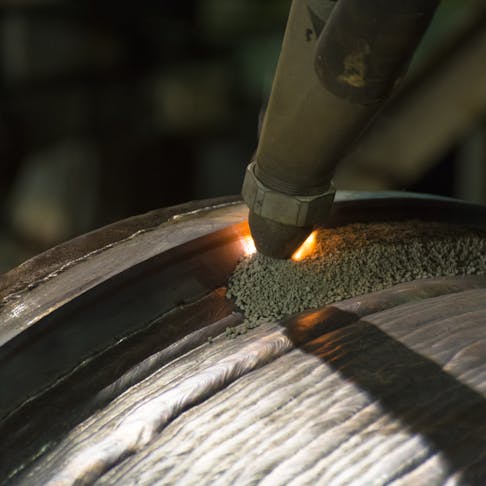
Submerged Arc Welding (SAW): Definition, Purpose, and How It Works
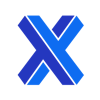
Submerged arc welding (SAW) is a well-established process that uses a continuous feed of a filler/electrode, melted by an electric arc between the electrode/filler and the work. Submersion refers to the hopper-fed flux powder that covers the weld path. This approach allows greater control and automation of straightforward welds. It reduces the direct need for operator skill, as the process—once established and validated—will be highly repeatable.
This article will discuss submerged arc welding, its importance, how it works, its advantages and disadvantages, and the equipment used.
What Is Submerged Arc Welding (SAW)?
Submerged arc welding is a long-established, automated welding process in which an AC arc is formed between a heavy gauge workpiece and a continuously fed electrode. The arc is shielded by a directly deposited granular flux material of several possible varieties. This flux stream is fed over the weld zone to provide the exclusion of atmospheric contamination and a reducing environment. It also acts to contain some of the arc energy in the melt pool, enhancing weld quality and improving the application of energy. The non-adhesive, gravity-fed nature of the flux material implies a significant limitation—that only welding of upward-facing and close-to-horizontal seams is practical using SAW.
Submerged arc welding is commonly used for welding thick sections of steel, especially in applications such as shipbuilding, structural steel fabrication, pressure vessel manufacturing, and pipeline construction. It offers high deposition rates and throughput, deep penetration capabilities, excellent weld quality, and the potential for simple automation to reduce reliance on skilled labor.
What Is the History of Submerged Arc Welding (SAW)?
The history of submerged arc welding originates in the early 1930s when it was developed as a more reliable welding process that reduced the need for direct operational skills. The SAW process was initially developed by the National Tube Company (now part of the U.S. Steel Corporation) in the US. It was initially developed for welding longitudinal seams in pipes formed from rolled plates. The process involved using a bare electrode and a layer of flux powder to shield the arc and the weld pool. During World War II, SAW underwent significant improvements and gained wider acceptance, as a way to accelerate wartime production of ships and heavy military vehicles. The process was refined by the use of covered electrodes and the development of fluxes with more precisely tailored compositions and properties, improving the control over the weld pool and the metallurgical and crystalline properties of the resultant welds. In the 1950s, SAW gained wide acceptance in industrial applications, due to process and quality developments. During the 1960s–80s, further advancements included the development of more sophisticated fluxes with improved slag removal characteristics and enhanced chemical compositions. Automatic welding systems, including mechanized and robotic setups, were also introduced. Recent advancements have focused on optimizing process parameters, improving weld quality, and increasing throughput. The use of smarter power sources, CNC control systems, and optical monitoring techniques have greatly improved productivity and quality, keeping the process as a mainstay in heavy plate welding applications.
How Does Submerged Arc Welding Differ From Arc Welding?
Submerged arc welding and arc welding are closely related welding processes that differ in several details. In SAW, the welding arc is submerged beneath a layer of granular flux, which shields the arc from the surrounding atmosphere. The flux serves multiple purposes, such as providing a protective shield, reducing spatter, and removing impurities. Arc welding refers to a broad category of welding processes in which the arc is shielded from the atmosphere by a variety of other means such as flux-coated filler rods, and blown or sealed atmospheric blankets.
SAW utilizes a granular flux material that is continuously deposited onto the melt pool. In arc welding, various methods can be employed, including gas tungsten arc welding (GTAW or TIG), gas metal arc welding (GMAW or MIG), and shielded metal arc welding (SMAW).
SAW is highly suited for automation and mechanization due to its tightly controlled process parameters. It is commonly used with CNC or robotic welding systems, whereby the electrode, flux delivery, and weld parameters can be precisely tuned and held stable. Arc welding processes can range from manual, handheld operations to semi-automated and fully automated systems. For more information, see our guide on What is Arc Welding?
What Is the Primary Purpose of Submerged Arc Welding?
The core purpose of SAW is to weld larger sections of steel quickly and repeatably. SAW is specifically suited for welding large structural parts, heavy-gauge plates, and components that require deep penetration into heavy sections.
How Important Is Submerged Arc Welding?
