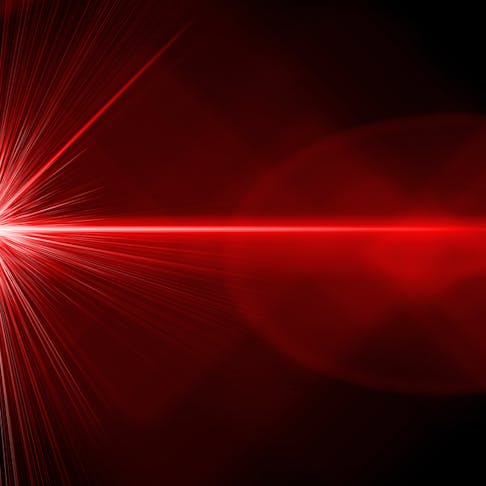
Laser Beam Profiler: Definition, How It Works, and Purpose
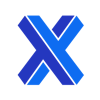
The measurement of a laser beam’s optical profile plays a pivotal role in various laser applications. It guides the design and fabrication of lasers to achieve the desired beam characteristics. To accomplish this precision of the laser beam, a beam profiler comes into action. It captures, displays, and records the laser beam's intensity distribution at a selected plane transverse to the laser beam's direction of travel. By monitoring beam quality, critical advancements can be made in laser material processing applications. Tasks such as hole drilling benefit from consistent monitoring, ensuring the maintenance of the desired level of quality throughout the laser's operation.
This article will discuss the fundamentals of laser beam profilers, how they work, and their significance in optimizing laser performance.
What Is a Laser Beam Profiler?
A laser beam profiler is a device used to capture, display, and record the intensity distribution of a laser beam with respect to a plane transverse to the direction of beam propagation. It is a critical tool used in various laser applications to ensure that the laser beam has the desired spatial characteristics and that the beam meets the required specifications. Some of the common applications of lasers that can benefit from beam profiling include: laser cutting, welding, engraving, measuring, and other laser-based manufacturing processes, as well as medical and scientific research.
How Does a Laser Beam Profiler Work?
A laser beam profiler provides valuable insights into the shape, size, energy level, and uniformity of a laser beam. Two primary techniques are employed in laser beam profilers: camera imaging and photodetector methods. In the camera imaging method, the laser beam is attenuated and directed onto a CCD (charge-couple device) or CMOS (complementary metal-oxide semiconductor) camera, which captures a 2D image of the beam's intensity profile. Each pixel on the camera's sensor represents a specific area of the beam, and the intensity of light falling on each pixel is measured. This results in a visual representation of the laser beam's characteristics.
Photodetector techniques, on the other hand, such as knife-edge and scanning-slit methods, involve blocking or scanning the beam and measuring the transmitted power to reconstruct the intensity profile. The laser beam profiler's software then processes the data, allowing for calculations of key parameters like beam diameter, shape, quality (often measured by the M² value), divergence, astigmatism, jitter, and other spatial characteristics.
What Is the Primary Use of a Laser Beam Profiler?
The primary use of laser beam profilers is as process-monitoring tools — ways to track beam quality — for the myriad manufacturing and scientific uses of laser technology. The important properties that can be measured include: beam shape and size, divergence, astigmatism, and intensity distribution. Laser beam profilers are essential during the design, fabrication, and testing phases of lasers. The data captured enables researchers, engineers, and manufacturers to gain insights into the laser's behavior and ensure it meets specific application requirements.
What Is the Role of a Laser Beam Profiler in Laser Cutting?
In laser cutting processes, a laser beam profiler can play a critical role in ensuring continued accuracy, edge quality, and efficiency of the cutting process. One of the key functions of the profiler is to analyze the spatial characteristics of the laser beam, including beam shape and size, divergence, and energy intensity distribution. This information allows operators to ensure that the beam is properly focused to deliver the required power density at the cutting point.
Adjusting the power density based on the material properties, thickness, and desired cutting speed optimizes the cutting process for different materials. Moreover, the profiler assists in aligning the laser beam to the cutting head and focal point accurately, which is crucial for achieving precise cuts.
To learn more, see our guide on How to Laser Cut.
How Important Are Laser Beam Profilers in Laser Engraving?
The laser beam profiler can be essential in the laser engraving process, as it analyzes and measures the dimensional features of the laser beam. This includes parameters such as: beam shape and size, divergence, and intensity distribution, ensuring that the laser is properly focused, and delivering the desired power density at the engraving point. The profiler enables monitoring of the laser beam's stability during engraving. It allows immediate detection and correction of any fluctuations or irregularities, thus ensuring consistent engraving quality. Moreover, the laser beam profiler helps in optimizing the engraving process for different materials, contributing to efficient material removal and reducing the risk of damage or overcutting.
