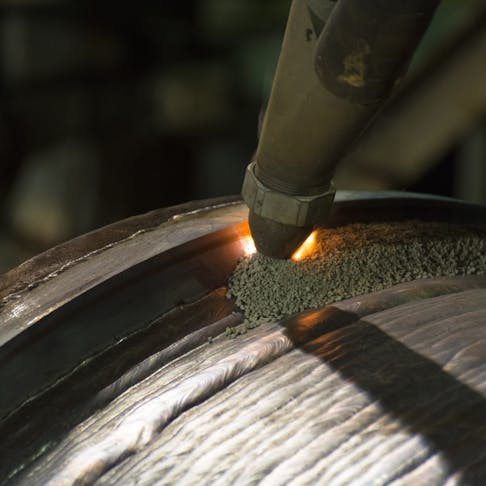
Flux Welding: Definition, How It Works, Types, and How To Use
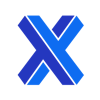
Among all the different types of welding, flux welding stands out as a useful, dependable, and versatile metal joining process. Flux welding is a type of arc welding that uses a material called “flux” to protect the weld pool from interacting with elements in the air during the welding process. Flux materials generally consist of borax, hydrochloric acid, or zinc chloride. In flux welding, a joint is blanketed with flux, or else a flux-coated or flux-cored electrode is used. When the weld pool forms, the flux melts onto the pool and protects it from reacting with atmospheric elements. There are three different types of flux welding: FCAW (flux-cored arc welding), SAW (submerged arc welding), and SMAW (shielded metal arc welding — also called “stick welding).
This article will define flux welding, explain how it works, describe the available types, and review how to perform this welding process.
What Is Flux Welding?
“Flux welding” is a group of arc welding processes that use a particular material, called “flux,” to protect the pool of molten material that is generated during the joining process. Materials like borax, hydrochloric acid, and zinc chloride are examples of flux materials. The pool of molten metal that is generated during the welding process can interact with elements in the air such as oxygen and nitrogen. This can cause welds to be porous, brittle, and weak. The flux melts on top of the weld pool, creating a slag that acts as a barrier to atmospheric gasses. Proper protection by an appropriate flux enables the production of strong, resilient, welded joints.
What Is Flux Welding Used For?
Flux welding is used for a variety of applications due to its ability to create strong, permanent welded joints in any environment. Flux welding is used across a broad spectrum of industries, from high-rise and pipeline construction, to automotive manufacturing, to repair and maintenance. In construction, flux welding is used to weld structural members together. In automotive manufacturing, flux welding is used for joining chassis and other assemblies. Flux welding is also used to repair damaged components in industries ranging from automotive and construction to infrastructure and power generation.
When To Use Flux Welding?
All arc welding techniques must provide protection against atmospheric contamination of the molten weld pool, whether by using shielding gasses or flux welding methods. Flux welding is particularly useful in windy, outdoor environments or confined spaces with little ventilation.
How Does Flux Welding Work?
Flux welding methods form a subset of the arc welding processes. Like other arc welding methods, such as MIG (metal inert gas) or TIG (tungsten inert gas), flux welding involves generating an electric arc between a workpiece and an electrode. The electrode is either coated with flux, cored with flux, or the flux is applied directly to the weld area. The electric arc generated between the workpiece and electrode melts the two materials by heating them to temperatures as high as 7000 °F. As the electrode and the workpiece melt together, the flux also melts, forming a liquid layer on top of the weld pool which protects the joint from interacting with elements in the air.
How Does Flux Welding Differ From Gas Welding?
Flux welding differs from gas welding in that gas is not necessary for flux welding. Flux welding is a collection of arc welding processes that uses the heat generated from an electric arc to weld parts together. Gas welding uses the heat generated from combustible fuel to melt and fuse materials together. For more information, see our what is gas welding guide.
Does Flux Welding Need Gas?
No, flux welding does not require shielding gas. The flux fulfills the same purpose as shielding gas during welding. That is, flux protects the weld pool from reacting with elements in the air in the same manner as shielding gas.
What Are the Different Types of Flux Welding?
