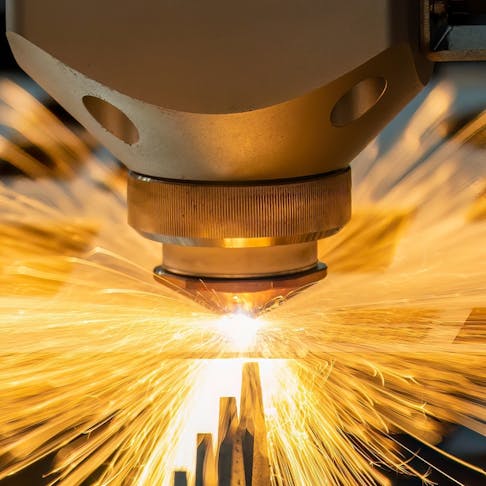
Laser Power: Definition, How It Works, Importance, and How to Determine
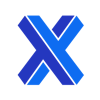
Laser power is the energy delivered by a laser beam per unit of time and per unit of area. A range of factors defines the application and utility of laser emission. These include: monochromaticity, central frequency, coherence, collimation, beam quality, minimum spot size, beam power, and irradiance. Laser power can be measured in a variety of ways. The most powerful source does not necessarily equate to the most powerful effect. The source power is usually a product specification item, rather than a factor to measure, although there are photometer tools that can do this. The power and its ability to generate a high-intensity spot are the critical properties of a laser in a laser cutter application. Spot size and energy intensity of the spot describe the beam’s ability to initiate and perform the cutting.
This article will further discuss laser power, its definition, how it works, importance, and the recommended settings.
What Is Laser Power?
Laser power defines the energy delivered by a laser beam per unit of time and per unit of area. It is a crucial parameter in laser systems and plays a significant role in determining the cutting, engraving, or marking capabilities of a cutting or engraving machine. The absolute laser power is typically measured in watts (W, kW), representing the rate of energy transfer to the cut point. The power output of lasers varies widely, ranging from a few milliwatts for low-power devices in consumer electronics or laser pointers to tens of kilowatts for industrial laser systems used in cutting or welding.
In laser cutting or material processing applications, the laser power directly affects the cutting speed and the depth or intensity of the laser's interaction with the material. Higher laser power enables faster cutting of thicker sections or harder-to-cut materials. The ability to process material rapidly also depends on the spot size and beam quality, as these increase the power per unit area, concentrating the laser power onto the smallest possible spot size to increase the intensity of energy at the cut by increasing the specific energy.
The appropriate laser power for a specific application depends on factors such as the material type, thickness, desired cut quality, and the capabilities of the laser cutting machine. Plastics or organic materials generally have higher absorption rates in the more common laser cutter frequency ranges, requiring lower laser power for effective cutting.
Laser power can often be adjusted or modulated to suit specific application requirements. Laser systems typically provide control over the power level or pulse frequency/duration, allowing operators to optimize the power output based on the desired cutting speed, precision, material type/thickness, and required cut quality.
How Does Laser Power Work?
The laser produces a stream of coherent and collimated photons that are directed towards the workpiece or application point, via light pipes or mirrors. Just before the beam hits the surface to be cut/welded/engraved, it passes through a lens arrangement that focuses the laser to a minimum spot size, to deliver a narrow spot of maximum intensity at the required cut point. The energy that hits the surface causes extreme excitation of atomic bonds, which manifests as heat at the laser contact point. When that heat is sufficient, it either liquefies the material at the laser spot or vaporizes it—or a combination of the two.
When the beam delivered is of high quality, the energy distribution is symmetrical around the center-line of the beam and offers a Gaussian distribution, making the focused dot the maximum possible intensity at its center. A lower-quality beam may have a less regular/symmetrical distribution of energy. The energy concentration may be lower at the center of the spot—making the specific energy at the spot center lower, reducing the available cutting power.
What Is the Importance of Laser Power?
Laser power, assessed by various overlapping methods, plays the most crucial role in laser-based applications. In laser cutting, welding, or engraving applications, laser power significantly affects process speed and productivity. Higher power capacity allows faster processing rate and higher productivity. It also increases the spectrum of processing capability, allowing throughput of thicker or more resilient materials that require more energy. Higher available laser power provides flexibility in the delivery of a wider range of processing—important for thicker material, hard/resilient material, and faster processing. Elevated laser power allows for sharper cuts, finer engraving, and greater intricacy.
The upper limit of laser power impacts efficiency and productivity, enabling reduced processing time. This results in cost savings by reducing machine time and improving throughput/capacity. Importantly, in cost terms, the ability to adjust laser power (up or down) to suit specific material requirements can help minimize material waste and improve overall process efficiency.
How Important Is Laser Power in Laser Cutting?
Power is important, but it is by no means the only important factor in laser cutting. In reality, for the majority of tasks, quite low power is required. Cutting thin organic materials and polymers, for example, places very low absolute power demands on a cutting machine. At the more challenging end of processing such as: handling metals, thicker materials, reflective surfaces, and harder materials, power is often the deciding factor in the ability to complete the task. For more information, see our guide on What Does a Laser Cutter Do?
How To Determine Laser Power?
Some methods to measure laser power are listed below:
- Laser Power Meter: A sensor or detector is used that absorbs the net laser energy and converts it into an electrical signal measured by the meter. These can be thermal sensors, photodiodes, or pyroelectric sensors.
- Integrating Sphere: A spherical enclosure with a highly reflective interior surface. It is used to measure the total power emitted by a laser. The laser beam is directed into the sphere, where it is scattered and evenly distributed. The power is then measured using a sensor or detector placed within the sphere—out of the direct laser path. Integrating spheres are more applicable to high-power lasers and the assessment of pulsed beams.
