-effective material alternative, keep in mind that depending on the geometry, tight tolerances can be harder to achieve with plastics, and parts can warp post-machining because of the stress created when material is removed.
Here are a few additional guidelines to consider for choosing the metal or plastic that’s right for your part:
What will your part be used for?
The end environment where your CNC machined part will be used will have the most significant impact on material selection. For example, if you’re using your part outside or in wet environments, use stainless steel as opposed to carbon steel so your part won’t rust.
Design specifications like stress load, tolerance, and types of fastening (welding, rivets) can also impact your choice of material, as can specifications such as for military and aerospace parts or FDA-regulated environments.
Strength and heat resistance
There are many different ways to measure material strength including tensile strength, material hardness, and wear resistance. Choosing the material that incorporates the different types of strength your design calls for will allow you to select the best material for your part.
Likewise, very low or very high temperatures will restrict you from using certain materials. Environments where there is high temperature fluctuation are particularly important to consider since some materials will expand or contract considerably even with small temperature changes.
For more information on which material is best for your parts, you can contact our expert engineers via support@xometry.com. You can upload your 3D CAD file directly on our Instant Quoting Engine, or use our free SOLIDWORKS, Autodesk, and Onshape Add-Ins for instant quoting and manufacturability feedback.
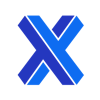