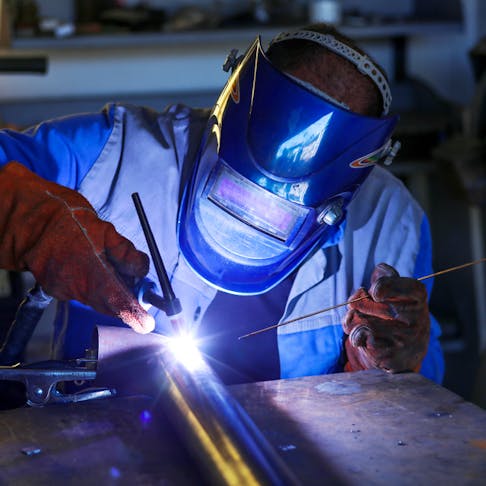
MIG Welding: Definition, Importance, How it Works, and Advantages
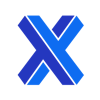
Metal inert gas (MIG) welding runs high voltage through a consumable metal wire electrode to heat and fuse metals under a shielding inert gas. It is important to various industries as it is a cost-effective, fast, and simple process for reliably fabricating metal parts.
MIG welding works by feeding a metal wire through a gun to melt and create a permanent joint. The wire acts as both the electrode and the feed material that goes into the weld. This process is achieved under the shielding of an inert gas which prevents oxygen and other contaminants from reacting with the molten metal. MIG welding is easy to learn, it doesn't require post-processing, and it is suitable for thin metals.
What Is MIG Welding?
MIG welding is one of several welding techniques that use electricity to create joints. MIG welding was invented in 1948 and despite a lot of equipment upgrades, the process has not changed. MIG welding is a form of gas metal arc welding (GMAW) and has been referred to by different names including flux-core arc welding, spray arc welding, gas metal arc welding, and short-circuit welding.
Who Is the Inventor of MIG Welding?
H.E. Kennedy invented MIG welding in 1948 in the USA. The invention of MIG welding improved upon other welding techniques as it uses a filler rod as an electrode to create an arc. This differed from previous techniques in which the electrode would deteriorate over time and require replacement.
How Does MIG Welding Differ From Laser Welding?
MIG welding uses a constantly fed metal wire and a high-voltage circuit to create electrical arcing which heats and welds metal pieces together. In MIG welding, the arc is shielded by an inert gas. The laser welding process instead uses a laser to heat and melt the metal to create a joint. The laser welding technique creates a stronger and more precise weld but MIG welding can join thicker metal together and can weld at a faster rate.
What Is the Importance of MIG Welding in Manufacturing?
MIG welding is valuable because it is fast, creates a strong joint, and can weld thick metal pieces together. MIG welding is also simple. Since it’s easy for first-time and experienced welders alike, there’s usually no shortage of MIG operators in the workforce.
What Is the Primary Purpose of MIG Welding?
MIG welding is used to join metal parts together. It functions to join steel, stainless steel, cast iron, and aluminum. MIG welding is used on sheet metal, pressure vessels, steel structures, pipelines, and automotive parts.
How Does MIG Welding Work?
MIG welding works by feeding a metal wire through a gun which conducts electricity from the welding machine. It generates an arc with the target material in order to melt both the metal wire and part of the joint and form a metal bond. As the wire is fed through and a molten weld pool is created, the weld is protected by a shielding gas. The shielding gas protects the weld from contaminants in the atmosphere.
How To Weld Using MIG Welding
When MIG welding, it is important to get the setup correct. The general steps are listed below:
- Connect the ground wire to the workpiece or welding table.
- Configure the welding machine for the metal to be welded.
- Wear the correct personal protective equipment (PPE).
- Clamp the pieces to be welded together in place.
- Create tack welds at either end of the joint*.
- Weld along the joint either by pushing or pulling the weld**.
*A tack weld is a quick spot weld meant to hold the two workpieces together for the full welding process that will follow.
**Pushing or pulling the weld refers to the gun’s positioning and direction of movement. It should be angled at 10 degrees and “pulled” so the electrode trails the gun or “pushed” so it leads the movement.