There are different types of flux welding; each type utilizes a different method for applying flux. The different types of flux welding are described below:
1. Flux-Cored Arc Welding (FCAW)
Flux-cored arc welding, or FCAW, is a flux welding process that utilizes a hollow, continuously fed electrode filled with flux. FCAW can be performed indoors or outdoors because the flux is integrated within the electrode. Additionally, flux-cored arc welding is a great choice for welding contaminated surfaces and for welding a variety of workpiece materials. Disadvantages of FCAW, however, include more expensive electrodes compared to other welding processes, and the formation of slag that must be removed after each welding pass.
2. Submerged Arc Welding (SAW)
Submerged arc welding (SAW) is a type of flux welding in which the joint area of a workpiece is blanketed with flux. In SAW, a continuously fed electrode is used to generate an electric arc between it and the workpiece. The electric arc produces extremely high temperatures that melt both the workpiece material and the flux. As the flux melts, both a shielding gas and a slag are formed. Both act as protective barriers against elements in the air.
One advantage of submerged arc welding is that it limits the amount of splatter and sparks generated during the welding process. Another advantage of SAW is that the blanket of flux suppresses the emission of toxic fumes and UV radiation. Despite these advantages, SAW is limited to use on ferrous metals, and requires slag to be removed after each welding pass.
3. Shielded Metal Arc Welding (SMAW)
Shielded metal arc welding (SMAW), also known as stick welding, is a type of flux welding that uses an electrode that is coated with flux. Like FCAW and SAW, stick welding works by striking an electric arc between the electrode and the workpiece. The intense heat generated from the arc melts the workpiece and the flux-coated electrode to create a weld pool that is protected from elements in the air. Advantages of stick welding include portability, low costs, and the ability to weld indoors and outdoors. However, stick welding is an essentially manual process that requires the constant replacement of individual electrode rods as they are consumed. As with the other flux welding processes, the slag formed by the flux must be removed after each welding pass.
How To Use a Flux Welding Machine?
Using a flux welding machine is not too different from using welding machines designed for other processes like TIG (tungsten inert gas) or MIG (metal inert gas). The steps below explain how to use a flux welder:
- Ensure that the work environment is safe. Wear proper protective gear, including gloves, boots, and welding goggles. Clear the work environment of flammable or hazardous materials. It should be well-ventilated in order to evacuate harmful fumes and gasses generated during welding.
- Connect the welding machine to a grounded power source. Make sure the polarity of the wires on the welding machine is correct, as the polarity affects heat dissipation in the weld. Adjust the electrode wire feed speed based on the type of wire and the workpiece material.
- Clean the workpiece and remove any contaminants that could affect the quality of the weld. Rust, debris, dust, paint, and oil should be removed. Then, secure the workpiece as desired.
- Depending on the type of flux welding process being used, hold the welding torch or electrode holder firmly and maintain a constant angle and distance from the workpiece. Start the arc between the workpiece and electrode and begin welding along the joint line in a steady, consistent manner. Slag will form during the process and should be removed after it has fully cooled. If using FCAW, the wire will feed automatically. If stick welding, the electrode will shorten during the welding process and the distance from the workpiece will change unless the position of the electrode is changed to compensate for the shortening of the electrode during the welding process.
- Allow the welded joint to completely cool. Inspect the quality of the weld and clean the area by removing slag and spatter. Perform heat treatment to the part as necessary to relieve thermal stresses and improve the strength of the welded joint.
What Types of Materials Can Be Flux Welded?
Flux welding can be used on both ferrous and nonferrous metals. A list of materials that can be welded by flux welding is shown below:
- Carbon steel
- Cast iron
- Stainless steel
- Low alloy steels
- High-nickel alloys
- Aluminum
- Copper
- Nickel
Can Aluminum Be Joined Using Flux Welding?
Yes, flux welding can be used to join aluminum. While FCAW, SAW, and SMAW can all be used for welding aluminum, using the three flux welding processes is often more difficult than other arc welding processes. Generally, aluminum is a difficult material to weld due to its high thermal conductivity, its surface oxide layer, and its tendency to be porous when cooled from a molten state. A special aluminum flux-coated electrode, the correct amperage associated with that electrode, and a skillful operator are needed to successfully weld aluminum.