- Beam Profiling: Informs about the spatial distribution of the beam, assessing beam quality and uniformity. Evaluating the divergence from Gaussian distribution informs about effective power. A CCD (charge-coupled device) camera or a scanning slit device can help visualize and analyze this characteristic.
- Measurement: The absolute power can be indirectly estimated by measuring the beam diameter and the energy density. Power density is derived by dividing the measured net energy by the pulse duration or the exposure time. This method is most relevant to pulsed lasers.
What Is the Recommended Laser Power for Laser Cutting?
Recommendations for laser power setting are very wide-ranging, encompassing as they do a huge range of equipment types, materials, thicknesses, and quality implications. For example, varied materials have characteristic absorption spectra for laser energy, affecting equipment selection (laser frequency) and power needs. Some metals are highly reflective in the IR spectrum that common lasers emit. The precise properties of the material being cut profoundly influence the power required.
Thicker materials require higher laser powers to achieve useful productivity and minimize the heat-affected zone (HAZ). Thicker materials cut with too little power enable excessive heat buildup—rather than fast vaporization or melt-blow removal. Thinner materials benefit from lower laser powers to minimize HAZ and char damage.
Determining the optimal power setting for a task involves experimentation and adjustment through sample testing, assessment of results, and adjustment of power.
How Thick Can a 6,000-Watt Laser Cut?
The thickness of aluminum that a 6 kW laser can cut will vary according to the laser type/frequency, beam quality, optics quality, and the type and grade of aluminum. While a 6,000-watt laser can cut aluminum of considerable thickness, there are absolute limits to the thickness, for good quality and rapid processing. In general, a 6,000-watt laser can cut aluminum up to approximately 25–30 mm (1–1.2 inches) for low-alloy aluminum and 20–25 mm (0.8–1 inch) for high-grade plate aluminum.
What Is the Recommended Laser Power for Laser Engraving?
There is no simple instructed value for power level in laser engraving aluminum. It depends on a variety of factors like the desired engraving depth, surface finish, and the type/grade/annealing of the aluminum.
For example, the types and grades of aluminum have different absorption properties for laser energy. Generally, aluminum is a highly reflective material, so high laser power is required for effective engraving. The desired depth of the engraving also plays a central role in determining the laser power. Deeper engravings typically require higher laser powers. However, less-deep engraving often benefits from an approach using lower power and increased passes.
For many aluminum engraving applications, a power of 10 to 50 W suffices for good results, and few applications benefit from laser powers of more than 100 W. For more information, see our guide on the Laser Engraving Process.
Are 100 Watts of Laser Power Too Much for Laser Engraving?
Yes, a 100 W laser at fixed power may well be too powerful for good-quality engraving. If power can be reduced by absolute settings or by pulse duration, then a 100 W laser will provide a great capability that can be exactly adjusted to the task. It is a good idea to evaluate performance in a task’s initial setup, dialing back power settings and speeds and then increasing them cautiously.
What Is the Recommended Laser Power for Laser Welding?
The recommended laser power for laser welding is highly dependent on the type and thickness of the materials being welded, the joint configuration, the weld quality required, and the specific capabilities/quality of the welding system being used. For example, materials have varied absorption properties for the beam energy, so the power required to initiate welding will depend on the material. Also, the section thickness will profoundly affect the ability to generate sufficient heat. Thicker material at the joint line will require higher power to achieve proper penetration and weld strength. As with all laser-based processes, a careful evaluation of equipment capabilities, operational parameters, and quality of results is required, using sample materials before a process can be confidently executed. For more information, see our guide on How Laser Welding Works.
Is 4-kW Laser Power Good for Laser Welding?
Yes, a 4-kW laser will suffice for welding aluminum, depending on the joint geometry, material thicknesses, and speed of operation required. Aluminum has relatively high reflectivity and thermal conductivity, compared to many materials. This tends to impose higher power requirements for effective processing. Welding productivity/capability will also be affected by laser type, given the better energy absorption that occurs at some laser frequencies. For example, CO2 laser energy is significantly reflected by aluminum, whereas Nd:YAG emission frequencies are almost entirely absorbed.
Which Is More Important, Laser Power or Speed?
Both laser power and speed are critical factors in achieving good productivity in laser cutting aluminum. In reality, the power defines the processing speed to a great extent. Laser power is critical in processing aluminum effectively. Sufficient power is necessary for effective melt/vaporization, to deliver a clean and precise cut. Higher power provides for faster processing, especially for thicker sections. Multiple passes can compensate, at a cost to throughput and quality.
Striking a balance between power and processing speed is the route to optimal results. Consider the thickness and type of aluminum, desired cutting quality, and the parameter capabilities of the laser processing equipment. The goal is to maximize cutting speed without sacrificing the quality and accuracy of the cut.
Summary
This article presented laser power, explained it, and discussed its importance and how it works. To learn more about laser power, contact a Xometry representative.
Xometry provides a wide range of manufacturing capabilities, including sheet cutting and other value-added services for all of your prototyping and production needs. Visit our website to learn more or to request a free, no-obligation quote.
Disclaimer
The content appearing on this webpage is for informational purposes only. Xometry makes no representation or warranty of any kind, be it expressed or implied, as to the accuracy, completeness, or validity of the information. Any performance parameters, geometric tolerances, specific design features, quality and types of materials, or processes should not be inferred to represent what will be delivered by third-party suppliers or manufacturers through Xometry’s network. Buyers seeking quotes for parts are responsible for defining the specific requirements for those parts. Please refer to our terms and conditions for more information.
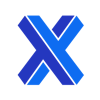