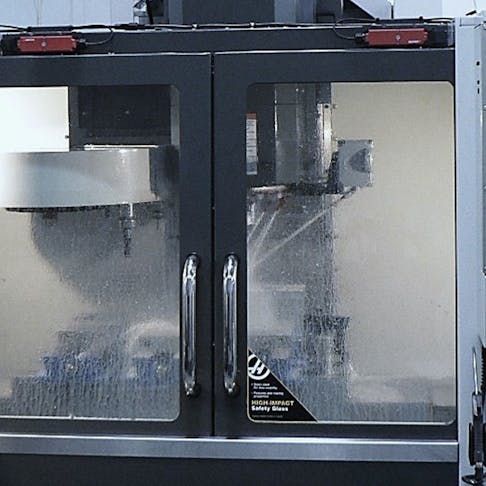
The Advantages of 5-Axis CNC Machining
If you have questions about creating sturdy parts using CNC Machining, you’ve come to the right place. Our quick guide will help you understand the advantages of 5-axis CNC machining so you can get started on your next part.
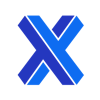
What is 5 Axis Machining?
CNC (computer numerical control) Machining is a means to remove material using high-speed, precision machines that use a wide variety of cutting tools to create the final design. There are three main types of CNC machines: vertical milling machines, horizontal milling machines, and lathes. To successfully make a part on a CNC Machine, programs dictate tool movement. The programmed instructions given to the CNC machine are encoded using CAM (computer-aided manufacturing) software in conjunction with the CAD (computer-aided design) file uploaded to the Xometry quote page.
A 5 axis machine has two more axes than the historically more common 3-axis machine. "5 axis" means that the cutting tool can access the part in 5 directions instead of 3, allowing for more movement and rotation. 5 axis platforms are achieved by adding tilt and rotation to either the workholding platform or the tool spindle itself. With a 5th axis, machinists can machine up to 5 faces in just one operation, making the process both highly precise and efficient. 5th axis machines are best used for parts that require complex movements, or where GD&T datums and features benefit from minimal setups. A majority of CNC parts require 5 faces to be machined, so this process is getting more common and more valuable with both domestic and overseas shops.
The picture illustrates a part being rotated so that the tool remains tangential to the part. 5 of the 6 faces can be machined with one setup saving you time and money on your part. The CAD model is loaded into the CAM software and tool paths are created based on the required geometry of the manufactured part. Once the tool paths are determined, the CAM software creates machine code that instructs the machine as to how fast to move, how fast to turn the stock and/or tool, and the location to move in a 5-axis X, Y, Z, A and B coordinate system.
What are the Axis in 5-axis? X, Y, Z, A, and B
X | Y | Z | A | B |
---|---|---|---|---|
X Left to right | Y Front to back | Z Top to bottom | A Rotation around X (tilt forward, backward) | B Rotation around Y (Spin, tilt left to right) |
What are the Advantages of 5-Axis Machining?
5-axis machining means that the mill and the part can be moved in up to 5 ways simultaneously around multiple axes. Xometry’s 5-axis machining capabilities allow complex parts to be manufactured most cost-effectively.
Here are five main advantages:
- The number of setups is minimized
Multiple setups (with 3-axis machining) are used to create the geometry by manually rotating the part for contoured parts or parts with machining on several faces. Using the 5-axis technology versus conventional 3 -0xis machining requires fewer setups to create a part with complex geometry. - Often eliminates the need for complex fixtures
With 3-axis machining, complex fixtures must often be made to hold the part in the orientation necessary to create the feature. 5-axis machining eliminates the need and cost of creating the fixtures because the part can be held once and rotated to create the geometry. - Faster material removal
5-Axis machining allows for the cutting tool to remain tangential to the cutting surface. Lower cycle times and costs are achieved because more material can be removed with each tool pass. - Better surface finishes
Better surface finishes result by using the 5-axis capabilities on contoured geometry. With traditional 3-axis machining, very minor cuts must be used in order to create a good surface finish resulting in longer lead times. - Best for achieving complex GD&T call-outs
5-Axis machining pairs well with GD&T call-outs where datum features can be produced in a single operation versus multiple setups on a 3-axis. For example, off-axis holes that are respective to a central datum feature. 5-axis machining also benefits when surface profile tolerances are required, particularly on complex contoured surfaces.
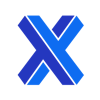