What Range of Material Thicknesses Can Be Joined by Flux Welding?
There are no restrictions on how thick a material can be to be flux welded, so long as proper joint preparation is completed. Additionally, the thickness of a material that can be joined using flux welding processes largely depends on the amperage of the welding machine. Flux welding is typically used for welding parts with thicknesses between 20 gauge (0.0375”) and 0.5”. However, parts thicker than 2” can be flux welded if a welding machine with sufficient amperage is used.
Are Flux-Welded Joints Strong?
Yes, joints produced by flux welding are strong. As long as proper joint preparation, form, and technique are used to create the weld, the resulting joints are both strong and permanent.
What Are the Benefits of Flux Welding?
Flux welding has a number of benefits. These benefits are listed and described below:
- The presence of flux protects the weld pool from reacting with elements in the air. It contributes to the creation of a strong, permanent joint.
- Flux welding processes do not require shielding gas. Therefore, flux welding can be used indoors, outdoors, and in poorly ventilated areas. Additionally, since operators do not have to carry gas canisters, welds over large distances or welds in confined spaces can be completed more easily.
- Flux, especially if using SAW, helps mitigate spatter and sparks that are often generated during the welding process. This creates a safe workspace for the operator and surrounding people.
- Flux welding can deeply penetrate the workpiece to create strong, deep welds. The weld pool is protected from the elements in the air which helps heat generated from the electric arc to penetrate deeper into the part. Especially with FCAW, the current density in the flux-cored wire is high which allows a higher arc density and the ability to penetrate deeper into a part.
What Are the Disadvantages of Flux Welding?
Flux welding is not without its disadvantages. Some disadvantages of flux welding are listed below:
- Can be more expensive over time compared to other arc welding processes due to the need to continuously buy flux material, and flux-coated or flux-cored electrodes. Welding equipment including the actual welding machine is also more expensive compared to other arc welding processes.
- Can take more time than other arc welding processes since the welding joint area must be properly cleaned and prepared before welding and slag must be removed before every welding pass. Additionally, the need to prepare flux, whether by blanketing the workpieces or spooling flux-cored wire, adds extra processes that aren’t needed in other welding processes like TIG or MIG.
- Can be limited in its potential applications due to necessary welding orientations such as with SAW and the need to have a highly skilled operator. SAW can only be completed on a flat surface and cannot be completed at an angle. Additionally, FCAW and stick require a relatively high level of expertise to successfully weld parts compared to other processes like MIG.
What Is the Difference Between TIG and Flux Welding?
The primary difference between TIG (tungsten inert gas) welding and flux welding is that TIG welding uses a shielding gas to protect the weld pool, while flux welding uses a flux material. Another difference is that a non-consumable tungsten electrode is used in TIG while a consumable or non-consumable electrode may be used in flux welding.
What Is the Difference Between Flux and Laser Welding?
The main difference between flux welding and laser welding is that flux welding uses an electric arc to heat the workpiece while laser welding uses electromagnetic energy to heat the workpiece. Another big difference between the two is that flux welding is a slower process compared to the CNC-automated laser welding process. For more information, see our guide on what is laser welding.
Summary
This article presented flux welding, explained it, and discussed its various types and how it works. To learn more about flux welding, contact a Xometry representative.
Xometry provides a wide range of manufacturing capabilities, including sheet cutting and other value-added services for all of your prototyping and production needs. Visit our website to learn more or to request a free, no-obligation quote.
Disclaimer
The content appearing on this webpage is for informational purposes only. Xometry makes no representation or warranty of any kind, be it expressed or implied, as to the accuracy, completeness, or validity of the information. Any performance parameters, geometric tolerances, specific design features, quality and types of materials, or processes should not be inferred to represent what will be delivered by third-party suppliers or manufacturers through Xometry’s network. Buyers seeking quotes for parts are responsible for defining the specific requirements for those parts. Please refer to our terms and conditions for more information.
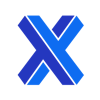