To learn more, see our guide on How to Laser Engrave.
What Are the Key Parameters That a Laser Beam Profiler Measures?
A laser beam profiler measures several key parameters that characterize the spatial and intensity distribution of a laser beam’s energy. These parameters include:
1. Beam Astigmatism
Astigmatism is a condition where the laser beam has different focal lengths along two perpendicular axes. A laser beam profiler measures the degree of astigmatism to ensure proper beam symmetry. It also allows the detection of other beam properties (project specific) and allows the operator the make corrections to ensure that the beam adheres to the specifications.
2. Beam Quality
The beam quality, often represented by the M² value, is a measure of how closely the laser beam approaches an ideal Gaussian beam profile. The M2 value provides information about the beam's mode structure and whether it is functioning the way it should.
3. Beam Width
The beam width represents the diameter of the laser beam at a certain point along its propagation. It helps determine the spot size of the beam.
4. Beam Divergence
Beam divergence measures the spread of the laser beam as it propagates. Measurement of beam divergence is essential for determining the beam's collimation and the effectiveness of its focusing optics.
5. Beam Jitter or Wander
Beam jitter (or wander) refers to random variations in the position of the laser beam that can result in fluctuations in its intensity at the target. Profilers can monitor beam jitter to ensure stability and consistency in laser applications.
What Methods Do Laser Beam Profilers Use for Measuring?
There are several instruments for measuring laser beam profiles due to the wide range of laser types available. No single laser beam profiler can accommodate all possible wavelengths, power levels, repetition rates, pulse durations, and beam sizes. Laser beam profilers typically use three methods for measuring and characterizing laser beams. Each of these profiling techniques is discussed below:
1. Camera-Based Profiling Method
In this method, the laser beam is attenuated and focused onto a CCD (charge-coupled device) camera. The camera captures the intensity distribution of the beam's cross-section, creating a two-dimensional image of the beam profile. Silicon-based CCDs are commonly used for this purpose. They are suitable for measuring wavelengths in the visible and near-infrared range, typically from 250 nm up to around 1100 nm. The camera's pixels collect the light intensity information, enabling analysis of the beam's shape, size, divergence, and intensity distribution. Camera-based techniques provide a complete two-dimensional image of the beam profile, showing fine details and hot spots.
2. Scanning-Slit Method
Scanning-slit profilers move a narrow slit across the path of the laser beam, forcing the laser beam to pass through it. The light intensity passing through the slit is recorded by a photodetector as a function of position. The slit profiler covers the entire beam during the scan. However, if the beam lacks circular symmetry and is not near Gaussian in shape, the resulting profile might not precisely represent the intensity profile. The scan's resolution depends on the slit's width. A narrower slit yields higher resolution but reduces the amount of light reaching the detector, leading to a lower signal-to-noise ratio. This method allows for the measurement of beam width (and also, collectively, the shape), divergence, intensity, and astigmatism. Scanning slit profilers offer higher accuracy for measuring small beams directly. They are especially useful for applications that require accurate focus control or analysis of beam shape at specific points along its propagation.
3. Knife-Edge Scanning Method
Unlike the scanning-slit profiler, which makes use of a thin wire instead of a single knife edge for its measurements, the knife-edge technique relies on a sharp blade that intercepts the laser beam. Subsequently, a photodiode is used to measure the incident power corresponding to the blade's position. This information is used to determine the beam profile. By moving the knife across the beam's cross-section, the intensity profile can be reconstructed, providing data on beam width and shape.
The scanning-slit profiler offers several advantages over slit or pinhole scans. Firstly, it avoids limitations on beam intensity imposed by the size of the pinhole or slit width. Secondly, it achieves a remarkably high signal-to-noise ratio. Thirdly, its resolution is not restricted by the aperture size, enabling measurements of beams with diameters as small as a few microns at a resolution of 0.1µm. Additionally, accurate power and noise measurements can be obtained when the full beam reaches the detector during the scan.
Similar to the slit scanner, the accuracy of the scan depends on the beam's geometry. For optimal results, the beam should be circularly symmetric and approximately Gaussian in shape.
How Accurate Are Laser Beam Profilers?