What Are Some MIG Welding Techniques?
To create a good weld, the most important thing is to maintain a steady hand with a good gun position. The tip of the gun should be no more than 3 ⁄ 4'' from the metal when welding so that the gas sufficiently covers the weld pool. The gun should be held in one hand and, where possible, rested on the index finger of the other open hand for stability. When welding two metals butted together, the gun should not angle toward one or the other. When the two metals are perpendicular, the gun should be at 45 degrees to the metal faces. Lastly, it is helpful to first rehearse running the weld without actually welding to gain a feel for the right movement.
Is MIG Welding for Beginners?
Yes, MIG welding can be done by beginners. The process is simple, the equipment is cheap, and it is relatively safe when compared to some other welding techniques. MIG welding is one of the more forgiving methods of welding.
What Are the Factors That May Affect the Quality of MIG Welding?
The most important variable that will affect the quality is the weld technique. While the setup does matter, as long as the current, gas flow, and wire feed rate are roughly correct, it shouldn't affect the final weld too much. Some of the most important variables are:
- Distance from the gun to the weld.
- Angle between the gun and the weld.
- Speed of the gun movement.
- Weld current.
- Wire feed rate.
- Gas flow rate.
- The removal of contaminants from the workpiece prior to welding.
What Type of Gas Does MIG Welding Use?
Most MIG welding machines use helium and argon because they do not react with oxygen and nitrogen. Argon is the most common shielding gas. Helium is a more expensive gas and is used for welds which require more heat.
Can You MIG Weld Without Gas?
Yes, MIG welding can technically be done without a gas tank. However, the weld still needs a shielding source to prevent oxygen in the air from reacting with the weld. To achieve this, a metal wire with a flux core is used. When the flux core is heated, it produces a gas that shields the weld. “Gasless” MIG welding requires a specialized gasless MIG welder.
What Is the Correct Parameter Setting for MIG Welding?
There are five main parameters for MIG welding: current, length of arc, angle, manipulation, and speed. None of these parameters have a standard setting and will all vary based on what metal you’re welding and the thickness of the weld. There are, however, standard charts that indicate the normal parameter settings for different welds. Generally, high current is used for welding thick metals. The shorter the arc, the hotter the weld. The gun should be held at half of the angle between the parts to be joined (i.e. the gun should be held at 90 degrees to a butt joint, 45 degrees to a T-joint, etc.). Manipulation describes whether the welder pushes or pulls the weld pool. Finally, the speed must be steady. Moving too slow will result in an oversized weld bead and possible holes in the weld joint; moving too fast may result in a lack of weld penetration.
What Are the Common Materials Used in MIG Welding?
The most common materials used in MIG welding are listed below:
1. Copper
Copper is a soft, malleable metal used in plumbing and electrical applications. MIG welding is the preferred process for welding copper. However, the heat required to weld copper is about twice that of steel where the heat temperature makes it easier and possible.
2. Aluminum
Aluminum is a soft, silvery, non-ferrous metal. Welding aluminum requires 100% pure argon gas. Aluminum welding can be difficult as the melt pool can quickly burn through the part and drip out the other side. For more information, see our guide on Aluminum Characteristics.
3. Steels
Steels are alloys made mainly of iron and carbon, usually also including sulfur and phosphorus. When welding steel, it is advised not to use 100% argon gas for shielding but rather 75% argon and 25% carbon dioxide. This is because 100% argon gas will reduce the ductility of the weld. To learn more, see our guide on the Properties of Steel.
4. Nickel Alloys
Nickel alloys are composed of nickel and usually chromium, iron, molybdenum, and/or copper. Usually, 100% argon gas is used to weld nickel alloys. However, when more energy is required, up to 40% helium can be used. For more information, check out our guide on Nickel Alloy.
What Is the Hardest Material to MIG Weld?
The hardest material to MIG weld is aluminum as it has a very low melting point paired with high thermal conductivity. Poor heat conductivity means that aluminum does not absorb the heat from the electrical arc well and so it is hard to keep a stable temperature throughout the process without either burning through or failing to penetrate the joint at all.