SAW is a critically important manufacturing process with central relevance in various industries. SAW is particularly applicable to welding very thick sections of steel. It facilitates high throughput, allowing for the rapid processing of welding. Deep penetration capability makes SAW crucial when welding thick plates or components. It reliably produces high-quality welds with excellent mechanical properties. The low spatter levels and reduced risk of defects make this a widely relied-upon process.
How Does Submerged Arc Welding (SAW) Work?
SAW involves the formation of a steady and extremely high-power arc between a continuously fed electrode and the workpieces. The arc melts the edges of the workpieces and the filler rod, merging these into a single and consistent melt pool that is traversed along the weld path. Oxidation and weld-degrading inclusions are prevented by a reducing flux cover that is applied prior to the arc. Figure 1 is a SAW diagram:
Submerged arc welding schematic diagram.
Image Credit: https://www.researchgate.net/
What Is the Process of Submerged Arc Welding (SAW)?
SAW is a process that can be established to be extremely repeatable. Its parameters and material options are adaptable to a wide range of applications. The general process steps of SAW are listed below:
- Prepare the workpieces by cleaning and positioning them for welding.
- Prepare the tubular electrode. A tubular electrode material is often considered to improve melt characteristics in the arc, behaving as if a higher power is being applied. The electrode must be made of a material compatible with the base metals being welded. Granular flux is deposited over the weld in advance of the arc.
- Strike the arc between the electrode and the workpiece. This creates an intense and highly localized heating that melts the electrode and the surrounding material into a melt pool. The flux covering the arc melts and forms a protective slag layer over the weld pool, shielding it from oxygen.
- As the arc heats the metal, a molten weld pool is formed, merging the parts and the electrode material. The electrode wire is continuously fed into the weld zone, adding filler metal to the pool, and the parts or welding head are moved to extend the melt pool in the direction of the weld. The trailing edge of the melt pool solidifies as it cools, creating a strong bond between the base metals. In this way, the initial weld gap is filled through the merging of the edges of workpieces and filler material.
- After the welding is complete, the joint and overlying slag layer formed by the flux cools and solidifies. The slag is then chipped off or removed using abrasion, revealing the completed weld joint. The weld may undergo additional finishing processes such as grinding, cleaning, and inspection.
What Is the Best Method of Submerged Arc Welding (SAW)?
The best method for executing a SAW process will be highly dependent on the materials, joint geometry, and quality requirements of the outcome. A stainless steel pressure vessel, for example, will have much higher quality expectations placed upon it than a dry gas pipeline.
What Equipment Is Used for Submerged Arc Welding (SAW)?
SAW requires specific equipment to perform the welding process effectively. Here are the key equipment components used in SAW:
- Constant-Current or Constant-Voltage Power Module: This conditions the electrical energy to induce and maintain the welding arc and can be constructed from a transformer-rectifier unit or an inverter.
- Welding Head: The welding head (or boom) retains and orientates the welding torch. It can be a stationary or movable component, wherein either the boom moves along the weld or the parts traverse under the boom to perform the weld.
- Electrode Wire: The continuously fed electrode is directed into the weld joint. The feed rate is under operator control, preset, or under dynamic control.
- Welding Torch (or Head): The delivery mechanism for the electrode wire.
- Flux Hopper/Delivery System: Supplies a flow of flux granules over the arc and the weld pool.
- Flux Recovery System: Collects and recycles the unused or over-applied flux. This helps control costs, as flux is a significant part of the consumable value.
- Cooling Apparatus: Improves the longevity of the welding equipment.
- CNC Control Panel: To adjust and regulate various parameters of the SAW process.
What Is the Flux Used in Submerged Arc Welding?
In SAW, a granular flux material is used to cover the arc and the weld pool. It is gravity deposited as a blanket over the active weld area. The flux serves several purposes, playing a crucial role in the welding process. Flux composition and properties vary depending on the application and the base metals being welded. Examples of flux are: basic (alkali) fluxes, acidic fluxes, neutral fluxes, and alloyed fluxes.
Does Submerged Arc Welding Need Gas?
No, SAW does not benefit from gas shielding. Any gas supplied to encompass the weld would blow away the flux coating, with severely negative consequences.
What Are the Metals Used for Submerged Arc Welding (SAW)?
SAW is primarily applied to high- and low-alloy content steels, including medium-carbon and stainless steel. Some materials used are listed below:
1. Stainless Steel
All of the readily weldable stainless steels can be joined using SAW. The process can also be applied to some difficult-to-weld alloys, with great care, some post-processing for stress relief, and minimization of inter-granular corrosion effects. To learn more, check out our guide on the Composition of Stainless Steel.
2. Carbon Steel
Carbon steels respond very well to SAW jointing, with few special concerns or limitations.
3. Low-Alloy Steels
By careful control of flux and welding parameters, SAW can be applied to HSLA (high-strength low-alloy) steels with good results.
4. Nickel-Based Alloys
Solid solution nickel steel alloys respond well to SAW processing.
How Strong Is Submerged Arc Welding (SAW)?
The strength of SAW jointing is reliant upon the properties of the parts being welded, the welding parameters used, the filler rod, flux selection, and optimization of the welding technique. When performed correctly with appropriate materials and techniques, SAW welds can achieve high strength levels. This is particularly true on thicker sections, for which its deep penetration enables single-pass welding, making significantly superior joints when compared with processes that require multiple passes.