The accuracy of laser beam profilers can vary based on several factors. Achieving precise measurements is a multi-faceted challenge. Unlike the case for standardized tools such as power meters or calipers, there is no industry-standard laser that can be universally referenced, making the accuracy assessment more complex.
The specific technology and model of the profiler also affect accuracy. Other factors that can influence the accuracy of the measurements include: profiler calibration, laser beam size and power, beam shape, background noise, and the software used to analyze the data. Generally, modern laser beam profilers offer high accuracy and precision in characterizing laser beams.
Reputable laser beam profiler manufacturers provide detailed specifications regarding the accuracy of their devices under specific conditions. For example, using Ultracal and Auto-Aperture can achieve second-moment beam width accuracy of about +/- 1-2% for all modes and mode mixes. However, under less favorable conditions, accuracy can reduce to about +/- 5%.
How Often Should You Use a Laser Beam Profiler?
The frequency with which a laser beam should be checked using a beam profiler varies depending on the specific application and the level of laser precision required. Generally, laser beam profilers are used during the initial process setup and calibration of laser systems to ensure proper alignment and achieve the desired beam characteristics. In critical applications, where maintaining optimal laser performance is crucial, regular beam profiling may be incorporated into a maintenance routine to identify any drift or changes in the laser beam over time.
Can a Laser Beam Profiler Be Used in the Laser Welding Process?
Yes, laser beam profilers can be used in the laser welding process. Welding is a widely used industrial application of lasers that requires precise control over the laser beam to achieve high-quality welds. Using a laser beam profiler to monitor the laser welding process allows manufacturers to ensure that the beam is well-focused and has the desired profile for the welding application.
Can Laser Beam Profiles Measure Different Types of Lasers?
Yes, laser beam profilers can be used to measure the beam properties of different types of lasers. Whether the laser is CW (continuous wave) or pulsed, ultraviolet (UV), visible light, near-infrared (NIR), or short-wave infrared (SWIR), beam profilers can capture and analyze the intensity and spatial characteristics of the laser beam. However, since there is such a wide range of lasers available, it is important to note that no single laser beam profiler can accommodate all wavelengths, power levels, repetition rates, pulse durations, and beam sizes. Each type of laser may require a specific beam profiler optimized to accurately characterize its unique spatial characteristics and output parameters.
How Much Does a Laser Beam Profiler Cost?
The cost of a laser beam profiler can vary significantly depending on such factors as the brand, type, model, and capabilities of the profiler. At the lower end, simpler and more basic laser beam profiling devices are available for under $1,000. These are often used in educational settings, small research labs, or entry-level laser applications. Mid-range beam profilers with higher accuracy, resolution, and additional features can range from $1,000 to $3,500. These laser beam profilers are suitable for a broader range of applications and offer more sophisticated analysis capabilities. For high-end or specialized laser beam profilers with advanced features, high precision, and the capability to handle high-powered or ultrafast lasers, the cost can go up to about $10,000. These profilers are typically used in cutting-edge research, industrial applications, and large-scale laser systems.
What Is the Best Laser Beam Profiler?
The “best” laser beam profiler depends on the specific requirements of the application, the type of laser being used, and the desired accuracy and features needed. It is essential to consider the wavelength range, beam size, power level and required measurement accuracy. Additionally, the quality and accuracy of the software algorithms used for data processing and analysis are also crucial factors in ensuring reliable and consistent results.
For camera-based profilers, for example, CMOS sensors are commonly used for laser beam profiling due to their performance and costs. Sensors Unlimited, Inc. (SUI) produces InGaAs detectors that are ideal for laser beam profiling in the near-infrared (NIR) range (wavelengths from 0.9 to 1.7 µm). These cameras can provide high-resolution imagery with linear power response, making them suitable for a wide range of applications.
Summary
This article presented laser beam profilers, explained them, and discussed how they work and their purpose. To learn more about laser beam profilers, contact a Xometry representative.
Xometry provides a wide range of manufacturing capabilities, including sheet cutting and other value-added services for all of your prototyping and production needs. Visit our website to learn more or to request a free, no-obligation quote.
Disclaimer
The content appearing on this webpage is for informational purposes only. Xometry makes no representation or warranty of any kind, be it expressed or implied, as to the accuracy, completeness, or validity of the information. Any performance parameters, geometric tolerances, specific design features, quality and types of materials, or processes should not be inferred to represent what will be delivered by third-party suppliers or manufacturers through Xometry’s network. Buyers seeking quotes for parts are responsible for defining the specific requirements for those parts. Please refer to our terms and conditions for more information.
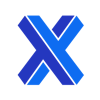