What Is the Easiest Material to MIG Weld?
The easiest material to MIG weld is mild steel. This is because of its high melting temperature, which makes mild steel very forgiving to changes in welding parameters. The lower the carbon content of mild steel, the easier it is to weld.
What Materials Cannot Be MIG Welded?
Materials such as wood, composites, and plastics cannot be MIG welded. Additionally, dissimilar metals cannot be welded together — aluminum, for instance, cannot be welded to steel or copper.
Can Stainless Steel Be Used in MIG Welding?
Yes, stainless steel can be MIG welded. Some of its alloying elements can make the process difficult. However, stainless steel material is poor at dispersing heat which helps the heating of the metal during the welding process.
What Industries Use MIG Welding?
MIG welding is the most common technique for repairing vehicles such as motorbikes, cars, vans, etc. Other industries that make extensive use of MIG Welding include:
- Construction
- Aerospace
- High-production manufacturing
- Shipping
- Rail
What Are Examples of MIG Welding Products?
MIG welding can cover a huge range of tasks. Examples of applications include: sheet metal welding, welding of pipelines, automotive repairs, steel structures, and heavy constructions such as bridges and building materials
What Are the Advantages of MIG Welding?
The main advantage of MIG welding is the speed of the process. Compared to other welding styles, it can contribute to shorter production times and, as a result, lower costs. Other advantages include:
- It is easy to learn.
- The process doesn't require highly skilled operators.
- Finished welds do not need much (if any) cleaning or finishing.
- It’s suitable for thin materials.
What Are the Disadvantages of MIG Welding?
The main disadvantage of MIG welding is that the finished welds are not as strong and accurate as those of other welding styles. Other disadvantages include:
- The finished welds are not as aesthetically pleasing unless they receive extra cleaning and finishing.
- MIG is less precise than other forms of welding
- The use of shielding gas means that gas has to be regularly ordered. Machine downtime is incurred as the gas cylinders must be regularly changed
- A MIG welder less portable than a gas welder due to its power requirements
Is MIG Welding Expensive?
No, MIG welding is not considered expensive. The necessary supplies and machines are cheaper when compared to other forms of welding. Additionally, MIG welding does not require highly skilled operators, nor does it need much prep work. The overall production time for MIG welds is relatively short, so it’s cheaper than most similar processes.
Is MIG Welding As Strong as Stick Welding?
Stick welding produces stronger welds than MIG welding because it can penetrate thicker surfaces and dirty surfaces. If a deeply welded joint is the goal, the stick welder will be more efficient and easier to use.
What Is the Difference Between MIG Welding and TIG Welding?
One of the main differences between MIG welding and TIG welding is the welding electrodes that are used to create the electric arc. TIG uses a hand-held rod as filler material and a non-consumable electrode, while MIG’s consumable electrode doubles as the filler. MIG tends to do its work faster and at a lower price than TIG. MIG is also a simpler process that demands less training. TIG Welding produces a stronger weld, greater weld precision, and better aesthetics. Finally, MIG welding is better suited to thicker materials and TIG Welding is more appropriate for thinner materials.
Summary
This article presented MIG welding, explained what it is, and discussed its various applications. To learn more about MIG welding contact a Xometry representative.
Xometry provides a wide range of manufacturing capabilities, including sheet cutting and other value-added services for all of your prototyping and production needs. Visit our website to learn more or to request a free, no-obligation quote.
Disclaimer
The content appearing on this webpage is for informational purposes only. Xometry makes no representation or warranty of any kind, be it expressed or implied, as to the accuracy, completeness, or validity of the information. Any performance parameters, geometric tolerances, specific design features, quality and types of materials, or processes should not be inferred to represent what will be delivered by third-party suppliers or manufacturers through Xometry’s network. Buyers seeking quotes for parts are responsible for defining the specific requirements for those parts. Please refer to our terms and conditions for more information.
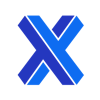