What Is the Minimum Thickness for Submerged Arc Welding (SAW)?
The minimum thickness for SAW can vary depending on various factors, including the specific application, welding parameters, joint design, and base metal composition. While there is no strict minimum thickness requirement for SAW, the process is most effective and efficient with welding materials that are at least 6 millimeters (0.24 inches) thick or more.
What Are the Industries That Apply Submerged Arc Welding (SAW)?
SAW is widely applied in various industries due to its productivity, high deposition rates, quality outcomes, and ability to weld thick sections of steel. Some industries that use it are:
- Shipbuilding and offshore construction
- Pressure vessel manufacturing
- Pipeline construction
- Rail and transportation
- Energy sector
Can Submerged Arc Welding Be Done Underwater?
Yes, SAW can be performed underwater, and it is known as underwater submerged arc welding (USAW) or wet welding. The process of USAW is similar to conventional SAW, but it involves additional material considerations and equipment to accommodate the underwater environment. USAW has its limitations and challenges compared to welding in dry environments. The presence of water can affect the weld quality, and additional precautions are necessary to mitigate the risks associated with working in underwater conditions.
What Are the Advantages of Submerged Arc Welding (SAW)?
SAW has advantages that make it a popular welding process in various industries. These include:
- Enables high deposition rates and deep welds in single-pass processes.
- Deep penetration provides excellent fusion between thick-section components, resulting in high-integrity welds.
- With well-managed parameters, SAW produces welds with exceptional mechanical properties, including high strength and good impact resistance.
- Ideally suited to automation and mechanization and can be readily integrated into automated manufacture.
- Requires less operator skill compared to some other welding processes, once the parameters are set.
- Excellent bead aesthetics result from well-operated SAW. The process generates minimal spatter and produces uniform and regular weld beads, reducing the need for post-processing.
- Can be applied to a wide range of materials, including carbon steels, HSLA steels, stainless steels, and some non-ferrous metals.
What Are the Disadvantages of Submerged Arc Welding (SAW)?
SAW also has some limitations and disadvantages. These include:
- Only functions effectively on flat or horizontal welding positions. Welding in vertical or overhead positions is possible with SAW, but controlling the flux application and weld pool requires specialist methods.
- Requires access to both sides of a joint for effective flux and electrode placement.
- Unsuitable for very thin materials.
- Requires the use of flux, which must be properly handled, stored, and managed. This adds complexity and costs to the setup/operation process.
- Produces significant fumes, smoke, and emissions during the welding process.
- The submerged nature of SAW means that the weld is performed blind. This can make it impossible to visually monitor and control the weld pool conditions in either manual or automated applications.
Is Submerged Arc Welding (SAW) Expensive?
It depends. The setup cost of SAW can vary depending on several factors including: the specific application, application requirements, material, and welding parameters. While SAW has a relatively high initial setup cost, it can offer huge advantages in terms of productivity, efficiency, and weld quality that make it cost-effective for higher volume and more challenging tasks.
Is It Hard To Learn Submerged Arc Welding (SAW)?
No, submerged arc welding (SAW) is generally considered to be relatively easier to learn compared to some other welding processes. Although SAW is considered relatively easy to learn compared with some welding techniques, it still requires effective training, experience, and adherence to safety protocols.
What Is the Difference Between SAW and SMAW?
SAW and shielded metal arc welding (SMAW or stick welding) are related welding processes that have distinct characteristics and application differences. In SAW, the arc is formed between a continuously fed bare wire or tube electrode and the workpiece. The arc is shielded by an overlay of granular flux. Shielded metal arc welding (SMAW), on the other hand, uses a flux-coated electrode, which melts during welding, creating a shielding gas and reducing slag to protect the weld pool. In SAW, the arc is submerged under the layer of flux, making it difficult to directly observe the weld pool. The SMAW arc is visible as it is formed between the electrode and the workpiece. The welder can visually monitor the arc and the weld pool, allowing adjustments to be made throughout the process.
SAW is really only suited to flat and horizontal welding positions, as the molten metal will sag or drip when not guided into the weld by gravity. SMAW can be performed in various positions, including flat, horizontal, vertical, and overhead when performed with highly developed skills.
Summary
This article presented submerged arc welding, explained it, and discussed its purpose and how it works. To learn more about submerged arc welding, contact a Xometry representative.
Xometry provides a wide range of manufacturing capabilities, including sheet cutting and other value-added services for all of your prototyping and production needs. Visit our website to learn more or to request a free, no-obligation quote.
Disclaimer
The content appearing on this webpage is for informational purposes only. Xometry makes no representation or warranty of any kind, be it expressed or implied, as to the accuracy, completeness, or validity of the information. Any performance parameters, geometric tolerances, specific design features, quality and types of materials, or processes should not be inferred to represent what will be delivered by third-party suppliers or manufacturers through Xometry’s network. Buyers seeking quotes for parts are responsible for defining the specific requirements for those parts. Please refer to our terms and conditions for more information.
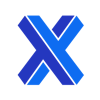